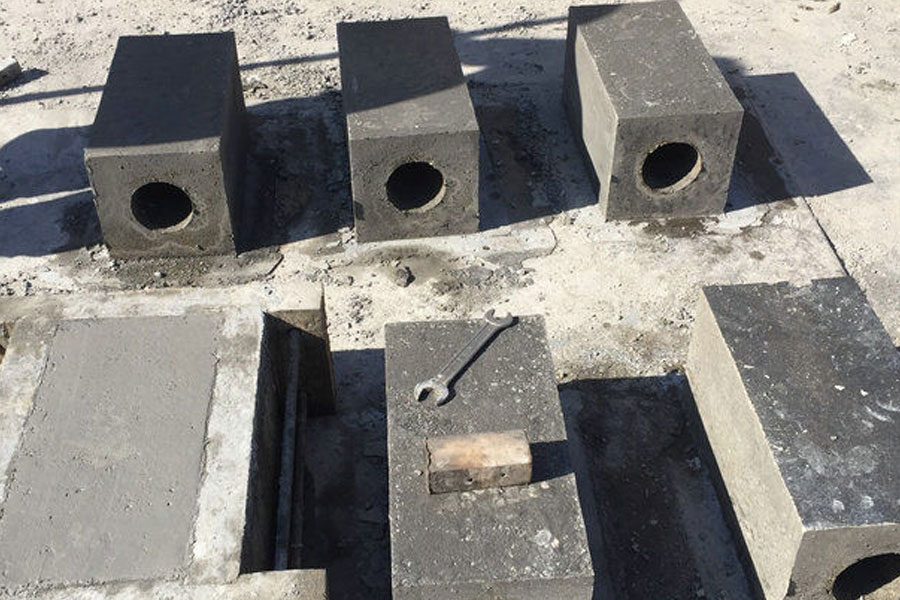
影响水杯 "老化 "的因素有哪些?如何消除水杯的 "老化"?
刚配制好的水玻璃是真溶液。但在储存过程中,水玻璃中的硅酸会发生缩合聚合反应,由真溶液逐渐缩聚成大分子硅酸溶液,最后成为硅酸凝胶。因此,水玻璃实际上是由聚合度不同的多硅酸组成的异质混合物,容易受到其模量、浓度、温度、电解质含量和储存时间的影响。
在储存过程中,水玻璃的分子会发生凝结聚合形成凝胶,其粘结强度会随着储存时间的延长而逐渐降低。这种现象被称为水玻璃的 "老化"。
以下两组测试数据可以解释这种 "老化 "现象:高模量水玻璃 (M=2. 89, ρ=1. 44g/cm3) 经过 20 天、60 天、120 天、180 天、240 天的储存后,二氧化碳硬化水玻璃吹砂的干拉伸强度相应下降了 9.5%, 36.8%和 40%;低模量硅酸钠(M=2. 44,ρ=1. 41g/cm3)干燥后分别贮存 7、30、60 和 90 天。拉伸强度分别下降了 4.5%、5%、7.3% 和 11%。
水玻璃的储存时间对酯硬化水玻璃自硬砂的初始强度影响很小,但对后期强度影响很大。根据测量,高模量水玻璃的后期强度降低了约 60%,低模量水玻璃降低了 15-20%。残余强度也会随着储存时间的延长而降低。
在水玻璃的储存过程中,聚硅酸的缩聚和解聚同时进行,分子量比例失调,最终形成单正硅酸和胶体粒子共存的多分散体系。也就是说,在水玻璃的老化过程中,硅酸的聚合度不成比例,单正硅酸和高聚硅酸的含量随着储存时间的延长而增加。由于水玻璃在贮存过程中发生缩合聚合和解聚反应,粘结强度降低,即出现 "老化 "现象。
影响水玻璃 "老化 "的主要因素有:水玻璃的储存时间、模量和浓度。储存时间越长,模量越高,浓度越大,老化越严重。
长期存在的水玻璃可以通过各种方式进行改装,以消除 "老化",恢复水玻璃的新鲜水性能:
1.物理改造
水玻璃的老化是一个缓慢释放能量的自发过程。老化水玻璃的物理改性是利用磁场、超声波、高频或加热向水玻璃体系提供能量,促进聚硅酸胶的高度聚合。颗粒重新解聚,促进聚硅酸分子量的均匀化,从而消除老化现象,这就是物理改性的机理。例如,经过磁场处理后,硅酸钠砂的强度提高了 20-30%,硅酸钠的添加量减少了 30-40%,节省了 CO2,提高了可塌落性,具有良好的经济效益。
物理改性的缺点是不耐久,处理后存放时粘结强度会降低,因此适合在铸造车间处理后尽快使用。特别是对于 M>2.6 的水玻璃,硅酸分子浓度较大,经过物理改性和解聚后,会较快地发生聚凝。处理后最好立即使用。
2.化学改性
化学改性是在水玻璃中加入少量化合物,这些化合物都含有羧基、酰胺基、羰基、羟基、醚基、氨基等极性基团,通过氢键或静电吸附在硅酸分子或胶体粒子上。表面,改变其表面势能和溶解能力,提高聚硅酸的稳定性,从而阻止 "老化 "的进行。
例如,在水玻璃中加入聚丙烯酰胺、变性淀粉、聚磷酸盐等可以达到更好的效果。
在普通水玻璃甚至改性水玻璃中掺入有机物可以起到多种作用,如:改变水玻璃的粘流性能;改善水玻璃混合物的造型性能;增加粘结强度,使水玻璃的绝对添加量减少;提高硅酸凝胶的可塑性;降低残余强度,使水玻璃砂更适用于铸铁和有色合金。
3.物理化学改性
物理改性适用于加工 "老化 "水玻璃,改性后可立即使用。化学改性适用于加工新鲜的水玻璃,改性后的水玻璃可以长期保存。物理改性和化学改性相结合可以使水玻璃具有持久的改性效果。例如,在高压釜中加入聚丙烯酰胺对水玻璃进行改性就有很好的效果。其中,压力和高压釜的压力都会用到。搅拌属于物理改性,添加聚丙烯酰胺属于化学改性。
如何防止二氧化碳吹硬硅酸钠砂型(芯)表面粉化?
苏打硅酸钠砂经吹二氧化碳硬化并放置一段时间后,有时会在下模(芯)表面出现一种类似 "嗬霜 "的物质,这种物质会严重降低该处的表面强度,在浇注时容易产生洗砂缺陷。据分析,这种白色物质的主要成分是 NaHCO3,可能是硅酸钠砂中水分或 CO2 过多造成的。其反应如下
解决方案如下
如何提高水玻璃砂模(芯)的防潮性能?
通过二氧化碳或加热方法硬化的苏打水玻璃砂芯被组装在湿粘土模具中。如果不及时浇注,砂芯的强度会急剧下降,不仅可能发生蠕变,甚至坍塌;存放在潮湿环境中砂芯的强度也会明显降低。表 1 列出了二氧化碳硬化的钠水玻璃砂芯在相对湿度为 97% 的环境中放置 24 小时后的强度值。在潮湿环境中存放时强度降低的原因是钠水玻璃的再水化。硅酸钠粘结剂基体中的 Na+ 和 OH- 会吸收水分并侵蚀基体,最终破坏硅氧键 Si-O-Si,导致硅酸钠砂的粘结强度显著下降。
解决这一问题的措施有
4 二氧化碳吹硬水玻璃-碱性酚醛树脂砂复合工艺有什么特点?
近年来,为提高铸钢件质量,一些中小企业迫切需要采用树脂砂工艺。但由于经济能力有限,无力购买树脂砂再生设备,旧砂无法回收再利用,导致生产成本居高不下。为了找到一种既能提高铸件质量,又不会过多增加成本的有效方法,可以将二氧化碳吹炼硬化硅酸钠砂和二氧化碳吹炼硬化碱性酚醛树脂砂的工艺特点结合起来,采用二氧化碳吹炼硬化硅酸钠-碱性酚醛树脂。树脂砂复合工艺以碱性酚醛树脂砂为面砂,水玻璃砂为背砂,同时吹入 CO2 进行硬化。
CO2- 碱性酚醛树脂砂中使用的酚醛树脂是由苯酚和甲醛在强碱性催化剂作用下缩聚而成,并加入偶联剂。其 PH 值≥13,粘度≤500mPa-s。砂中酚醛树脂的添加量为 3% 至 4%(质量分数)。当 CO2 流量为 0.8~1.0m3/h 时,最佳吹气时间为 30~60s;吹气时间过短,砂芯硬化强度低;吹气时间过长,砂芯强度不提高,浪费气体。
CO2 碱性酚醛树脂砂不含 N、P、S 等有害元素,因此消除了由这些元素引起的气孔、表面微裂纹等铸造缺陷;浇注时不释放 H2S 和 SO2 等有害气体,有利于环保。因此消除了由这些元素引起的气孔、表面微裂纹等铸造缺陷;浇注过程中不释放 H2S 和 SO2 等有害气体,有利于环境保护;塌落性好,易于清理;尺寸精度高;生产效率高。
二氧化碳吹硬水玻璃-碱性酚醛树脂砂复合工艺可广泛用于钢铸件、铁铸件、铜合金和轻合金铸件。
复合工艺简单方便。其工艺流程如下:首先将树脂砂和硅酸钠砂分别混合,然后装入两个砂桶中;再将混合好的树脂砂作为面砂加入砂箱中捣实,面砂层厚度一般为 30-50mm;然后加入水玻璃砂,使背砂填充密实;最后向模具中吹入 CO2 气体进行硬化。
吹管直径一般为 25 毫米,可硬化范围约为吹管直径的 6 倍。
吹气时间取决于砂模(型芯)排气塞的大小、形状、气体流量和面积。一般情况下,吹气时间控制在 15~40 秒内。
吹硬砂模(型芯)后即可取模。砂模(芯)强度上升很快。取模后半小时内刷涂料,4 小时后封箱浇注。
复合工艺特别适用于没有树脂砂再生设备但又需要生产高质量铸件的铸钢厂。该工艺简单易控,生产的铸件质量与其他树脂砂铸件相当。
二氧化碳发泡硬化硅酸钠砂还可与二氧化碳发泡硬化聚丙烯酸钠树脂砂复合,用于生产各种优质铸件。
二氧化碳-有机酯复合硬化硅酸钠砂工艺有哪些优缺点?
近年来,CO2-有机酯复合硬化硅酸钠砂工艺有扩大应用的趋势。其工艺流程如下:混砂时加入一定量的有机酯(一般为正常所需用量的一半或水玻璃重量的 4~6%);造型完成后,吹 CO2 硬化至脱模强度(一般要求抗压强度在 0.5MPa 左右);脱模后,有机酯继续硬化,造型砂强度以较快速度上升;吹 CO2 并放置 3~6h 后,即可合模浇注。
硬化机制是
当水玻璃砂吹入二氧化碳时,在气体压差和浓度差的作用下,二氧化碳气体会向成型砂的各个方向流动。二氧化碳气体接触到水玻璃后,立即与水玻璃发生反应,形成凝胶。由于扩散效应,反应总是由外向内进行,外层首先形成一层凝胶膜,阻止二氧化碳气体与水玻璃继续反应。因此,在短时间内,无论用什么方法控制二氧化碳气体,都不可能使其与所有水玻璃发生反应。据分析,当成型砂达到最佳吹制强度时,水玻璃与 CO2 气体的反应约为 65%。这说明水玻璃并没有充分发挥其粘结作用,至少有 35% 的水玻璃没有发生反应。有机酯固化剂能与粘结剂形成均匀的混合物,充分发挥粘结剂的粘结作用。芯砂各部分的强度增长速度相同。
增加水玻璃的添加量可以提高砂模的最终强度,但其残余强度也会增加,导致砂子难以清理。水玻璃添加量过少时,最终强度过小,不能满足使用要求。在实际生产中,水玻璃的添加量一般控制在 4% 左右。
单独使用有机酯硬化时,有机酯的添加量一般为水玻璃量的 8-15%。在使用复合硬化时,据估计,在吹二氧化碳时,约有一半的水玻璃已经硬化,约有一半的水玻璃尚未硬化。因此,有机酯的用量占水玻璃用量的 4% 至 6% 比较合适。
复合硬化法能充分发挥二氧化碳硬化和有机酯硬化的双重优势,能充分发挥水玻璃的粘结作用,达到硬化速度快、脱模早、强度高、可塌性好、成本低的效果。综合效果。
然而,二氧化碳-有机酯复合硬化工艺需要比简单的有机酯硬化方法多添加 0.5%至 1%的水玻璃,这将增加废旧水玻璃砂再生的难度。
使用硅酸钠砂工艺生产铸铁件时,为什么容易产生粘砂?如何防止?
当使用硅酸钠砂制成的砂型(型芯)浇注铸铁件时,往往会产生严重的粘砂现象,从而限制了其在铸铁生产中的应用。
硅酸钠砂中的 Na2O、SiO2 与浇注过程中金属液产生的氧化铁形成低熔点硅酸盐。如前所述,如果这种化合物中含有较多的易熔无定形玻璃,则这层玻璃与铸件表面的结合力很小,收缩系数与金属不同。较大的应力很容易从铸件表面去除而不会粘砂。如果铸件表面形成的化合物中 SiO2 含量高,而 FeO、MnO 等含量低。则其凝固结构基本上为结晶结构,会与铸件牢固结合,造成粘砂。
用硅酸钠砂生产铁铸件时,由于铁铸件浇注温度低、含碳量高,铁和锰不易氧化,产生的粘砂层具有结晶结构,在铁铸件和粘砂层之间难以建立合适的粘砂层。氧化铁层的厚度与铸件和粘砂层之间的树脂砂不同,在生产铁铸件时,可通过树脂热解产生一层光亮的碳膜,因此粘砂层不易去除。
为了防止铁铸件生产过程中产生碱水玻璃砂,可以使用合适的涂料。如水性涂料,涂刷后表面需要干燥,因此最好使用醇基快干涂料。
一般情况下,铸铁件还可在硅酸钠砂中加入适量的煤粉(如 3%至 6%)(质量分数),使铸件与砂层之间的煤粉热解产生光亮的碳膜。它不会被金属及其氧化物润湿,因此粘性砂层很容易从铸件上剥离。
硅酸钠砂是否有望成为不排放废砂的环保型造型砂?
水玻璃无色、无味、无毒。如果接触皮肤和衣服,用水冲洗也不会造成严重问题,但必须避免溅入眼内。水玻璃在混砂、造型、硬化和浇注过程中不会释放刺激性或有害气体,也不会产生黑色和酸性污染。但如果工艺不当,加入过多硅酸钠,硅酸钠砂的塌落性就会不好,在清砂时粉尘飞扬,也会造成污染。同时,旧砂再生困难,废砂排放对环境造成碱性污染。
如果能克服这两个问题,硅酸钠砂就可以成为基本不排放废砂的环保型成型砂。
解决这两个问题的根本措施是将水玻璃的加入量减少到 2% 以下,这样基本上就可以将砂子抖落下来。水玻璃添加量减少后,旧砂中残留的 Na2O 也会减少。采用相对简单的干法再生方法,可以将循环砂中的 Na2O 残留量保持在 0.25% 以下。这种再生砂可以满足中小型铸钢件单造型砂的应用要求。此时,旧硅酸钠砂即使不采用昂贵而复杂的湿法再生,而采用相对简单而廉价的干法再生,也能得到充分的循环利用,基本不排放废砂,砂铁比可降至 1:1 以下。
如何有效再生硅酸钠砂?
如果旧硅酸钠砂中残留的 Na2O 过高,在砂中加入硅酸钠后,成型砂将没有足够的使用时间,而且过多 Na2O 的积累会使石英砂的耐火度变差。因此,在再生使用过的硅酸钠砂时,应尽可能去除残留的 Na2O。