铸造流道损失
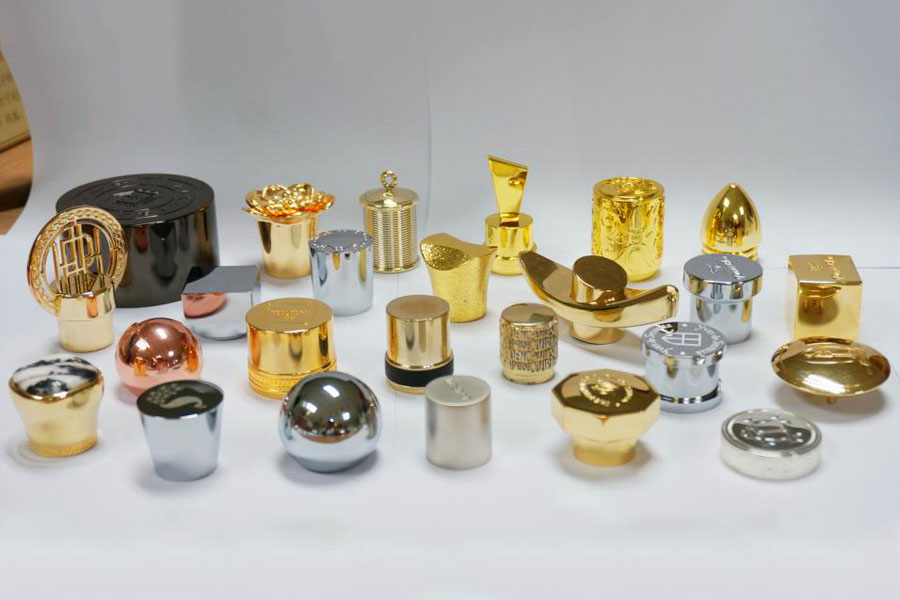
了解压铸的人都知道,流道或剩余材料是铸件的一部分。虽然没有利润价值,但在生产过程中无法避免。这部分成本一般只按铸件成本的固定比例计算。同时,考虑到锌合金的可回收性,最常见的局部处理方法是实时抛回机炉重熔。由于需要控制质量问题,使用中央熔炼炉回收流道或废品逐渐被业界接受(图 1)。至于炉渣,规模较大的压铸厂可自行回收,一般会将剩余材料卖回给原材料供应商,以换取新材料。锌材料在当地的回收价格一般是新材料价格的 50% 至 70%。如果没有良好的环境条件,锌渣处理很容易造成空气污染。
以一台 160 吨热室压铸机为例。每次至少生产 150 克流道(不包括溢流井),假设三班倒,生产周期为 20 秒,机器利用率为 80%,年产量为 口流道可达 190 吨。另一个例子:用一台 80 吨的机器每次生产 100 克流道,假设相同,但生产周期改为 12 秒,流道年产量超过 210 吨。
可见,转轮设计会影响成本的重要性。
各种回收方法
在回收方法中,直接将流道扔回炉内是最简单、最节省成本的方法。回流熔炼刚产生的流道不需要预热,减少了储存空间,但熔融材料的质量难以控制,其中熔渣较多,炉温难以控制,合金成分无法得知;更重要的是,它靠的是操作人员的手艺,比如新材料的配比、观察锅炉水的变化等,而工作人员把溢流井、闪蒸炉等放入炉内,不仅会使情况变得更糟,这种直接熔化废料的方法还藏污纳垢。缺陷率高、模具设计和压铸参数不稳定等问题使管理者无法进行有效的改进。这种方法不适合生产表面质量要求高的铸件,而且很难准确计算流道损失成本。
中央熔炉回收喷嘴和次品已在产量较大的压铸厂中得到普及。其好处非常明显,即回收材料的集中处理可以提高熔炉效率,控制合金质量。如果熔融金属直接从中央熔炉送入熔炉,压铸机材料温度可保持稳定,熔渣也较少。如果配备自动进料控制装置,液位变化可降至最低。目前流行的中央熔炼炉分为几类:容量较大的铸铁坩埚炉、不锈钢坩埚炉和连续熔炼型非坩埚炉。锌液运输也分为几类:有天车式液料运输、地面小车式(无轨或有轨)保温炉(带加料装置)运输和保温槽式重力输送装置,它将熔炉与中心熔炉连接起来。其缺点是投资比较大,只适用于单一合金(小型坩埚炉在此不谈),车间占地面积大,小型压铸厂(五台以下)不适用,老车间改造和合作困难。因此,一般只有在新建厂房时才会重新规划。使用小型坩埚炉重新熔化浇口材料,由于缺乏规模效益,成本会高于中心炉,所以不作为计算参考。
熔化成本计算
只需以中央熔炼炉为参考,计算流道的熔炼成本即可。以一家拥有五台 80 吨或 160 吨压铸机的公司为例。假设设备投资为 50 万,分 10 年计算。每年处理约 1,000 吨流道回收料(实际情况应按新料比例熔化,纯粹方便计算重熔成本)。
每公斤浇口材料的熔炼成本为 0.93 美元。按以上五台机器计算,年产 1000 吨流道喷嘴涉及近 1000 万元。如果算上次品回收,这个数字就更惊人了(如 平均铸件重量 100 克,次品率 5%,周期 12 秒,年回收次品约 53 吨)。虽然加工量越大,熔炼成本越低,但环保和严格的质量控制成本在此不作计算。可见,浇口重熔的成本相当惊人,压铸厂必须将成本降到最低。因此,如何减轻浇口重量是控制成本的重要关键。
转轮费用分摊计算方法
精炼喷嘴的成本必须计入铸件的生产成本。最常用的方法是将所用材料乘以一个固定的百分比。例如,如果原材料价格为 10 美元/千克,而喷嘴熔炼成本为铸件重量的 3%,则在计算铸件材料价格时将使用 10 美元。这种方法虽然简单,但可能会导致成本计算出现偏差,掩盖水口回收的真实成本。现在可以用下面的例子进行比较:
如果以固定百分比计算:
如按实际回收成本计算:
这个差距看似很小,但以 20 秒为生产周期,机器利用率为 80%,三班制生产,每台机器每年生产 1 261 440 次。差距如下
如果采用固定比率法,则 A 和 B 的铸件成本相同,但实际上 B 的铸件成本更高。从这个案例中可以看出,使用固定比率法计算铸件 B 不仅低估了生产成本,还间接鼓励设计人员不要以减轻喷嘴流道重量为目标,而应推广应用实际成本法(见下表)。
为了减轻浇口的重量,比较常见的是采用短浇口(短喷嘴)设计,并减少模板的厚度。它使用较长的机器喷嘴(一般比普通喷嘴长 20 毫米),结合深腔浇口模具设计来减轻浇口重量。以下是一种新型热室压铸流道设计。
热室压铸流道设计
压铸流道是熔融金属从喷嘴流入模腔的通道。它由浇道和流道的分支组成。由于需要固定铸件并方便脱模,浇道必须具有一定的倾斜度。同时,活动模板上的分流块可以减小浇道的厚度;在分流块上增加冷却水道,有利于模具热量的平衡,缩短冷却时间,并将铸件拉出和顶出。澳大利亚联邦科学与工业研究组织(CSIRO)在 20 世纪 70 年代初进行的一项研究发现,在误差可接受的情况下,锌合金液在压铸情况下可归纳如下:
液体表现为不可压缩流体
符合流体力学的一般原理
高雷诺数表明流动过程是湍流。
根据上述研究成果,熔融金属的理想流动状态应为
1.流道部分为圆形
由于圆周/面积比最小,圆形截面管道的表面电阻最小,因此压力损失也最小。与相同的梯形截面积相比,圆周面积减少了 20% 以上。
2.流动管道是直的
弯曲的管道会产生偏流,在熔体中混入气泡,造成压力损失。特别是当弯曲半径/管道直径比小于 1 时,压力损失会迅速增加。
3.就液体流量而言,流道剖面逐渐缩小
管道剖面的快速变化,无论是变大还是变小,都会造成较高的压力损失和涡流。最好的解决办法是逐渐缩小管道轮廓,以补偿管道表面造成的阻力损失。