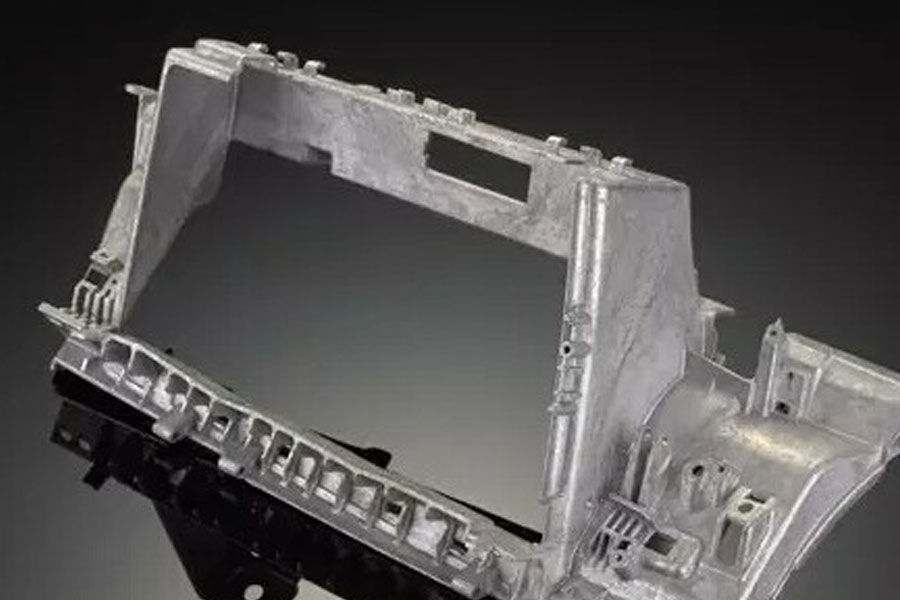
由于其生产效率高、成本低,且能生产形状较为复杂的产品,铸造成型工艺具有良好的充液能力,在镁合金成型方法中占据主导地位。但由于铸造镁合金的生产工艺,结构不够致密,存在缩孔、缩腔等诸多缺陷,力学性能较差。通过挤压、锻造、轧制等塑性加工工艺生产的镁合金产品,结构更致密,机械性能更好。通过挤压、锻造、轧制等塑性加工工艺制造的镁合金产品,结构更致密,能很好地改善镁合金产品的机械性能。目前,由于缺乏高效、低成本的镁合金塑性加工方法,镁合金塑性加工的应用受到限制。因此,开发高效率、低成本的镁合金塑性加工方法已成为推动高强度镁合金大规模应用的必由之路。镁合金主要有以下几种塑性加工技术:
Forged
镁合金的锻造工艺较为复杂。在锻造过程中,局部变形容易产生不均匀,因此工件的性能和结构也会不均匀。Mg-Zn-Zr 系列和 Mg-Al-Zn 系列是常用的锻造镁合金。当对材料在较高温度下的强度有较高要求时,在 WE 系列中添加稀土元素的镁合金强度很容易满足要求。在锻造过程中,变形程度、终锻温度和变形方式是影响镁合金锻件机械性能的主要因素。目前,主要开发了冲锻、等温锻造和温精锻造等成形技术。
挤压成型
挤压成型是一种塑性加工方法,将待成型的金属坯料置于封闭的挤压筒中,对坯料施加一定的压力,使材料在挤压模中变形。由于金属坯料在成型过程中处于三维压应力状态,因此金属坯料的塑性可以在成型方法中得到充分发挥。挤压产品表面质量好、尺寸精度高、结构紧凑。因此,汽车、航空航天和电子领域对镁合金挤压产品的需求量很大。一般来说,镁合金的挤压可分为热挤压和温挤压,所用设备与其他金属材料基本相同。
滚压成型
镁合金板材因其独特的优势,在航空航天和汽车 3C 行业有着广阔的应用前景。目前使用的大多数镁合金板材都是通过轧制成型的。然而,镁合金板材的轧制成形工艺较为复杂,通常需要 3 次或更多次的热轧。镁合金板材轧制具有以下特点:产量低、生产效率低、利润大、品种相对单一。
冲压和成型
镁合金的冲压工艺与其他材料不同。镁合金在室温下的塑性较低。传统的冷冲压成形不适合镁合金。镁合金通常需要加热到 150°C 或更高温度才能进行热冲压成形。目前,对镁合金的热冲压成形已有一定的研究,但其关键问题尚未得到很好的解决,这在一定程度上阻碍了镁合金板材在工业中的广泛应用。
拉伸成形
在镁合金的拉伸和成型过程中,材料处于拉伸和压缩的双向应力状态。此时,材料的塑性难以发挥。因此,拉拔不适合镁合金的成形。拉拔产品具有表面粗糙度高、尺寸精度好的特点。线材和管材采用拉拔成形工艺生产,生产效率高,易于实现高速连续生产。拉拔成型的镁合金线材强度更高。
超塑性成型
超塑性成形工艺可用于加工形状复杂、变形量大的工件。它是一种在特定条件下超过一般塑性指数的金属特性。因此,超塑性成形可用于加工塑性较差的镁合金产品。然而,由于对镁合金超塑性成形的研究刚刚起步,存在很多问题。镁合金的超塑性变形机理难以达成共识。镁合金的超塑性成形还需要进一步研究。