1 球墨铸铁的凝固特性 球墨铸铁和灰铸铁的凝固方式不同,是因为球状石墨和片状石墨的生长方式不同。
在低共晶灰铸铁中,石墨开始在原生奥氏体边缘析出。石墨片的两侧被奥氏体包围,并从奥氏体中吸收石墨使其变厚。石墨片的尖端位于液体中。它通过吸收石墨生长。
在球墨铸铁中,由于石墨是球形的,石墨球在析出后开始吸收周围的石墨。由于 w(C) 量减少,周围的液体变成固态奥氏体并包围石墨球;在奥氏体的包围下,能从奥氏体中吸收的碳相对有限,而液体中的碳通过固体缓慢扩散到石墨球中,奥氏体的包围限制了它的生长;因此,即使球墨铸铁的碳当量远高于灰铸铁,球墨铸铁的石墨化也更加困难,因此没有足够的石墨化膨胀来抵消凝固收缩;因此球墨铸铁容易产生缩孔。
此外,包裹石墨球的奥氏体层厚度一般是石墨球直径的 1.4 倍。也就是说,石墨球越大,奥氏体层越厚,液体中的碳就越难通过奥氏体转移到石墨球上。大[1]。
低硅球墨铸铁容易出现白口的根本原因还在于球墨铸铁的凝固方式。如上所述,由于球墨铸铁的石墨化困难,石墨化产生的结晶潜热没有足够的时间释放到铸型中,增加了过冷度,石墨来不及析出形成胶结物。此外,球墨铸铁具有生长快、下降快的特点,这也是极易出现过冷的因素之一[1]。
2 无冒口铸造球墨铸铁的条件
从球墨铸铁的凝固特点不难看出,球墨铸铁件实现无冒口铸造的难度较大。笔者根据多年的生产实践经验,对球墨铸铁实现无冒口铸造工艺所需的条件进行了一些归纳和总结,在此与同仁分享。
2.1 铁水成分的选择
2.1. 1 碳当量 (CE)
在相同条件下,微小的石墨容易溶解在铁水中,不易长大;随着石墨的长大,石墨的生长速度也变快,因此原生石墨在铁水中共晶之前产生,对促进共晶凝固石墨化非常有利。具有过共晶成分的铁水可以满足这样的条件,但过高的 CE 值会导致石墨在共晶凝固前长大,当长大到一定尺寸时,石墨开始上浮,造成石墨上浮缺陷。此时,石墨化引起的体积膨胀只会导致铁水液面上升,不仅对铸件的进料没有意义,而且由于石墨在液态时吸收了大量的碳,在共晶凝固时会导致铁水凝固。介质中低含量的 w(C) 无法产生足够的共晶石墨,也无法抵消共晶凝固造成的收缩。实践证明,将 CE 值控制在 4.30% 和 4.50% 之间是最理想的。50%.
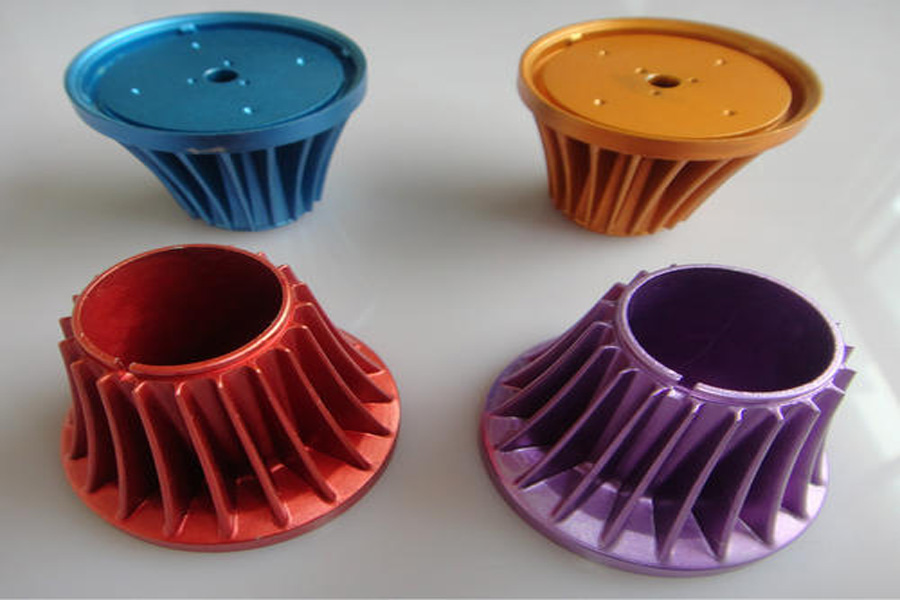
2.1. 2 硅 (Si)
一般认为,在 Fe-C-Si 合金中,Si 是一种石墨化元素,大量的 w(Si)有利于石墨化扩展,可以减少缩孔的发生。很少有人知道 Si 会阻碍共晶凝固石墨化。因此,无论从喂料还是防止碎裂石墨产生的角度来看,只要能通过强化接种等措施防止白口,就必须尽可能减少 w(Si)的用量。
2.1.3 碳 (C)
在合理的 CE 值条件下,尽可能增加 w(C) 的用量。事实证明,球墨铸铁的 w(C) 含量控制在 3. 60%~3. 70%,铸件的收缩率最小。
2.1.4 硫 (S)
S 是阻碍石墨球化的主要元素。球化的主要目的是去除 S。然而,球墨铸铁的快速生长和衰退与 w (S) 的低含量有直接关系,因此需要适量的 w (S)。w(S) 的量可控制在 0. 015% 左右,并可利用 MgS 的成核效应来增加石墨芯颗粒,从而增加石墨球的数量,减少衰退[2]。
2.1. 5 镁 (Mg)
镁也是一种阻碍石墨化的元素,因此在球化率能达到 90% 以上的前提下,镁的含量应尽可能低。在原铁水 w(O)和 w(S)不高的条件下,残余 w(Mg)含量控制在 0. 03%~0. 04% 是最理想的。
2.1. 6 其他要素
锰、钾、铬和其他阻碍石墨化的元素尽可能少。
注意微量元素(如 Ti)的影响。当 w(Ti)的含量较低时,它是一种强烈促进石墨化的元素。同时,Ti 是一种形成碳化物的元素,也是一种影响球化和促进蛭石石墨生成的元素。因此,w(Ti)的含量越低越好。笔者所在的公司曾经有一套非常成熟的非冒口铸造工艺。由于原材料暂时短缺,公司使用了 w(Ti)含量为 0.1%的生铁。生产出的铸件不仅表面有缩孔,而且在加工后内部也出现了集中类型。缩孔。
总之,纯净的原材料有利于提高球墨铸铁的自进料能力。
2.2 浇注温度
实验表明,球墨铸铁的浇注温度从 1 350 ℃ 到 1500 ℃,对铸件的缩孔体积无明显影响,但缩孔形态逐渐从集中型过渡到分散型。随着浇注温度的升高,石墨球的尺寸逐渐增大,石墨球的数量逐渐减少。因此,没有必要要求过低的浇注温度。只要模具足够坚固,能够抵抗铁水的静压力,浇注温度就可以高一些。铁水用于加热模具,以降低共晶凝固过程中的过冷度,从而使石墨化有足够的时间进行。但浇注速度应尽可能快,以尽量减少铁水在模具中的温差[3]。
2.3 冷铁
根据笔者使用冷烫的经验和上述理论分析,冷烫可以消除收缩缺陷的说法并不准确。一方面,局部使用冷铁(如穿孔件)只能转移收缩型腔而不能消除收缩型腔;另一方面,大面积使用冷铁可以达到减少进料或不冒口的效果。无意识地增加模具强度而不是冷铁,会减少液态或共晶凝固收缩。事实上,如果过多使用冷铁,会影响石墨球的生长和石墨化程度,反而会加剧收缩。
2.4 模具强度和刚度
由于球墨铸铁大多选择共晶或超共晶成分,因此铁水在铸型中冷却到共晶温度需要较长的时间,即铸型的静水压力比共晶成分的静水压力长。如果灰铸铁的时间更长,模具就更容易产生压缩变形。当石墨化膨胀引起的体积增加无法抵消液体收缩+凝固收缩+模具变形体积时,缩孔是不可避免的。因此,足够的模具刚性和抗压强度是实现无冒口铸造的重要条件。有许多实现无冒口铸造的砂包铁铸造工艺就是这一理论的证明。
2.5 接种处理
强力孕育剂和瞬间延时孕育工艺,既能使铁水获得大量的铁芯颗粒,又能防止孕育量下降,还能保证球墨铸铁在共晶凝固过程中有足够的石墨球;石墨球大而小,减少了液中 C 向石墨芯的传递距离,加快了石墨化速度。在短时间内,大量的共晶凝固可以释放出更多的结晶潜热,降低过冷度,防止白口的产生,同时还可以强化石墨化膨胀。强孕育对提高球墨铸铁的自养能力至关重要。
2.6 液体铁过滤
铁水经过过滤后,一些氧化夹杂物被滤出,从而提高了铁水的微流动性,降低了微观收缩的概率。
2.7 铸造模数
由于铸造珠光体球墨铸铁时需要添加阻碍石墨化的元素,这将影响石墨化程度,并对铸件自给的实现产生一定影响。因此,有数据介绍。无冒口铸造适用于 QT500 以下的球墨铸铁。此外,由铸件形状和尺寸决定的模量至少应为 3.
值得注意的是,厚度小于 50 毫米的板铸件很难实现无冒口铸造。
还有资料表明,QT500 以上球墨铸铁实现无冒口铸造工艺的条件是其模量应大于 3.