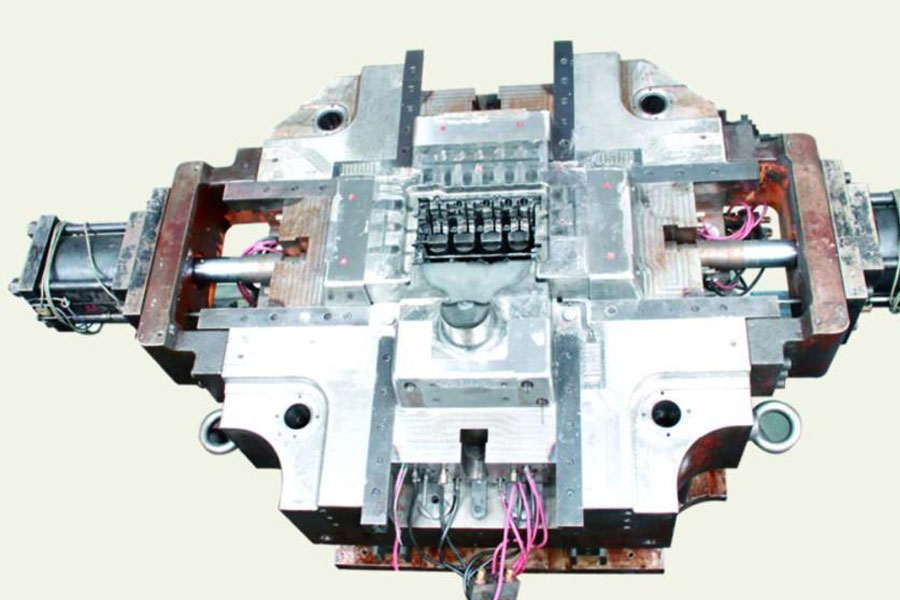
\铸造 "是一种液态金属成型工艺。众所周知,液态金属在高温下会在大气中表面氧化并产生氧化膜。
然而,长期以来,这种氧化膜对铝合金铸件质量的影响基本上只考虑了熔融金属中的非金属夹杂物问题,没有做进一步的讨论。
J.英国伯明翰大学的坎贝尔在多年研究的基础上发现,折叠双膜从宏观和微观方面对铝合金铸件的质量有着非常重要的影响。坎贝尔等人认为,对双膜的认识是最激动人心的发现。目前,我们暂且将 Campbell 等人获得的初步结论和见解称为 "双膜理论"。
层间氧化膜参与铝合金液后,其对铸件质量的影响大致可分为两个方面:
一是宏观方面。除了切割金属基体降低机械性能外,还会诱发气孔和小收缩等铸造缺陷;
另一个是微观方面,它对铝硅合金中的晶粒大小、树枝状晶粒间距以及 Na 和 Sr 的修饰效果有重要影响。
1.液态金属表面氧化膜的特征
分析氧化膜的特性时,不能同时考虑附着其上的金属母液的密度和熔点。以钢和铁的铸件生产为例。钢水氧化产生的 FeO 熔点和密度远低于钢水,在高温下非常活跃,基本上不可能单独存在。FeO 可以与 SiO2 结合形成低熔点的 FeO。SiO2,它能与钢中的硅和锰反应生成 MnO 和 SiO2,然后结合成 MnO.SiO2。它还能与钢中的碳反应生成 CO,其中会有一小部分。溶解在钢水中。如果脱氧处理不当,或钢水出钢后二次氧化,会增加钢中非金属夹杂物的数量,或在铸件表面造成气孔或夹渣等缺陷。然而,钢水表面产生的氧化物熔点低于钢水温度,只能累积。它们无法折叠成氧化膜夹层并悬浮在钢水中,因此不会出现氧化膜夹层造成的问题。.
铝合金和镁合金的情况完全不同。铝合金的简述如下:铝在液态时非常活泼,熔融铝的表面很容易与大气中的氧气发生反应,形成 Al2O3 薄膜。Al2O3 的熔点远高于液态铝合金,而且非常稳定。Al2O3 的密度略高于熔融铝。因此,Al2O3 薄膜易于悬浮在铝液中,不会聚集在一起,也不会与铝液分离。当铝合金液受到扰动时,表面的 Al2O3 膜会折叠成夹层,被卷入熔融金属中,造成铝合金的许多特有问题。
2.氧化膜夹层的形成及其有害影响
铝合金液在熔炼过程中、从熔炼炉中倒出时、变质处理过程中、高风速喷射和净化过程中以及浇注过程中都会受到强烈扰动。金属液表面的扰动会拉扯其表面的氧化膜,使其膨胀、折叠和破裂。氧化膜断开时露出的洁净合金液面会被氧化,生成新的氧化膜。氧化膜的折叠会使面向大气一侧的干燥表面相互粘附,两个干燥表面之间会包裹少量空气,成为 "氧化膜夹层"。氧化膜夹层很容易卷入熔融金属,并在受扰动的熔融金属的作用下被挤压成小团块。
由于 Al2O3 的熔点比铝合金液的温度高一千多摄氏度,且化学稳定性高,因此小团块不会熔化,也不会溶解在铝合金中。虽然 Al2O3 的密度略高于铝合金液的密度,但包裹在空气中的氧化膜夹层的密度与铝合金液的密度比较接近。因此,氧化膜夹层除了在大型保温炉中长期放置可能下沉外,在一般铸造生产条件下,会更稳定地悬浮在铝合金液中。悬浮了氧化膜夹层的铝合金液再次受到扰动时会产生更多的氧化膜夹层。在铸件生产过程中,合金熔炼、出炉浇注、改性处理、净化处理、浇注等操作都会对铝合金液产生强烈扰动。铝合金液除了保留原有的氧化膜夹层外,还会再次受到扰动,不断加入新的氧化膜夹层。因此,进入空腔的熔融金属含有大量微小的氧化膜夹层。熔融金属充满空腔后处于静止状态,被挤压成团的氧化膜夹层会逐渐拉伸成小块。熔融金属冷却到液相线以下后,树枝状物的成核和生长也是促进被挤压成团的氧化膜夹层拉伸的因素。
铸件凝固后,大量片状小氧化膜夹层本身就是小裂纹,起到切割金属基体的作用。当然,合金的机械性能会降低,但危害更大的是诱发气孔和小缩孔。随着液态金属温度的逐渐降低,氢在熔融金属中的溶解度不断降低,但氢很难以气孔的形式从液态金属中析出。当均相液相中产生另一新相(气相)时,它总是先由少数原子或分子聚集而成,其体积很小。这种微小的新相具有非常大的比表面积(即单位体积的表面积)。要产生新的界面,需要对其做功。这就是新相的界面能,即它的表面积和表面张力。的乘积。在铝合金液的冷却过程中,实际上不可能获得如此大的能量。即使产生了新相的核心,它的长大也需要大量的能量,只有当新相的尺寸超过某个临界值时才有可能长大。小于临界值的新相核心无法长大,只能自行消失。从理论上讲,气相很难在液相中成核和长大。事实上如果没有其他诱发因素,在氢含量基本正常的条件下,均质铝合金不可能因氢的析出而产生气孔。
当熔融金属中含有大量悬浮氧化膜夹层时,情况就完全不同了。大部分氧化膜夹层被少量空气覆盖。当熔融金属的温度降低,氢在其中的溶解度降低时,氧化膜夹层中的小气泡就会成为氢的真空,溶解在熔融金属中的氢就会向气泡移动。介质扩散非常方便。氢气扩散到小气泡中,使氧化膜夹层膨胀,在铸件中形成气孔。如果铝合金液的净化处理良好,熔融金属中的氢含量很低,铸件中的气孔就会很少。但是,如果熔融金属中没有氧化膜夹层,即使熔融金属中氢含量很高,凝固时氢也只能以过饱和状态溶解在合金中,不可能产生气孔。如果铸件的进料条件不好,在凝固和收缩过程中就会产生缩孔。由于氧化膜的夹层是空心的,很容易被拉开,缩孔大多在氧化膜的夹层处形成。在这种情况下,溶解在熔融金属中的氢也会扩散到其中,导致孔隙扩大。
综上所述,可以认为对于铝合金铸件而言,氧化膜夹层是造成材料力学性能下降和铸件针孔、气孔缺陷的主要原因。为了改善材料的机械性能和提高铸件的致密性,采取措施消除氧化膜夹层比加强脱气和净化操作更为重要。