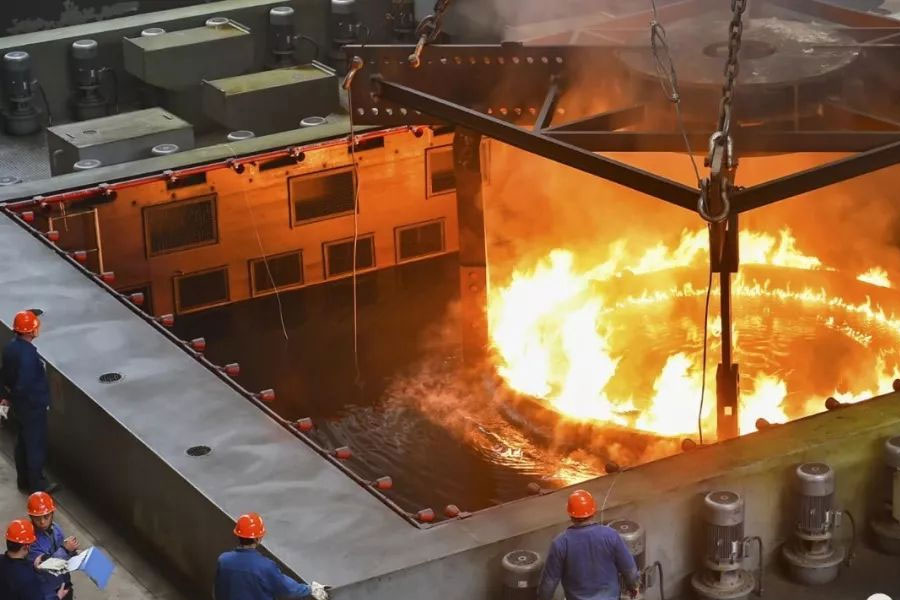
1.淬火变形
淬火变形的类型可分为两类,即体积变形和形状变形。
淬火前后各种结构比容的差异是体积变化的主要原因。马氏体→贝氏体→珠光体→奥氏体的比容依次减小。原始结构为珠光体的工件淬火后变成马氏体,体积膨胀。如果组织中有大量残留奥氏体,则体积可能会缩小。只有精度特别高的工件才会考虑由体积均匀膨胀引起的体积变化。
工件各部分相对位置或尺寸的变化,如板和杆的弯曲、内孔的膨胀和收缩以及孔间距的变化,统称为形状变形。变形的原因如下:
2.减少淬火变形的途径和方法
3.校正失真
对于热处理后零件的变形,可采用冷压矫直、热点矫直、热矫直、回火矫直、反击矫直、收缩处理等方法。
冷压矫直是在弯曲工件的最高点施加外力,使其产生塑性变形。这种方法适用于硬度小于 35HRC 的轴类工件;热点矫直是用氧乙炔焰加热凸形工件,然后用水或油快速冷却,使加热后的工件在热应力作用下收缩。这种方法适用于硬度大于 35-40HRC 的工件;而热矫直是将工件淬火至接近 Ms 温度,利用奥氏体良好的塑性和相变超塑性使变形得到矫正;回火矫正是对工件施加外力,然后进行回火,回火温度高于 300℃;反击矫直是用钢锤连续敲击凹槽,使工件产生小面积塑性变形;缩孔处理是将淬火后膨胀的工件加热到 600-700℃ 处变红。为防止水进入孔内,用两块薄板盖住工件两端,将工件迅速投入水中快速冷却。孔洞缩小,经过一次或多次重复操作后,膨胀的孔洞即可得到修正。
4.淬火开裂
淬火裂纹是一种因热处理应力超过材料断裂强度而产生的裂纹现象。裂纹呈断续串联分布,断口处有淬火油或盐水痕迹,无氧化色,裂纹两侧无脱碳现象。产生淬火裂纹的场合和原因如下:
5.防止淬火开裂的措施
6.硬度不够
淬火后工件表面硬度低于所用钢材的淬火硬度值,称为硬度不足。
淬火硬度不足的原因
控制措施
7.软斑
淬火后,工件表面局部区域硬度较低的现象称为软斑。碳钢和低合金钢由于淬透性差,通常容易出现淬火软点。
产生软斑的原因
控制措施
8.表面腐蚀-点蚀
工件经过淬火、酸洗或喷砂处理后,表面会出现密密麻麻的点状凹坑,这些凹坑被称为 "坑",是介质腐蚀形成的。这些凹坑会使工件失去光泽,影响表面光洁度。
形成点蚀的原因很多,但我们可以在工作中减少这种缺陷,比如降低盐浴中的硫酸盐含量,避免基体腐蚀;同时降低硝酸盐温度;高温淬火加热工件预冷后再放入溶液中,避免硝酸盐分解;高温局部加热时,对未加热部分进行盐浸,使其包裹一层坚固的盐壳,防止点蚀。