随着汽车轻量化的发展,铝合金铸件在汽车上的应用越来越广泛。一些用于汽车车身的薄壁铸件主要采用高压铸造,而一些结构复杂的铸件,如轮毂、发动机缸体和缸盖等,则大多采用低压铸造成型。低压铸造具有充型稳定、速度可控、加压凝固便于进料等特点。然而,人们对低压铸造的充型过程关注不够。最近,一些研究人员发现,如果低压铸造过程中加压速度过快,熔融金属的充型速度会超过临界充型速度值(0. 5 m/s),从而造成夹带和夹渣缺陷,降低铸造成本。机械性能。在低压铸造的充型过程中,加压速度和铸件结构会对夹渣缺陷产生影响。因此,本课题结合数值模拟和实验,对三种不同结构和不同加压速度的扁平铸件进行了比较。通过研究,阐明夹带缺陷产生的原因,为低压铸件顺利充型的工艺设计提供参考。
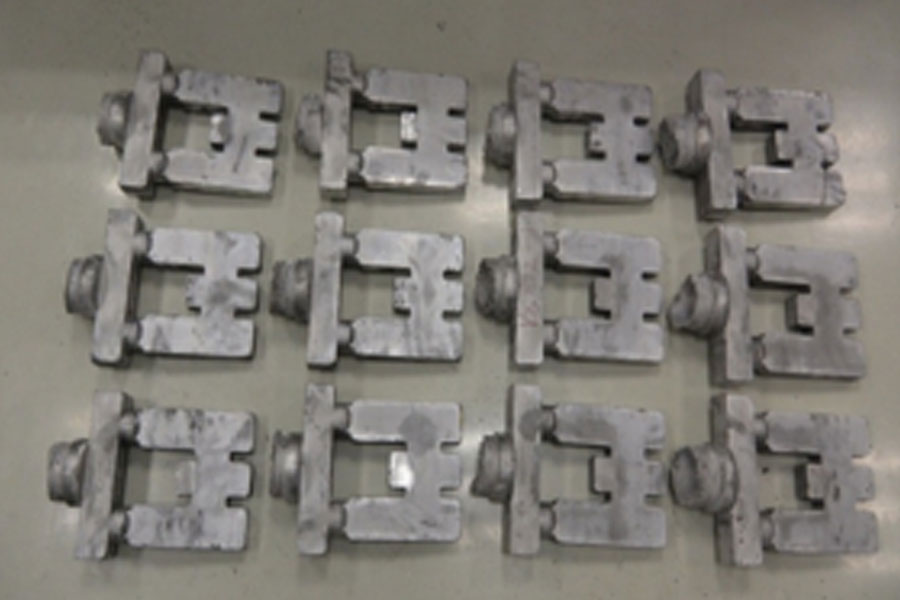
测试方法
主要研究铸件结构和加压速度对填充过程的影响。因此,设计了三种不同结构的简单模型,如图 1 所示。铸件尺寸为 280 mm×150 mm×30 mm。三个平板铸件的中心位置具有不同高度的瀑布结构。落水高度分别为 0、15 和 30 毫米。结构对铸件质量的影响。
使用 Flow-3D 软件模拟了三种不同的模型和不同的充气压力。应用软件中的夹带模型,分析不同方案充气过程中的夹带量。将这三个模型保存为 STL 文件并导入 Flow-3D。铸造网格分为 500 万个。铸件材料为 ZL101A,浇注温度为 700℃,合金粘度为 0.0019Pa-(根据软件自己的数据库),模具材料为 H13 钢,预热温度为 250℃。对于这三种模型,依次输入 2000、1200、600 和 300Pa/s 的升压速度进行仿真
根据模拟结果,选择夹带量最大和最小的模型进行试生产。ZL101A 在现场煤气炉中冶炼,Al-10Sr 和 Al-5Ti-1B 母合金用于改性和精炼。工艺参数设计与模拟参数设置一致。为确保铝合金状态的一致性,本实验在坩埚中完成。对成功生产的铸件的铸造机械性能进行了分析。每个铸件取 4 个 M6 拉伸样本。取样位置如图 2 所示。每个模型分析 6 个铸件,共 24 个拉伸样品,并采用国际拉伸试验。DIN EN ISO 6892-1 标准。取机械性能最低的样品,使用 SEM 进行断裂分析,分析机械性能降低的根本原因。
以 V3.1 方案为例,观察充填过程中的夹带分布,如图 3 所示。可以看出,当充填时间为 2. 9 s 时,熔融金属稳定上升;当充填时间达到 3. 6 s 时,熔融金属进入瀑布区,造成剧烈湍流,夹带严重;随着充填过程的继续,瀑布区产生的夹带气体会随着熔融金属的上升而随机分布到铸件中。
模拟结果显示了不同模型在不同加压速度下充气后的气量分布。可以看出,机型 V1 的气量较少,随着增压速度的增加,气量略有增加。无论增压速度是否增加,模型 V2 和 V3 的夹带程度不同,分布也不同。
为了明确升压速度和下降结构对风量的影响,对各方案的风量进行了定量分析,通过 Flow-3D 得出各方案的风量,如图5所示。从夹带量的定量分析结果可以看出,当无下降结构时,夹带量随升压速度的增加而增加;当有下降结构时,夹带量随升压速度的增加变化不明显;同种升压速度下,增加下降结构的高度,夹带量会明显增加。因此,铸件中的下降结构是影响夹带量的主要因素。当没有下降结构时,加压速度将影响夹带量。
实际铸件的机械性能和断裂分析
对于 V1 型和 V3 型,试制时使用的填充压力速度相同,均为 300 Pa/s。每个模型生产了 12 件。可以看出,铸件质量良好,轮廓清晰。其中 6 件被选中用于拉伸试棒加工。
通过拉伸试验可以获得铸件的抗拉强度和伸长率,如图 7 所示。从图中可以看出,无坠落结构铸件的抗拉强度和伸长率相对稳定,平均抗拉强度为 191MPa,平均伸长率可达 5.3%;而有 30 mm 坠落结构的铸件的抗拉强度和伸长率 伸长率有一些相对较低的值。平均抗拉强度为 178MPa,平均伸长率仅为 3.8%。选择抗拉强度低于 160MPa 的下落结构试样,对断口进行 SEM 分析,如图 8 所示。可以看出,断口表面存在比较大的夹杂鳞片缺陷。结合模拟结果分析,主要原因是下落结构中产生了严重的夹带行为。