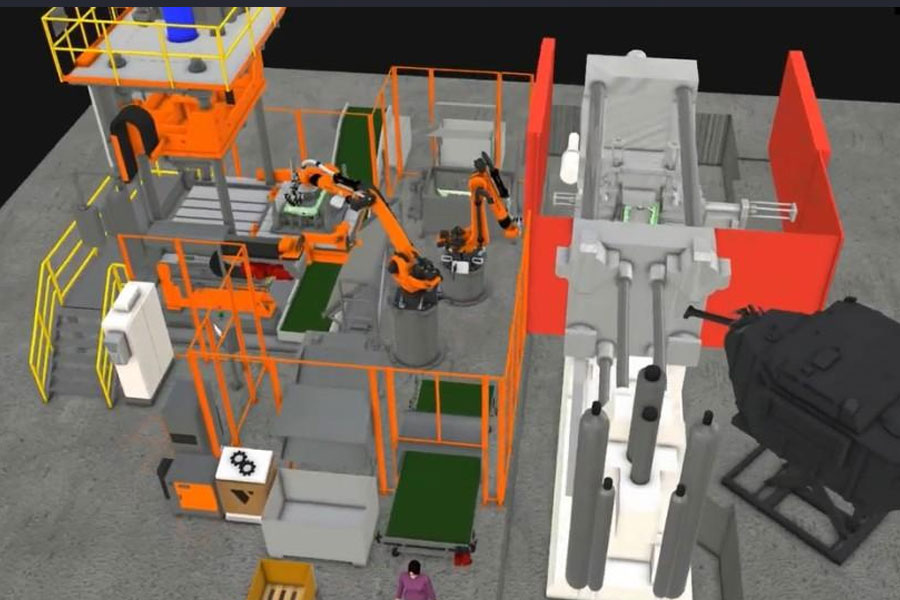
在气缸体生产领域,普通砂型铸铁气缸体具有工艺简单、成本低、刚性好、耐热性强等优点,但也存在重量过大的缺点。
如果把气缸体下面的曲轴和气缸体上面的气缸套一分为二,下面用铝合金,上面用铸铁,就可以一举两得,既降低了气缸体的质量,又保持了铸铁气缸体的优点。
下缸体是指发动机曲轴一分为二后的下部。由于下缸体是厚壁件,且壁厚变化很大,压铸成型难度很大。我们借鉴国内外相关经验,设计开发了一套适用于 1.5T 发动机的下缸体压铸工艺,试验非常成功。
1.铝合金下缸体的压铸难题
铝合金下缸体铸件质量为 8.4kg,外形尺寸为 382mm×258mm×67mm,压铸件质量为 11.1kg,材料为 A380,平均壁厚为 7.2mm。1 kg,材料为 A380,平均壁厚为 7.2 mm。由于下缸体与曲轴相连,因此需要在底部放置一个铸铁镶块。
下缸体铸件的压铸工艺比较复杂,主要难点如下:
2.铝合金下缸体压铸技术要点
根据试验分析,我们认为下缸体压铸生产的主要技术要点如下:
在下缸体的压铸过程中,科学合理的工艺参数是获得高质量下缸体的保证。我们认为,以下工艺参数是铸造成型的关键影响因素:
3.铝合金下气缸压铸件的缺陷及对策
铸件成型后,我们对铸件进行了 X 射线检查,发现铸件存在一些内部缺陷,如缩孔、气孔和缩孔。
为了改善缺陷,提高质量,我们提出了相应的对策,主要方向如下:
4.结论
近年来,随着我国节能减排政策的推进和汽车轻量化的大趋势,铝合金材料在汽车上的应用越来越广泛,越来越多的汽车零部件采用压铸成型,其中就包括汽车的核心部件--发动机。目前,采用铝合金铸造下缸体已成为一种趋势,它可以减轻缸体的重量,获得质量更好的缸体。但由于下缸体结构复杂,壁厚差异较大,铝合金下缸体的压铸难度较大。
本文通过实验研究,分析了铝合金下缸体压铸技术的难点,提出了科学设计的缸体压铸铸造系统,采用齿形冷态排气缸体真空压铸技术对镶块等铝合金进行预热。下缸体压铸技术要点。此外,还总结了铝合金下缸体的压铸缺陷,如缩孔、气孔、缩孔气隙等,并提出了相关对策,为汽车发动机铝合金下缸体的压铸提供了理论参考。