1 压铸件粘连的原因
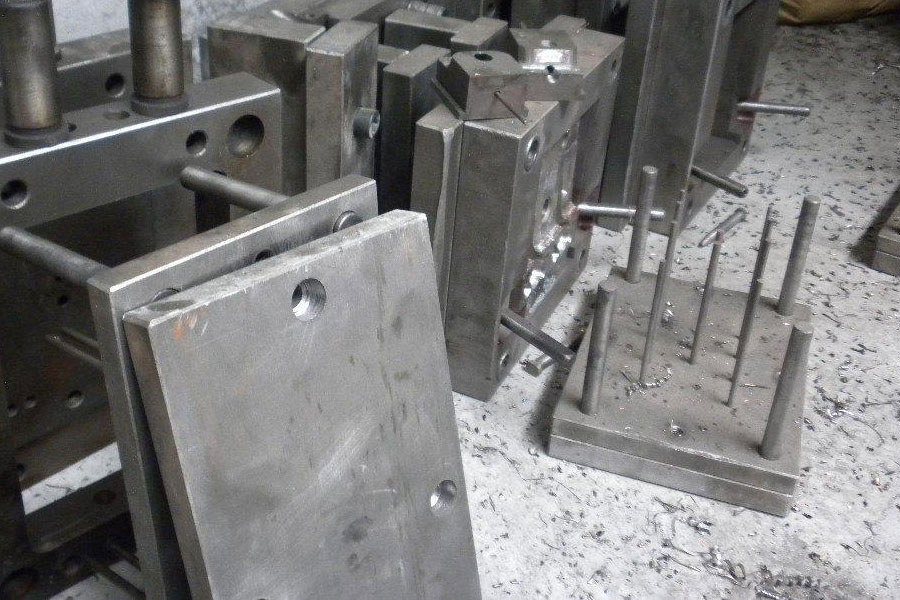
粘模缺陷对铸件的危害是:压铸件粘模后,轻者表面粗糙,影响外观粗糙度;重者铸件表面起皮、缺肉、拉伤、开裂,还可能造成铸件漏气,导致铸件成批报废。压铸件粘连的现象很多,粘连的基本原因如下。
1.1 压铸合金与模具钢的亲和性
压铸合金与模具钢的亲和力越大,就越容易熔化并相互粘合。压铸合金与模具壁粘合后,脱模阻力会增大,铸件在脱模时会产生应变。目测铸件粘连部位有拉丝痕迹,如表面粗糙、脱皮或缺料(注:与积碳相区别),粘连严重时铸件会撕裂损坏。模腔表面目测粘附的是层状铸造合金,颜色为白色。
压铸合金液注入或流出后撞击模壁或型芯,模壁或型芯的温度随之升高。在高温下,合金液与模壁的模具钢熔化并焊接在一起,造成相互粘连。合金液温度越高,注塑速度越快,模具温度越高,模具硬度越低,铝合金液与模具钢的亲和力就越高,就越容易发生熔化和焊接粘附。压铸合金粘附的模具表面脱模时,型腔表面与铸件表面受到挤压撕裂,会撕裂铸件表面,铸件表面会出现粘模应变。
压铸合金液在内流道中的填充速度越快,熔融金属流对模壁的冲击力就越大。熔融金属直接冲击型芯或型壁,冲击力转化为热能。不仅合金液的温度会升高,受冲击部位的模具温度也会大幅升高,这就大大增加了铝合金液与模具钢之间的亲和力。因此,模具中的流道受合金液高速冲击的部分最容易发生粘模。如果撞击到固定模具的侧面,则会增加铸件在固定模具侧面的包装力。
模具的硬度不够,脱模时模具表面会受到压铸合金的挤压而变形,或者模芯会弯曲变形,从而增加铸件的脱模阻力。
模具材料使用不当,当模具温度较高时,压铸合金容易粘附在模具表面。
1. 2 脱模角
模具脱模斜度太小(或无脱模斜度,或反向脱模斜度),模具侧面不平整(侵蚀、挤压、缺陷等),表面粗糙等。铸件在脱模方向受阻。铸件脱模时,铸件表面受到模具应变,铸件表面沿开模方向出现线状应变痕迹,即铸件深腔起始处的疤痕宽而深,而模具末端的疤痕逐渐变小甚至消失。整个面部的应变。
模具的固定成型表面过于粗糙,或有加工制造的痕迹,不够光滑,或加工抛光痕迹的线条与脱模方向不一致,或脱模方向的平整度差,这样的不良表面会由于脱模阻力增大而阻碍铸件的脱模,造成铸件表面有抛光或划伤的痕迹。这些刮痕是脱模方向上的线性沟槽,浅的小于 0.1 毫米,深的约 0.3 毫米。
1.3 铸件与模具的紧密度
铸件整体或局部收缩对模具的锁模力过大,或锁模力分布不平衡、不合理。此时,铸件会因粘模而变形、开裂或断裂,甚至铸件会粘在固定的模具上。或者出现铸件粘在动模上面出不来的现象。
对于压铸过程中经常出现的粘模现象,应详细分析其发生的原因。例如,压铸时铸件粘在固定模上,要检查铸件对固定模的紧固力过大的原因;检查铸件固定模一侧的外观,顺着脱模方向看,铸件表面是否有模具的痕迹。当粘模严重划伤或刮伤时,会产生较大的脱模阻力,使铸件部分或整个铸件在型腔中出不来,铸件会被粘住,造成粘模;严重时,不仅铸件会被撕裂损坏,型芯和型腔也会出现拉伤、裂纹、断裂等现象。压铸件的粘模现象在铝合金中最为常见。解决压铸件粘模缺陷的具体措施如下。
2 防止铸件粘在固定模具上的措施
2.1 防止铸件粘在压铸模具固定模具上的措施
在新生产模具的试模过程中,或压铸生产开始热模时,经常会出现压铸件粘模的现象。当压铸操作过程正常时,铸件粘模的主要原因不是压铸工艺,而应该是铸件结构设计、模具设计或制造的问题。虽然可以通过压铸工艺和喷涂调试进行补救,但补救效果一般且不太稳定,铸件粘连现象仍会发生。
如果铸件容易粘在固定的模具上,压铸前应充分预热模具,并在模具型腔涂上防粘模具膏和压缩空气,然后再开始低速注塑。吹气要均匀,每个压铸模具涂一次,试压铸 20 个左右模具,如果模具还是固定不动,说明模具有问题,需要修补。
对于已设计的铸件,铸件对固定模具的锁模力确实大于对活动模具的锁模力。有必要让铸件镶嵌在定模的一侧,以便顶出铸件,并让铸件的表面镶嵌在定模的一侧。留下顶出痕迹,或使顶出痕迹易于去除。这样,在设计模具时,铸件的顶出机构应设计在固定模具的一侧。
注意计算动模和定模的合模力。对于定模的填料力大于动模的填料力的铸件,或者定模和动模的填料力与动模的填料力相近的铸件,有可能会粘住定模,也有可能会粘住动模的铸件。在设计铸件或模具时,有必要改变铸件或模具的结构、拔模角度、表面粗糙度等。并尽量使动模的浇注力大于定模的紧固力。
对于在定模一侧有比较大的填料力的铸件,在设计新模具时,分型面应尽量选择在偏向定模的一侧,并尽量将铸件放在动模型腔内,以增加铸件的配对性。动模的紧固力。为了减小定模的紧固力,需要与铸件设计人员重新确定定模的脱模斜度,应尽量增大定模的脱模斜度,特别要注意修正或增大定模一侧的铸件。模粘连部位的脱模斜度。同时,适当减小动模的脱模斜度;特别注意纠正或减小顶针附近动模的脱模斜度。尽量在活动模具上设置型芯,或增加活动模具一侧的型芯长度。
要防止固定模在制造和抛光过程中产生影响脱模的缺口或粗糙表面;在试模后或压铸过程中,要纠正固定模型腔因挤压和碰伤而产生的变形;使用抛光剂或化学清洗剂清除合金 如果不及时清除定模表面的附着痕迹和模具上的合金附着物,时间长了,粘模现象会越来越严重;更好地抛光定模型腔侧壁的粗糙表面。但固定模打磨成镜面后,不利于涂料的附着。开模时,铸件与模具之间会产生紧密的真空间隙,增加了脱模阻力,因此固定模深腔底部无法打磨成镜面。.对于已经氮化的模具,抛光时要小心,防止损伤表面的氮化层,防止越抛光越粘模。
改造流道,适当改变流道的位置、尺寸和充填流向,以消除或减少因流道对固定模具的冲击而产生的侵蚀和粘模缺陷。例如
火花冶金法喷涂碳化钨微粒层,金属钨微粒与基体金属不会脱落,可提高模具表面的防粘性能,如在压铸模具表面沉积 2 至 4 微米厚的涂层,其硬度可达 HV4 000~4 500,工作温度可达 800℃。
为了将铸件拉到活动模的一侧,可从顶出杆的头部修出一个楔形倒钩(钩长 5-8mm,铸件厚度为 1-2mm,见图 1),使压铸的倒钩手柄 将铸件拉到活动模的一侧,然后取下铸件上的倒钩。为了增加铸件对动模的紧固力,对于铸件上需要精加工的部位和不影响外观质量的部位的侧表面,可以增加相应模具部位的表面粗糙度,以增加铸件对动模紧固力的作用。更明显
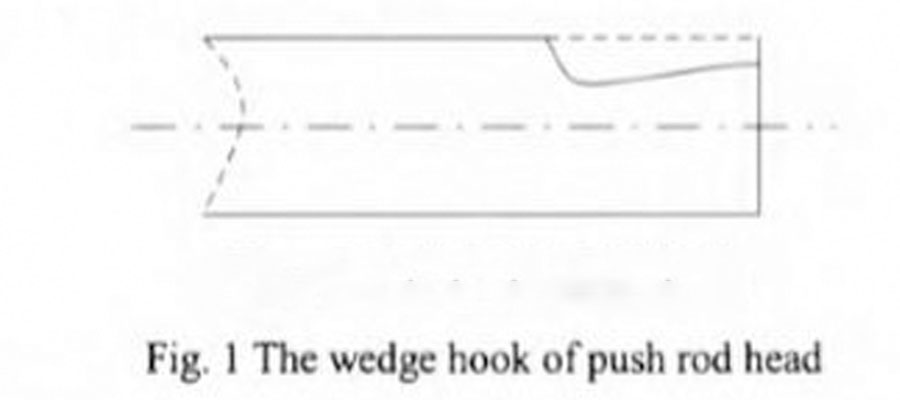
为了增加活动模具的紧固力,可以适当使用拉杆(见图 2):
对于定模一侧的浇注力大于动模一侧的浇注力的铸件,为了使铸件能顺利地从定模中顶出,设计了顶出板、顶出杆和复位杆,使铸件能像动模一样顶出。可以在定模的一侧加装油缸或弹簧,在开模的同时推动定模上的顶板和顶出杆将铸件顶出。顶出板后面有一个弹簧。开模时,固定模顶出杆从分型面顶出。合模时,利用活动模具分模面推动四根复位杆,推动固定模具推板和顶出装置复位。
为了利用顶出杆将铸件从固定模中顶出,还可采用与三板两件式分型模类似的挂钩杆、冲击块和滚轮机构(见图 5,图中铸件、顶出杆和复位杆均未示出),依靠开模动作带动固定模顶出推板将铸件从固定模中顶出。其结构如下针对给定模具设计顶针顶出铸件的顶出结构,让定模的顶出板 5 伸出定模模型 6,在动模 1 上设置四个(或两个)挂钩。合模时,四个(或两个)挂钩杆 4 延伸至固定模 6 的一侧。挂钩杆 4、撞块 7、弹簧 3 和滚轮机构 8 用于使四个挂钩杆 4 与固定模具 6 的顶推板通过挂钩连接。开模时,动模拉杆 4 钩住定模顶出推杆 5,定模推杆推动顶出推杆 5 移动,将铸件从定模顶出。此时,铸件和动模同步移动。移动到一定行程后,利用冲击块、滚轮、弹簧机构使四根钩杆的钩子与定模顶出推板脱开,定模顶出推板停止移动,合模时也使用动模分型面。将四根复位杆推回固定脱模推板,使固定脱模器回到原位。
2.2 压铸过程中防止铸件粘在固定模具上的措施
模具上的喷涂层、合金液的流动冲击速度和模具温度是影响铸件粘连的主要因素。
脱模剂的品种、质量、浓度、喷涂位置、喷涂时间和用量都会影响铸件Ⅲ的粘着情况。利用脱模剂的喷涂量来调节铸件在动模和定模两侧的脱模效果。为防止铸件粘在定模上,可适当减少动模上喷涂脱模剂的时间和用量。动模上喷涂的涂料要薄而均匀,但不能漏涂。增加定模上脱模剂的喷涂量,以降低定模表面的温度,特别是对定模上有拉伤的铸件表面和有拉痕的表面,要增加喷涂量。当定模侧面无固定位置或无定模痕迹时,注意适当增加涂料喷涂量。
在有拉丝痕迹的模具表面,在压铸后喷漆前涂上防粘模浆,使防粘模浆在高温下烧结到模具表面,使合金液与模具表面之间形成一层较厚的隔膜层,能起到较好的脱模作用。
正确调整和控制模具温度。要分析铸件致密性和粘模应力、模具温差和铸件收缩率,以及模具温度与合金收缩率和模具致密性之间的关系。如果铸件表面有粘模应变,在保证铸件表面质量的前提下,尽量使用较低的模具温度。如果铸件本身有较大的紧模力,则尽量使用较高的模具温度,这样可以减少铸件在脱模过程中的收缩,即当铸件还没有达到较大的紧模力时,就会开始脱模。
相对降低活动模具的温度,促进铸件的收缩,可以增加铸件与活动模具的密合度;相对提高固定模具的温度,减少铸件的收缩,可以降低铸件与固定模具的密合度。增加动模冷却水的流量,可以降低动模的模温;减少或关闭定模冷却水的流量,可以提高定模的模温。一般来说,压铸铝合金铸件时,应在开模后 1 至 3 秒内测量动模型腔的表面温度。表面温度不应大于 300℃,最好为 (240±40)℃;喷涂后合模前 1 至 3 秒内测量定模型腔的表面温度,不应低于 140℃。
浇注温度与模具温度一样,会改变铸件的收缩率和填料的密实度。提高浇注温度和缩短开模时间可以减小填料力,但会增加合金液与模具钢之间的亲和力,造成铸件厚壁部分粘连的可能性。
3 防止铸件粘在移动模具上的措施
3.1 压铸模具方面防止铸件粘在活动模具上的措施
铸件粘在活动模具上的主要原因是铸件对活动模具的紧固力过大,顶杆的顶出力不足。如果顶出力不够大,则需要增加压铸机顶出油缸的液压或顶出速度。如果顶针直径太小或顶针数量较少,顶针强度不够,顶针可能会弯曲或断裂。
如果铸件粘在活动模具上的力较小,铸件脱模时应变较轻,或模具表面粗糙造成的阻力较小,但铸件顶出时会变形,应打磨粘模部分,氮化或增加脱模剂的喷涂量,以减小脱模阻力。.如果铸件粘在活动模具上的力很大,铸件脱模时严重拉伤,铸件顶部断裂或脱开,或铸件被顶出装置顶出,则应适当增大浇注角度。改进铸件或模具的设计,消除造成铸件粘模和影响收缩的不合理结构。
为防止因铸件顶出力不均匀而造成粘模拉伤,压铸机推动脱模板的四根推杆长度必须一致,相差不得大于 0.20 毫米;压铸机推杆与顶出杆的位置应均衡合理,不得偏离模具型腔中心,也不得偏离压铸机顶出油缸中心。
如果抽芯和顶出设置不平衡,铸件将受力不均并发生偏移。如果压铸机液压顶出缸的推杆长度不一致,铸件的顶出力不均匀,或推杆位置布置不当,铸件在顶出时就会发生偏斜。改进措施如下修改模具结构,调整抽芯机构和顶出杆的位置,使铸件的顶出力均匀,确保铸件被平行均匀地推出;调整压铸机的顶出机构、推杆位置和数量(最多使用 4-6 根推杆),使模具顶杆和铸件受力均匀;合理增加顶杆数量,增大顶杆直径,合理安排顶杆位置,确保顶出平衡。
如果平面零件和薄壁铸件的抗变形能力不足,则应增加顶针的数量和直径。也可以在顶出位置增加一个小凸台,让顶针靠在铸件的小凸台上。较大的顶出力面积可使铸件受力均匀。
使用优质模具钢,这样当模具温度较高时,压铸合金不易粘附在表面。使用优质模具钢,模具表面不会过早形成微裂纹,这也是消除合金粘连的基础。
模具硬度不足或脆性大时,合金液容易粘模。有必要检查模具硬度是否合理,同时检查热处理工艺,防止模具钢脆化。能承受内流道冲击的模块、模具镶件和所有型芯的硬度要比模腔模块的硬度高 HRc3~5。当模具设计确认没有问题,而铸造模具粘模应变仍难以消除时,必须采用氮化、KANI 7C、镀钨、PVD 纳米镀钛等表面处理措施来提高模具表面硬度。
对于模具型腔的表面,一般用油石和砂纸打磨。如果用气动工具打磨粘模部分,一定要注意不要损伤模具,以免损坏模具表面的氮化层,否则越打磨越粘模。案例。在清理粘模或粘帘的非型腔部分时,可以用铲刀铲除凹凸,然后用砂纸轻轻打磨。不要将凹坑舀出,否则会造成更严重的粘连。注意任何时候都不要用凿子清理模腔内的粘模,以免凿坏模腔。
3.2 防止压铸过程中铸件粘在移动模具上的对策
降低压铸机的高速注塑速度,或增加模具内流道面积,适当降低流道的填充速度。如果在不提高内流道充填速度的情况下增加内流道面积,可以缩短充填时间,减少内流道冲击产生的总热量,达到减少内流道冲击的效果。
适当降低铸造压力:对于薄壁零件和无气孔要求的铸件,可选用较小的压力,如40~55MPa;一般铸件选用55~75MPa;对于厚壁零件和有气孔要求的铸件,可选用较大的压力,如75~100MPa;必须使用较大压力时,可选用100~140MPa。铸造压力越高,铸件的机械性能越好,铸件与模具的紧密度也越高。如果出现粘模现象,有必要确认是否使用了适当的浇注压力。适当缩短开模时间(模具冷却时间),使铸件在较高温度下脱模,模具锁模力未达到最大值,从而降低铸件对模具的锁模力,减少粘模。
如果铸件的脱模角过小,最容易造成铸件粘模。因此,必须根据铸件的合金材料和尺寸结构选择合适的脱模角。发生粘模时,适当增大脱模角可以消除热冲击和收缩引起的粘模现象。如果铸件结构不合理,会导致铸件在收缩和冷却过程中各部分收缩不均匀,抗收缩能力不平衡。在可能和必要的情况下,改进铸件的设计结构,使壁厚均匀,如改变 断面厚度,尽量将厚部位设计成空心结构或筋连接结构;避免厚度差异较大的过渡部位;消除不合理的凸台、凸耳、加强筋等。在铸件凹角处增加铸件圆角或脱模角,也可防止粘模。
在模具内流道附近和合金液充满冲击型腔的部位、铸件壁厚较厚的模具部位以及铸件的凹角处,长时间容易受到合金液的影响。铸件会产生粘连和拉伤,因此应在模具的这些部位设置冷却水管进行水冷却。对于细长型芯冷却,应增加冷却水的压力。这些都能很好地降低模具温度,防止粘模。
如果压铸合金在铸件表面粘附在模具表面,表面会出现一些小气泡。针对这种现象,用砂布和油石打磨模具表面,模具又会被反复粘住,这并不能彻底解决问题。解决这种粘模现象的较好办法是对粘模表面进行喷丸处理,或在铸型粘模部位的表面做成宽 0. 2~0. 5 毫米、深 0. 5 毫米、间隔 2~5 毫米的网纹,可消除铸件表面的粘模缺陷。
流道收缩会导致铸件变形和粘模。应加长支流道的长度,减小支流道的面积;减少流道的宽度,加长道数;增加冷却水对模具流道的冷却,消除流道收缩对铸件的影响。
压铸铝合金液中的铁含量越少(如小于 0. 6%),铝合金液与模具钢的亲和力越大,越容易粘在模具上。适当增加铝合金液中的铁含量,可以更好地降低铝合金对模具的粘附性;一般要求压铸铝合金液中的铁含量控制在 0.6% 至 0.95%。这对于防止与低熔点金属混合造成的模具粘连是必要的。在使用母合金调整化学成分时,除镁、锌等个别金属外,不能在铝液中添加纯金属,以防止严重偏析造成粘模。
压铸合金的收缩率越大,不仅越容易粘模,而且高温强度也越差。有些合金的收缩率较大;合金的液相和固相温度范围越宽,合金的收缩率就越大。根据铸件的结构形状和复杂程度,如果收缩引起的粘模和变形难以消除,可考虑改用体收缩和线收缩小、高温强度高的合金;或调整合金成分(如铝)。当硅合金中的硅含量增加时,铸件的收缩率变小),降低收缩率;或对合金进行改性,在铝合金液中加入 0. 15%至 0. 2%的金属钛等晶粒细化剂,降低合金的缩孔倾向。
4 结论
造成压铸件粘连的原因有很多,解决粘连的措施也各不相同。本文具体提出了解决压铸件粘模缺陷的措施。我们应仔细观察和分析产生粘模的原因,并采取有针对性的措施。相应的对策可以有效解决模具粘模问题。