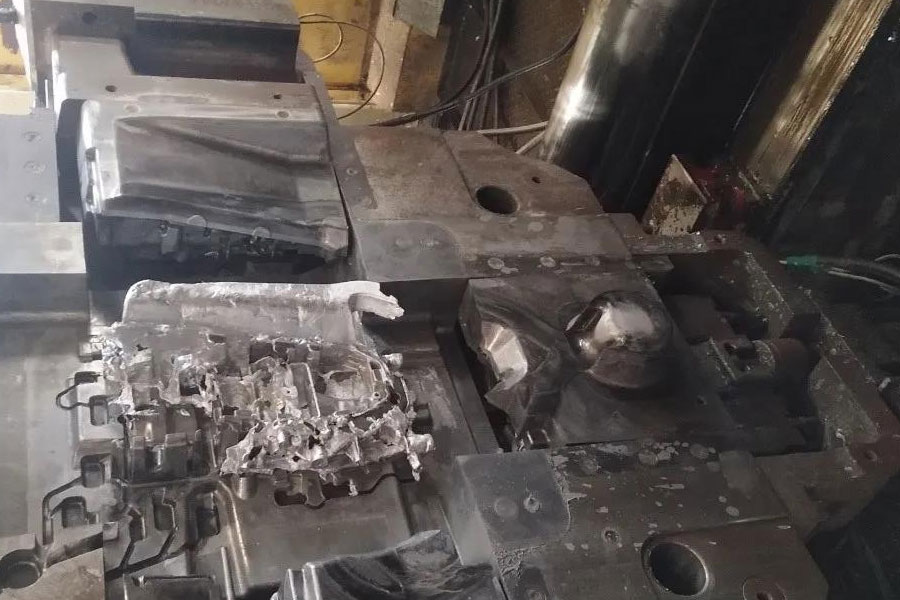
随着汽车工业的快速发展,对零部件的材料、设计和制造提出了更高的要求,高集成度、高性能、低成本已成为发展趋势。油底壳和下缸体都是汽车发动机的重要部件。通过将下缸体平衡轴和油底壳的集油和过滤功能集成在同一部件上,可有效减轻发动机的重量和体积。但由于结构复杂,壁厚变化大,需要拆分成不同的产品分别加工,然后再组合加工,造成产品制造困难。
本课题所研究的发动机集成油底壳包含三个铸件:油底壳本体、平衡轴承盖和单个平衡轴承盖。使用 A380 改良合金材料,铸件的平均壁厚为 3 毫米,最小壁厚为 2.5 毫米,毛坯的质量为 10.74 千克。74 千克。要求内腔在 300 kPa 下无泄漏,油道在 600 kPa 和温度超过 60 ℃ 时无泄漏。泄漏,用于 1.5T 发动机,年产量 40 万件,属于典型的复杂油底壳铸件。
压铸设计的技术要点
1.1 转轮设计
铸件 1 采用三面浇注设计,但侧重于一面的整体浇注,如图 1 所示。由于产品较长(上下长度达到 437.2 毫米),三面浇注设计可有效缓解工序长的问题,从而在不同区域对产品进行填充。但考虑到产品整体壁厚较厚,且浇注位置凸起嵌件较多,为避免铝熔体流动性受阻,加强单侧填充,整体逐渐缩小横截面积,加速铝熔体流动。设计浇口。
铸件 2 是平衡轴承盖,形状相对简单,只有中间两个平衡轴油槽较厚。根据铝熔液的简单流动规律,为了节约成本,提高铝熔液的有效产出率,采用了单面浇注方案,在壁厚区域设置浇口进行进料,如图 2 所示。
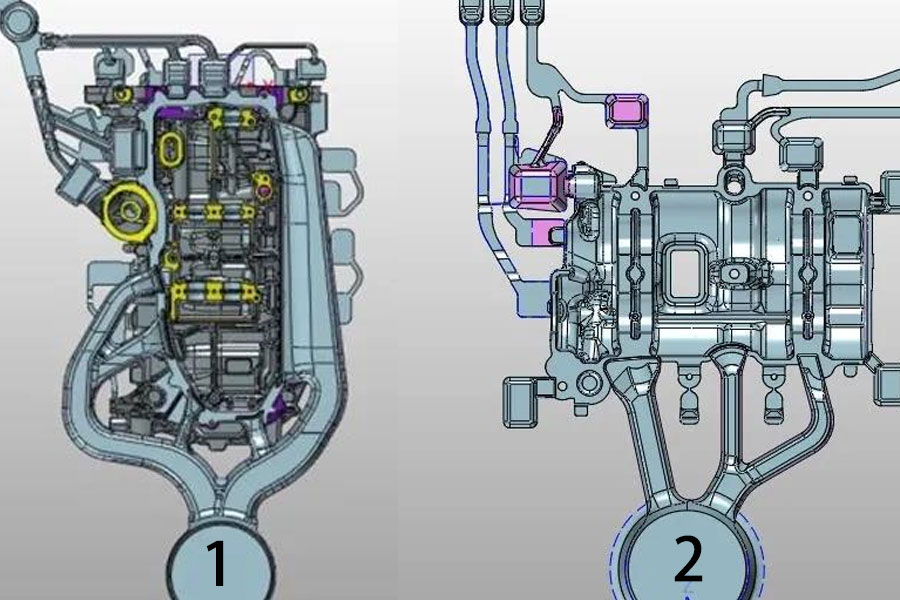
铸件 3 为单个平衡轴瓦盖,零件较小(尺寸为 63 毫米)×15 毫米× 采用一腔八模的设计进行填充和浇注,如图 3 所示。
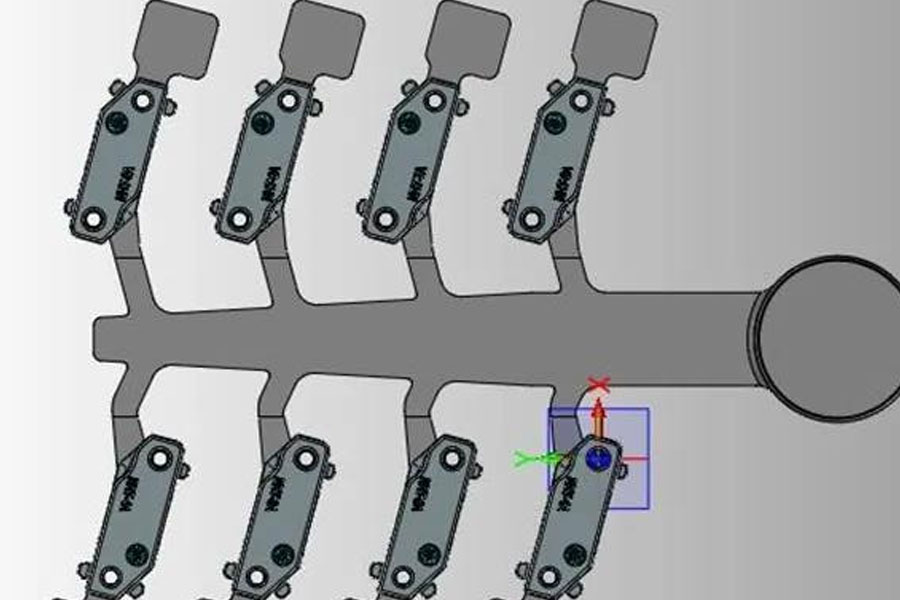
1. 2 排气方法
对于复杂的铸造 1,采用高真空排气。铸造 2,采用普通 "洗板 "式排气块。铸件 3 直接采用渣袋和渣袋尾部的型芯排气通道。在此强调一下铸造 1 的排气技术要点。
由于铸件的高压油道和滤油器都集中在水尾,因此水尾的排气效果是决定这些位置内部质量的关键因素。铸件 1 采用高真空排气来降低铸件水尾负压区的气压。首先,真空罐的容积必须选择≥800 L(这里的 800 L 是包含型腔和型槽的模具容积的 10 倍以上),以快速形成负压通道。其次,连接模具和真空机的管道必须密封、不透气,管道的真空度应保持在 2 000 Pa 以内。第三,模具用密封带密封,所有顶针和芯针都涂上密封胶。合模后,型腔真空度必须保持在 4 000 Pa 以内。最后,选择最佳的密封冲头生产,或使用加长版冲头,增加冲头的密封面积,有效缓解型腔漏气。
1.3 模具温度
由于高真空的特点,铝液没有完全按照理论流态填充(见图 4),铝液被吸入后容易在某些地方快速凝固,造成压铸件气孔、缩孔、裂纹等压铸缺陷。该铸件 1 的产品在冲头移动到 410 mm 位置时开始抽真空(铝液饱满度达到 70% 的要求),在 540 mm 位置时关闭真空。在如此短的时间内,必须确保抽出的铝液不会提前在水尾的重要位置凝固。因此,使用油温机将这些位置的模具温度分别控制在 220 ℃ 和 180 ℃。模具温度的提高和铝液流动性的增强是确保这两个重要位置内部质量的关键。
铸件 2 和 3 结构相对简单,填充距离短,易于成型。它们对模具温度的要求不高,只要模具表面温度较高且产品不变黑即可。
1.4 种模具冷却方式
该铸件 1 采用超点冷却技术和间歇供水技术。由于铸件生产需要保持较高的温度,而动模一侧的镶件凸台较多,因此不仅要保证高温,还要保证凸起的镶件不会形成热接缝,造成缩孔开裂等缺陷。对每个镶件进行切割处理,并将点冷却驱动至镶件内部。同步外围设备采用间歇供水方式。在产品凝固阶段,打开电磁阀对产品进行局部冷却。这样不仅可以获得较高的温度,还能获得良好的冷却效果。超点冷却工艺是专为压铸芯针设计的,如图 1 中箭头所示。壁厚区域中间的 4 毫米针会直接导致收缩。对 4 毫米的针采用超点冷却设计,可以解决螺纹孔的孔隙问题。同样,在其他横热区,也采用了超点冷针设计,针头可弹出,大大缓解了烧伤、气孔、断针等问题。超点冷却和间歇供水的时间设置需要考虑打孔材料的壁厚及其位置。因此,需要对这些不同区域的冷针进行分区控制。
铸件 2 仅在平衡轴中部有一个 4 毫米的油槽孔,在进料口有一个 Φ8 毫米的螺栓孔,采用超点冷控制。由于铝液被冲刷后,中间壁厚区域之间会形成疏松通道,因此必须使用超点冷针强行增加针孔周围的致密层,延迟时间为 1 s,冷却时间为 10 s。铸件 3 中的 16 个 Φ8 mm 小针均采用超点冷控制,以保持针孔附近致密层的厚度。
1.5 本地挤压技术的选择
局部挤压销可以快速解决壁厚区域的收缩问题,在压铸领域得到了广泛应用。模流热节分析如图 5 所示。铸件 1 的热节较多,需要合理安排挤压销的位置。首先,消除可以利用冷针消除的热节,其次消除不在关键位置的热节。最后,需要考虑挤压针筒在模具内部空间的布置。挤压针筒一般布置在结构复杂和防止漏气的位置。.
压铸过程控制要点
2.1 压铸过程中的喷流控制
在压铸过程中,动模和定模分别测量喷射流量,动模控制在 3 200 mL,定模控制在 2 200 mL。此外,动模和定模流量的上下限偏差值也分别设定。由于所选电磁流量计的精度为 50 mL,因此设定偏差为 ±200 mL,而 200 mL 是减少一个喷枪后的实际测量值。在生产过程中,如果超出偏差值,将直接输出报警信号,停止压铸生产周期。因此,可有效防止因喷枪堵塞而造成的喷涂粘模和灼伤。
2.2 熔铝温度的过程控制
由于保温炉的保温效果好,但加热速度比定量炉慢,因此需要控制铝熔液的入口温度。铝熔液的铸造温度为 675±10℃,因此铝熔液在运输钢包中的进料温度必须保持在 700℃以上。低于此温度的进料会影响铝熔液在填充过程中的流动状态,导致局部位置的气孔比例增加。加料温度高于 730 ℃ 会造成铝在模具表面严重烧焦和粘连,影响铸件的外观质量。设置保温炉的铝熔液温度报警器。如果浇注温度不在范围内,保温炉会报警并停止压铸生产循环,可有效防止铝熔液温度偏差造成的缺陷。
2.3 真空控制
由于铸件 1 的模具是用可移动和固定的模具密封带密封的,所有顶针和芯针都是通过涂抹密封剂密封的,滑道也是整体滑道,但冲头没有使用专用的密封冲头,而是使用加长板冲头(加长到 150 毫米)。在这种密封状态下,当真空度设定超过 4 kPa 时(4 kPa 是根据生产过程中的高通过率设定的经验报警值),就会触发报警,真空度一般在 2.3k Pa。清洁度和堵塞值一般接近 101 kPa,设定的报警值为 90 kPa(90 kPa 是根据工厂过滤罐的清洁周期设定的)。清洗周期结束后,应及时清洗真空阀过滤罐。否则会影响吸尘效果。真空罐的设定值为 1 kPa,一般在 2.2 至 400 Pa 之间。只要超过规定值,就会发出警报并关闭压铸机。
2.4 监测实际注入参数
压铸机采用国产宇部1650T 机型。除了自身的压铸机参数控制系统外,还利用二维码追溯系统(厂方称之为 MES 系统)连接压铸机和周边辅助设备,使 MES 系统能够实时读取各模具的生产参数,并反馈到云端进行云端对比(云端对比值按要求提前输入云端,根据不同参数的实际达成情况输出不同的范围值。例如,慢速为 ± 0. 05 m/s,高速为 ±3 m/s,等等。见表 2),对比后超出范围的产品将被系统锁定,判定为不合格。云大数据还会根据更新的数据量,定期计算产品报废与参数变化的实时关系。找出一段时间内废品率波动的原因,提高维修产品的合格率。压铸生产过程中会出现波动,可快速找出问题点,有效促进现场良性循环。
2.5 压铸水运输控制
输水开始时,每条管线用一个电磁阀控制直接冷却或普通点冷水输送的时间。水压为 0.4 兆帕,水温为 30℃纯水。除料槽、料套、冲头、分锥和料套强制冷板为常开直接冷却外,其他直接冷却(水障)和大点冷却均由电磁阀控制,延时 3 s,冷却 15 s,以保证模具温度。所有针头,从 Φ4 mm 到 Φ14 mm(中心管从 Φ1.5 mm)均采用超点冷控制,超点冷输水压力为 10 MPa,输水温度为 10 ℃(此处温度不能设置过低,过低虽然能带走更多热量,但容易造成断针)、每组相同规格的超冷针不超过 8 支(超过 8 支的超冷针直径超过 G1/2 连接管直径),所有超冷针合并为共 6 组,除 Φ4 mm 点冷针外,延时 5 s,冷却 13 s,Φ4 mm 点冷针设置为延时 4 s,冷却 13 s,以针对模具温度场。在需要快速冷却的区域,减少热点的出现。既保证了模具温度的平衡和保温,又消除了局部热点,保证了产品质量。
3.新型多功能油底壳的质量。三种产品分别由两台不同的机器生产,从铸件 1 到铸件 3 的日产量分别高达 980 件/天、1 500 件/天和 12 000 件/天。从铸件 1 到铸件 3 的日产量分别高达 980 件/天、1 500 件/天和 12 000 件/天,三种产品到最终装配的总体合格率高达 97%。图 8 是铸件 1、2 的外观和铸件 1、2、3 的内部质量图片。