第一个因素,产品的合理设计是影响模具成本的最大因素。
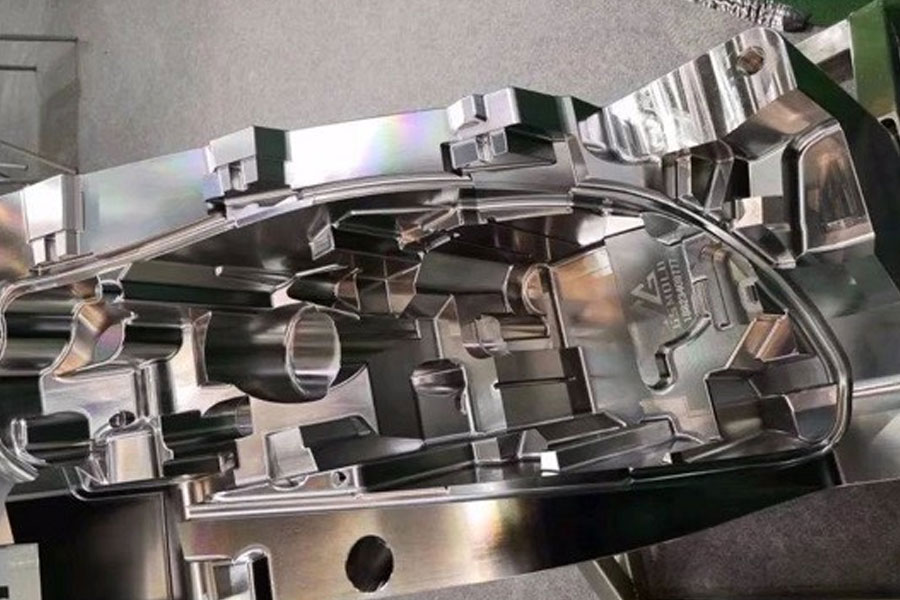
我相信在场很多人都不会同意我的观点。产品设计合理与否,怎么会是影响模具成本的最大因素呢。我们来看一看。第一脚把球踢给了我们的汽车厂。但仔细想一想。如果产品设计不合理,对模具公司来说将是一场灾难。我从事模具工作 40 多年。我经历过很多这样的事情。有时,为了在产品上实现暗切,产品工程师和模具设计师沟通不畅,模具的成本就会成倍增加。
我有幸参与了上海一家汽车公司适合残疾人使用的汽车内饰件的设计工作。其中一个部件叫中央隔板。根据最初的设计,这个零件非常大,模具的生产成本约为 400 万元。配套的注塑机在 4000 吨以上。后来我建议把它分成两块。两套模具的总生产成本不超过 200 万。配套的注塑机都是 1500 吨的型号。最后,皆大欢喜。这样的例子太多了。因此,产品设计师应尽可能多地学习有关模具的知识,使设计出的产品尽可能适合模具工程的进度,而不要不合理地增加模具的难度和成本。在满足整车装配要求的前提下,与模具部门保持良好的沟通是降低模具成本最有效、最直接的措施。还有一个生产效率和生产关系的哲学问题。有些产品工程师认为,模具成本是你模具公司的事,与我无关。但是,如果生产关系重组了,注塑公司和模具公司是一回事呢?其实,这也是社会大趋势。现在经营得比较好的公司就是注塑公司和模具公司的结合体。单靠做模具的企业很难生存。因此,不合理的产品设计会直接增加模具成本。
影响模具成本的第二个因素是产品的设计变更。
模具公司经常会遇到这种情况。在某个项目中,模具刚设计好,模座刚订购,客户的设计变更通知就来了。如果是不影响模具整体结构的小改动,那还无所谓,有时情况会比较严重,因为产品的形状发生了变化,模具必须加装机构,甚至连模座都要重新订购。这就大大增加了成本。因此,应尽量减少设计变更。现在有很多快速成型方法。在制作模具之前,先制作三维原型,组装整车,及时修正产品的三维,可以最大限度地减少产品设计更改带来的成本增加。记得我曾经参与过北京吉普切诺基 213 的研发工作。在深圳注塑的样车要到北京试装,在飞机上来回跑了几十个来回。很难说这个费用是算材料费还是加工费。
影响模具成本的第三个因素是模具设计是否完美。
这里要分析两种情况。首先是模具设计的合理性和可加工性。
在一般的模具公司,设计团队中既要有经验丰富的老设计师,也要有刚从学校毕业的年轻工程师。我们不能要求年轻工程师刚来公司就独立设计高水平的模具。经验丰富的模具工程师,如果闭门造车,模具结构未必完美,肯定会有一些考虑不周的细节。其中最重要、最有效的方法就是集体评审。记得上世纪 70 年代,我买过一本德国的模具书。书名叫《高级模具结构 80 例》。对我影响最大的是书中提到的模具制作过程,必须在模具结构上重复多次。集体评议。这对我的模具生涯影响最大,确实受益匪浅。在这个问题上,我相信大家都有共识。有很多模拟方法,例如模流分析、模具结构动态分析、测试产品与设计产品的三维对比分析等。这些方法可以最大限度地减少因模具设计不合理而造成的成本增加。
第二种情况是设计浪费。如果模具用户明确只需要生产 500 个样品,就可以用来开拓市场,但如果我们设计的模具寿命是 30 万个模具,成本就会很大,也是一种设计浪费。
模具成本控制的第四个要素是尽量减少试模次数。
许多模具公司根据模具订购后的天数来计算模具加工费,模具合格后的天数为加工费。如果模具经多次试模仍不能交付使用,除按合同规定罚款外,模具在工厂停留的天数越多,加工费也就越多。当然,试模费用也是非常可观的。因此,多次试模或试模不可控是模具成本控制的一大盲点。
让我们来分析一下霉菌审判数量居高不下的原因。
首先是模具设计没有经过充分的集体评审,模具结构不合理,使得模具在试验后需要多次改进,使得模具成本超出预算。如果经过多次改进就能完成,那么还好,不满意的情况也很多,即使模具要报废重做,这个成本也是无法控制的。有些时候,模具设计很好,但模具加工不到位,使得试模次数无端增加,直接增加了模具成本。对这个问题没有异议,所以很多模具企业都加大了对测量设备的投入。
二是试模时没有选择最佳的成型工艺和注塑机型号。模具做得很好,但注塑出来的产品并不理想。无故增加试模次数,直接增加了模具成本。这是一些小型模具厂的通病。
第三是对塑料的物理性质还不完全了解,甚至连收缩率也不准确。这种情况时有发生。因此,有必要在设计模具前了解塑料的物理性质,以有效减少试模次数。
影响模具成本的第五个因素是购买模具材料和标准件。
选择稳定、信誉好的供应商。如果因为贪图便宜而仓促采购,导致模具破损,那将是非常可惜的。事实上,这样的案例比比皆是。虽然可以追究供应商的责任,但损失最大的还是模具公司和模具用户。