铸件检验主要包括尺寸检验、外观和表面目视检验、化学成分分析和机械性能测试。对于要求更重要或在铸造过程中容易出现问题的铸件,还需要进行无损检测,球墨铸铁铸件可采用无损检测。用于质量检测的无损检测技术包括液体渗透检测、磁粉检测、涡流检测、射线检测、超声波检测和振动检测。
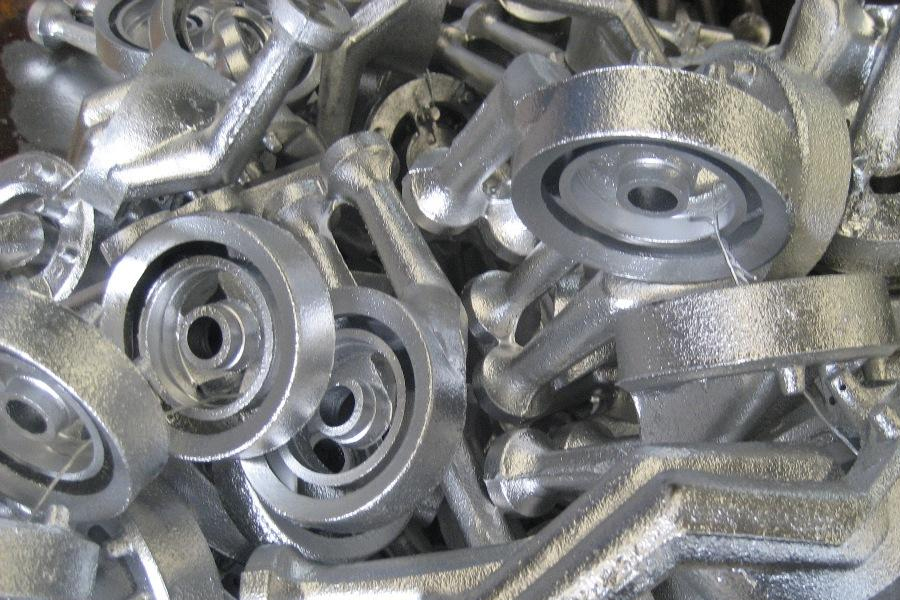
检测铸件表面和近表面缺陷
1.液体渗透检测
液体渗透试验用于检查铸件表面的各种开口缺陷,如表面裂纹、表面针孔和其他肉眼难以发现的缺陷。常用的渗透测试是颜色测试,即在铸件表面湿润或喷洒渗透能力强的有色(通常为红色)液体(渗透剂)。渗透剂渗入开口缺陷,并迅速擦掉表面渗透剂。然后在铸件表面喷洒易干显示剂(也称显影剂)。残留在开口缺陷中的渗透剂被吸出后,显示剂被染色,可反映出缺陷的形状和形貌。尺寸和分布。需要指出的是,渗透剂检测的精度随被检测材料表面粗糙度的增加而降低,即表面越浅,检测效果越好。磨床的表面检测精度最高,甚至可以检测到晶间裂纹。除了颜色检测,荧光渗透检测也是一种常用的液体渗透检测方法。它需要配备紫外线灯进行照射观察,检测灵敏度高于颜色检测。
2.涡流测试
涡流检测适用于检测表面下一般不超过 6 至 7 毫米深的缺陷。涡流检测分为放置线圈法和贯通线圈法两种:当试件放置在带交流电的线圈附近时,进入试件的交流磁场会在试件中感应出与激励磁场垂直的涡流方向的电流(涡流)。这将产生一个与激励磁场方向相反的磁场,从而部分减弱线圈中的原始磁场,导致线圈阻抗发生变化。如果铸件表面存在缺陷,涡流的电特性就会发生畸变,从而检测出缺陷的存在。涡流检测的主要缺点是无法直观地显示检测到的缺陷的大小和形状,一般只能确定缺陷的表面位置和深度。此外,在检测工件表面的小开口缺陷时,其灵敏度也不如渗透检测。
3.磁粉测试
磁粉检测适用于检测表面缺陷和表面下几毫米深的缺陷。它需要直流(或交流)磁化设备和磁粉(或磁悬浮液)来执行检测操作。磁化设备用于在铸件内外表面产生磁场,磁粉或磁悬浮液用于显示缺陷。当在铸件的一定范围内产生磁场时,磁化区域内的缺陷将产生漏磁场。当洒下磁粉或悬浮液时,磁粉会被吸引,从而显示出缺陷。以这种方式显示的缺陷基本上是与磁力线交叉的缺陷,与磁力线平行的长形缺陷无法显示。因此,在操作过程中需要不断改变磁化方向,以确保能检测到未知方向上的各种缺陷。.
检测铸件内部缺陷
对于内部缺陷,常用的无损检测方法是射线检测和超声波检测。其中,射线检测的效果最好。它可以获得反映内部缺陷类型、形状、大小和分布的直观图像。但对于厚度较大的大型铸件,超声波检测的效果非常好,可以更准确地测量内部缺陷的位置。, 等效尺寸和分布。
1.射线检测
射线检测一般使用 X 射线或 γ 射线作为射线源。因此,需要设备和其他辅助设施来产生射线。当工件暴露在射线场中时,射线的辐射强度会受到铸件内部缺陷的影响。通过铸件发出的射线强度随缺陷的大小和性质而局部变化,形成缺陷的射线图像,通过射线胶片可视化记录,或通过荧光屏、射线计数器进行实时检测和观察。其中,通过射线胶片显影和记录的方法是最常用的方法,通常称为射线检测。射线照相法反映的缺陷图像直观,缺陷的形状、大小、数量、平面位置和分布范围都能显示出来,但缺陷深度一般不能反映出来,需要采取特殊措施和计算才能确定。如今,出现了射线计算机断层扫描方法的应用。由于设备相对昂贵,使用成本较高,目前还不能普及,但这项新技术代表了未来高分辨率射线检测技术的发展方向。此外,使用近似点源的微聚焦 X 射线系统实际上可以消除较大聚焦设备产生的模糊边缘,使图像轮廓清晰。数字图像系统的使用可以提高图像的信噪比,进一步提高图像的清晰度。
2.超声波检测
超声波检测也可用于检查内部缺陷。它使用带有高频声能的声束在铸件内部传播。当遇到内部表面或缺陷时,声波会反射并发现缺陷。反射声能的大小与内表面或缺陷的指向性和性质以及该反射器的声阻抗有关。因此,各种缺陷或内表面反射的声能可以用来探测缺陷的位置、壁厚或表面。下一个缺陷的深度。超声波检测是一种应用广泛的无损检测方法。其主要优点是:检测灵敏度高,可检测出细小裂纹;穿透能力强,可检测出厚截面铸件。其主要局限性是:难以解释轮廓尺寸复杂、指向性差的断开缺陷的反射波形;对于不理想的内部结构,如晶粒大小、结构、气孔、夹杂物含量或细小分散析出物等。此外,测试时应参考标准试块。