1.气孔 这是金属凝固过程中未逸散的气体形成的小空腔。其内壁光滑,含有气体,对超声波有较高的反射率,但由于其基本呈球形或椭圆形,即为点状缺陷,影响反射波的振幅。钢锭中的气孔在锻造或轧制后被压平成面积缺陷,有利于超声波检测发现。
2.收缩和孔隙率
当铸件或钢锭冷却凝固时,体积会发生收缩,最终凝固的部件会因为无法得到金属液的补充而形成空洞缺陷。大而集中的空洞称为缩孔,小而分散的空洞称为气孔。它们一般位于钢锭或铸件中心的最终凝固部分。内壁粗糙,周围有许多杂质和小孔。由于热胀冷缩的规律,缩孔是不可避免的,但根据加工方法的不同,缩孔的形状、大小和位置也不同。当它们扩展到铸件或钢锭体时,就会成为缺陷。如果钢锭在坯料锻造过程中没有切断缩孔并带入锻造,就会成为残余缩孔(缩孔残留物、残余缩孔管)。
3.夹渣
在冶炼过程中,炉渣或炉体上的耐火材料剥落后进入金属液中,并在浇注过程中卷入铸件或钢锭体中,形成夹渣缺陷。夹渣通常不会单独存在,它们通常密集或分散在不同深度。它们与体积缺陷类似,但通常具有一定程度的线性。4.夹杂物
冶炼过程中的反应产物(如氧化物、硫化物等)--非金属夹杂物,或金属成分中的某些添加剂未完全熔化而残留形成金属夹杂物,如高密度、高熔点成分--钨、钼等。
5.隔离
铸件或钢锭中的偏析主要是指在冶炼过程或金属熔化过程中由于成分分布不均匀而形成的成分偏析。偏析区域的机械性能与整个金属基体的机械性能不同,且差异超过允许标准范围,成为缺陷。
6.铸造裂缝
铸件裂纹主要是由于金属在冷却凝固过程中的收缩应力超过了材料的极限强度所造成的。它与铸件的形状设计和铸造工艺有关,对金属材料中某些杂质含量过高而引起的裂纹也很敏感。性能有关(如硫含量高时的热脆性、磷含量高时的冷脆性等)。).钢锭也会出现轴向晶间裂纹。如果这些裂纹不能在随后的钢坯锻造中被锻出,它们就会留在锻件中,成为锻件的内部裂纹。
7.冷藏室
这是铸件特有的分层缺陷,主要与铸件的铸造工艺设计有关。它是由金属液浇注时的飞溅、翻滚、浇注中断或两股(或来自不同方向的多股)造成的。)金属流相遇等原因,因金属液表面冷却形成的半固态膜残留在铸件本体内而形成的膜片状区域缺陷。
8.翻转皮肤
这是在炼钢过程中将钢锭从钢包浇注到钢锭模的过程。由于浇注的中断和暂停,在空气中浇注的液态金属表面迅速冷却,形成一层氧化膜。继续浇注时,新浇注的液态金属将去除氧化膜。突破钢锭体并转入钢锭体而形成的分层(区域)缺陷,在随后的钢锭方坯锻造中无法通过锻造消除。
9.各向异性
铸件或钢锭在冷却凝固时,从表面到中心的冷却速度不同,因此形成的结晶结构也不同,表现为机械性能的各向异性,这也导致了声学性能的各向异性,即从中心到中心的各向异性。表面具有不同的声速和声衰减。这种各向异性的存在会对铸件超声波检测过程中缺陷的大小和位置产生不利影响。
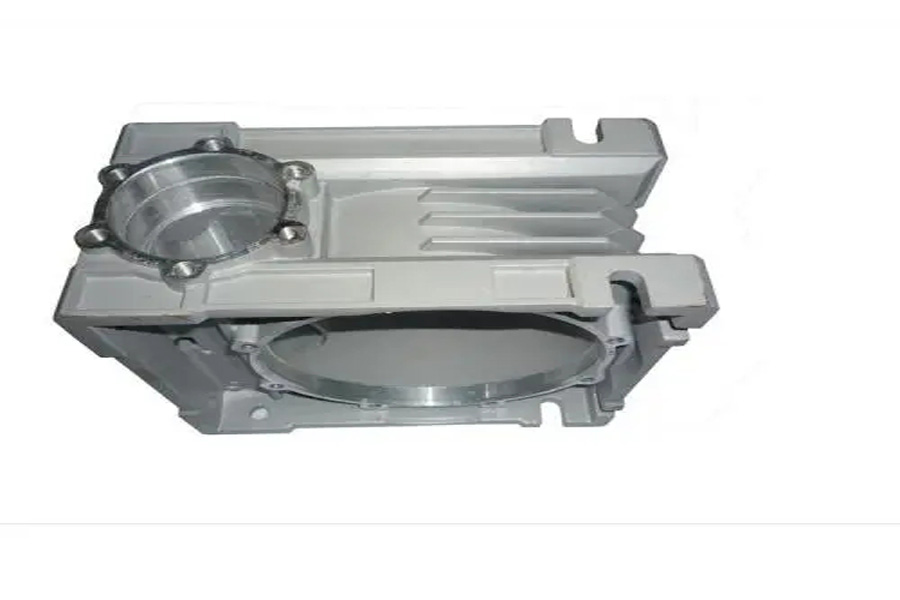
3.改进措施
(1) 熔炼设备对铁水成分的保证能力差,混砂设备稳定性差。铁水成分受焦炭、炉型、风量、原料条件等诸多因素制约;树脂砂受温度、树脂、加酸等因素影响。例如,砂子往往不经过再生冷却床,使砂子温度很高,严重影响砂型强度,造成铸件胀砂严重,铸件缩孔、气孔倾向增大。
(2) 在浇注过程中,型腔中的松散砂粒和铁水的冲击力会直接造成砂眼和夹砂缺陷。
(3) 在熔炼设备中,铁水中总会产生熔渣。在浇注过程中,铁水中的固态和液态熔渣与铁水一起进入型腔,形成渣孔。
(4) 在生产过程中,铁水中的氮含量随温度的升高而增加,随碳当量的增加而减少。当氮和氢在一起时,容易形成气孔,这就是主要的气孔。
(5) 模具底板刚性差,造型前放置时砂模分型面不平整。合模时上下分型面之间的间隙较大,导致分型面的尺寸和形状不佳。
(6) 在浇注过程中,2.2 米阀体底部的砂芯向下漂移,这是造成底部壁厚不均匀的主要原因。
针对阀门铸件缺陷产生的原因,我们主要从以下几个方面采取了改进措施:
(1) 适当提高铁水的碳当量,利用石墨化膨胀增强材料的自给能力。
(2) 在冲洗砂箱时,可确保造型砂的密实度,提高砂模的强度,增强铸件的自给能力。
(3) 合模前吹掉型腔中的松砂,并仔细检查型腔。
(4) 现场浇注后留下未浇注的阀体砂模,其浇口杯和通气孔应盖严,防止散砂进入。
(5) 浇注前清理铁水表面的固渣;提高铁水的初始浇注温度,减少铁水产生二次氧化渣的趋势;尽量将阀门铸件安排在开炉后的初始阶段浇注,减少衬砌次数 使用后产生大量薄渣;对于 610mm (24in) F 阀体,针对横流道重叠,结合浇注过程中的其他参数,在进出口处安装过滤网,并将多片搭接纤维过滤网改进为单片式,以提高浇注系统的挡渣效果。
(6) 尽量使用碳钢、普通灰铸铁或球墨铸铁作为原材料;降低铁水中 Cr、Mn 等合金元素的含量,以减少铁水中的气体含量;下砂芯前要全部涂漆。要限时存放,防止砂芯吸潮;在阴雨天或湿度较大的季节,最好在定芯前用喷灯烘烤型腔和砂芯表面,以减少砂子产生的气体量;采用高温浇注小阀门,以利于铁水自排,减少熔渣的产生。
(7)浇注 1067mm(42in)F 体阀时,要求在固定混砂机前的同一底板上上下捣实,底板上不得有杂物,不允许放在其他地方,以减少变异源:严禁将砂模和底板一起抬起,防止底板变形。
(8) 浇注 2. 2n 时,应在浇注阀体时在底脚砂芯上放入适量树脂砂,并尽快成型。
采取上述改进措施后,全年共生产阀门 2413.78 吨,内部废品率为 1.15%,外部废品率为 1.73%,综合废品率为 2.88%。与改进前后的阀门铸件废品率相比,内部废品率降低了 2.39%,外部废品率降低了 2.85%,综合废品率降低了 5.24%。效果显著。