铝压铸件具有生产效率高、加工成本低廉、生产过程易于机械自动化、铸件尺寸精度高、表面质量好、综合机械性能好等优点,但在铸造过程中容易产生气孔、流痕和划痕。缺陷,如瑕疵、凹痕、裂纹、欠铸等。这些缺陷使压铸件的外观质量和机械性能下降。为了避免压铸成型过程中出现上述问题,结构设计师需要在压铸件的结构设计中提前对方案进行评估,并在零件的结构设计中进行合理布局,通过优化结构将缺陷降到最低。
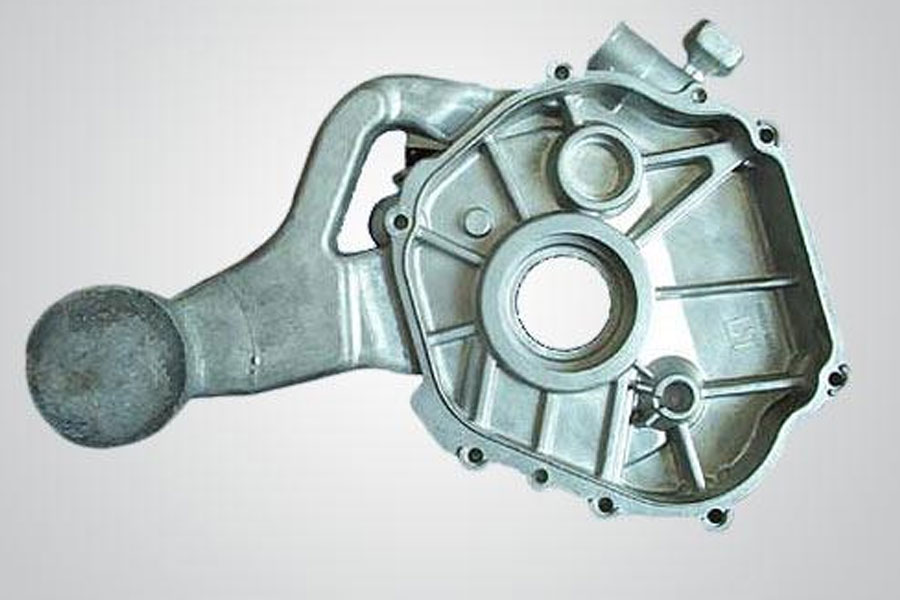
铝合金压铸的成型原理
铝合金压铸件必须通过模具成型,结合压铸机和铝合金进行综合利用。压铸工艺的原理是利用高压将熔融金属高速流入精密金属模具型腔,熔融金属在压力作用下冷却凝固形成铸件。冷室压铸和热室压铸是压铸工艺的两种基本方法。在冷室压铸中,熔融金属通过手动或自动浇注装置浇入压室,然后压射冲头推进,以液压方式将金属压入型腔。在热室压铸工艺中,压室与坩埚垂直,熔融金属通过压室上的进料口自动流入压室。注射冲头向下移动,将熔融金属通过鹅颈推入型腔。熔融金属凝固后,打开压铸模具,取出铸件,完成整个压铸成型过程。
肋条厚度与压铸件壁厚的关系(毫米)
铝合金压铸件的设计要点
压铸件设计的合理性关系到整个压铸成型工艺。在设计压铸件时,应充分考虑压铸件的结构特点和压铸的工艺要求,尽量减少所设计的压铸件在压铸成型过程中的缺陷。通过优化设计方案,最大程度地提高压铸件的质量。
最小压铸斜度
2.1 合理设计压铸件的壁厚
设计铝合金压铸件结构时应充分考虑壁厚。壁厚是压铸过程中一个具有特殊意义的因素。壁厚与整个工艺规范有着密切的关系,如充型时间的计算、内浇口速度的选择等。凝固时间的计算、模具温度梯度的分析、压力(最终比压)的影响、模具停留时间的长短、铸件顶出温度的高低和操作效率;如果设计壁厚太厚,会出现缩孔、砂眼和气孔,内部晶粒粗大等外部表面缺陷,降低机械性能,提高零件质量,增加成本;设计壁厚太薄,会造成铝液充填不良,造型困难,铝合金溶解不良,铸件表面填充困难。, 缺料等缺陷,给压铸工艺带来困难;随着气孔的增大,压铸件内部气孔、缩孔等缺陷增多。因此,在保证铸件足够强度和刚度的前提下,应尽量减少铸件壁厚,并保持截面厚度均匀。
2.2 压铸件加强筋的合理设计
对于大平面或薄壁压铸件,其强度和刚度较差,容易变形。此时,使用加强筋可以有效防止压铸件收缩和断裂,消除变形,提高压铸件的强度和刚度。对于平台等结构,可以使用加强筋来改善应力分布,防止根部断裂。同时,加强筋还能帮助熔融金属流动,改善铸件的填充性能。此处加强筋根部的厚度不大于壁厚,厚度一般设计为 0. 8~2.0mm;加劲肋的拔模角度一般设计为 1°~3°,高度越高,拔模角度越小;加劲肋根部应加圆角,以避免零件截面的急剧变化,同时有助于熔融金属的流动,减少零件的应力集中,提高零件的强度。此处的圆角一般接近壁厚;肋的高度一般不超过其厚度的 5。加强筋的厚度一般要求均匀。如果设计太薄,加强筋本身容易断裂;如果太厚,则容易出现凹陷和气孔等缺陷。表 1 显示了加强筋厚度与压铸件壁厚之间的关系。
2.3 合理设计压铸角
压铸件斜度的作用是减少铸件与模腔之间的摩擦,使铸件易于取出;保证压铸件表面不受力,并可延长模具寿命。模具的倾斜度与压铸件的高度有关。高度越大,模具的倾斜度越小。一般情况下,压铸件外表面的出模角度约为内腔出模角度的 1/2,但在实际设计中,为了保持壁厚,压铸件的内外表面可以设计成相同的角度。均匀性,简化结构设计。例如,表 2 是各种合金压铸件最小拔模角的参考值,表 3 是各压铸件型腔拔模角与深度的关系。
型腔倾斜度与模具深度之间的关系
2.4 合理设计加工余量
在设计压铸件时,应尽量避免机加工。机械加工会破坏零件表面的致密层,影响零件的机械性能;会暴露压铸件的内部气孔,影响表面质量,增加零件的成本。在无法避免压铸件机加工的情况下,应尽量避免采用切削量较大的设计,结构设计应尽量便于机加工或减少机加工面积,降低机加工成本。
压铸件上部尺寸精度要求高,或某些平面粗糙度要求高,压铸工艺难以满足要求。此时,需要进行后续加工。对于这部分结构,在设计时应尽量预留加工余量。压铸件的表面强度和硬度比内部高。加工时要注意保持表面密度,因此加工余量不宜过大。过度加工可能会导致气孔和外表面缺陷。表 4 留作机加余量的参考。
2.5 铝合金压铸件的喷涂设计
压铸件的表面喷涂设计一般采用粉末喷涂工艺,其原理是静电喷涂:涂料主要通过电极极化,然后被喷物体带相反的电荷,粉末在电场力的作用下均匀地附着在物体表面。.粉末喷涂工艺的特点:粉末静电喷涂不会造成空气污染,粉末可回收利用,降低材料消耗成本,涂膜具有良好的耐酸、耐碱和耐腐蚀性能。