自 20 世纪 90 年代以来,中国的压铸业取得了惊人的发展,并已发展成为一个新兴产业。目前,铝合金压铸工艺已成为汽车铝合金成形工艺中应用最广泛的工艺之一,占各种汽车成形工艺方法的 49%。
中国约有 3000 家压铸企业。压铸件产量从 1995 年的 26.6 万吨增加到 2005 年的 87 万吨,年增长率保持在 20%以上。其中,铝合金压铸件占 3/4 以上。中国压铸产品种类繁多,包括汽车、摩托车、通讯、家电、五金制品、电动工具、IT、照明、扶梯梯级、玩具灯等。随着技术水平和产品开发能力的提高,压铸产品的种类和应用领域不断扩大,其压铸设备、压铸模具和压铸工艺也发生了巨大变化。
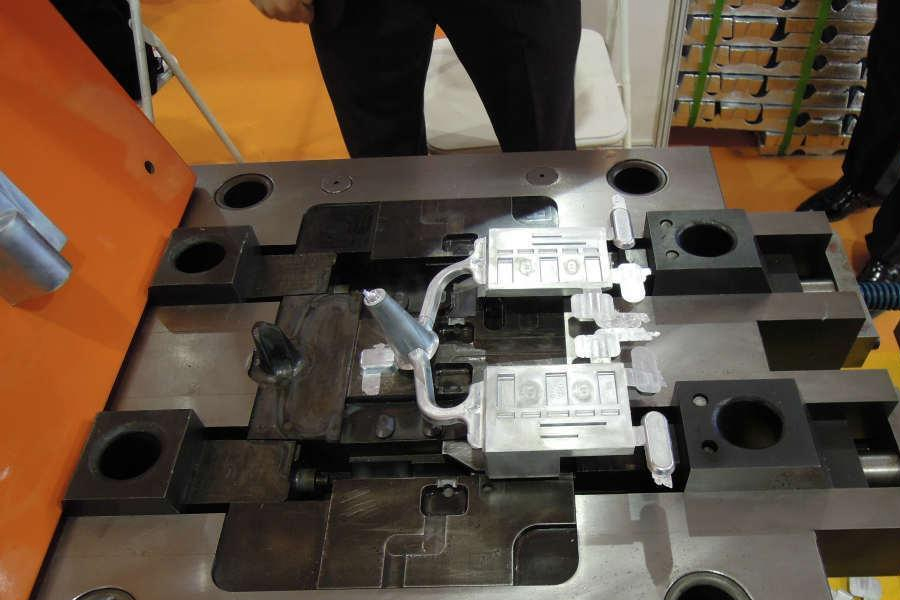
压铸铝合金
压铸铝合金自 1914 年投入商业生产以来,随着汽车工业的发展和冷室压铸机的发明,得到了迅速发展。压铸铝合金按其性能可分为中低强度(如中国的 Y102)和高强度(如中国的 Y112)。目前,在工业应用中使用的压铸铝合金主要包括以下系列:Al-Si、Al-Mg、Al-Si-Cu、Al-Si-Mg、Al-Si-Cu-Mg、Al-Zn 等。
压铸铝合金机械性能的提高往往伴随着铸造工艺性能的降低。由于压铸件高压快速凝固的特点,这一矛盾在某些方面更为突出。因此,一般压铸件很难进行固溶热处理,限制了压铸铝合金机械性能的提高,虽然充氧压铸和真空压铸是提高合金机械性能的有效途径,但仍难以广泛应用。因此,新型压铸铝合金的开发和研究一直在进行。
先进的压铸技术
早期卧式冷室压铸机的压铸工艺只有一种速度将熔融金属推入模具,压射速度仅为 1m~2m/s 。在这种工艺下,铸件内部气孔多,结构疏松。不久后将改进为两阶段注塑。注塑过程简单分为慢速和快速两个阶段,但快速速度只有 3m/s。以慢速和快速提高压铸件的密度
之后,又增加了一个增压阶段,成为慢速喷射、快速喷射和增压三个阶段。这就是经典的三级注塑。20 世纪 60 年代中期,这种三段式压射被普遍推开,快速压射阶段的速度提高到 5m/s。在此后的 40 年中,世界上主要的压铸机制造商都对压射工艺进行了研究和实验,并开发出了一些新工艺,如 70 年代的抛物线压射系统、80 年代的无毛边压铸系统以及 90 年代的无毛边压射系统,其中一些工艺从三级压射中重新分解出了各个阶段,是这种经典三级压射不断发展的延伸。现在,喷油速度和压力已由原来的手动手轮调节控制改为电脑控制。近年来,为了解决压铸件的气孔和缩孔问题,人们可以生产出高强度、高密度、可焊接、可热处理、可扭曲等各种高要求的压铸件。除了继续改进真空压铸外,还开发了挤压铸造和半固态压铸等新技术,一般称之为 "高密度压铸法"。
真空压铸技术
真空压铸法是将型腔中的气体抽空或部分抽空,降低型腔中的气压,以利于合金熔体中气体的充填和排除,使合金熔体在压力作用下充满型腔,并在压力作用下凝固,获得致密的压铸件。与普通压铸法相比,真空压铸法具有以下特点:
最近,真空压铸主要用于去除型腔中的气体,主要有两种形式:
使用真空压铸时,模具排气管位置和排气管面积的设计非常重要。排气管有一个 "临界面积",它与型腔中抽出的气体量、抽气时间和填充时间有关。当排气管的面积大于临界面积时,真空压铸效果明显;反之,则不明显。真空系统的选择也非常重要。要求在真空泵关闭之前,型腔内的真空度能保持到充填完成。
充氧压铸技术
压铸件孔隙中的大部分气体是 N2 和 H2,几乎没有 O2。主要原因是 O2 会与活性金属反应形成固体氧化物,这为充氧压铸技术提供了理论依据。充氧压铸是在压铸前向型腔中充入氧气,以取代型腔中的空气。当熔融金属进入型腔时,一部分氧气从排气槽排出,剩余的氧气与熔融金属反应生成分散的氧化物颗粒,在模具中形成瞬间真空,从而获得无气孔的压铸件。在充氧压铸过程中,型腔内的真空是通过化学反应产生的。为确保生产安全,应严格控制充氧量,并降低型腔压力,使之与充氧压力相匹配。将真空压铸与充氧工艺相结合,使型腔处于负压状态,可以获得更好的效果。在熔融金属填充工艺中,熔融金属应在分散喷射状态下填充。流道尺寸的大小对充氧压铸的效果也有很大影响。适当的流道尺寸既能满足熔融金属以紊流形式填充模具,又能防止熔融金属温度下降过快。氧化物的高度分散分布不会对铸件产生不利影响,但可以提高铸件的硬度,细化热处理后的结构。充氧压铸可用于与氧气发生反应的铝、镁和锌合金。目前,充氧压铸可生产各种铝合金铸件,如:液压变速器壳体、加热器热交换器、液压变速器阀体、计算机支架等。
对于需要热处理或组焊、高气密性和在较高温度下使用的压铸件,充氧压铸具有技术和经济优势。
半固态压铸技术
半固态压铸是一种在凝固过程中搅拌液态金属,在一定冷却速度下获得固相成分约为 50%或更高的浆料,然后利用浆料进行压铸的技术。半固态压铸技术目前有两种成形工艺:流变成形工艺和触变成形工艺。前者是将液态金属送入专门设计的注塑机料筒,通过螺杆装置剪切冷却成半固态浆料,然后进行压铸。后者是将固态金属颗粒或废料送入螺旋式注塑机,金属颗粒在加热和剪切的条件下转化为浆料,然后进行压铸。半固态压铸成型工艺的关键在于半固态合金浆料的有效制备、固液成分比例的精确控制以及半固态成型过程的自动化控制的研发。为了实现半固态成形的自动化生产,美国科学家认为需要大力发展以下技术:
挤压压铸技术
挤压铸造也称为 "液态金属成型"。该铸件具有致密性好、机械性能高、无浇冒口等特点。我国一些企业已将其应用于实际生产中。挤压铸造技术具有很好的技术优势。它可以替代传统的压铸、挤压铸造、低压铸造、真空压铸等工艺,并兼容差压铸造、连铸连锻、半固态加工等流变铸造工艺。专家认为,挤压铸造技术是一项前沿新技术,横跨多个工艺领域,内涵丰富,创新性强,极具挑战性。
电磁泵低压铸造
电磁泵低压铸造是一种新兴的低压铸造工艺。与气体式低压铸造技术相比,其加压方式完全不同。它采用非接触式电磁力直接作用于金属液,大大减少了因压缩空气不纯和压缩空气中氧分压过高而引起的氧化和吸入问题,实现了铝液的平稳输送。而充填式则可防止湍流造成的二次污染。此外,电磁泵系统完全采用计算机数字控制,工艺执行非常精确,重复性好,使铝合金铸件在成品率、机械性能、表面质量和金属利用率等方面具有明显优势。随着对该技术的不断深入研究,该工艺已日趋成熟。
压铸设备的发展
经过近几年的发展,我国压铸机的设计水平、技术参数、性能指标、机械结构和制造质量都有了不同程度的提高,特别是冷室压铸机,已由原来的全液压合模机构改为托格式合模机构,并增加了自动上料、自动喷涂、自动取料、自动切边等功能。电器也由普通电源控制改为计算机控制,控制水平大大提高,有的已达到或接近国际水平,正向大型化、自动化、模块化迈进。在此期间,国内新的压铸机企业不断涌现。香港力劲公司就是其中的典型代表。该公司已开发出多款国内领先的压铸机型。例如,卧式冷室压铸机的最大空气注射速度为 6m./s(1997 年)和 8m/s(2000 年初)、镁合金热室压铸机(2000 年初)、匀加速压射系统(2002 年)、最大空气压射速度 10m/s 和多级压铸系统(2004 年 6 月)、压射系统实时控制(2004 年 8 月)以及锁模力达 30000kN 的大型压铸机(2004 年 7 月)等。近年来,上海压铸机厂、灌南压铸机厂等骨干企业相继开发出最高空气压射速度超过 8m/s 的卧式冷室压铸机和锁模力超过 10000kN 的大型压铸机;2005 年广东顺威亿力精密冲压技术有限公司投产将生产出最高空气压射速度超过 8m/s 的卧式冷室压铸机和锁模力超过 10000kN 的大型压铸机。2005 年广东顺威亿力精密冲压技术有限公司投产,将生产 10000kN~30000kN 的大型压铸机。由此可见,中国正在形成强大的具有自主知识产权的压铸机制 造业。
中国压铸机总数为 12,000 台,其中国产压铸机约占 85%,进口压铸机约占 15%。近两年,中国压铸机年销量超过 1800 台,其中 10000kN 及以上压铸机占 2%,8000kN~9000kN 压铸机占 5%,5000kN~7000kN 压铸机占 13%,3500kN~4000kN 压铸机占 20%,3000kN 及以下压铸机占 60%。在 3000kN 以下的压铸机中,热室压铸机约占 30%。中小型压铸机仍以国产设备为主。国产压铸机与国外先进压铸设备的差距主要表现在以下几个方面:
压铸模具的发展
最早的压铸模芯材料使用 45% 钢、铸钢和锻钢等。由于其高温抗冲击性差,所以当时的使用寿命很短。随着科学技术的发展,压铸模芯材料发生了重大变化。如今,高温、高强度的 3Cr2N8VH13 热锻钢被用作芯材。近年来,还使用了进口的 8407 材料,大大提高了模具的使用寿命。特别是近年来,国内大多数工厂都采用了计算机设计和模拟填充技术,大大提高了压铸模具的生产质量,并大大缩短了生产周期。中国模具工业发展迅速。1996 年至 2004 年,模具产量年均增长率为 14%。2003 年,压铸模具产值为 38 亿元。
目前,中国国产模具对市场的满足率仅为 80%左右。其中,以中低端模具为主。大型复杂精密模具在生产技术、模具质量和寿命、生产能力等方面都不能满足国民经济发展的需要。
研发方向
汽车、摩托车行业及汽车配件的消费和配套产品的需求,为压铸件的生产提供了广阔的市场。压铸铝合金在汽车上的应用也将不断扩大。在未来的压铸技术研发中,铝合金压铸的深化仍将是压铸技术发展的主要方向。为适应市场需求,今后应进一步解决以下问题: