インベストメント鋳造品の寸法精度を継続的に向上させ、オーバーサイズによる廃棄物を削減することは、常に国内外のインベストメント鋳造従事者が追求する主要目標の一つである。
1.インベストメント鋳物の寸法安定性
1.ワックスモデルの寸法安定性とその影響因子
多くの場合、鋳物の大きさが変動するとワックスモールドの大きさも大きく変動しますが、例外もあります。全体として、ワックスモールドの大きさの変動は、鋳物の大きさの変動の10%から70%を占めています。
成形工程のパラメータは、ワックス鋳型の寸法安定性に決定的な影響を与える。主な要因は以下の通りである:
(1) ワックスプレス温度
成形材料によって、ワックスプレス温度の影響による性能の違いがある。ワックス系成形材料を使用する場合、ワックスプレス温度はワックス金型寸法安定性の影響に非常に敏感であるが、樹脂系成形材料は影響が少ない。
(2) 射出圧力
圧力が小さい場合、圧力が上がるとワックスモールドの収縮率は大きく減少する。しかし、圧力がある程度(≥1.6MPa)高くなると、圧力はワックスモールドの大きさにほとんど影響しなくなる。海外の試験結果では「圧力はワックスモールドの大きさに関係ない」と結論づけられることが多いのは当然ですが、多くの国内企業の印象は全く同じではありません。
(3) 流量
金型材料の流量は次の2つの方法で変えることができるが、ワックス金型のサイズに与える影響は同じではない:
-ワックスプレスの流速設定を変えることで、ワックスモールドの収縮にほとんど影響を与えない。しかし、複雑な形状の薄肉部品や中子入りワックス型の充填性や表面品質に重要な影響を与えます。
-ワックス射出口の断面積を大きくすることで、ワックスのプレス温度を下げることができるだけでなく、ワックス射出口での鋳型材料の凝固時間を長くすることができ、それによってワックス鋳型の圧縮収縮の度合いと表面収縮を減らすことができるからです。
(4) 注入時間
ここでいう射出時間とは、充填、成形、保持の3つの時間を含む。充填時間とは、成形材料が成形キャビティに充填されるまでの時間を指し、成形時間とは、成形材料が充填されてからワックス射出ノズルが閉じるまでの時間を指し、保持時間とは、ワックス射出ノズルが閉じてから金型が射出されるまでの時間を指す。
射出時間はワックスモールドの収縮率に大きな影響を与える。これは、射出時間を長くすることによって、より多くの金型材料がキャビティに絞り込まれ、ワックス型がより圧縮されるため、収縮率が低下する可能性があるからである。ワックス模型の重量は、成形時間が長くなるほど増加する。成形時間は適切でなければならない。成形時間が長すぎると、ワックス注入口の金型材料が完全に固化してしまい、成形がうまくいかなくなる。また、図4から分かるように、射出時間が短い場合(15~25秒)、ワックス押し付け温度が上昇し、収縮率が高くなるが、射出時間を25~35秒に延ばすと(充填時間が一定であることを前提に、実際は成形時間を延ばす)、ワックス押し付け温度の影響が小さくなる。射出時間が35秒以上になると、逆の状況、つまりワックス押し付け温度が上昇すると、代わりにワックス金型の収縮率が低下する。この現象は、金型材料温度を上げ、成形時間を長くすることは、ワックス金型の成形度を上げることと同じ効果があると説明できる。
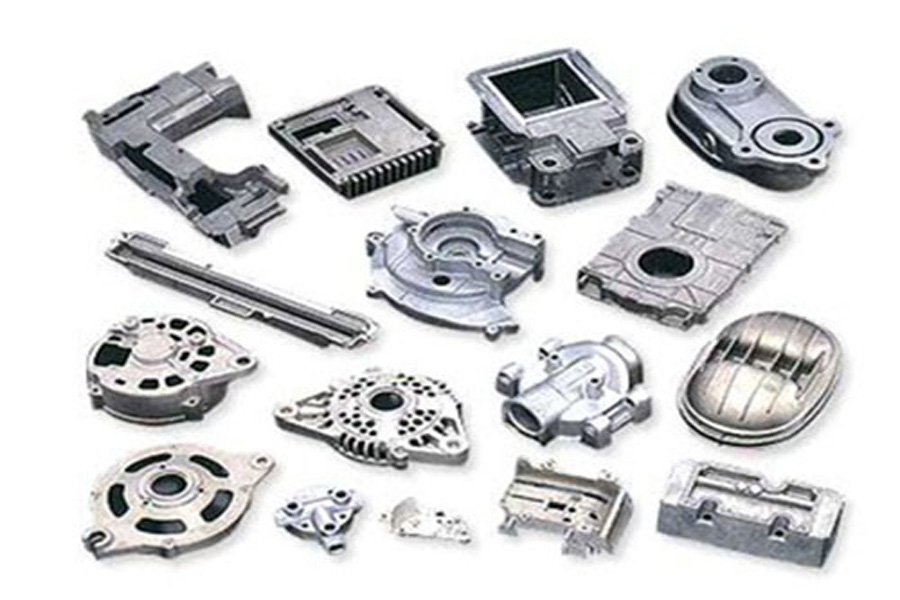
(5) 成形温度とワックスプレス装置
成形温度が高く、ワックスモールドの冷却が遅く、収縮率が高くなる。これは、ワックス型が離型する前はまだ圧縮成形中であり、収縮が制限されているが、離型後は自由に収縮するようになるためである。したがって、離型時にワックス型の温度が高ければ、最終的な収縮率は大きくなり、その逆であれば収縮率は小さくなる。
同様に、ワックスプレスの冷却システムは、ワックスモールドのサイズに約0.
最後に、ワックスベースの金型材料を使用する場合、ワックスペーストは固体、液体、気体の三相共存系であることを強調する価値がある。この三相の体積比がワックス鋳型の大きさに大きな影響を与える。この三者の比例関係は実際の生産ではコントロールできず、これがワックス系成形材料を使用したワックス鋳型の寸法安定性が悪い重要な理由でもある。
2.鋳造品の寸法安定性に及ぼすシェル材料とシェル製造プロセスの影響
鋳型シェルが鋳物のサイズに与える影響は、主に焼成時の鋳型シェルの熱膨張と熱変形(高温クリープ)、および鋳物の冷却収縮に対する鋳型シェルの制限(閉塞)に起因する。
(1) シェルの熱膨張
主にシェル材質による。耐火物によって膨張率は異なる。一般的に使用される耐火物の中で、溶融シリカの膨張率は最も小さく、次いでケイ酸アルミニウム、シリカは最も大きく、不均一である。試験の結果、ケイ酸アルミニウムのシェルは室温から1000℃まで加熱した場合、約0.25%の膨張を生じ、鋳物サイズの全体的な収縮に占める割合は小さいことが判明した。従って、このような耐火物を使用すれば、溶融シリカのような寸法安定性に優れたシェルが得られる。しかし、シリカを使用した場合、シェルのサイズは大きく変動する。
(2) 熱変形(高温クリープ)
例えば、水ガラスをバインダーとするシェルは、シリカゾルやエチルシリケートシェルに比べ、1000℃以上の高温でのクリープ度が著しく大きい。また、溶融コランダム自体は高屈折率であるが、酸化ナトリウムなどの不純物が存在するため、シェルの焼成温度が1000℃を超えるとクリープが発生し、寸法安定性が悪くなることがある。
(3)鋳物の収縮に対する鋳型シェルの拘束-鋳型シェルの後退と崩壊性 これも主に鋳型シェルの材料に依存する。
要約すると、シェルが鋳物のサイズ変動に与える影響には耐火物が大きな役割を果たすが、バインダーの役割も無視できない。一方、シェルの製造工程による影響は小さい。
3.鋳物の不均一冷却による応力が寸法安定性に及ぼす影響
鋳物の各部分(ゲートシステムを含む)の冷却速度が異なるため、熱応力が発生して鋳物が変形し、寸法安定性に影響します。これは、実際の生産でしばしば遭遇することです。鋳物の冷却速度を下げたり、湯道の組み合わせを改善したりすることが効果的な予防策となります。
2.精度向上の鍵-成形収縮率を正しく割り当てる
上記の「寸法安定性」は、「寸法精度」や「精度(正確さ)」とは異なる。寸法安定性(精度)とは、寸法のばらつきやばらつきの程度を表す寸法安定性と同義であり、通常は標準偏差σで測定される。寸法が不安定になる主な原因は、工程管理の甘さであり、これはランダムエラーである。精度とは、多くの測定値の算術平均が、鋳物上のあるサイズについて公称サイズからどの程度ずれているか、つまり平均偏差の大きさを指す。インベストメント鋳造の場合、寸法精度が悪い主な原因は、プロファイリング設計時の収縮率の不適切な割り当てであり、これは系統的な誤差であるため、通常は鋳型の修復を繰り返して調整する。寸法精度(精度)は上記2つの組み合わせである。従って、鋳物の寸法精度を向上させ、製品の寸法公差の問題を解決するためには、工程を厳密に管理して寸法の変動を抑えるだけでなく、プロファイル設計時に鋳物の各寸法の収縮率を正しく割り当てる必要があります。
精密鋳造品の最終的な総収縮率は、ワックスモールド、合金の収縮、および少量のシェルの膨張の組み合わせであることはよく知られている。シェルは約0.25%膨張し、その影響は限定的である。合金の線収縮率はワックスモールドの線収縮率より大きいことが多いが、ワックスプレス工程による寸法変動の方が影響が大きい。金型補修のコストを抑え、鋳造寸法の変動を小さくするためには、ワックス金型の収縮率をコントロールすることが非常に重要である。
1.ワックス型の収縮
ワックスモールドの収縮率は、ワックスモールドのサイズが完全に安定してから測定する必要があります。ワックス鋳型の収縮は鋳型が排出された後も完全に止まらないからだ。ワックス鋳型の収縮は鋳型を排出した後、数日しか経たずに安定することもある。しかし、基本的に鋳型の収縮は鋳型が排出されてから1時間から数時間で完了する。ワックス鋳型の収縮率には主に次のような要因がある:
(1) 金型材料の種類;
(2) ワックスモデルの断面サイズ;
ワックス鋳型の断面サイズは収縮率に大きな影響を与えることを強調しておく価値がある。例えば、一般的な未充填の型材で、厚みの異なるワックス型をプレスした場合の収縮率である。ワックス型の断面の厚さは一般的に13mmを超えないことが望ましい。厚さが13mmを超える場合、収縮率を下げるという目的を達成するために、コールドワックスブロックやメタルコアを使用して肉厚を減らすことができ、これは非充填鋳型材料にとって特に重要である。
注:1.水溶性金型材料の収縮率は約0.25%である;
2.ソリュブルコア、セラミックコア、石英ガラス管を使用する場合、コアに接するワックスモールドの線収縮はありません;
(3) コア・タイプ
ワックス鋳型のキャビティサイズは、間違いなく中子の形状と一致する。したがって、中子を使用することは、ワックス鋳型のキャビティの寸法精度を向上させる方法となっている。
2.合金の収縮
合金の収縮は主に以下の要因に依存する:
- 鋳造合金の種類と化学組成;
- 鋳造形状(拘束状態と断面サイズを含む);
- 注湯温度、シェル温度、鋳造冷却速度などの鋳造パラメータ;
- セラミックコア、石英ガラス管などの使用
注湯温度、シェル温度、鋳造冷却速度などのプロセスパラメータは、一般的に、生産工程中の標準プロセスカードによって厳密に制御されているため、これに起因するサイズの変動は、異なる生産バッチ間で大きくはありません。注湯温度がプロセス仕様で要求される範囲を超えても、鋳造サイズの変動は通常大きくない。ワックス鋳型と同様に、鋳物の断面寸法と鋳型シェルの制約が合金の収縮に影響を与える主な要因である。経験上、完全拘束サイズの収縮率は自由収縮率の85%~89%、半拘束サイズは94%~95%である。
3.測定のための最初のバッチサンプルの最小数
上記の収縮率は過去の経験に基づく経験値であり、実際の収縮率ではありません。これらのデータに従って金型を設計・製造すれば、補修は避けられない。補修の精度と成功率を高め、補修回数を減らすためには、十分な数の試作鋳造サンプルのサイズを入念にチェックすることが重要なつながりとなります。なぜなら、製造する鋳物の大きさは全く同じにはできないので、測定サンプルの数が十分に多くて初めて、得られる平均値が真の算術平均に近づくことができるからです。このことから、測定サンプルの最小数が、製品サイズの一貫性を管理する生産工程の工程能力(Process Capability)に直接関係していることを理解するのは難しいことではありません。鋳物のサイズが完全に同じであれば、試験するサンプルは1つだけでよい。逆に、鋳物のサイズが大きく変動する場合、
より正確な収縮データを得るためには、多くのサンプルを測定する必要がある。前述したように、サイズを制御する生産工程の能力は、この工程で生産される鋳物サイズの6σで表すことができます。ほとんどのインベストメント鋳造工場の現在の技術水準からすると、Hpは0.5を超えることがほとんどであるため、最初の測定サンプルバッチには一般的に少なくとも11個のサンプルが必要である。
の3つです。測定システム分析
製品サイズの問題を分析・解決する際には、使用する測定システムの精度と信頼性に注意を払わなければなりません。測定機器や装置自体の校正を頻繁に行うことはもちろんですが、測定誤差を最小限に抑えることも重要です。測定システム(作業者、操作方法を含む)の誤差が大きいと、不合格品が良品と判定されるだけでなく、多くの良品が不合格品と誤判定される可能性があり、いずれも大きな事故や不要な経済的損失を招く恐れがあります。測定システムが特定の測定タスクに適しているかどうかを判断する最も簡単な方法は、再現性と繰返し性の適格性試験を実施することである。いわゆる再現性とは、同じ検査員が同じ機器(または装置)と方法で同じ部品を検査し、その結果の一貫性を得ることを意味します。再現性とは、異なる作業者が異なる機器を用いて同じ部品を検査し、得られた結果の一貫性を意味する。アメリカの自動車産業行動グループ(Automotive Industry Action Group)は、測定された鋳物サイズの変動の標準偏差における再現性と再現性の積分標準偏差RandRの割合が30%以下であることを、測定システムが要件を満たすための基準として規定しています[5]。一部の大型で複雑な形状の鋳物の測定では、すべての測定システムがこの要件を満たせるわけではありません。鋳型を測定する際の許容測定誤差はより小さくする必要があり、通常は1/3である。鋳型の構造と加工レベル
金型の構造や加工品質がワックス金型の寸法や形状に重要な影響を与えることはよく知られている。例えば、位置決めとクランプ機構が正確で信頼できるかどうか、可動部品(可動ブロック、ボルトなど)のマッチングクリアランスが適切かどうか、鋳造品の寸法精度を確保するために絞り方法が有益かどうかなどである。言うまでもなく、国内の相当数のインベストメント鋳造工場にとって、金型設計と製造のレベルはまだ緊急に改善する必要がある。
最後に
上記の分析から、インベストメント鋳造品の寸法精度を向上させることは、インベストメント鋳造製造工程のあらゆる側面を含む体系的なプロジェクトであることを理解するのは難しいことではありません。主なポイントをまとめると以下のようになる:
1) 成形工程のパラメータ、特に鋳物のサイズに大きな影響を与えるパラメータを厳密に制御する。
2) 適切なシェル素材を選ぶ。
3) 縮小率の割り当て精度を向上させるため、統計的原則に則った正しい方法で、縮 小率に関するデータを収集、集計、分析する。
4) 測定システム(装置、検査員、技術を含む)を頻繁に監視し、繰り返し性と再現性の誤差が指定された要件を満たしていることを確認する。
5) 金型設計と製造のレベルを継続的に向上させる。
6) 鋳造矯正や安定化熱処理などの対策は、今でも多くの場面で不可欠である。