铝镁合金因其密度低、强度高而得到越来越广泛的应用。其中,铝镁合金压铸技术作为一种先进的切削工艺,具有生产效率高、节约原材料、降低生产成本、产品性能好、精度高等特点。铝镁合金主要应用于电子、汽车、电机、家电等行业,一些高性能、高精度、高韧性的优质铝镁合金产品也已应用于大型飞机、船舶等技术要求相对较高的行业。
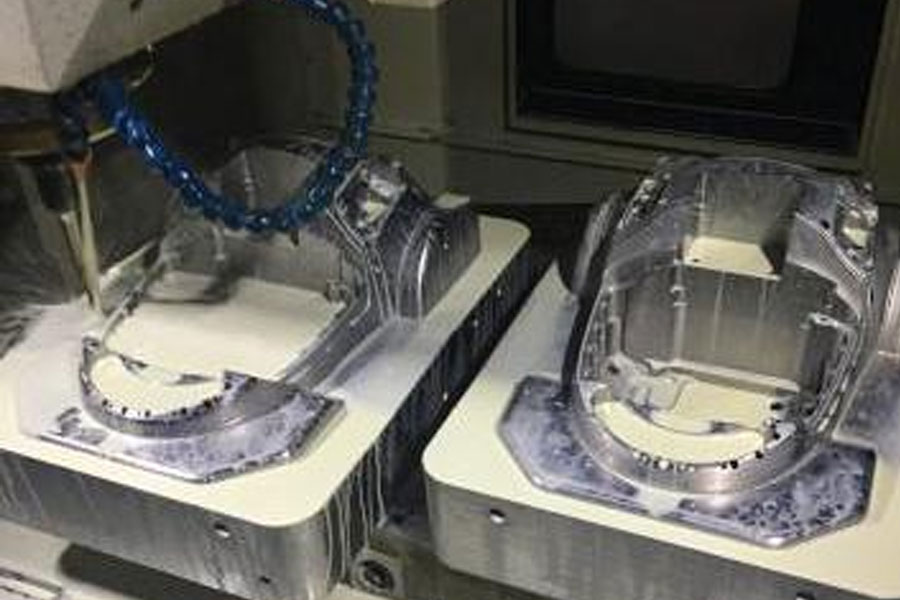
铝镁合金压铸模具的工作条件和性能要求
铝镁合金压铸模具是一种成型模具,用于在压铸机上压铸铝镁合金铸件。铝合金的熔点为 600~750℃,镁合金的熔点为 600~700℃。工作表面温度一般可升至 500~600℃。型腔、芯轴和喷嘴的表面都承受着剧烈的温度波动,模具表面容易出现热疲劳裂纹。此外,铝镁合金在压铸过程中容易粘附在模具表面,影响压铸生产的连续运行。液态铝镁合金对模具表面有很强的侵蚀作用。因此,制造铝镁合金压铸模具,要求模具材料在 600°C 左右具有较高的回火稳定性和抗冷热疲劳性,并具有良好的耐高温、高压、高速和高抗液态铝镁合金侵蚀性。的强度和韧性,同时需要正确的热处理来挖掘模具材料的潜力,提高模具的使用寿命。目前,模具制造中常用的铝镁合金压铸模钢包括3Cr2W8V 钢、4Cr5MoSiV1 钢、4Cr3Mo3SiV 钢、4Cr5MoSiV 钢,以及新钢种 4Cr5Mo2MnSiV1 钢和 3Cr3Mo3VNb 钢。
铝镁合金压铸模具的制造工艺路线
铝镁合金压铸模具的制造工艺为:冲裁→锻造→球化退火→机加工→淬火、回火→修整、打磨、抛光→氮化(软氮化)→组装和使用。
铝镁合金压铸模具的强化和增韧处理工艺
铝镁合金压铸模具的增韧处理是通过改变钢的结构来获得模具所需的结构和性能。热处理应根据模具材料、模具形状、尺寸和复杂程度来确定热处理工艺规范。
3.1 预热处理
压铸模具的预热处理可采用连续退火、等温退火和淬火回火热处理三种工艺。目的是在最终热处理前获得均匀的组织和分散的碳化物,以提高钢的强度和韧性。连续退火工艺相对简单,也可获得较好的粒状珠光体结构。对于形状复杂、要求较高的压铸模具,可采用等温退火工艺,以获得更理想的粒状珠光体结构。
3.2 淬火和预热
压铸模具钢多为导热性能较差的高合金钢。在淬火和加热过程中通常会采取预热措施。预热次数和温度取决于模具钢的成分和对模具变形的要求。对于淬火温度低、形状简单、变形要求低的模具,在淬火和加热过程中需要进行一次预热(800~850℃),且不会产生裂纹。对于淬火温度较高、形状复杂和变形要求较高的模具,需要进行二次预热(600-650℃,800-850℃)。目的是减少加热过程中产生的应力,同时使模具的整体结构均匀。
3.3 淬火加热
压铸模具的淬火加热温度可根据各钢种的淬火加热规格执行。例如,3Cr2W8V 钢的淬火温度为 1050~1150℃,H13 钢的淬火温度为 1020~1100℃。提高这两种钢的淬火温度可以提高压铸模具的高温强度和抗热疲劳性能,但会增加模具的变形。在盐浴炉中加热时,为避免模具表面氧化脱碳,应使用脱氧效果好的氯化钡盐浴,并应经常脱氧。在箱式电阻炉中加热时,应采用保护气氛;或在包装后在普通箱式电阻炉中加热。为了保证碳化物的充分溶解,获得均匀的奥氏体,获得良好的高温性能,应适当延长压铸模具的淬火和加热保温时间。一般来说,盐浴炉中的加热保温系数为 0.0 min/mm。
3.4 淬火冷却
油淬速度快,性能好,但变形和开裂倾向大。一般情况下,形状简单、变形要求低的压铸模具采用油冷淬火;形状复杂、变形要求高的压铸模具应采用分层淬火,以防止模具变形和开裂。淬火冷却应尽量缓慢,以减少淬火变形,在真空电阻炉中加热淬火,冷却时可采用气淬。在盐浴炉中加热淬火,冷却时可采用分级淬火。模具淬火冷却时,一般冷却至 150~200℃,浸泡后立即回火。不允许冷却至室温。
3.5 回火
压铸模具的硬度是通过回火实现的,压铸模具型腔的硬度直接影响模具的冷热疲劳寿命。不同的材料,淬火温度不同,回火温度也不同。例如,3Cr2W8V 钢铝镁合金压铸模的硬度一般为 42~48HRC,其回火温度一般选择在 560~620℃ 之间,但如果采用高温淬火,回火温度则高达 670℃。在 1150℃淬火、650℃回火后的硬度为 45HRC;而在 1050℃淬火、650℃回火后的硬度为 35HRC。H13 钢铝镁合金压铸模的硬度要求为 44~50HRC。H13 钢在 500℃回火时出现二次硬化峰,但峰值的大小与淬火温度有关。回火温度一般为 560~620℃。回火应进行 2 至 3 次。第一次回火的温度可以低一些。第一次回火后,测量硬度值。如果达到硬度要求,回火温度应降低 20~30℃,以避免硬度下降。如果硬度过高,应根据硬度高低适当调整回火温度,以满足硬度要求。第三次回火是为了提高韧性,回火温度应高于第二次回火。
二次回火温度低 30~50℃。回火和保温时间应足以消除淬火时产生的应力,减少模具裂纹的形成。每次回火的保温时间为 2 小时,大型模具的保温时间可适当延长。由于压铸模具淬火后热应力和微观结构应力较大,一般在冷却至 150-200°C 后立即进行回火。
铝镁合金压铸模具的表面强化处理工艺
铝镁合金压铸模经过淬火和回火后,表面硬度不是很高。为了使模具表面获得较高的硬度和耐磨性,而芯部仍保持足够的强度和韧性,并提高铝镁合金压铸模具的抗粘连性能,可对模具进行表面渗氮或氮化处理。渗碳处理。
4.1 氮化处理
氮化是对钢材表面进行氮化处理,以提高表层氮浓度的一种热处理工艺。氮化的目的是减少模具零件的变形,提高铝镁合金压铸模具的表面硬度、耐磨性、疲劳强度和抗咬合性能,提高模具对大气和过热蒸汽的耐腐蚀性,提高抗回火和软化性能。缺口敏感性。固体氮化、液体氮化和气体氮化是常见的氮化方法。离子氮化、真空氮化、电解氮化和高频氮化等新技术可大大缩短氮化周期,获得高质量的氮化层,提高企业的经济效益,因此在生产中得到广泛应用。
4.2 渗氮
硝基渗碳是氨加醇类液体(甲醇、乙醇)和共渗介质,如尿素、甲酰胶和三乙醇胶。在一定温度下发生热分解反应,产生活性氮和碳原子,由铝镁合金压铸而成。模具表面吸收后,扩散并渗入模具表层,获得氮基软化层,从而使模具获得更高的表面硬度、抗疲劳性、耐磨性和耐腐蚀性。软氮化方法包括液态软氮化和气态软氮化,生产中使用最多的是气态软氮化。H13 钢铝合金压铸模在高温盐浴炉中经过 550℃×40min、850℃×40min 两段预热处理,1030℃淬火,600℃回火,然后在 580℃下进行气体软氮化热处理。硬度在 900HV 以上,基体硬度在 46~48HRC 之间,模具的耐磨性、抗疲劳性和耐腐蚀性明显提高,无粘连、剥落、划痕和腐蚀,有效提高了模具的使用寿命。
Conclusion
铝镁合金压铸模具作为重要的加工设备,直接影响着企业的产品质量和经济效益。调查统计表明,由于热处理工艺不当造成的模具故障约占总故障的 50%。因此,合理选择强化增韧处理和表面强化处理工艺,严格控制热处理工艺规范,是提高模具性能和寿命的重要途径。在铝镁合金压铸模具生产中,要根据模具工况分析研究失效原因,合理制定热处理工艺,确保模具表面硬度、耐磨性、型芯强度和韧性,防止金属液腐蚀和模具粘连,有效降低废品率,显著提高模具使用寿命。