近年来,世界经济全球化进程的加快为我国铸造业的发展提供了机遇,铸件需求呈现出持续快速增长的趋势。汽车产量的快速增长进一步刺激了铸造业的发展。因此,我国许多铸造企业进行了大规模的技术改造,以适应市场需求,提高铸件生产能力。许多铸造车间都进行了新建、改建和扩建。现在我们就来谈谈铸造车间技术改造中应该注意的一些问题。
这项工作对项目投资和项目完成后的设备运行成本影响很大,因此非常重要。然而,很多企业往往忽视了这一重要环节,认为谁购买了设备,谁就负责设计。他们认为这样可以节省很多设计费用,但这种想法是很不科学的,有时还可能是错误的。
铸造企业具有高噪音、高粉尘、振动大、物料运输量大等特点。因此,企业在上马新项目时,极有必要根据铸造企业的特点,结合企业自身的实际情况和企业所在地的气候特点来考虑设计。总平面。例如:噪声大的工业部门应尽量远离办公区和居民区;铸造车间应建在机加工车间、装配车间、办公区等不产生有害气体和粉尘的下风处,减少二次污染;炉料、新砂、膨润土 原辅材料仓库的安装区域以靠近使用部门为宜,尽量靠近使用部门,减少无价值物流等。
企业平面设计不准确,必然会导致工厂布局混乱、现场无序、不同生产单位之间相互干扰、生产运输线混乱无序等问题,不仅影响生产和工人的劳动条件,影响工厂的环境保护。和生产成本,造成明显的生产损失,而且还造成了许多可以避免却无法预料的实际发生的经济损失。一直被认为是企业正常运转不可或缺的正常投资。与同行相比,企业的运行 成本增加了很多,降低了企业的经济效益。
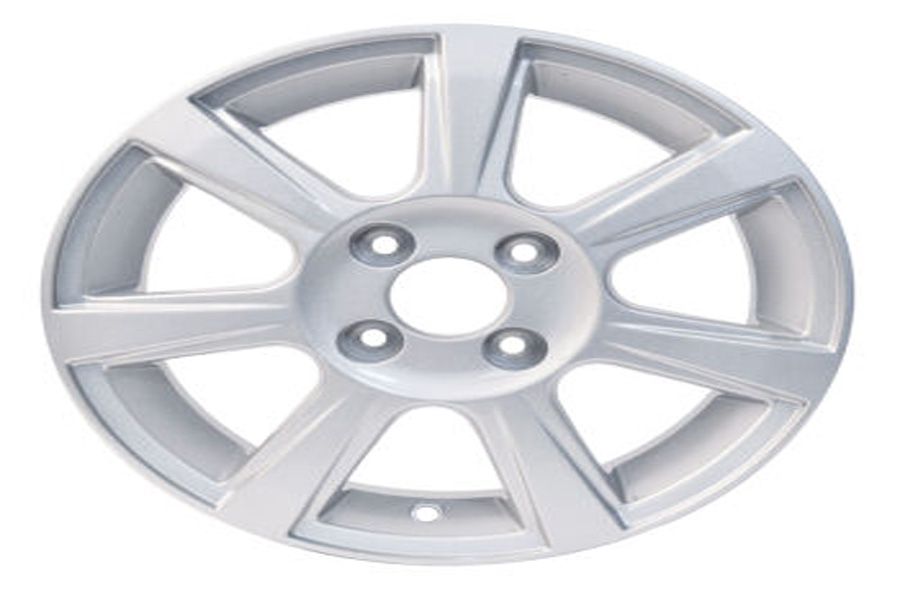
做好企业产品定位,制定技术改造工艺方案
铸造生产的目标是用最高的效率和最低的成本生产出质量合格、稳定的铸件,以取得相应的效益。根据产品定位、批量大小、材料要求等,对其进行详细、科学的工艺分析,制定工艺方案,进而建立适应性强的工艺流程。对其进行详细、科学的工艺分析,制定工艺方案,进而建立适应性的技术改造计划。要树立适用的最佳理念,明白无论多么先进复杂的设备,都是满足铸造生产工艺要求的更复杂的 "专用工装"。目前,各种工艺技术竞相发展,每种技术都有其优势,但也有一定的局限性和适用范围。先进的高科技工艺不一定都适用于任何铸造生产。
根据铸件质量要求、材质要求、批量大小、价格水平以及企业厂址等自身条件,选择技术上适用、经济上合理的工艺,并注重技术与经济的结合,才能做出切合实际的选择,达到工艺改造的目的。总之,工艺保证能力不足或工艺保证能力过剩,都会使企业增加不必要的运营成本,降低效益。由此可见,做好企业的产品定位,制定工艺方案,进而确定适用的技术改造方案是非常重要的。
注重各部门之间的设备匹配
为了实现计划控制的目标,设备的配置必须具有系统性和兼容性。目前,国内许多企业在技术改造过程中,特别重视成型部的设备。成型生产线的主机要么直接从国外进口,要么选择国内知名品牌,对其他部门的设备重视不够。厂家的配置就够了,根本不了解国内的实际情况。不同的设备生产厂家,即使设备型号相同,生产出来的设备实际生产率与样本中宣传的生产率也不一样,有的甚至相差很大。另外,很多配套的检测仪器也不考虑配备。
因此,国内很多厂家的造型设备都非常先进,达到了世界一流水平,但一些工程部的设备却很差,可靠性不高,不仅故障率高,而且实际生产效率也达不到设计要求。整条生产线的设备没有,生产过程中出现了瓶颈。这不仅严重影响了造型线的开工率,还使得生产周期时有波动,增加了工艺参数的控制难度,增加了铸造废品的风险。因此,生产线的整体效率与设计目标相去甚远。
加强流程改进和员工培训
从技术改造项目开始,就要同步抓好管理、技术、运行维护人员的培训。人才培训注重实效,需要培训什么就要有针对性地培训什么。培训不是文凭,不是证书,只是岗位需要。同时,注意引进一些岗位紧缺的特殊人才。最大限度地提高整个执行团队的技术和管理素质,保证生产线的正常运转。同时,注重生产过程中的铸件质量跟踪,根据其波动情况,注重工艺流程的改进。
总之,铸造技术改造是一项复杂的、多学科的综合性工作,没有中间试验,也不允许失败。因此,建议建立一个多部门、多学科的专业团队,运用 "头脑风暴法 "从不同角度对项目进行综合分析,对整个项目的前期、中期、后期进行精心策划,确保建成后的铸造项目达到实用、节能、环保、低耗、高效的目标。