随着体育运动和科学技术的不断发展,人们的生活水平不断提高,对汽车的质量和实用性也提出了更高的要求。为了保证汽车的良好性能,保证汽车的实用性,提高汽车的设计工艺和质量。文章主要论述了对汽车铝合金压铸件质量的综合诊断与控制进行分析研究,为汽车生产厂家和设计人员提供有效的材料,促进汽车制造业的发展。
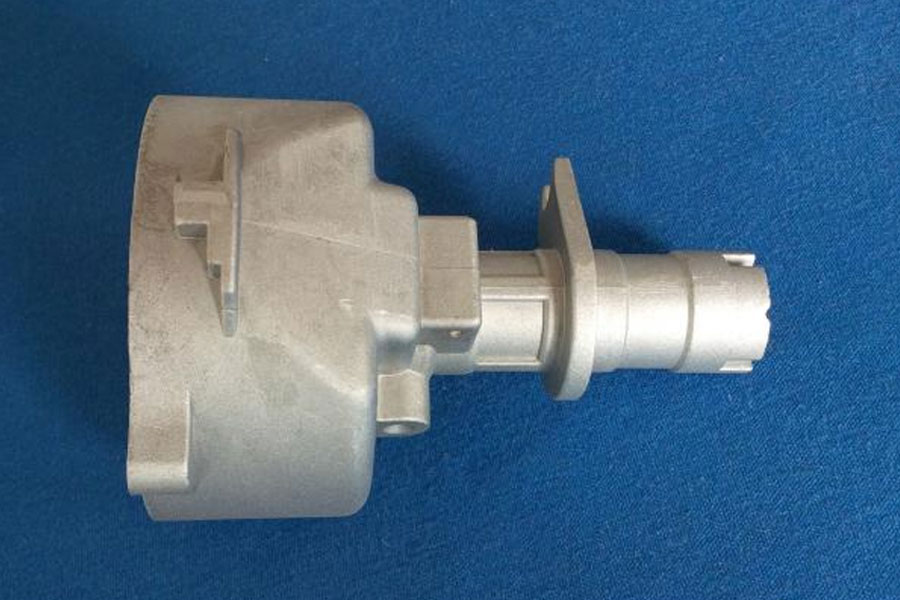
通过对汽车铝合金压铸件质量的综合诊断与控制进行分析研究,发现其存在以下弊端与缺陷。对于汽车铝合金压铸件来说,汽车缸体的环节比较多,尤其是缸体的头盖位置占用空间大,结构比较复杂。有些部位的加工环节和缸体表面不得有孔洞,严重影响了压铸件的质量。其次,由于外购零部件和材料、操作不当等原因。其次,由于外购零部件和材料、操作不当等原因,也会给汽车压铸件带来质量影响。为了提高汽车压铸件的质量,必须加大对上述弊端的重视程度,改进工艺设计环节和孔洞弊端。
全面诊断和控制汽车铝合金压铸件的质量
1.1 诊断缺陷描述
对于汽车铝合金压铸件整体来说,汽车缸体部分的链接比较大,尤其是缸体头盖的位置占据空间较大,结构相对复杂。有些部位的加工环节和缸体表面是不能存在孔洞的。对于那些允许孔洞存在的缸体表面,孔洞的分布较为分散,且对尺寸有严格的规范和要求。对于气缸盖环节,凸轮轴位置伴随着探伤。加工后,孔的尺寸必须满足监测要求,达到最低监测标准。对于这类零件,给设计和生产工作带来了很大的难度,严重影响了设计效率和生产效率。铸件的技术和工艺不能充分考虑到整个铸件的不同环节和位置,与生产环节和工艺设计环节的匹配性较差。有的坯壁伴有光滑特征,坯壁深度大,伴有空气污染问题。其次,还存在气孔连气穴、缩孔等缺点。
1. 2 过程综合诊断分析和图像模拟分析
外购零部件和材料、操作不当、工艺设计缺陷、机械装置的实用性等,都对汽车铸件的安全性有很大影响,导致铸件质量发生变化,严重的会导致铸件报废。这些因素都会对汽车铸件的安全性产生较大影响,导致铸件质量发生变化,严重时会导致铸件报废。上述因素都具有可变性的特点,因此对铸件质量的影响较大。任何一个环节的变化都会带来铸件质量的波动。要找到外部采购的零部件和材料、操作不当、工艺设计的疏漏以及机械设备的实际应用性等因素导致铸件质量变化的主要原因并不容易。面对这种情况,有必要加大对铸造设计和工艺环节的持续跟踪和调查。首先要对不同铸件的生产日期进行观察和分析,建立合理化的时间安排,确立以铸件质量为指导目标,并对以下缓解措施进行监控和持续观察。包括对铸件原材料、辅助材料、冶炼环节、铸件设计和工艺生产参数、铸件质量监控等环节的全面监控和跟踪[21。对于图像模拟分析,铸件的主要缺陷体现在齿轮室。这种缺陷的主要影响因素是气体变化和缩孔的影响,给孔洞带来很大的缺陷。对于铸件来说,产生的气体主要来自熔体内部和脱模剂产生的气体。铸造过程中产生的意外气体。溶液中产生的气体与铸件材料的类型和性能密切相关,与铸件的熔炼技术密切相关。
优化和改进措施
2.1 图像模拟管理和改进
对于铸件,产生的气体主要来自熔体内部和脱模剂。铸造过程中产生的意外气体。溶液中产生的气体与铸件材料的类型和特性密切相关,与铸件的熔炼技术密切相关[41。脱模剂产生的气体与铸造工艺设计环节的选择和铸件的压制环节模型密切相关。针对铸件发展中的这一缺陷,可以采用调整铸件冶炼工艺和调整喷涂工艺的方法进行改进和优化。铸件在压制过程中带来的气体弊端与金属液的运行形式有着密切的关系。铸件的胀缩弊端与铸件的温度和凝固密切相关。在明确铸件的设计方案后,可以对流道进行扩充设计和配置,设置排气管路和溢流设备,设置铸型的温度,设置压机的系数。在设计和配置压制件的系数和参数时,应考虑金属液在铸型体内的流动形式,考虑金属液的凝固情况,尽量减小型腔收缩值,尽量减小极限值。此外,在这一环节中还可以使用图像模拟进行分析。图像模拟法是分析铸件规律、了解其充型的主要方法。它为铸件缺陷产生的原因提供了科学依据。改变时序模型,以三角形的形式呈现,然后给出其技术和工艺的仿真系统,并分辨出 STL 文件的格式。识别完毕后,使用 Msgmasoft 软件开始划分网络。给其十万个网络节点,并配以铸件和浇注系统。经过对 Msg-masoft 软件的深入研究和分析,以及对其的实际应用,发现使用 Msgmasoft 软件具有实际的适用性,可以对铸造工艺模具进行改革和创新,为铸造模具和工艺的设计奠定理论基础。.
2.2 加强对溶解气体的管理
当定时齿轮在进行熔炼操作时,从齿轮室出来的炉料包括50%的铝沉积物和39%的炉料。因为在回炉操作过程中,水分和其他一些物质会不断增加,从而增加气体含量,这时要及时对物料进行处理和管理,降低熔融元素含量,在物料入炉前进行添加和清除。对于气体和液体,增加了对气体含量的监测和观察。同时,要改变和优化工艺流程,改进喷射技术,调整喷射管线,确保高效脱气操作,提高脱气效率。确保一百克铝材料的气体含量在 0.2 毫升左右。
2_3 提高工艺参数的合理性,优化铸造条件
关于工艺参数的合理性,首先要根据监测结果,对可能影响铸件的工艺参数和质量关系进行分析研究,在不改变浇注条件的情况下提高铸件质量。为了保证工艺参数的合理性,可以采用注射工艺来提高铸件的密实度、工艺中充填气体的压力等。从而提高铸造工艺的合理性。其次,要加大对铸造条件的重视程度,保证工艺的合理运行,加大对孔洞的重视程度,调整流道的大小,在液面交界处增加排气管。在铸件的实际生产和设计活动中,要加大对铸件孔洞的观察力度,看是否存在缺陷和弊端,观察其大小和扩散范围。这种对铸件的观察主要是为了监督铸件的实际适用性,看是否需要报废更新。对铸件的缺陷环节进行拦截,对缺陷部位进行再加工,确保其符合标准铸件的要求,提高铸件的实际适用性。对于成品铸件,要注意观察孔壁,看孔壁是否粗糙。对于孔壁比较粗糙的,主要表现为树枝的性质。在使用显微镜进行观察分析时,可以发现底部的连续性较好,同时伴有幼虫的收缩和松动。
结束语
要治理汽车铝合金压铸件的质量缺陷,首先要加大对溶解气体的管理,改变和优化工艺,提高工艺参数的合理性,优化铸造条件,对铸件进行监控和观察,看是否需要报废和更新。对有缺陷的零件进行再加工,确保其符合标准铸件的要求。对铸件时序性能的主要缺陷进行图像模拟和分析,可以采用调整铸件熔炼工艺和调整喷涂工艺的方法。