本文首先分析了铝合金型壳的结构和压铸工艺,并利用 UG 软件完成了铝合金型壳压铸模具的设计。实践证明,设计的压铸模具合理,获得的铸件表面光洁,产品质量符合要求。
铝合金后壳压铸件的结构和工艺分析
压铸工艺参数设计
2.1 压铸机的选择 选择压铸机时,首先必须确定锁模力。锁模力有两个作用:一是用来平衡背压,达到锁定分型面的目的;二是防止熔融金属飞溅,达到目标尺寸精度的目的。在设计的铸件中不存在局部膨胀力,因为该模具没有侧芯牵引(压铸件没有侧孔和暗槽)。因此,F lock≥KF main=1. 25×1288.352=1610.44kN 。根据上述计算,可得出夹紧力值和铸件重量。根据这两个主要因素,对压铸机进行选型,最终选定的机型为:卧式冷室压铸机(2500kN)--J1125 型,主要参数:
2.2 压铸压力 压铸压力是压铸过程中的主要参数之一。因此,掌握压铸过程中金属液的压力变化,合理控制压铸过程各阶段的压力具有重要意义:
2.3 压铸速度 压铸速度的选择包括以下两个方面:压射速度选择和充填速度选择。这两个速度的选择非常重要,直接决定了铸件的内外质量和轮廓清晰度。选择充填速度时应考虑的因素:
具体选择:
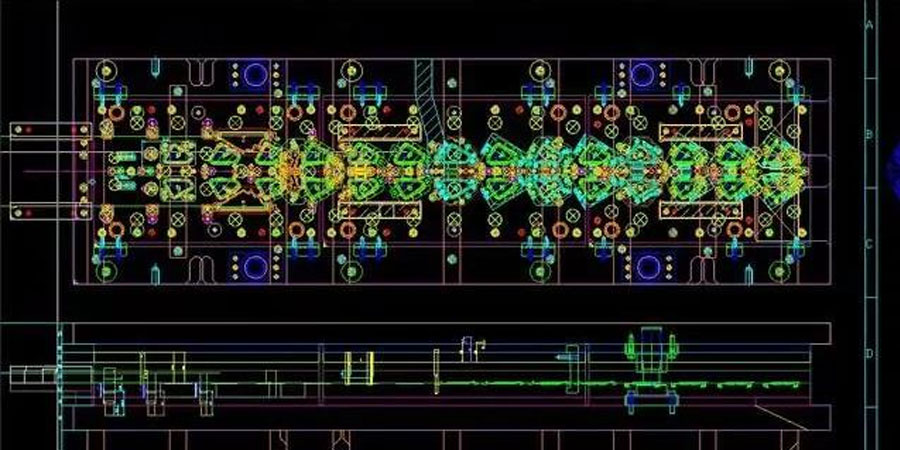
2.4 压铸时间 压铸时间由所需时间的三个部分组成:充填时间、保温时间和压铸件在压铸模具中的停留时间。压力、速度、温度、熔融金属特性以及铸件结构(主要是壁厚和容积)和模具结构(尤其是浇口系统和排料系统)等因素共同决定了这一结果。填充时间大多在 0.01 至 0.2 秒之间。其长短由铸件的大小和结构的复杂程度决定:结构简单、体积大的铸件,充型时间相对较长;结构复杂、壁厚较小的铸件,充型时间较短。经过实际测试,充型时间设定为 0.2s 左右,这对于本文设计的中小型铝合金压铸件是合理的。保压时间的作用是:注射冲头有足够的时间对未凝固的金属施加压力,使结晶过程在压力作用下进行,从而提高进给量,成功获得致密结构。影响时间长短的因素有:所选合金的熔点、结晶温度范围和铸件壁厚。熔点高、范围大、壁厚大的铸件需要较长的时间,2~3s;当确定的时间太短时,会出现缩孔,但如果保温时间延长,则影响不大。一般保温时间范围为 1~2s。本设计中铸件的平均壁厚为 3mm。考虑到其结构和合金特性,选择 3s 作为保温时间。5 压铸温度 保证铸件合格的主要工艺参数--熔融金属的浇注温度和模具的工作温度。影响因素很多:铸件结构、壁厚、充填压力、速度、合金种类等。必须综合考虑上述参数,确保压铸温度稳定在合理范围内,并提供良好的充型条件。如果浇注温度不在合理范围内,产品质量就会下降,甚至不合格:
浇注温度过高--会造成冷却过程中收缩过大,产品容易出现裂纹、晶粒变大、力学性能变差,甚至造成粘模,降低模具寿命;
浇注温度过低--导致冷障、表面花纹和浇注不足等缺陷。为了获得合格的铸件,除了浇注温度、压力外,还应同时考虑压铸模具温度、充填速度和铸件所选用的合金。压铸件由铝硅合金制成。根据其流动性和模具特性,选择 620℃作为压铸温度。
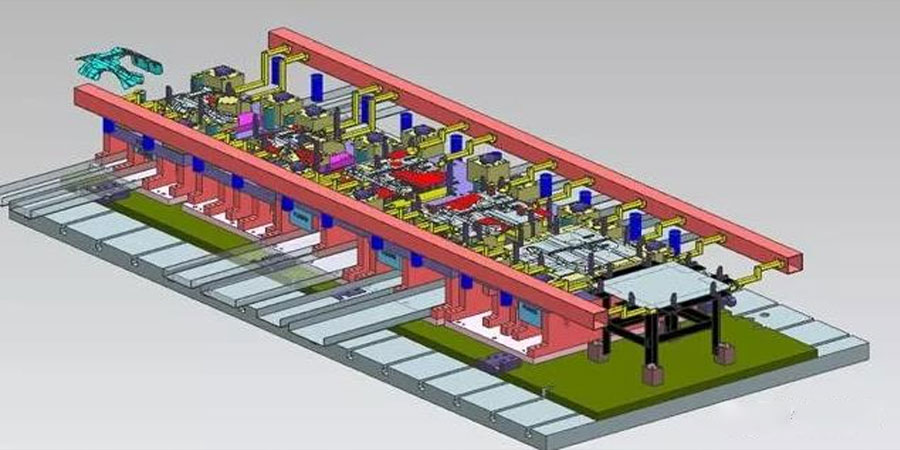
背壳压铸件的结构设计
3.1 分型面的确定 该零件结构简单。根据分型面的选择原则,应选择最大的凸出部分,如图 2 所示。
3.2 门控系统的设计 门控系统由四个部分组成:
具体设计:
3.3 溢流槽和排气系统的设计 对溢流槽进行结构设计,综合考虑各种因素,选择的截面形状为梯形(图 4)。合理的结构具有以下功能:
3.4 顶出系统的设计 在压铸过程中,完成一个完整的成形循环后,需要打开模具以取出压铸件,这时会发现包裹的压铸件位于冲头的一侧,需要将其取出。这项工作需要额外的顶件机构来完成。顶出系统在模具结构设计中占有重要地位。顶出系统有三个主要部分:
设计系统中的限位装置:
3.5 计算成型部件的尺寸
3.5.1 型腔和型芯尺寸:
3.5. 2 计算中心距和位置尺寸: 式中 L-成形件中心距和位置的平均尺寸(毫米); L-压铸件中心距和位置的平均尺寸(毫米)。
3.6 冷却系统的设计选择了一种高效且易于控制的模具冷却方式--水冷,以获得高质量的铸件和较长的模具寿命。水冷却的冷却效果取决于型腔中冷却通道的布局:
3.7 压铸模具总装配图 绘制后壳盖压铸模具总装配图(图 6)。压铸模具由固定模具和活动模具两部分组成。固定模具固定不动,位于固定模板上。活动模具随从动模板移动,位于从动模板固定板上。通过活动模具相对于固定模具的移动,实现模具的闭合和打开。
合模:二者闭合形成型腔,利用浇口系统在高压下向型腔填充熔融金属;②开模:二者保压后分离,由顶出机构完成将产品顶出型腔的任务。
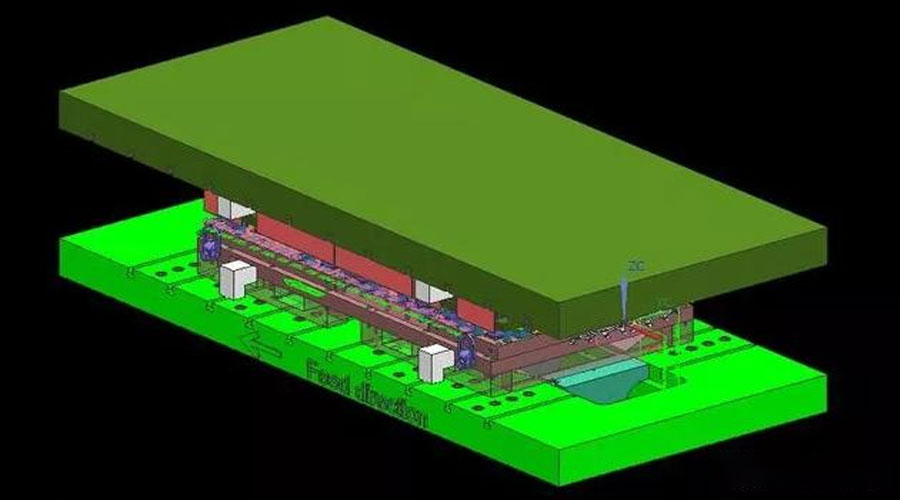
本文利用 UG 软件对后盖零件进行建模,完成了后盖零件的工艺分析、压铸工艺参数和模具结构设计。型腔受以下因素的限制:制造、工艺和生产效率等。综合考虑以上因素,确定了较为合理的一模四腔布局。实际生产表明,选择压铸比压为 90MPa,压铸速度在 20-90m/s,压铸时间为 0.2s,保温时间为 3s,压铸温度为 620℃,得到的后壳闷盖表面光滑,符合产品质量要求。