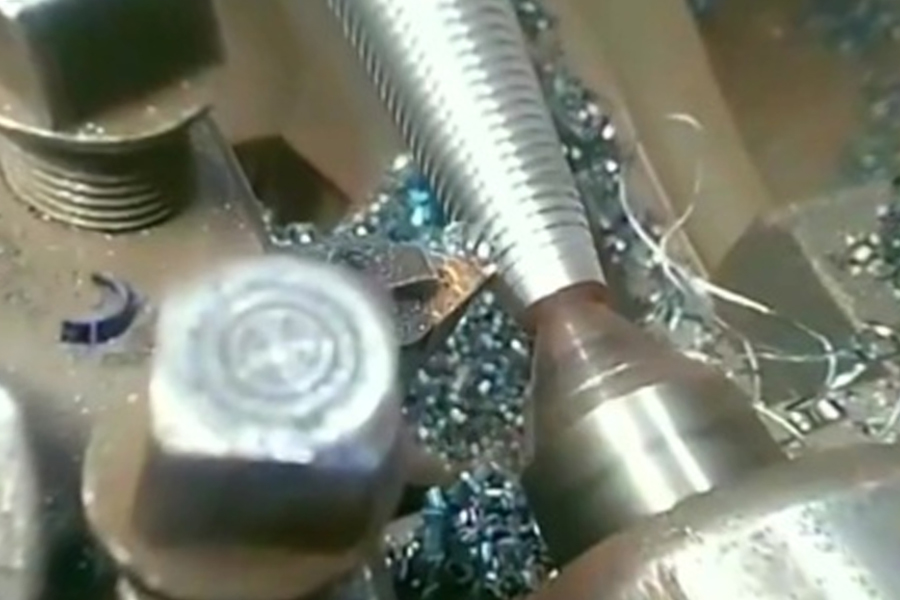
对于用户来说,使用可转位螺纹车刀在数控车床和加工中心上进行螺纹加工非常重要。正确合理地选择螺纹切削技术非常重要。
螺纹切削工艺取决于加工零件的结构和所使用的数控机床。一般来说,使用右切削刃加工右旋螺纹和使用左切削刃加工左旋螺纹具有刀片支撑稳定的优点。当然,在一般情况下,也可以采用相反的方法。
保持一致,以避免刀片一侧过度磨损,尽可能缩短刀具寿命。
d2--螺距直径 A--刀片倾角通常由可转位螺纹车刀的垫片决定。标准刀具为 +,但对于直径为 16mm 和 020mm 的内螺纹刀具,由于空间狭小,没有垫片。因此,当刀片倾斜度大于 +2° 时,无法进行加工。
螺纹车削的进给方法取决于切削机床、工件材料、刀片几何形状和加工螺纹的螺距。通常有以下四种进给方式:*常用的切削方式,车刀左右两侧同时切削,轴向切削分力在一定程度上被抵消,部分克服了轴向切削分力造成的车刀偏差现象。两侧磨损均匀,可保证齿形清晰,但存在排屑不畅、散热不良、受力集中等问题。适用于切削螺距小于 1. 5 毫米的螺纹。D 型单侧进给铣刀的进给方向与径向成一定角度。切屑被卷离刀片形成条状,散热效果较好。缺点是由于摩擦部分不切割,另一侧刃口会硬化。D 单面进料方向 30° 角进料切割。切削刃两面切削形成滚屑,排屑顺畅,散热性好,螺纹表面粗糙度值低。一般来说,这是车削不锈钢、合金钢和碳钢的最佳方法。大约 90% 的螺纹材料都使用这种方法。在数控车床上加工螺纹最好使用这种方法。一般来说,可以调用一个固定的周期,编程也很简单。
左右侧进给交替切削,即每次径向进给时,向左或向右横向移动一定距离,使车刀只有一侧参与切削。这种方法一般用于通用车床和中距大于 3mm 的螺纹加工,在数控车床上编程比较复杂。
螺纹铣削主要用于加工中心等数控镗铣机床。一般来说,小直径内螺纹(20 毫米)可以通过攻丝加工。但对于大直径内螺纹和外螺纹的加工,攻丝和套筒螺纹存在很多问题。因此,中粒铁切削是最好的加工方法。
螺纹铣削不同于螺纹车削加 X,这是因为花纹数控铣削主要是通过机床的三轴联动和螺旋插补加工来实现的,即在加工两轴圆弧敏感切削的同时,先进行三轴直线进给运动。轴向运动距离进行铣削。这是一种单边铣削加工。因此,最好的进给方式是采用径向直接进给的切削方式,这样两个切削刃同时切削,受力比较均匀。这样可以保证螺纹的精度,而且数控编程也相对简单。
二、螺纹车削和铣削切削的选择 螺纹切削参数(切削速度、反切削量、切削遍数)的选择由刀具和零件的材料决定。螺纹车削的切削速度一般比普通车削低 25% ~50%。螺纹背切削量和切削遍数的选择也尤为重要。D 值是否正确直接关系到中样是否合格。数量直接影响切割力的大小。蜈蚣回刀量需遵循递减原则,即回刀量必须小于前一回刀量,最小回刀值不得小于。5 胃。以下两个表格提供了公制内、外介质花纹的背刀值。此表也适用于螺纹铣削。
表 1 ISO 公制花纹背刀设定值(外螺纹)(mm)间距背刀切削次数 香味背刀数量切削次数 表 2 ISO 公制花纹背刀设定值(内螺纹)镉背刀切削次数 对于数控镗铣床而言,虽然螺纹铣削是通过三轴联动螺旋插补加工实现的,与螺纹车削不同,但切削用量的选择仍可采用车削介质。型的相关切削参数。由于螺纹铣削采用单刃切削,因此切削速度应为车削的一半,反切量仍可按车削选择。
3.螺纹车削和铣削数控程序编制 对于数控车床,一般标准螺纹车削编程指令为 G33(固定螺距切削)、G34(变螺距蝶形切削,螺距增大)、G35(变螺距螺纹切削,螺距减小)。中距由 / 和人尺指定,其中 K /、A:分别对应 X 轴和 Z 轴。不过,一般的数控系统和机床制造商都会提供螺纹车削罐装循环供用户使用,只需输入必要的参数即可。H. 在加工特殊蝶形花纹时,需要使用 G 命令和自行计算坐标点的编程方法。
螺纹铣削加工的编程与数控车削不同。主要使用 G02 和 G03 圆弧插补命令,即在增加第三轴直线插补的同时,增加两轴圆弧插补,形成螺旋插补运动。下面是普通内螺纹 M30X 2、深 14mm 数控铣削加工程序,回刀至 1.2mm,采用径向直接切削方式。
F200 采用边缘补偿,径向进给到反抓刀的位置。在蜈蚣切削中,往往由于刀具(包括刀片、垫片、芯轴等)的选择、进给方式、切削用量等的正确性。影响蜈蚣的加工质量,如:螺纹表面有冲击痕迹,表面粗糙度值为篼。这可能是由于零件或刀具伸长过大、刚性差、刀具中心切削过大,以及切削用量、刀片、刀刺选择不当等因素造成的。可以通过提高或降低切削速度、缩短刀具外伸长度、调整中心高度或进刀方式、采用侧向进刀或径向进刀、充分冷却、增加切削遍数等办法解决。
刀具磨损快、寿命短是由于切削速度过快、冷却不足、切削次数过多、刀片品牌不对等原因造成的。可采用降低切削速度、充分冷却、减少切削次数、选择韧性好的耐磨刀片 D 的硬度、改变切削角、增加冷却、提高切削速度、减少后刀量、调整中心架等方法。
在传统加工工艺中,底面先划线刨光,然后在 T611 镗床上加工。在加工过程中,每件工件都需要校正,装夹麻烦,费时费力,效率低下。
加工能力不足。因此,我们设计了用于车削和镗削的专用工装夹具,以生产轴承支架(H7rr35,中心高 257s),这是工件的主要尺寸。在此基础上,工装夹具的设计如图所示。夹具在 CW6263 车床上使用。
夹钳由主体 3 和三爪自定心卡盘 4 组成。取下三爪自定心卡盘的一个爪。主体 3 的左端与卡盘连接,并用螺栓 1 固定。A 侧工作台放在轴承支架的定位面上。s 首先确保轴承支架 5 的中心,然后使用三爪自选由于选择不当,要改变进给方式,切角。
切削刃上的堆积刃提高了切削速度并增加了冷却效果。涂层硬质合金刀片用于改进侧进给量的切削。
刀具塑性变形过大的原因是冷却不良、切削速度过高、刀片牌号不对,以及每次反抓量过大。应减少背抓量,增加冷却,降低切削速度,增加切削次数,使用高硬度、耐磨的硬质合金或徐层刀片。
如果螺纹上有毛刺,则应提高切割速度。利用切削定心卡盘 4 的自动定心原理夹紧工件进行加工。
然后拧紧卡盘,夹紧工件。
以车代撞充分满足了轴承支架的设计要求,保证了尺寸精度和位置精度,节省了工件划线和校正,保证了质量,工作效率比镗孔提高了 1.8 倍。
不同中心高度的轴承支架可以通过增加垫铁进行调整,但需要用螺栓固定。
使用前需要进行平衡调整,以避免离心力对工件质量和设备上的压板造成影响。