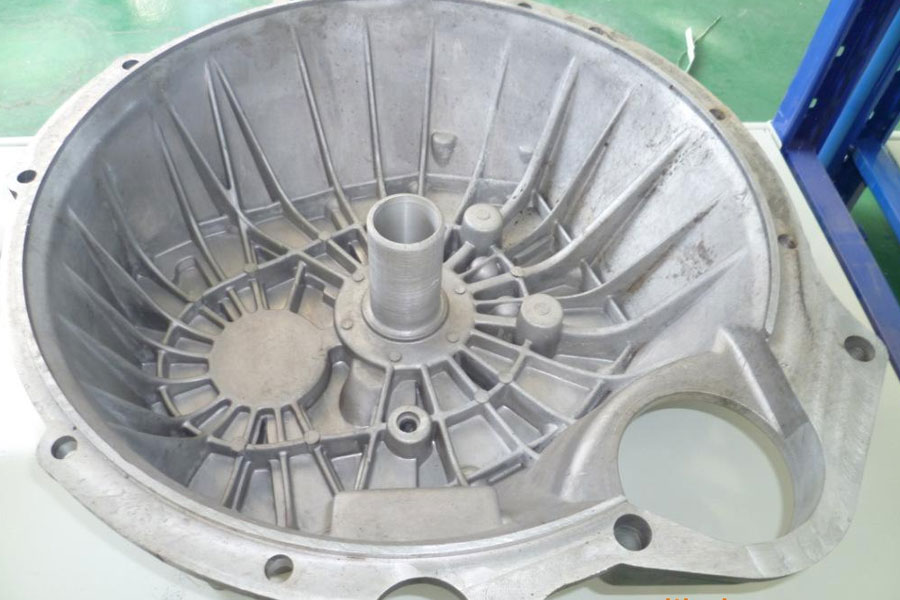
发动机缸体的设计正朝着重量更轻、结构更复杂的方向发展。由于铝合金密度低、铸造性能好,常用于生产形状复杂、壁薄、中等载荷的航空航天和汽车零件。长安汽车江北发动机厂生产的一系列发动机缸体采用优质铝合金(类似于国内品牌 YL113)在模具中高压铸造成型。该系列发动机的缸体为高强度薄壁复合铸件。缸体上的大部分孔都是用模芯预铸而成,这不仅对模具、压铸机等硬件设备要求高,而且整个生产过程的控制保证了交付 循环顺畅,对产品质量的提高也具有重要意义。
过程控制
在压铸生产的过程管理中,从铝液控制、模具控制、压铸过程控制和产品检验等方面稳定和提高产品质量尤为重要。
铝水控制
铸造铝合金的凝固缺陷严重影响铸件的性能,控制或消除凝固缺陷对提高铸件的成品率具有重要意义。随着对合金综合性能的要求越来越高,添加更多种类的合金元素以提高合金综合性能的研究也越来越深入,合金成分控制方法也变得越来越重要。工程中铸造铝合金常见的凝固缺陷,如偏析、热裂纹、微孔、缩孔等,需要从源头上加以控制。这些缺陷需要从源头上加以控制。为响应绿色制造,该机型的生产基地长安汽车江北发动机厂采用了铝熔体直供的方式,因此铝熔体直供的质量作为铝熔体是否满足要求的依据。使用真空样品制备装置检测铝合金锭的密度当量,使用光谱分析仪进行理化分析,并定期对机旁炉铝水进行 K 模检测,以监测铝合金的密度当量、化学成分和纯度。
霉菌控制
模具的管理、点检和维护是压铸工作的一部分,模具状态对产品质量非常重要。模具底座由铸铁制成。在注塑过程中,铝水自下而上流经压力室、浇口、横流道和内流道进行注塑。整个浇口系统采用封闭式设计,以减少铝水夹带。模腔内部用水打开,以平衡模具的温度场,缸体各部分同时凝固,铝水中的残余气体被分散和分布。浇注孔应尽可能用冷却水预浇注。可根据实际需要选择高压点冷却或往复水冷却方式。冷却水可直接到达浇铸销的顶部,这样顶部也能得到冷却。
在生产过程中,模具温度对产品和模具寿命的影响很大,温度过高容易发生粘模,铸件表面粗糙,还可能出现缩孔和裂纹。由于粘模,摩擦。
摩擦力的增加会使局部拉力加倍,从而使模具的局部运动不准确,损坏模具。模具温度控制一般根据铸件的壁厚和熔融铝流的分布来设定。模具不同部位的冷却水量和冷却时间均可调整。模具外的冷却也很重要,它与脱模剂喷洒的位置、方向和程序(时间)有很大关系。脱模剂的选择、比例和用量会影响模具的使用和产品的质量。模具维护分为预防性维护、预测性维护和点检。根据积累的经验确定模具的预防性维护周期,根据模具的状态和使用情况确定预测性维护时间,并在生产过程中进行日常检查。维护内容包括冷却系统(水、油、气)、真空系统、密封、型腔表面清洁等。
过程参数控制
压铸工艺的控制和优化是压铸生产的重要环节,直接影响压铸件的表面和内部质量。压铸工艺参数主要包括压力、速度和时间。
对技术控制参数进行定量控制,确保金属液的流动、凝固和热交换按设定方式进行,从而保证压铸件的质量。铸件的内部质量对压射参数的变化非常敏感。如果压力过低,铸件会出现大量气孔、缩孔等缺陷。如果压力过高,虽然铸件结构致密,但会产生较大的飞边和毛刺,从而损坏模具。.在生产过程中,还需要说明的是,从慢速注塑到快速注塑的转换点也非常重要。如果要过早转换,熔融铝会通过内流道,高速进入型腔。路线长,造成铝液紊流,卷入大量气体,容易形成一些不规则铸造缺陷;换型过晚,铝液在压力腔内停留时间长,温度低,容易产生冷障、浇注不足等缺陷。其实,从解剖学角度看,铸件存在气孔和缩孔是不可避免的。关键在于调整注射参数,使铝液中的气体尽可能有效地排出,剩余的少量气孔分散分布在内部。穿透部分会导致铸件渗漏。注塑速度包括冲压速度(即活塞在注塑缸中的移动速度)和填充速度(即浇口速度)。
充填速度是指熔融合金通过内流道的线速度,是保证压铸件质量的重要参数。压射时间由慢速压射时间、快速压射时间、加压时间、保压时间和模具停留时间组成。在生产中,保压时间和模具保持时间通常是一起控制和优化的,称为保压和模具保持时间。足够的保压时间和模具保持时间意味着压铸件在开模和顶出过程中不会变形或拉伸。这是产生裂纹的必要条件。这些重要参数需要每天进行监控,并根据铸件的状态不断优化。
产品检测
铸件检验包括外观尺寸检验、内部质量检验、铸前孔位检验、壁厚检验、缸套壁厚差检验、铸件热处理离线终检,根据人员安排和实际生产要求按固定频率和标准进行 铸件是否合格。生产过程中的抽检可以及时发现问题,快速做出反应,不会因为发现问题的时效性差而造成批量问题。
Sutras
压铸生产是一个相对复杂的过程,涉及到铝熔液的质量、压铸模具的状态、压铸机的参数、压铸过程和产品检验等。这些都与压铸件的质量密切相关。在压铸生产中,过程决定结果,良好的过程管理将带来稳定的产品质量,可控的批量生产将带来大规模的经济效益。