铝合金铸造工艺性能
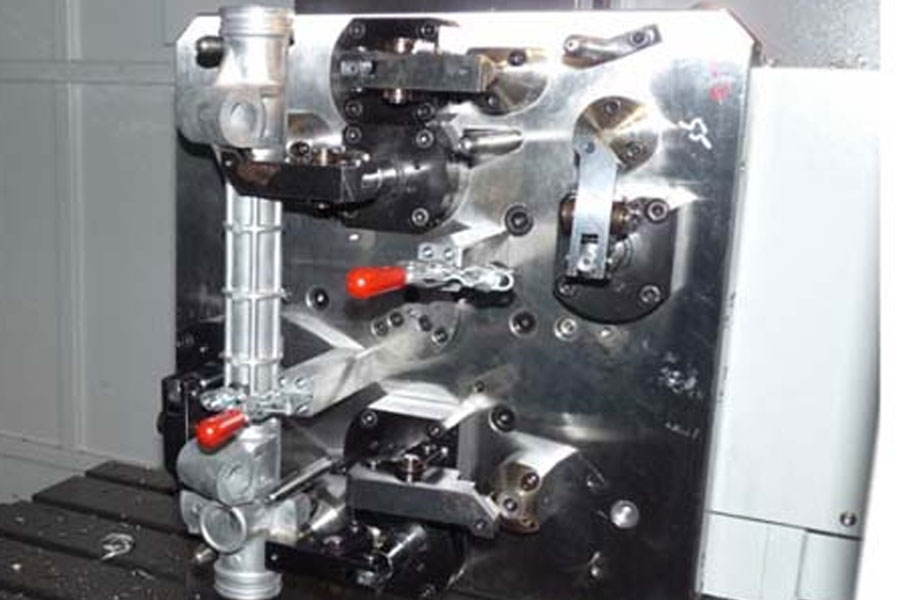
铝合金铸造工艺性能。它通常被理解为在填充特性、结晶和冷却过程中最突出的那些特性的组合,如流动性、收缩性、气密性、铸造应力和吸气性。铝合金的这些特性取决于合金的成分。但也与铸造因素、合金加热温度模具的复杂性、浇注冒口系统和浇口形状有关。
(1) 流动性
流动性是指合金充液特性的能力。流动性决定了合金能否铸造出复杂的铸件。影响流动性的因素很多。主要因素是合金液中的成分、温度以及金属氧化物、金属化合物和其他污染物的固体颗粒,而外部客观因素则是浇注温度和流动压力(俗称冷凝喷射头)。
(2) 收缩性
收缩是铸造铝合金的主要特征之一。合金从液态浇注到凝固直至达到室温分为三个阶段。它们分别是液态收缩、凝固收缩和固态收缩。合金收缩对铸件质量有决定性影响。它影响铸件缩孔的大小、应力裂纹的形成和尺寸的变化。快速恒定锫的收缩分为体收缩和线收缩。在实际生产中,一般采用线性收缩来改善金合金的收缩率。铝合金的收缩大小。通常用百分比表示,称为收缩率。
身体收缩
体收缩包括液体收缩和凝固收缩。
铸造合金液从浇注到凝固。凝固结束时,会出现宏观或微观的越面收缩。这种由缩孔引起的宏观缩孔肉眼可见,分为集中缩孔和局部缩孔。集中缩孔的孔径大而集中。它们分布在铸件的顶部或表面的厚热点。分散缩孔分散而细小。它们大多分布在铸件轴线和热接缝处。肉眼很难看到微观缩孔。大部分微观缩孔分布在晶界下或树枝状晶粒之间。
收缩和气孔是铸件的主要缺陷之一。其原因是液态收缩大于常态收缩。在生产过程中发现,铸件铝合金凝固范围较小。结晶越多形成的雷仲收缩空穴越多。检查凝固范围。因此。在设计中,铸缝铝合金必须符合顺序凝固的原则。印模铸件在液态手凝固时的体收缩应由合金液补充。缩孔和疏松主要集中在铸件的外冒口处。对于容易出现散孔和疏松的铝合金铸件。百口安装的数量要多于集中缩孔的数量。并在产生结晶的地方设置冷铁,提高局部冷却速度。使其同时凝固或快速凝固。
线条收缩
缩线的大小会直接影响铸件的质量。系统收缩大。铝铸件产生裂纹和应力的趋势也更大:冷却后铸件的尺寸和形状都会变大。
对于不同的铸造铝合金,接合处的收缩率不同,而印刷的是同一种合金。铸件不同。收缩率也不同。在同一个铸件上。其长、宽、高的收缩率也是不同的。应根据具体情况确定。
(3) 热裂纹
铝铸件出现热裂纹的主要原因是铸件的收缩应力超过了金属晶粒之间的结合力。大多数裂纹沿晶界出现。从裂纹断口可以看出,裂纹处的金属通常已被氧化,失去了金属光泽。裂纹沿晶界延伸,呈 "之 "字形,表面宽,内部窄,有些裂纹甚至穿透整个铸件端面。
不同的铝合金铸件具有不同的裂纹倾向。这是因为铝合金铸件在凝固过程中形成完整结晶框架的温度与凝固温度之间的差值越大,合金的收缩率就越大,热裂倾向也就越大。即使是同一种合金,由于模具的阻力、铸件的结构、浇注工艺等因素的影响,其热裂倾向也不尽相同。为避免铝铸件出现裂纹,生产中通常会采用退火铸造模具或改进铸造铝合金铸件系统等措施。热裂纹环法通常用于检测铝铸件中的热裂纹。
(4) 气密性
铸铝合金的气密性是指空腔型铝铸件在高压气体或液体作用下不漏气的程度。气密性实际上表征了铸件内部结构的紧凑和纯净程度。
铸造铝合金的气密性与合金的特性有关。合金的凝固范围越小,产生气孔的可能性就越小。同时,析出气孔越小,合金的气密性越高。同一种铸造铝合金的气密性还与铸造工艺有关。例如,降低铸铝合金的铸造温度、放置冷铁以加快冷却速度、在压力下凝固结晶等。这些都能使铝铸件的气密性得到改善。浸渍法还可用于堵塞泄漏间隙,以提高铸件的气密性。
(5) 铸造应力
铸造应力包括三种应力、相变应力和收缩应力。各种应力的成因并不相同。
铸造铝合金的气密性与合金的特性有关。合金凝固范围越小。产生硫松的倾向也越小。同时,产生的气孔也小。否则,合金的气密性会很高。同样铸铝合金的气密性也与铸造检验工艺有关。如降低铸铝合金的铸造温度、放置冷铁加快冷却速度、加压凝固结晶等。这些措施可以提高铝铸件的气密性。通过处理方法堵塞泄漏量大的缝隙,也可提高铸件的气密性。
(6) 吸入
铝合金易于吸收气体,这是铸造铝合金的主要特点。铝液和铝合金成分与炉料、有机物燃烧产物和模具中所含的水分反应产生的氢气会被铝液吸收。
铝合金熔体的温度越高,吸收的氢就越多。在 700°C 时,100 克铝中的氢溶解度为 0.5 至 0.9。温度升至 850°C 时,氢的溶解度增加 2 至 3 倍。当含有碱金属杂质时,氢在熔融铝中的溶解度会显著增加。
铸造铝合金除了在熔炼过程中会吸入气体外,在浇注到模具中时也会产生吸入气体。进入铸模的金属液随温度降低,气体的溶解度降低,多余的气体析出,有一部分气体无法逸出。它留在铸件中形成气孔,通常被称为 "针孔"。气体有时会与缩孔结合,而析出在铝熔体中的气体会留在缩孔中。如果气泡加热产生的压力大,气孔表面光滑,孔周围有一层光亮层;如果气泡产生的压力小,气孔内表面起皱,看起来像 "苍蝇脚",仔细观察还有收缩孔。特征。
铝合金铸液中的氩含量越高,铸件中产生的针孔就越多。铝铸件中的针孔不仅会降低铸件的气密性和耐腐蚀性,还会降低合金的机械性能。要获得无气孔或少气孔的铝铸件,关键在于熔炼条件。如果在熔炼过程中加入覆盖剂进行保护,合金的气体吸入量就会大大减少。对铝熔液进行精炼可以有效控制铝熔液中的氢含量。使用砂、粘土和其他辅助材料制作模具的铸造方法称为砂模铸造。砂模的材料统称为造型材料。用于有色金属的砂型由砂、粘土或其他粘合剂和水制成。
铝铸件的成型过程是金属与模具相互作用的过程。铝合金液注入模具后,热量传递到模具,砂模受到金属液的热效应、机械效应和化学效应的影响。因此,要获得高质量的铸件,除了严格掌握熔炼工艺外,还必须正确设计模具(型芯)的砂比、造型和浇注工艺。
3.金属模具铸造
1.简介和技术流程
金属模具铸造又称硬模铸造或永久性模具铸造。它是一种将熔化的铝合金浇注到金属模具中以获得铸件的方法。铝合金金属模铸造大多使用金属型芯,也可使用砂型芯或壳型芯。这种方法与压力铸造相比,铝合金金属模具的使用寿命较长。
2.铸造优势
(1) 优点
金属模具冷却速度快,铸件结构致密,可通过热处理强化,其机械性能比砂型铸造高 15%左右。金属模铸造,铸件质量稳定,表面粗糙度优于砂型铸造,废晶率低。工作条件好,生产率高,工人易于掌握。
(2) 缺点
金属型导热系数大,填充能力差。金属材料本身不透气。必须采取相应措施才能有效排气。金属模具没有回缩性,凝固时容易开裂变形。
3.金属铸件的常见缺陷和预防
(1) 针孔
防止针孔的措施:严禁使用被污染的铝合金铸件材料、沾有有机化合物的材料以及严重氧化和腐蚀的材料;控制熔炼工艺,加强脱气和精炼;控制金属型涂层的厚度,过厚易产生针孔;模具温度不宜过高,对铸件厚壁部位采取冷却措施,如镶铜或浇水等;使用砂模时,严格控制水分,尽量使用干燥型芯。
(2) 造口
防止气孔的措施:修改不合理的浇注和冒口系统,使液流稳定,避免气体卷入;模具和型芯应预热,然后涂漆,使用前必须彻底干燥;设计模具时应考虑与型芯充分的排气措施。
(3) 氧化和夹渣
防止氧化和夹渣的措施:严格控制冶炼过程,快速冶炼,减少氧化,彻底除渣。A1- Mg 合金必须在覆盖剂下冶炼;熔炉和工具应清洁、无氧化物,并应预热,缓冷后晾干涂层待用;
所设计的浇注系统必须具有稳定的流动性、缓冲性和挡渣能力;倾斜浇注系统用于稳定液流,避免二次氧化;所选涂料必须具有较强的附着力,在浇注过程中不会剥落并进入铸件形成夹渣。
(4) 热裂纹
防止热裂纹的措施:在实际浇注系统中应避免局部过热,以减少内应力;模具和型芯的倾斜度必须在 2°以上,浇注冒口凝固后可抽芯开模,必要时可使用砂芯 代替金属芯;控制涂层厚度,使铸件各部分冷却速度一致;根据铸件厚度选择合适的模温;细化合金结构,提高热裂能力;改进铸件结构,消除尖角和壁厚突变,减少热裂倾向。
(5) 松散
防止气孔的措施:合理设置冒口,保证凝固和供料能力;适当降低金属模具的工作温度;控制涂层厚度,减小厚壁厚度;调整金属模具各部分的冷却速度,使铸件厚壁具有较大的刺激能力;适当降低金属浇注温度。
相关页面:铝铸造 相关文章