在压铸新产品开发和新模具试制阶段,或多或少都会出现导致试制失败的问题。而影响试模失败的因素有很多。有哪些相关因素呢?
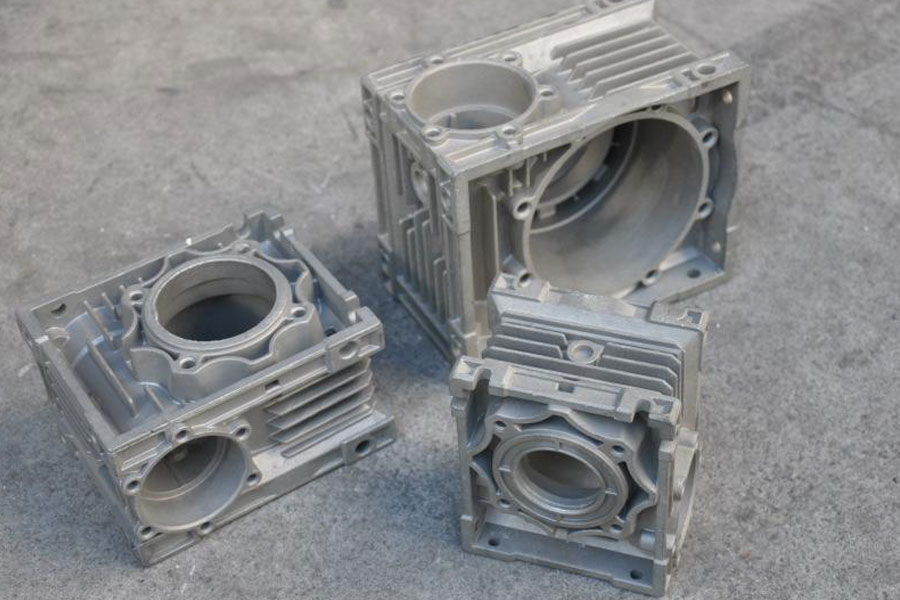
首先,在开发阶段对铸件结构和模具浇口系统设计进行审查和分析。其次,压铸生产的工艺参数,如熔融金属温度、压铸压力、速度和快速切换点等是否合理。等等,这些因素都是直接影响压铸件内外质量的关键。
但在大多数情况下,模具设计与生产密切相关。影响模具的因素包括型腔数量、浇口系统设计、浇口类型(位置、面积、方向)等。对于壁厚差异较大的铸件,还可采用局部高压点冷却和型芯冷却。以达到平衡模具温度的目的。只有模具设计得好,才能获得更宽的工艺参数范围,更有利于铸件的内外质量。为了具体审查和分析,我们必须使用一些辅助软件。例如:模流分析软件、工艺参数分析软件 PQ 2 图等。
理论数据分析
1) 通过模流软件分析初步设计的浇口位置、面积和方向,渣袋排气位置等。了解熔融金属在型腔内流动时的夹带、温度分布、流动路径和速度,以及渣袋的集渣和排渣情况,发现问题,为下一步的审查和修改提供依据,从而得到更好的浇口系统。
2)利用 PQ 2 图插入模具、设备等参数分析,可以初步设定工艺参数和压机吨位选择的合理性,发现工艺参数设置中存在的问题并及时纠正;还可以得到理论 以上工艺参数对压铸机工艺参数的调整具有指导意义。
压铸模具试验和工艺参数优化
试模的主要目的是找出优化的工艺参数和模具改造方案。这就要求即使材料、机器设置或环境因素发生了变化,仍能保证模具稳定、不间断地批量生产出合格的产品。将模具的 "适应性 "提高到极致,而不仅仅是得到几个好的试模样品。
试模前的准备工作。根据模具的设计图纸,详细检查相关尺寸(尤其是浇口套接口的尺寸);弄清模具各活动部件(抽芯和滑块)的动作顺序;确认所采用的压铸机型号、压射位置、油管接口、压腔直径和接口尺寸是否与模具的实际要求一致。必须特别注意的是,试模时使用的压铸机必须与批量生产模具时使用的压铸机型号相匹配,否则模具可能无法使用。
根据 PQ2 图得出的理论工艺参数,进行试生产,找出实际参数与理论参数的差异。并不断调整修改,直到获得内部质量良好的成型铸件。其中,压力机的性能可能不稳定,这让我们很难判断问题所在。此时,可以使用 "注塑监控器 "来监控注塑过程中的速度、压力、位移等参数,并通过曲线的波动情况进行判断。帮助我们准确发现问题,有效指导工艺参数的修正,了解设备的性能。最终获得一套适合该设备的最佳工艺参数。
模具厂生产的模具往往是由于设计考虑不周或生产过程中加工不当造成的。往往存在一些问题,如公差过大、局部过渡不平滑、结构不合理、冷却水布置不合理。温差过大等。导致铸件不合格或试模生产失败。由于实际结果与理论之间的差异,试模是发现模具问题最简单、直接和有效的方法。通过热成像图还可以了解模具的温度分布以及冷却水位置是否合理,这对延长模具的使用寿命非常有帮助。这对延长模具寿命也有很大帮助,同时对喷雾调整也有指导意义。
在试模过程中,工艺参数稳定后生产的试模件需要产品工程师、工艺技术人员和质量工程师根据客户要求进行现场审查。主要审查内容包括
压铸试模不仅是一个理论与实践推导和验证的过程,也是一个不断纠错和改进的过程。而且,当代压铸有了更多高科技的辅助软件和设备,帮助我们更科学地试模。对铸件结构、模具结构、压铸工艺和压铸设备性能进行系统分析,找出差异和问题。问题解决后,对模具结构和工艺参数进行优化。使我们的模具更适合稳定生产和质量维护。这充分体现了压铸试模的意义。