1.铸造涂层的主要技术指标
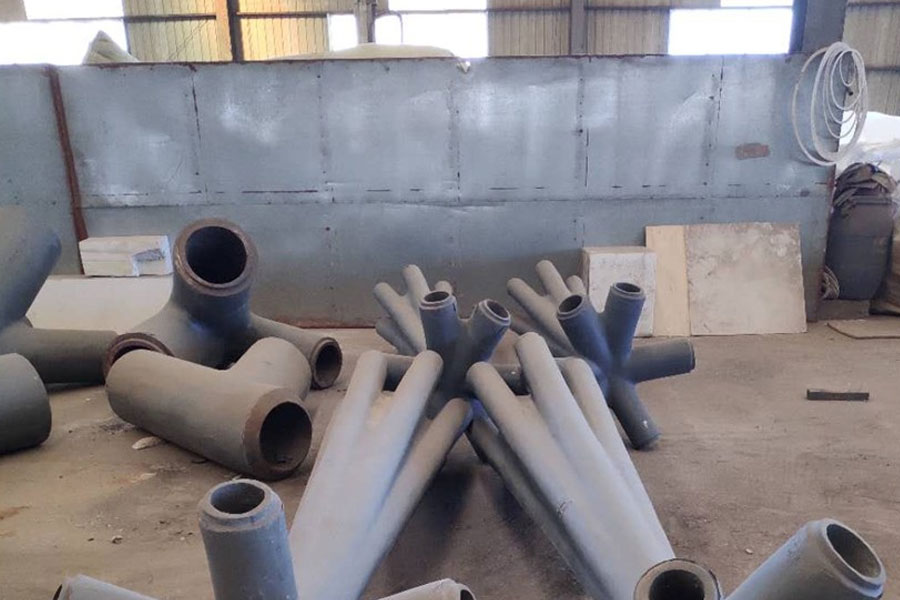
density
铸造涂料的密度反映了涂料中固体颗粒的多少。如果铸造涂料的密度太小,每次涂刷时在砂型和砂芯表面形成的涂料层厚度就不够,难以起到保护作用。因此,一般来说,铸造涂料的致密性是好的,但涂料的致密性;越大越好,如果致密性太大,涂料就难以涂抹,会造成涂料表面不平整、局部堆积等问题。而且还会对铸件质量产生不利影响。涂料密度和浓度之间存在一定的关系。铸造涂料的密度可以用量筒称量法或 Baumemeter 测量,但 Baumemeter 的读数受铸造涂料粘度的影响很大。
条件粘度
4 号和 1 号粘度杯通常用于铸造生产,以确定涂料的条件粘度。测量粘度的目的是控制涂料的可涂抹性、渗入砂模和型芯表面的深度以及涂层的厚度。一般来说,铸造涂料制造商都有推荐的涂料条件粘度。
Suspension
悬浮是铸造涂料的一项重要性能。一般的测量方法包括相对高度沉降法(量筒法)、沉降仪法和沉降速率法。其中,量筒法是最简单实用的方法。
Paintability
一般根据操作员的经验来判断,更客观的方法是测定不同剪切速率下铸造涂料的表观粘度。涂料在低转速(6r/min)和高转速(60r/min)下的表观粘度之比就是涂装指数 M。
Leveling
在砂模或砂芯表面刷涂或流涂涂料时,涂层在刷涂或流涂后堆积,表面往往会出现凹槽和刷痕。这些沟槽和刷痕可能会在短时间内消失,也可能会保留下来。能使湿涂料层表面的刷痕或凹槽自动消失的能力称为流平。
Flowability
由于重力的影响,铸造涂料在模具(型芯)的垂直表面上有向下流动的趋势,下层涂料的厚度大于上层涂料的厚度,甚至在模具(型芯)底部出现堆积现象。这种特性被称为流动性。
Permeability
铸造涂料的渗透性是指涂料渗入砂型孔隙的能力。铸造涂料的渗透率大,可以增强涂料对砂型的附着力,同时可以加固砂型,提高砂型的抗砂性。涂层的渗透深度可通过浸渍标准砂块来测试。
涂料的 pH 值:一般来说,铸造涂料的 pH 值在 4 至 11 之间,但碱性铸造涂料更常用,通常在 8 至 10 之间。pH 值不仅可作为铸造涂料的性能指标,还可作为涂料在使用和储存过程中的性能监测方法。它是涂料生产和使用过程的监测指标。通常涂料可通过比色法和电位计法进行测量。
涂层透气性
涂层在金属和砂模(型芯)表面之间形成隔离层。涂层要求致密。除泡沫脱落涂层外,透气性应较低。透气性可通过在一定压力下使用一定量的空气通过标准圆柱形样品来测量。
涂层的抗摩擦强度
砂模和砂芯涂覆后,必须经过搬运、烘干、除去表面灰尘、配盒等工序而不被损坏。因此,干燥固化后的涂层必须具有一定的表面抗磨强度。测量涂层抗划伤强度比较准确的方法有划痕法、压力法、机械擦洗法、落砂法和振动法等。.涂料生产商可以通过手工划痕法测定涂层的抗划伤强度。这种方法可将涂层的抗划伤强度分为四个等级:
用手刮法测量的涂层表面强度与附着粘合剂的类型和数量有关。随着粘合剂用量的增加,涂层的表面强度也随之增加。这表明影响涂层表面强度的主要因素是粘合剂的数量和类型。在考虑表面强度时,主要考虑粘合剂的影响。
涂料吸湿性
涂有水性涂料的砂型和砂芯在干燥后会吸收空气中的水分,使其性能变差,强度降低,气量迅速增大。严重时会导致铸件出现粘砂、结构疏松和气孔等缺陷。.涂料的吸湿性主要与粘合剂有关,水溶性粘合剂具有较强的吸湿性。对于铸造前涂有涂料的砂模和砂芯的长期存放,必须检测涂料的吸湿性。
测定涂层吸湿性的基本方法是将涂层样品放置在一定湿度的恒湿箱中一段时间,然后在保养前后称量样品的重量。
涂层导热性
在选择金属涂料时,铸件涂料的隔热性能和冷却性能尤为重要。冷却涂层用于铸件的厚壁,以加速铸件的冷却;隔热涂层用于薄壁,以缓慢冷却铸件。涂层的导热系数可通过浸入熔体法进行测量。
所谓气体演化是指单位质量分数的涂料在高温下产生的气体体积,以毫升/克为单位,用专用的气体排放计测量。
点火损失
点火损失是指在 105-110°C 下烘干的涂料样品占原重量的百分比。在非氧化气氛中逐渐加热至 950-1000°C 并燃烧 1 小时后,样品的重量损失为原始重量的百分比。
涂料烧结点
铸造涂料的烧结点表示涂料耐火填料颗粒表面或颗粒间混合物开始熔化的温度。有 SJY 图像式烧结点测试仪法和管式炉烧结法来确定涂料的几个接触点。采用五级评估法进行评估。
涂层耐火度
指铸造涂层中耐火粉末的熔点或软化点,即耐高温的能力。
涂层耐热性和抗裂性
铸造涂层的抗热裂性是指涂层抵抗高温加热引起的裂纹和剥落的能力。采用四级评价法进行测定。
从上述性能指标可以看出,铸造涂料作为一种特殊的涂料类别,其基本要求与常用涂料并无太大区别。无非是从涂层、涂装、使用效果三个方面考虑。如果不考虑高温性能,一般的民用涂料研究人员完全可以理解并介入这类涂料的研究。我国现有的铸造涂料水平,包括沉降、浇铸等较强的铸造涂料,也与国外产品有较大差距。笔者相信,只要有心,广大铸造涂料研究人员一定能够为我国在这一领域的发展,进而为我国铸造业的发展做出贡献。