主要材料管理
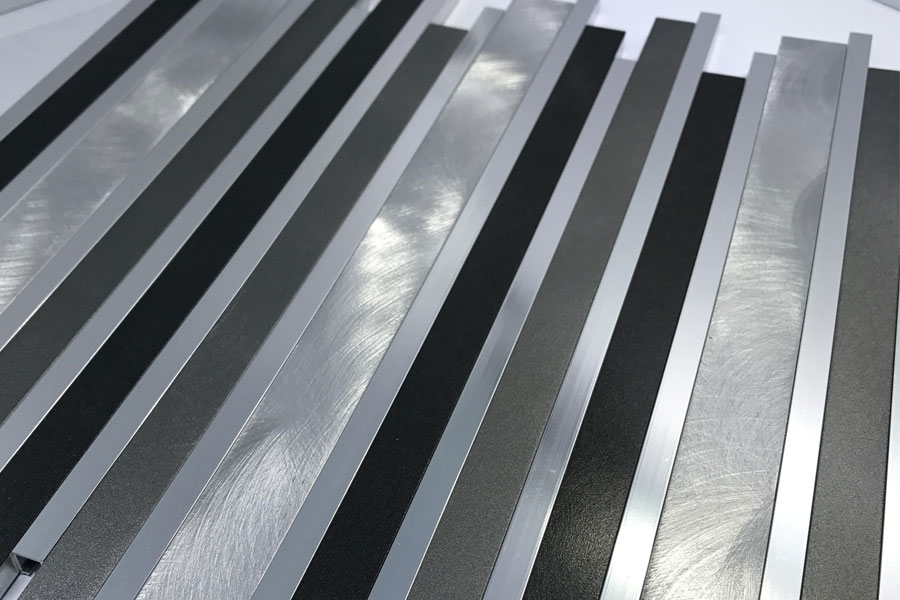
1.铝合金锭的入口控制
由于铝合金的含气量和硬点要求,铝锭生产厂必须做好精炼、脱气和除渣工作,防止铝锭中的高含气量和多种杂质等缺陷遗留到压铸铝液中。铝合金锭进厂后,首先要进行外观检查。要求铝锭表面光滑、无粗糙、无油污、霉斑、氧化鳞,铝合金锭的断口结构细密。不应有严重的偏析、缩孔和缩松现象。熔渣和夹杂物。对每批产品的成分和热号进行抽检,确保使用的合金成分合格。在生产有特殊要求的产品时,需要增加其他检测项目。例如,在生产有机械性能要求的产品时,铝合金锭交付生产时,要求每炉提交一根拉伸试棒;在生产有气密性要求的产品时,必须增加铝合金锭的针孔度。检测
实际生产中使用的铝合金种类往往不局限于一种牌号,而且每种牌号的铝合金对化学成分的要求也大不相同。一个牌号合金中的主要元素在另一个牌号的合金中。可将其视为杂质。对于多牌号共存的情况,有必要在视觉上明确区分各牌号的合金,以防止在使用过程中发生混合。一般的措施是对不同品牌、不同厂家的铝合金外观颜色进行明确统一的规定,不同材料到厂后存放在不同的区域。
2.铝合金熔化过程控制
生产实践表明,提高合金熔体质量是提高压铸件质量的关键因素。因此,要严把原材料管理关,不让不合格的原材料进入车间或投入生产。严格按照合金熔炼工艺要求的标准进行操作,加强对各种原材料(新材料、回收材料、辅助材料)的管理。
铝合金熔炼工艺必须对熔炼温度、熔炼时间、回炉料比例等有明确规定,特别是回炉料要严格分类管理,不得混用。复烧材料应清洁,无油、无锈、无淤泥、无水分、无插入物。再生料中的油性杂质可由铝锭生产厂家重新熔炼,不能直接投入熔炼炉使用;对于散落的铝块,必须进行筛分,除去里面的灰尘、沙子等杂物。使用:铝熔液用于再加热时,精炼剂和除渣剂的比例要大于仅用于熔炼铝合金锭时的比例。在相对湿度较高的天气生产时,再生料的比例不宜超过 30%,在干燥天气可适当增加再生料的比例,但不宜超过 40%。
应及时对熔炼后的铝液进行排渣和脱气,并按要求记录相应参数。在集中熔炼过程中,应检测每锅铝液的化学成分,确保熔炼过程中产品化学成分合格。此外,应避免长期熔炼,否则铝合金液中的氢含量会增加,从而影响压铸产品的强度和气密性。一般情况下,从熔化到压铸不超过 4h。
辅助材料管理
1.控制释放剂
使用脱模剂可使金属液充填顺畅,便于成形,防止粘模,使铸件获得光亮、光滑、平整的表面质量,对生产节奏、铸件表面和内部质量有很大影响。同时,它还能保护模具,避免高温金属液对模具表面的侵蚀,降低模具的导热系数和模具温度,延长模具的使用寿命。开模时,有利于铸件顺利顶出,对减少冲头、顶杆、活动部件的摩擦和磨损也有重要作用。脱模剂的控制不仅包括脱模剂本身的选择和配比,还包括操作人员对脱模剂喷洒和吹干的管理。一般来说,脱模剂的选择有以下要求。
目前,脱模剂的喷涂主要是人工操作,合理的喷涂操作是保证铸件质量、压铸模具寿命和生产效率的重要因素。脱模剂的喷涂时间也会随着不同类型脱模剂的脱模性能、稀释比例、不同的压铸件形状和不同的模具温度而发生变化。脱模剂从喷枪喷射到模具表面,凝结成一层保护膜。这需要很长时间。当这道工序没有完成时,就进行浇注操作,这往往是铸件疏松缺陷的根本原因。根据压铸工艺的规定,不同类型的脱模剂和不同的稀释比例应采用合理的喷涂时间范围。压铸工人必须了解工艺参数上下限的含义和调整影响趋势,并根据生产的压铸件表面状况进行适当调整。
使用水基脱模剂时,必须严格控制脱模剂的比例。如果脱模剂与水的比例过浓,会在模具表面形成较厚的膜,脱模剂会慢慢在模具表面堆积。脱模剂中的水分不能完全排出,会产生气体,使压铸件内部致密性变差。如果脱模剂与水的比例太稀,则达不到效果,压铸件会出现拉伤和粘模现象。
因此,在压铸车间的质量控制中,脱模剂的管理对压铸件的质量影响较大。必须加强这方面的管理,如指定专人负责脱模剂的配比,明确规定各类不同的脱模剂和水在压铸产品生产过程中的配比,根据脱模剂配制工艺进行确定和量化。喷涂时,操作人员要对喷涂动作进行严格培训,动作必须按照要求和规范进行,不允许多喷、少喷、漏喷。
2.冲压油管理
目前,大多使用油基冲头润滑油或颗粒润滑,无论哪种形式的冲头润滑,铝液进入机筒后,必须在短时间内充分燃烧,残渣必须分布在合金液的上层,这样冲头油对产品的影响才不会太大。否则,燃烧产生的气体和燃烧后的残渣会进入产品,结果可想而知。
验证冲油的简单方法是观察模具上料柄的颜色。一般情况下,料柄的厚度为冲头直径的 1/3 至 1/4 ,冲头油变黑的长度不应超过料柄厚度的 3。/5;同时,料柄末端不能有明显的发黑现象(即石墨粉残留过多)。否则,产品加工后,气孔等缺陷将不可避免地增加。
在生产过程中,我们还应随时注意冲头润滑装置的工作状态。如果润滑剂喷洒过多或过少,都会对压力室和冲头的寿命以及压铸件的质量产生不良影响。在调整润滑剂用量时,必须同时考虑冲头的润滑性和模具的脱模性。特别是在使用颗粒润滑剂时,无论压铸模中的蜡丸如何使用,都会存在有机物挥发的问题。如果大量挥发的有机物不能很好地排出,就会对压铸件气孔的产生产生很大的影响。
3.打孔管理
冲头和压力室构成一个相互依存的系统。正常情况下,压力室的寿命可达 2 至 3 年,而冲头的寿命短的一个班次,长的可达 1 万次以上。寿命的差异会造成产品质量的波动和生产成本的显著变化。因此,良好的冲头管理不仅能稳定压铸件的质量,还能大大降低压铸件的生产成本。
4.坩埚管理
坩埚的使用对铝合金压铸非常重要,尤其是铸铁坩埚的使用。如果坩埚不能严格按照坩埚规格操作,后续生产过程中铝合金成分中的铁含量就可能超标。根据我们的经验,如果铸铁坩埚能够严格按照新锅的使用要求刷上坩埚漆,并在使用过程中每隔 3 天刷一次,基本上在整个压铸生产过程中铁含量的增加不会超过 0. 2%(这是公司多年来的统计数据,不同公司之间可能会有一些差异)。在控制铝合金锭进厂检验的前提下,完全可以保证生产出的压铸件合金成分符合标准要求。在石墨坩埚的使用过程中,虽然不存在增铁的问题,但也应引起重视。必须严格执行石墨坩埚首次使用的干燥工艺。这些操作都会影响石墨坩埚日后的使用寿命,没有做好预热工作。石墨坩埚的使用寿命将受到很大影响。每个石墨坩埚的价格较高,会影响压铸件的生产成本。
Conclusion
在质量管理的五大要素中,以上主要讨论了 "物 "和 "人 "的问题。在管理好原材料和辅助材料的同时,要做好人员的培训和管理,压铸工人的技术水平也需要进一步提高。为了有效解决压铸生产中的质量问题,将全面质量管理的思想运用到压铸车间的质量控制中,用系统的压铸生产理论知识指导生产,必将把压铸车间的质量控制能力提高到一个新的高度。