压铸是有色金属成型的重要手段之一。在压铸过程中,由于熔融金属在型腔中的流动状态不同,可能会出现冷障、花纹、气孔和偏析等不良现象。为了防止这些不良现象,控制型腔中熔融金属的流动是非常必要的。控制型腔中熔融金属流动的关键在于压铸模浇口系统的研究和设计。
压铸模具的生产过程
压铸模具制作的 CAD/CAE/CAM/CAT 流程。
压铸模浇注系统的设计
在压铸模浇口系统的研究中,浇口位置和形状是控制溶液流动状态和填充方向的重要因素。首先,关注浇口的位置和流道的形状,设计浇口、流道、渣袋、溢流槽和排气管道;然后使用 CAE 软件分析型腔内溶液的流动情况。内流道和内浇口的位置和尺寸对填充方法有决定性影响。
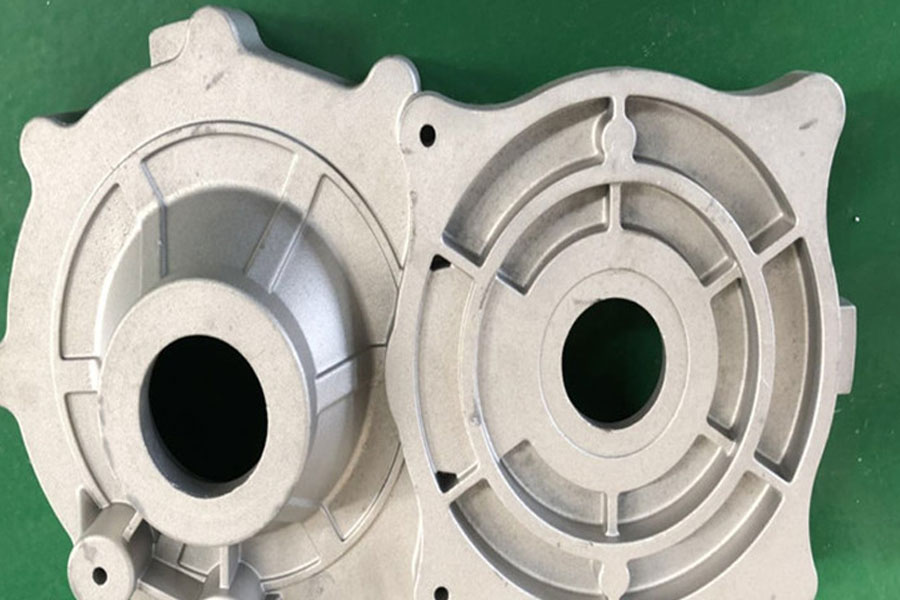
内门的设计
在成品上设置浇口时,通常按照以下程序进行:
浇口和排气系统的设计
内浇口应设置在熔融金属在型腔中流动最好、排气充满、型腔所有角落都能充满熔融金属的位置。尽可能使用内浇口。如果需要多个内浇口,则应注意确保熔融金属流不会相互干扰或在型腔中相遇而不分散(即引导金属流向一个方向流动),以避免熔融金属在型腔涡流中汇聚。
当压铸件尺寸较大时,有时仅靠一个流道无法获得所需的流道横截面积,因此必须使用多个流道。但应注意的是,内流道的设置应确保熔融金属只朝一个方向流动,以避免型腔中的熔融金属汇合时产生涡流。
熔融金属流在型腔中的转向应尽可能小,以便熔融金属能够到达压铸件的厚壁部分。
熔融金属流应尽可能短且均匀。
内流道的横截面积向内流道逐渐减小,以减少气体夹带,有利于提高压铸件的致密性。内流道在流动过程中应平稳过渡,尽量避免急转弯和流动冲击。
当有多个空腔时,应根据每个空腔的体积比,分段缩小流道的横截面积。
空腔中的空气和润滑剂挥发的气体应被流动的熔融金属推向排气槽,然后从排气槽排出空腔。尤其是,熔融金属的流动不应将气体留在盲孔中,以免过早堵塞排气槽。
金属流不应在散热不良的地方形成热冲击。对于带筋的压铸件,金属流应尽量沿筋的方向流动。应避免熔融金属直接冲刷容易损坏的模具部件和型芯。在不可避免的情况下,应在浇口上设置隔离区,以避免热冲击。
一般来说,内流道越宽、越厚,流动不均匀的风险就越大。同时,尽量不要使用过厚的浇口;避免在切割浇口时产生变形。
空腔排气
溢流槽用于清除浇铸过程中最初喷出的熔融金属,使模具温度保持一致。液流槽设置在模具易含气体的位置,用于排出气体,改善熔融金属的流动状态,引导熔融金属流向型腔的各个角落,获得良好的铸件表面。排气槽与溢流槽前端和渣袋相连,或直接与型腔相连。
排气槽的总横截面积应大致相当于内流道的横截面积。
分型面上排气槽的位置是根据熔融金属在型腔中的流动状态确定的。排气槽最好 "不直 "而 "弯曲",以防止熔融金属喷溅伤人。分型面上的排气槽深度通常为 0. 05mm-0. 15mm;型腔内的排气槽深度通常为 0. 3mm~0.5mm;模具边缘的排气槽深度通常为 0.15mm ;排气槽的宽度一般为 5mm~20mm 。
顶针和推杆之间的排气间隙对于型腔的排气非常重要,通常控制在 0. 01mm-0. 02mm,或者加大间隙直到不产生毛刺。
固定芯排气也是一种有效的排气方法。通常,在型芯外围控制 0. 05mm-0. 08mm 的间隙,从而在型芯定位颈部开出宽度和厚度为 1mm-2mm 的排气槽,型腔中的气体沿颈部排出排气槽。气体从空腔底部排出。排气槽的粗糙度不容忽视。应保持较高的光滑度,以免在使用过程中因油漆粘附污垢而堵塞,影响排气。
流量分析评估与对策
在模具设计过程中,应尽量让金属流朝一个方向流动。对流动进行分析后,当发现型腔中存在涡流时,应改变内浇口引线角度或尺寸,以消除涡流状态。
当熔融金属相遇时,应让熔融金属继续流动一定距离后再停止流动,因此应在交界处的型腔外增设溢流槽和渣袋,让过冷的熔融金属和空气化合物流入溢流槽和渣袋,并让随后的熔融金属保持清洁和常温。当不同部件的充填速度不同时,应调整内浇口的厚度或宽度(必要时逐渐增大),以达到充填速度基本相同的目的,但应尽量加宽内流道。
经过流动分析,找到充填滞后部分,还可以增加一个内流道。对于薄壁压铸件,必须选择较短的充填时间进行压铸;因此,应通过增加内流道的横截面积来缩短充填时间,以获得较好的表面质量。
对于密实度要求较高的厚壁压铸件,必须确保有效的排气。压铸件应采用中等充型时间。因此,应调整内部流道的横截面,以获得相应的充型时间,并获得更好的表面质量和内部质量。
总之,在压铸模具设计过程中,应注意避免出现许多不良现象。即使在有 CAE 分析方法的今天,在浇口设计初期,先将总结的经验考虑到浇口系统中,有机地结合、分析、改进、提升,必然会达到事半功倍的效果。