I.引言 由于生产条件和环境的变化,铸件的其他参数也会不可避免地发生变化。如果造型砂工艺不能及时调整,砂系就会不稳定,最终导致铸件清理更加困难,甚至报废;
这样,就需要对原有的造型砂工艺进行调整,以稳定砂系;造型砂的物质组成主要由旧砂、原砂、膨润土和添加剂组成。由于造型砂 95% 以上为旧砂,而旧砂又受铸件砂铁比不同、芯砂混入量不同等因素的影响,导致材料成分波动非常大。因此,要控制造型砂的成分,就必须检测造型砂中的有效膨润土含量、有效添加剂含量和含泥量,以确定混砂时膨润土、添加剂和原砂的添加量。
本文将简要介绍笔者所在企业的铸造车间是如何扎根于实际生产过程的。根据参数的变化,调整造型砂工艺,保证砂系统的稳定性。
2.成型砂关键参数的定义:
1.有效膨润土含量:有效膨润土(活性)含量是根据膨润土中所含蒙脱石矿物能吸附亚甲基蓝等染料的特性确定的,它是指用 5.00g 成型砂与 0. 20% 浓度试剂纯亚甲蓝溶液[mL]滴定;按膨润土标准曲线公式换算(%)。
2.有效添加剂用量:与成型砂添加剂的气体挥发量进行比较,计算公式为:900°C 下 1. 00g 成型砂的气体挥发量[mL]减去成型砂中活性膨润土的气体挥发量(计算前测得的平均量),然后与 1g 添加剂的气体体积(%)进行比较。
3.含泥量:根据国家标准 GB/T9442-1998,直径小于 20μm 的细粉末颗粒被定义为泥浆。通常采用冲洗法清除污泥[2]。
4.成型砂粒度:用 AFS 细度表示,即根据假想筛痕反映砂粒的平均粒度[3];
5.AFS 细度计算方法:美国铸造协会规定的 AFS 细度测量程序和计算方法如下:
①.首先称取约 50 克待测沙样,洗去泥土,晾干,然后过筛
②.称量并记录每个筛子上剩余沙粒的质量;
③.计算每个筛子上残留的沙粒量占沙样总量的百分比;
④.用每个筛子上残留的沙粒量的百分比乘以每个筛子对应的 "AFS 细度乘数";
⑤.将以上每个筛号的乘积相加,求出总和:
⑥.将第 5 项中得到的总和除以第 3 项中每个筛子上留砂百分比的总和,得出 AFS 细度
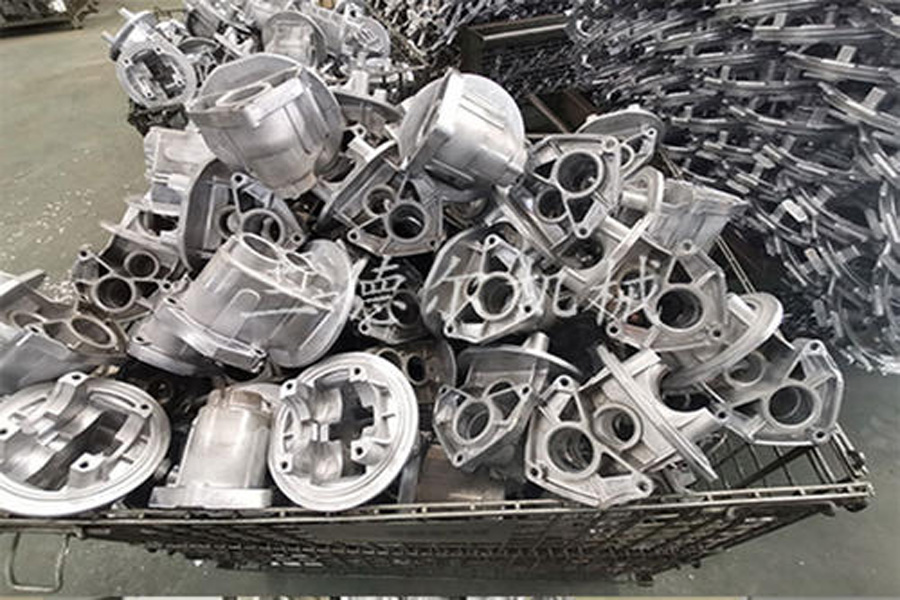
3.调整计划:
该厂使用的混砂设备是迪砂砂磨机和造型设备 KW 静压造型线,通过半年的数据统计,对其造型砂系统制定了如下方案:
1.统计资料:
① 根据造型主机的设定值,确定每箱铸件的造型砂加入量,并根据每箱铸件的重量和浇注系统的重量,以及铸件的芯砂用量,计算出每箱铸件的砂铁比;
废砂排放量、芯砂和辅助材料用量的统计数据
成型砂系统除尘统计
2.沙子调整:
根据生产情况,当一个铸件连续生产两天或两天以上时,造型砂辅料(膨润土、 添加剂)的添加量应固定,并统计造型砂有效用量的变化情况,然后在其他铸件的 连续生产过程中逐步验证砂铁比与添加量的关系;
成型砂粒度的调整:根据 50/100 筛的中值进行调整(50/100 筛的硅砂,平均细度的中值为 50 [4]),当成型砂的 AFS 小于或等于 50 时,通过添加细砂 70/140 或更细的新砂 140/70 进行调整,每台磨机添加 30kg-60kg,并分析粒度的变化。
成型砂含泥量的调整:通过对每天除尘量的统计,分析成型砂系统含泥量的变化;
第四,具体的调整过程:
1.铸造砂与铁的比例统计:
(注:由于 X2B1 缸体采用整体砂芯铸造,不会烧掉造型砂,因此铸件外造型砂的重量按 \"0\" 计算)。
2.根据铸件的砂铁比调整有效用量。56D 缸体的砂铁比为 6.57。在上述铸件中,气缸体铸件的砂铁比最高。因此,首先对 56D 缸体进行测试:
连续三天生产 56D 时,添加剂用量为 22kg/mill,粘土添加剂用量为 33kg/mill,添加剂的有效用量从 4.55%上升到 5.03%,粘土的有效用量从 6.56%上升到 7%,增加了约 0.5%,这说明生产 56D 筒体时,添加剂的用量应调整到高于砂系统的平衡值;
通过上述数据分析,辅料添加量调整如下:
1)筒体再现时,添加剂用量调整为 19kg/mill,粘土添加剂用量为 26kg/mill,连续三天的数据统计显示,添加剂有效用量由 4.7. 22% 变为 7.11% ;有效用量波动 0. 1% ;因此,工艺调整方案是合理的,能够保证造型砂系统的平衡;
2) 同样,通过实验数据分析和理论计算出其他铸件的辅助材料添加量与有效量之间的关系;在复制不同铸件时,调整适当的辅助材料添加量。
3.使用 70/140 目新砂和 140/70 目新砂调整砂粒大小(原型砂的含泥量为 11:)
从 1 月 16 日到 1 月 21 日,5 天内共磨砂 4257 次,约 4257*3/900=14 次,每次循环粒度变化约 0.26(每磨一次),因此,1 月 16 日成型砂的 AFS 值为 49.15;从 1 月 16 日开始,5 天内连续加入 70/140 新砂调整粒度,每磨一次 60kg,1 月 21 日成型砂的 AFS 值为 52.15;从 1 月 16 日开始,连续五天加入 70/140 新砂调整粒度,每磨 60kg,1 月 21 日成型砂的 AFS 值为 52.84;
从 1 月 25 日到 1 月 27 日,三天共磨砂 2165 次,约为 2165*3/900=7 个循环;每个循环的粒度变化约为 0. 22(每次磨砂);因此,1 月 24 日砂的 AFS =52.44,当成型砂粒度达到 52-53 时,连续加入 70/140 新砂对砂系 AFS 影响不大;从 1 月 26 日开始,连续三天加入 140/70 新砂进行调整,每次研磨加入 60kg,1 28 日砂 AFS 为 54。
(注:①一汽企业标准规定,70/140 石英砂 70、100、140 筛分率≥80%,其中 70、100 筛分率≥60%;140/70 石英砂 70、100、140 筛分率≥80%,其中 100、140 筛分率≥60%②每次研磨量为 3 吨,系统砂量预计为 900 吨。)
4.连续三个月的含泥量和除尘效果对比:
由于 2 月至 3 月北方气候寒冷,冷除尘管道中的粉尘在除去热粉尘后会凝结固化。如果不及时清理管道,就会经常出现堵塞现象,日排量在 4 吨至 8 吨不等。砂系统的含泥量波动很大。在此期间,只有通过增加除尘设备的风量和疏通管道,才能提高除尘能力,降低含泥量;
进入 4 月份后,温度逐渐升高,粉尘凝结固化现象不再出现,除尘量逐渐稳定,达到平均每天 7-8 吨的排量,含泥量波动范围减小;成型砂系统的含泥量也可以通过添加新砂或减少辅料添加量来降低。这两种方法的缺点将在试验结论中说明。
5.测试结论
1.调整砂配件的有效用量
膨润土晶体在加热过程中会受到一定程度的破坏,加水搅拌后湿粘结强度会明显下降。在较高温度和较长时间加热后,膨润土的晶体结构被完全破坏,成为没有内聚力的 "死粘土"。增加浇注厚度、降低砂铁比、提高浇注温度和延长冷却时间都会增加膨润土的烧失。
判断型砂中有效煤粉是否充足的最直接方法是观察铸件表面是否光滑,是否有粘砂现象。旧砂中的部分煤炭由于浇注熔融金属的热量而被烧毁,需要补充。另一方面,还需要添加新的材料,如新砂、混合芯砂和膨润土,以达到有效煤粉的水平。混砂过程中添加的煤粉总量是燃烧损失量和额外补充量之和。(有效煤粉相当于文中的有效添加剂)
2.调整砂粒大小:
高压造型砂的粒度一般为 50/140,而树脂砂芯的粒度大多为 50/100 或更粗。芯砂混入过多会影响整个旧湿砂的粗化,从而增加砂的透气性,使铸件表面粗糙。
为了防止造型砂的粒度变粗,可将除尘系统中的颗粒回收到旧砂中。或加入细的新砂进行调整;如铸造厂所述,当造型砂的 AFS 达到 48 左右时,可通过不断加入 70/140 或 140/70 的新砂进行调整;但由于铸件被打入砂系统的核心,砂量已经很大。如果造型砂的粒度没有粗化到无法忍受的程度,不建议连续加入如此大量的新砂,否则会对造型砂系统的其他性能指标(含泥量、有效含泥量、因新砂量过大而产生的强度)产生影响。)有影响;
3.调整泥浆含量
含泥量的增加会导致造型砂的透气性下降,浇注过程中会出现 "气爆 "现象,铸件会因爆炸粘砂而报废。造型砂体系的含泥量不宜过高;砂体系的含泥量可以通过减少辅助材料的用量来降低,但有效膨润土含量的减少会造成造型砂强度下降,提砂和抗砂能力降低;有效用量的减少会造成造型砂抗粘砂能力降低。
如果要增加新砂的加入量来调整含泥量,首先要计算出各种新加入的材料在型砂中产生了多少泥,然后才能计算出需要加入多少原砂才能使型砂的含泥量达到工艺规程的要求。
文章中提到,铸造车间每增加 30 kg 新砂,含泥量可降低 0.1%;但过多地增加新砂,不仅会造成成本浪费,还会降低造型砂系统中的旧砂比例,降低造型砂的性能。造型砂发散,影响造型砂的造型能力,在铸造过程中出现洗砂现象;
因此,笔者认为,如果能通过调整除尘设备来控制砂系统的含泥量,则是最佳选择。
总而言之,稳定砂系统就是要能够生产出高质量的铸件。通过这一理念,我们必须根据生产条件的变化不断调整造型砂工艺,以满足生产需要。