锻造是锻造和冲压的统称。它是利用锻造机的锤子、砧子、冲头或模具对坯料施加压力,使其产生塑性变形,从而获得工件所需形状和尺寸的一种成形加工方法。.
在锻造过程中,整个坯料发生明显的塑性变形,塑性流动量比较大;而在冲压过程中,坯料主要是通过改变各部分区域的空间位置形成的,内部没有大距离的塑性流动。锻造主要用于加工金属零件,也可用于加工某些非金属,如工程塑料、橡胶、陶瓷坯料、砖坯以及复合材料的成型。
冶金工业中的锻造、轧制和拉拔都属于塑性加工或压力加工,但锻造主要用于生产金属零件,而轧制和拉拔主要用于生产板材、带材、管材等。型材和线材等通用金属材料。
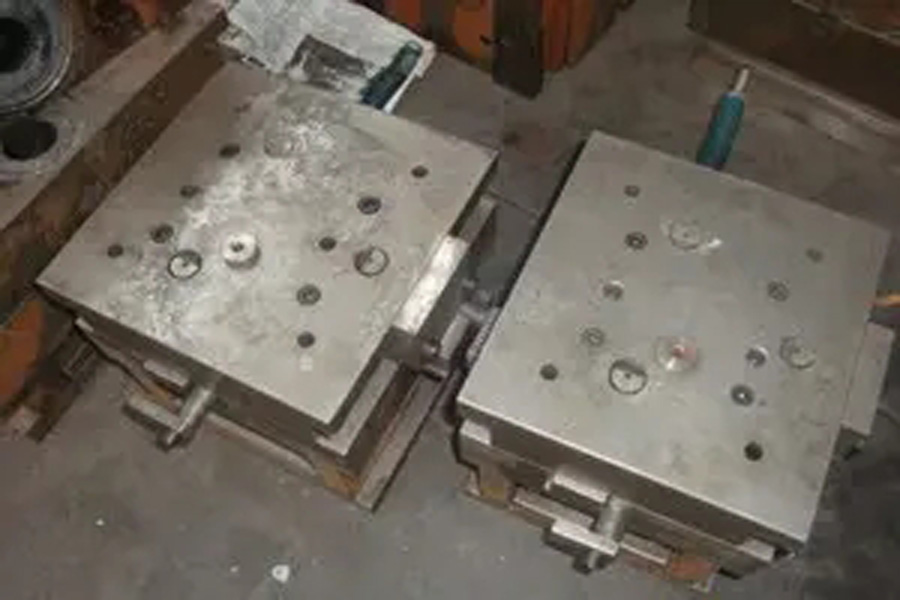
新石器时代末期,人类开始用锤子敲打天然红铜,制作装饰品和小物品。大约在公元前 2000 年,中国已经使用冷锻工艺制作工具。例如,甘肃武威黄娘台齐家文化遗址出土的红铜器物上就有明显的锤击痕迹。在商代中期,陨铁被用来制作武器,使用的是加热锻造工艺。春秋晚期出现的块状熔炼锻铁是通过反复加热和锻造挤压氧化物夹杂物而形成的。
起初,人们*裹着锤子进行锻造,后来出现了通过拉绳和滑轮举起重锤,然后自由下落锻造坯料的方法。14 世纪后,出现了畜力和液压落锤锻造。
1842 年,英国人纳斯密斯制造出第一台蒸汽锤,使锻造进入了应用动力时代。随后,锻造液压机、马达驱动的夹板锤、空气锻锤和机械压力机相继出现。夹板锤最早在美国南北战争(1861-1865 年)期间用于模锻武器零件,随后欧洲出现了蒸汽模锻锤,模锻技术逐渐得到推广。到 19 世纪末,现代锻造机械的基本范畴已经形成。
20 世纪初,随着汽车开始批量生产,热模锻迅速发展并成为主要的锻造工艺。20 世纪中期,热模锻压力机、平锻机和无砧锻锤逐渐取代了普通锻锤,提高了生产率,减少了振动和噪音。随着锻造新工艺的发展,如锻坯少氧化和无氧化加热技术、高精度长寿命模具、热挤压、成形轧制以及锻造机械手、机械手和自动锻造生产线等,锻造生产的效率和经济效果不断提高。
冷锻的出现早于热锻。早期的铜片、金片、银片和硬币都是冷锻而成的。冷锻在机械制造中的应用普及于 20 世纪。冷镦、冷挤压、径向锻造、摆动锻造等工艺相继发展,逐渐形成了无需切削即可生产精密零件的高效金属锻造工艺。
早期的冲压仅使用铲子、剪子、冲子、手锤和铁砧等简单工具,通过手工切割、冲压、铲打和敲击形成金属板(主要是铜板或铜合金板等)。制造锣、钹等乐器和壶。随着中厚板产量的增加以及冲压液压机和机械压力机的发展,冲压加工也在 19 世纪中期开始机械化。
1905 年,美国开始生产热连轧窄带卷钢。1926 年,美国开始生产宽钢带。后来,又出现了冷连轧带钢。与此同时,板材和带材的产量增加,质量提高,成本降低。随着船舶、铁路车辆、锅炉、集装箱、汽车、易拉罐等生产的发展,冲压已成为世界上最重要的钢铁生产设备之一。冲压已成为应用最广泛的成形工艺之一。
锻造主要按成形方法和变形温度分类。根据成形方法,锻造可分为锻造和冲压;根据变形温度,锻造可分为热锻、冷锻、温锻和等温锻。
热锻是在金属再结晶温度以上进行的。提高温度可以改善金属的塑性,有利于提高工件的内部质量,使其不易开裂。高温还可以降低金属的抗变形能力,减少所需的锻造机械吨位。但热锻工艺多,工件精度差,表面不光滑,锻件易氧化、脱碳和烧损。
冷锻是在低于金属再结晶温度下进行的锻造。一般来说,冷锻特指在室温下进行的锻造,而在高于室温但不超过再结晶温度下进行的锻造则称为温锻。锻造。温锻具有精度高、表面更光滑、抗变形能力低等优点。
常温下冷锻成形的工件形状和尺寸精度高,表面光滑,加工工序少,易于实现自动化生产。许多冷锻件和冷冲压件无需切削加工就可直接用作零件或产品。但在冷锻过程中,由于金属塑性低,变形时容易开裂,变形阻力大,需要大吨位的锻造机械。
等温锻造是指在整个成形过程中,坯料的温度保持恒定。等温锻造是为了充分利用某些金属在恒温下的高塑性,或获得特定的结构和性能。等温锻造要求模具和坯料保持恒温,成本较高,仅用于超塑性成形等特殊锻造工艺。
锻造可以改变金属结构,改善金属性能。钢锭经热锻造后,原有的铸态疏松、气孔、微裂纹等被压实或焊接;原有的树枝状晶体被破碎,使晶粒更细;同时,原有的碳化物偏析和不均匀被改变分布,使组织均匀,从而获得内部致密、均匀、细度好、综合性能好、使用安全的锻件。锻件经热锻变形后,金属呈纤维状结构;锻件变形后,金属晶体排列有序。
锻造是通过金属的塑性流动制成所需形状的工件。在外力作用下产生塑性流动后,金属的体积不会发生变化,金属总是流向阻力最小的部位。在生产中,工件的形状通常根据这些规则进行控制,以实现镦粗拉拔、扩孔、弯曲和拉伸等变形。
锻造工件尺寸准确,有利于组织批量生产。模锻、挤压、冲压等应用尺寸准确稳定。高效锻造机械和自动锻造生产线可用于组织专业化批量或大批量生产。
锻造的生产过程包括成形前的毛坯冲裁、毛坯加热和预处理;成形后的工件热处理、清洗、校准和检验。常用的锻造设备包括锻锤、液压机和机械压力机。锻锤冲击速度大,有利于金属的塑性流动,但会产生振动;液压机采用静态锻造,有利于锻透金属,改善结构,工作稳定,但生产率低;机械压力机行程固定,易于实现机械化和自动化。
未来,锻造工艺将在提高锻件内在质量、开发精密锻造和精密冲压技术、开发生产率和自动化程度更高的锻造设备和锻造生产线、开发柔性锻造成形系统、开发新型锻造材料和锻造加工方法等方面不断发展。
提高锻件的内在质量主要是为了改善其机械性能(强度、塑性、韧性、疲劳强度)和可靠性。这就需要更好地应用金属塑性变形理论;应用内在质量更好的材料;正确的锻造前加热和锻造热处理;对锻件进行更严格、更广泛的无损检测。
少切削、无切削加工是机械工业提高材料利用率、提高劳动生产率、降低能源消耗的重要措施和方向。少锻坯、无氧化加热,以及开发高硬度、耐磨、长寿命的模具材料和表面处理方法,将有利于扩大精密锻造和精密冲压的应用范围。