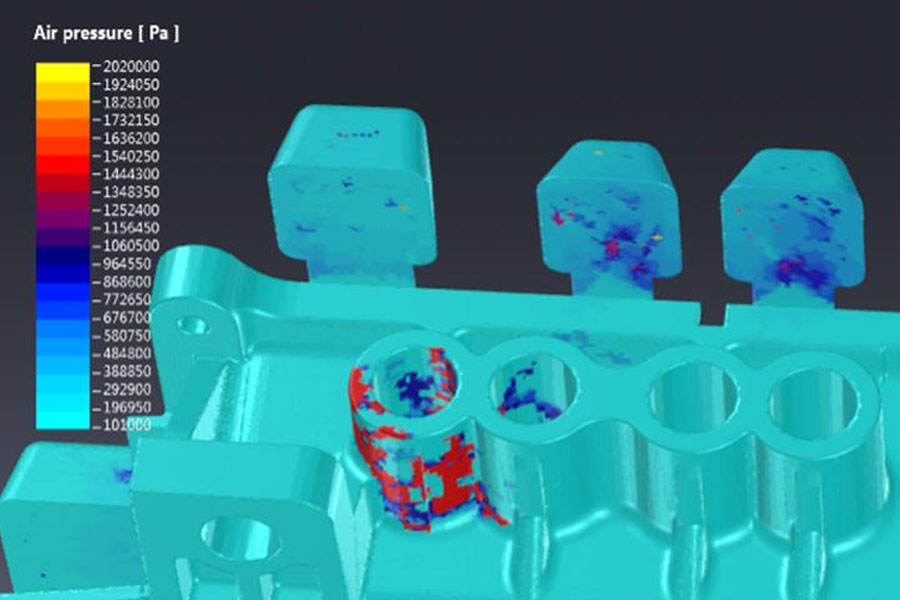
面对日益恶化的全球气候危机和日益严峻的节能减排、减少污染的趋势,汽车工业也将继续向节能减排、智能化方向发展;而在这种环境下诞生的电子节气门系统(Electronic Throttle Control System,简称 ETC)是当前汽车发动机系统中不可或缺的重要组成部分。它通过控制发动机的进气量来决定发动机的工作状态,以保证车辆获得最佳的动力和燃油。经济性,以进一步控制排放要求。可以预见,电子节气门作为先进汽车控制和安全系统的关键技术之一,必将与其他先进汽车控制技术一样,具有良好的应用前景。
作为电子节气门系统中最重要的部件之一,ETC 节气门铝壳铸件必然会影响到系统的可行性和稳定性,因此生产出符合要求的 ETC 节气门铝壳铸件就显得尤为重要。本文借助 MAGMASOFT 的 DOE 功能,在 ETC 节气门铝壳铸件的前期,对不同的浇注方案和各种工艺参数进行仿真分析比较和优化,选择最佳方案,从而缩短开发周期,保证该产品一次试模成功,顺利量产交付。
1 产品结构分析和技术要求
本文所研究的 ETC 节流铝壳铸件的压铸材料等级为 AlSi12Cu1Fe,其最大外形尺寸为 111mm*109mm*84mm。该铸件的平均厚度为 4mm,最大壁厚为 13mm。产品整体结构较为复杂。铝铸件有许多孤立的高筋,不利于铝熔液的有序充填;有些位置的壁厚相差较大,薄壁区首先凝固成固态,相当于将熔融合金分成许多 小封闭区,在厚壁处形成孤立的液相区。当这些孤立液相区的熔融金属凝固和收缩过程无法得到补充时,内部将不可避免地出现收缩空洞和气孔问题。
由于 ETC 节流铝壳铸件的工作环境比较复杂,需要通过抛丸强化铸件的表面质量,提高其耐腐蚀性能;对产品的配套安装位置有较高的几何尺寸公差要求;确保在 3bar 泄漏试验压力下的泄漏量小于等于 3cc/min,产品局部区域的缩孔直径不允许超过 0.7mm,总数不超过 5 个,间距不小于 10mm,且不超过总面积的 10%。7mm,总数不超过 5 个,间距不小于 10mm,且不超过总面积的 10%;因此,对于这种压铸件,需要非常高的铸造工艺设计要求,以确保铸件的内部质量能够达到客户的验收标准;
2 产品压铸方案和工艺参数设计
2.1 产品压铸方案设计
压铸生产技术中极为重要的压铸浇口设计环节,决定着压铸件的质量、压铸生产效率、模具寿命、压铸件的修整和清理、压铸合金的重熔率、压铸机的动力效率等。影响深远,因此设计合理的浇口位置、浇口厚度和尺寸、浇口数量是保证压铸件质量合格的关键;从产品结构特点和工艺设计经验分析,ETC 节流铝壳 有三个铸件位置适合设计进料口,因此本文将设计三种不同的压铸浇注方案。从理论填充路径和流动距离来看,不同的浇注方案会产生不同的填充效果,因此需要根据 MAGMA 仿真软件的结果进行对比分析验证;
2.1 浇注计划一设计
如图所示,第一种浇注方案的浇口数量设计为双股,分别设计在电机安装位置和阀板安装位置的侧壁区域。选择直径为 60mm 的注射冲头,注射速比为 1:14;该浇注方案的优点是熔融金属的流动时间相对较短,对填充过程中的温度降低值影响较小;三条流道的设计有利于压力的传递和熔融金属的进料,对降低后期生产过程中的缩孔缺陷风险有一定的积极作用;其缺点是由于产品分类和结构原因,流道必须设计一定的台阶和薄壁区域。这些位置在后期灌装过程中容易产生包气。另外,该产品电机安装位置未进行处理,此处设计有浇口,容易直接冲刷内壁芯,浇口位置温度较高,容易造成电机安装位置的模具缺陷和侵蚀缺陷;且浇口位置未进行处理,对后期压铸件的修整和清理有一定的负面影响;
2.1. 2 第二次浇注方案的设计
如图所示,第二种浇注方案的浇口数量设计为一个,位置设计在阀板安装位置的侧圆孔区域。选择直径为 60mm 的注塑冲头,注塑速比为 1:30;该浇注 方案的优点在于可以将流道设计得较为平滑过渡,有利于熔融金属的填充,减少填充过程中的气体包裹现象,减少流道带来的气体造成的缺陷;浇口设计在加工面的位置。减少压铸件的修整和清理工作量,降低生产成本;单股浇口可防止多股熔融金属进入型腔,造成涡流、夹带和氧化。缺点是处于浇口的远端。热点位置的进料效果基本没有,需要考虑其他辅助进料方案;且熔融金属流相对较长,对填充过程中的熔融金属温度有一定的负面影响,局部位置可能出现冷料缺陷。
2.1.3 第三浇注方案的设计
如图所示,浇注方案中三个浇口的数量设计为一个,位置设置在阀板安装位置的侧圆孔区域。选用直径为 60mm 的注塑冲头,注塑速比为 1:30;浇口的优点是浇口设计在加工面的位置,可以减少压铸机的修边和清理工作量,降低生产成本。浇口采用线性充填方式设计,可减少铝熔液的充填行程,降低铝熔液的温度损失。量减少;冲头与浇口距离短,可保证冲头压力的有效传递;缺点是后期生产调整参数的灵活性较差,不能通过调整压铸参数来提高产品质量。
2.2 产品工艺参数设计
根据 ETC 节流铝壳铸件的结构分析和质量要求,本产品采用 350T 压铸机,一模一腔设计,浇注压力设定为 100MPa,以保证足够的进料效率,减少后期缩孔缺陷的出现。浇注温度设计为 660-680℃,动、定模型芯预热至 180-200℃;充型过程中,低速设定为 0.25m/s,高速设定为 3m/s,分别在 340mm 和 350mm 处测试高速切换点。该位置用于确定熔融金属最稳定的填充状态和最少的涡流和夹带现象;同时,采用线冷却和点冷却的温度控制系统,以确保模具良好的热平衡;
3.一键式导入的数值模拟和比较分析
铸件的充型和凝固过程控制对压铸件的质量有着决定性的影响,但由于这两个过程在生产过程中都是在封闭的、看不见的型腔中完成的,无法直接或间接地观察和分析,因此前值模拟就显得尤为重要;通过使用 MAG 代码的 DOE 功能,一键导入以上三种压射方案和两种测试高速切换位置,一次性计算多种方案,最快预测缺陷位置,找到最佳方案,提高产品内在质量,缩短开发周期,降低生产成本。
3.1 装载过程的模拟和分析
如图 3 所示,图中第一行的仿真结果为填充时间。前三个方案的高速开关位置为 340mm,填充时间较短。后三种方案的高速开关位置为 350mm,填充时间较长。亮色位置为三种注塑方案的最后注塑位置;
图中第二行的结果为最大气压结果。模拟结果中的亮色为气压高的位置,气孔风险高。通过对比发现,方案 2 和方案 5 的气压值相对较低,气孔风险相对较小;
图片第三行的结果是填充量的结果。模拟结果中,明亮位置的空气含量较高,泄漏风险较大。通过对比发现,方案中第二和第五个体积的值相对较低,泄漏风险相对较小;
综合分析灌装过程的模拟结果可知,第二、五种方案的气压和夹带量相对较低,且第二种高速切换位置靠前,灌装时间短,整体成型性较好。
3.2 凝固过程的模拟和分析
如图 4 所示,图中第一行的结果为凝固温度场。模拟结果表明,方案 3 和方案 6 的内浇口凝固时间最长,压力供料时间最长;方案 1 和方案 4 次之,压力供料时间居中;方案 2 和方案 5 的内浇口凝固时间最短,压力供料时间最短;
第二行的结果是热接缝的有效进料时间,模拟结果的亮色是产品热接缝的位置,也就是产品结构相对较厚并最终凝固的位置。方案 1、2、4 和 5 的位置基本相同。方案 3 和方案 6 的内浇口相对较厚,因此如果将内浇口处的两个热点连接在一起,热点会增加;
第三行的结果是收缩结果。由于压送的原因,方案 3 和方案 6 的收缩状态最小,其他四种方案的收缩基本相同。相比之下,方案 2 和方案 5 的收缩率相对要小一些。
根据凝固过程的模拟结果分析,方案 3 和方案 6 的收缩腔最小,但内浇口处的热接缝最大,方案 2 和方案 5 的热接缝和收缩结果相对较好。
4.生产核查
综合模拟分析,采用第二种铸造方法进行生产。图5为 ETC 节流阀铝壳铸件的生产画面,通过产品检验和 X 光检查,铸件未出现气孔和缩孔等超出客户质量要求的缺陷;同时也通过了侧漏要求,未出现漏水现象;铸件表面光亮,未出现明显的冷料和浇注不足等缺陷,整体效果完全符合客户的质量检验要求,并顺利量产。