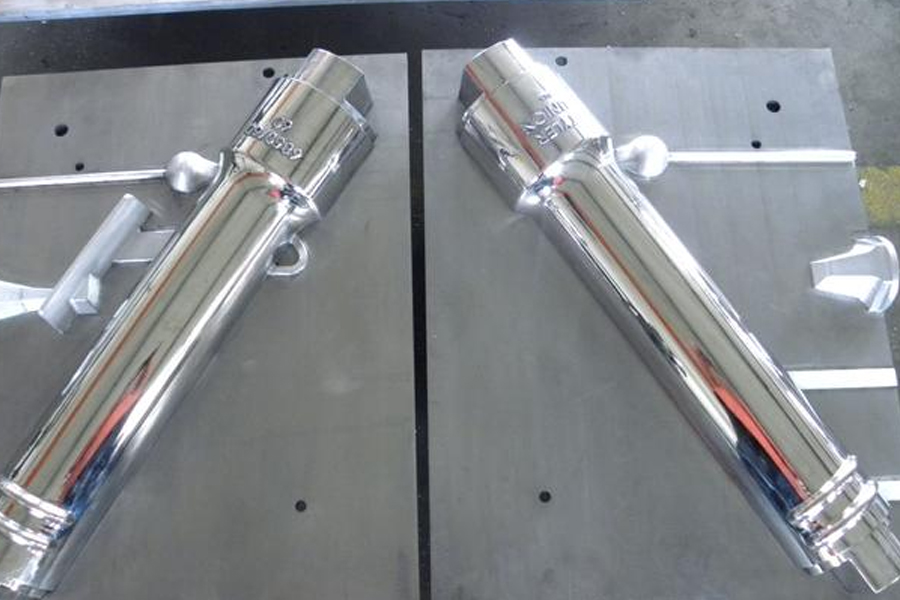
与重力金属模铸造相比,低压铸造由于在压力作用下充型和结晶凝固,具有成形质量好、工艺成品率高等优点,但对于形状复杂、性能要求高的气缸盖铸件,存在工艺复杂、控制要求高的技术难点。因此,本文重点介绍铝合金缸盖的低压铸造工艺及参数控制要点,以期充分发挥低压铸造工艺的技术优势,生产出高质量的缸盖铸件。
气缸盖低压铸造工艺的要点
2.1 门控系统示例
气缸盖的低压铸造工艺方案一般采用立管多浇口的形式,这也是一种多重量分流的形式。以四缸缸盖为例,具有代表性的浇口系统有两种,即在燃烧室一侧设置两个或四个浇口。图 2 是两个浇口的工艺示意图。这种方案适用于一个模具或两个模具。
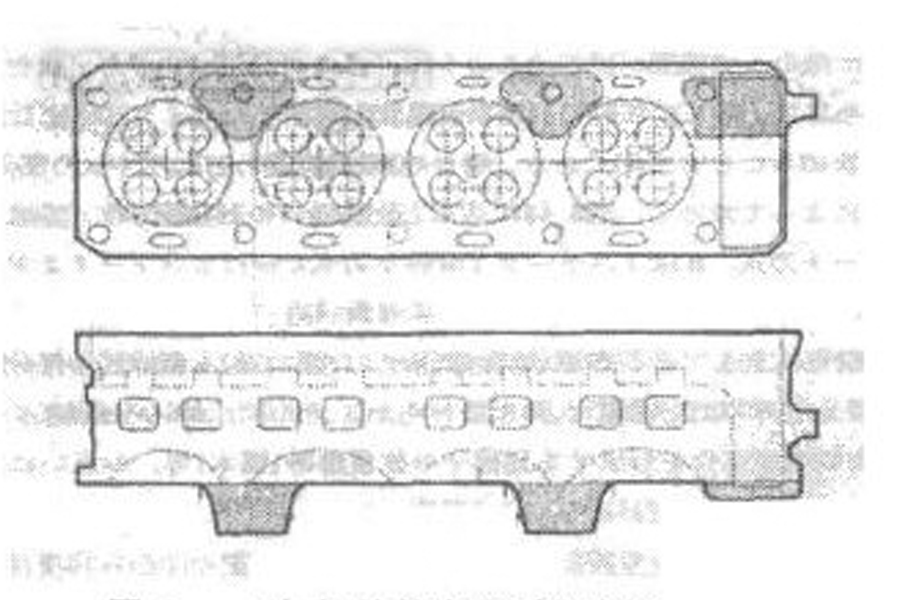
2.2 合金材料和熔化
铝合金气缸盖的材料一般选用 AI-Si-Cu 系列合金,如 ZL105 和 107。如果对伸长率和耐腐蚀性有要求,也可选用 ZL101 和 ZL104。为了获得高质量的熔融金属,标准操作应使用氩气旋转吹炼,并加入 Sr 进行改性和 AJ-Ti-B 精炼晶粒。
2.3 浇注过程
2.3.1 模具维护
定期清理和维护模具对于稳定生产高质量缸盖铸件和延长模具使用寿命非常重要。一般情况下,每生产 500-700 件铸件就应进行一次模具维护。主要内容是拆卸模具,用软毛刷清理型腔表面涂层,清除渗入顶杆与排气孔间隙的铝屑和涂层颗粒。, 保证铸件形状、顶出顺畅和排气顺畅的质量。
2.3. 2 涂层
浇注前,模具要预热到 200℃左右,并喷上油漆。气缸盖的形状比较复杂,因此要特别注意不同部位的油漆厚度不同。一般零件的涂层厚度控制在 0.1-0.2 毫米以内:精度要求高。例如,燃烧室表面的细颗粒涂层厚度应为 O. OSmn。对于闸门、立管、内流道和其他需要缓慢凝固的位置,可以厚一些,一般为 0.
2.3.3 过滤器
放置过滤器的目的是防止立管中的氧化物杂质进入空腔,形成层流充填。可采用廉价而有效的镀锌金属网,金属丝直径为 4--0.4--0. 6mm,1214 目。
2.3.4 温度
铝熔液的温度对缸盖的内部缺陷和外观质量影响很大。浇注度应在 680-730 范围内,实际操作中的温度偏差应控制在 20°C 以内。
低压铸造的特点是获得良好的顺序凝固。在此之后,重要的是控制报告的温度,使其在低压铸造中适中。理想的模具温度分布是从浇口到上模逐渐降低,并对每个零件的具体表面控制范围进行修改而得到的。上述温度场和缸盖铸件性能的改善及生产周期的缩短,必须在上模和侧模上强制执行。一般分为水冷和风冷,采用多通道设置,各通道独立自动控制(流量和压力)。水冷采用压送式水泵,解决模具内高温汽化导致水流不畅的问题,风冷采用压缩空气。
由于气缸盖有多个浇口,两个浇口之间的距离很短,会导致浇口之间的铸件部分温度升高,浇口和该部分的凝固顺序会颠倒。因此,必须在该部分设置局部强制冷却,以获得所需的温度梯度。
考虑到模具寿命和安全性,冷却方式应以间接冷却为主,局部铸件厚度较大时可采用直接冷却。冷却强度有两种方法:时间控制和温度控制。时间控制是指控制水或空气的通过时间。这种方法简单易行,但精度不高。温度控制是在冷却位置设置一个热电偶,PC 将根据热电偶测得的温度打开或关闭冷却水或冷却空气。控制精度相对较高。
近年来,凝固数值模拟技术的发展为缸盖低压铸造工艺的优化提供了很好的参考。它可以全面掌握不同条件下的凝固试验结果,加强对铸造过程的控制,确保铸件质量。
2.3.5 加压时间
浇口从充填到凝固的时间称为加压时间,它受温度的影响很大。在稳定的生产条件下,虽然加压时间随缸盖重量的变化而变化,但一般控制在 2-8min 左右。从提高生产效率的角度出发,可以采用一模两件、两级加压等方法来缩短时间。
2.3. 6 脱模时间
与加压时间一样,它也会随着温度的变化而变化。时间过短,铸件容易变形;时间过长,铸件容易卡在模具中无法取出。因此,一般控制在加压时间的 1/3 左右。为了提高铸件的冷却速度,拉模时可先开脱模阻力小的侧模,冷却一段时间后再开上模。
2.3. 7 压力曲线
加压压力直接影响流体的充型性能和熔融金属的喂料效果,加压曲线是低压铸造工艺控制的重要组成部分。加压压力可用下式计算:
P=γx(1+S/A) x ΔH x 10-2
上式中,P-压力(兆帕),γ-铝液比重(2. 4-2. 5),ΔH-铝液上升高度(米),S-提升管横截面积(平方米),A-空腔横截面积(平方米)o
冒口的进料压力一般约为 0. 005-0. 01MPa。虽然高压效果好,但如果压力超过 0.01 Mpa,就会造成涂料脱落,铝液堵塞模具通气孔,渗入砂芯。在浇注过程中,及时排出砂芯燃烧产生的气体是非常必要的,但由于缸盖所用砂芯结构复杂,数量最多,很难在模具上设置大量的排气孔。此时,将给料机的给料压力提高到接近上限,可有效防止气体卷入铸件。
柑橘洞中液位的变化会影响压力曲线的重复性,因此柑橘灾难中的压力应自动补偿。对于气缸盖铸件,可以设置传感器来精确控制压力曲线的零点 I81。
此外,如果立管下端与桔拐底部的间隔太短,溶液容易产生紊流。因此,在不影响溶液使用的情况下,立管下端与桔壶底部之间的距离约为 200 毫米。
铸造缺陷与对策
表 1 列出了低压铸造的常见缺陷和应采取的措施。对于气缸盖这样的复杂零件,各种参数的波动都可能影响铸件的质量。因此,有必要对工艺方案、模板设计、铸造工艺等多方面进行详细分析和调查,以明确缺陷产生的各种原因,并在此基础上采取相应措施。
Conclusion
迄今为止,铝合金缸盖是为数不多的适合低压铸造的有限汽车零部件之一。因此,他们充分发挥铝合金缸盖生产率高、内在质量好的优势,扩大国内铝合金缸盖低压铸造技术的生产和应用。以适应我国汽车技术的快速发展。