ブレーキドラムは保安部品であり、人命と財産の安全に関わると同時に、傷つきやすい消耗部品でもある。特に市場の需要は大きい。
現在、国内の年間生産量は約1,000万個以上である。製品構造が比較的単純なため、機械による造形や手作業による造形が容易で、ブレーキドラムを生産している鋳物工場がほぼ全国各地にある。私が訪問したいくつかの大企業は、機械化された組立ラインでブレーキドラムを生産しており、年間生産量は約100万個である。
また、年間生産高が数万の小さな会社にも行ったことがある。また、河北省龍窯県のある町には工業団地があり、そこでは百数十社の鋳物工場が自動車用ブレーキドラムを集中的に生産している。ただ、大企業が生産するブレーキドラムは国内のアクスル工場に供給されるか、海外に輸出されるのが一般的で、中小企業が生産するブレーキドラムのほとんどは部品やアフターパーツ市場に供給される。その製品の品質と信頼性は、通常のアクスル工場に受け入れられることは難しい。私が見聞したこれらの企業によると、製品構造や供給先が異なるため、生産工程も異なるが、総じて品質問題 自動車用ブレーキドラムの品質要求を満たせないものがまだ多い。そこで、皆さんとブレーキドラムの生産工程について議論・研究し、お互いの経験を交換する必要があると思います。以下は私の経験と理解に基づいています。もし間違っていたら、訂正してください。
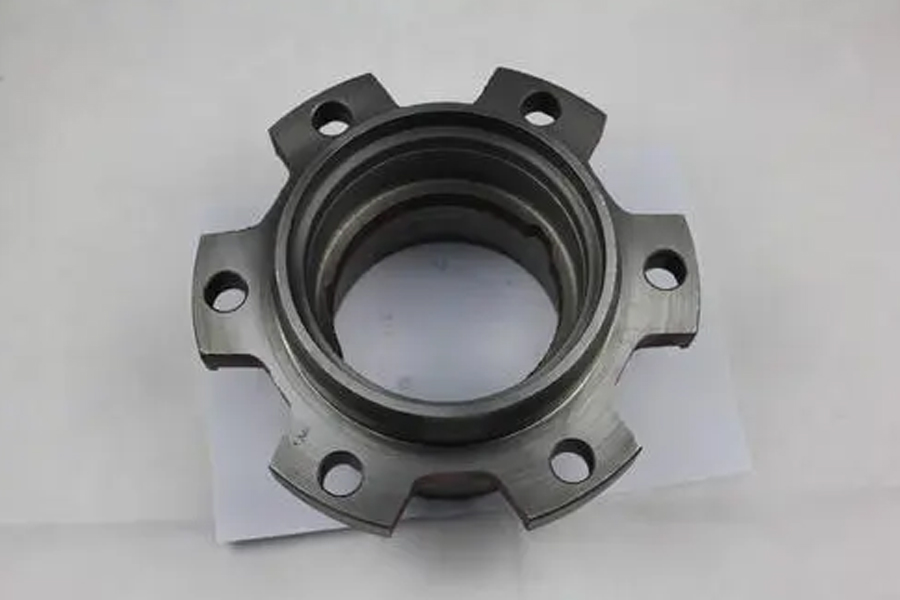
トラック用ブレーキドラムの品質要件
ねずみ鋳鉄は熱伝導性、衝撃吸収性、耐摩耗性に優れ、鋳造性能に優れ、製造コストが低いため、自動車のブレーキドラムはほとんどねずみ鋳鉄製で、等級はHT200とHT250である。
私の国のねずみ鋳鉄の規格はJB/T9439-2010しかなく、自動車のブレーキドラム用の特別なねずみ鋳鉄の規格はありません。機械規格にも特殊ねずみ鋳鉄の記述はありません。世界では、米国材料試験協会ASTMA159-83(1993年再調査)だけが自動車用ねずみ鋳鉄部品の特別規格を制定しています。ブレーキドラムには、耐荷重によって3つの鋳鉄等級が定められています。同時に、アメリカ自動車技術者協会の動力機械用ねずみ鋳鉄規格SAEJ431のブレーキドラムの品質要求は、基本的にASTMA159-83と同じです。現在、わが国と外国はほとんどアメリカのブレーキドラム規格を参考にしています。工場規格は図面または受入規格に記載されています。規格のレベルは、職人の技量と品質のレベルを反映します。高水準の規格のみが高品質の製品を生産することができるのです。
以下では、上記の米国規格と、海外の優良企業のブレーキドラムに関する品質要求事項を簡単に紹介し、参考として以下を紹介する。
機械的性質
化学組成
Microstructure
その他の要件
機械的特性、硬度、金属組織の許容に加えて、海外メーカーや国内OEMは、提供するブレーキドラムの技術的条件において、しばしばコンパクト性の要件を提示する。
鋳物に引け巣、引け巣孔、気孔、砂の混入、その他の鋳造欠陥があれば、それは緻密ではない。これらの欠陥はX線検査や解剖学的方法で確認することができる。欠陥が下表の規定以下であれば合格とする。規定を超えるものはスクラップと判断する。勿論、機械加工中に欠陥が露出した場合は、基本的に受入れられない。
ブレーキドラムの故障モードと原因
使用中のブレーキドラムの故障は主に亀裂と摩耗であるが、顧客からの苦情やクレームに反映されるデータ統計から見ると、主に前者である。つまり、故障したブレーキドラムのほとんどは、通常の摩耗、あるいはわずかな摩耗で、つまり割れてしまって使用できなくなっているのである。以下は、2014年にある工場から返却されたスクラップである。写真から、ブレーキドラムに1本から数本の縦クラックが発生していることがよくわかる。横クラックは、一般にトップドロップと呼ばれるフランジの丸みを帯びた角に多く発生している。
故障部品の故障分析から、故障の原因は主に3つあると結論づけられた:
最初の2つの故障原因は、ブレーキドラムを製造する私たちが改善すべきものです。ブレーキドラムの品質を安定させ、向上させる。詳しくは後述する。3つ目の故障原因については、私たちは無力で、主に過積載車の違法使用に対する国のガバナンスに頼っている。クレームという観点から見れば、その原因の大部分はそうした違法使用にある。しかし、その責任は一般的に鋳物工場に転嫁される。私の知る限り、ブレーキドラムを製造しているいくつかの会社では、クレーム率は3%程度だと主張している。毎年数百万件の補償がある。本来、このような責任は車のオーナーが負うべきものである。わが国から海外に輸出されるブレーキドラムは、概してよく反映される。補償はおろか、クレームすらほとんどない。乗用車や平野部を輸送される車のブレーキドラムもよく反映される。耐用年数が低いのは、ごく一部の山間部や鉱山地帯、個々の製品だけで、その原因はすべて、国内での深刻な過負荷、頻繁な急ブレーキ、ブレーキ工程でブレーキドラムを冷却するための散水などである。この場合、運動エネルギーはすべてブレーキドラムの熱負荷に変換され、その温度は800℃~850℃に達します。このことは、破損クラックの巨視的および金属組織学的検査からも判明する。このタイプの鋳物は、巨視的には白く明るい。金属組織学的には、黒鉛+マルテンサイト+ベイナイトである。これらはすべて、高温変態後のオーステナイト焼入れによって生じる。従って、ブレーキドラムは従来の割れではなく、曲げ応力、熱応力、機械的制動力に対する抵抗力の作用で破損する。これは中国式の故障モードかもしれない。
1.ブレーキドラムの製造工程
ブレーキドラムの製造工程は、主に2つの側面に焦点を当てている。ひとつは、機械的特性と金属組織をいかに確保し、製品の要求を満たすか。しかし、その鋳造欠陥をいかに減らすか。特に主要部品の内部欠陥です。鋳造欠陥を減らすという点では、今日はその引け巣をいかに減らすかということに焦点を当てたいと思います。
第一の側面は、主に溶鉄の冶金的品質を向上させることである。第二の側面は、メーカーに適した技術的手段を見出すことである。
現在、国産トラック用ブレーキドラムの材料はすべてHT250であるため、ブレーキドラムの製造に使用されるHT250の製錬と工程で注意しなければならないいくつかの問題に焦点を当てる。
本来、HT250の機械的性質と金属組織の要求を満たすだけであれば、何の問題もない。しかし、ブレーキドラムに使用されるHT250は、高炭素含有下での機械的特性、硬度、金属組織を確保する必要があり、一部の小規模メーカー、さらには一部の大手メーカーにとっては困難が伴う。Cr、Cu、Snなどの合金元素を添加せず、炭素含有率を3.40%以上にする場合、その性能を保証するのは難しいという。しかし、彼らの現実はコスト削減であり、一般的にはパーライトと引張強度を確保するためにCrとSnを添加するのみである。しかし、添加量が少ないと強度と硬度に達しないし、添加量が多いと金属組織中にセメンタイトが過剰に発生する。
とジレンマに陥っている。最終的に、長所と短所を測定するために、ほとんどの工場は機械的特性と硬度の要件を満たすために炭素含有量を減らす方法を採用している。もちろん、これまでのところ、ASTM規格は炭素含有量について厳しい規制を設けているが、中国の工場はそれを実施していない。海外の顧客でさえ、炭素含有率を3.4%以上にするよう一律に要求していないところもある。例えば、私が知っているいくつかの顧客は、ブレーキドラムの化学組成に対する要求は以下の通りである:
なぜなら、炭素含有率が高ければ高いほど、多量の黒鉛が保証され、熱伝導率と耐熱疲労性が向上するからである。米国の義務的規制には科学的根拠がなければならない。我々にとっても、高炭素含有を前提に、適格な機械的特性、硬度、金属組織を生み出す能力を持つ必要がある。
長年にわたる国内での高炭素高強度鋳鉄生産の実践を通じて、多くの成功体験が蓄積され、技術的なコンセンサスが得られたと言うべきでしょう。これがブレーキドラムの生産に良い基礎を築いたと言えるが、実際の状況もその通りである。多くの大企業が生産するブレーキドラムの品質は、顧客の要求に安定して応えることができている。これらの技術をまとめると、人造鋳鉄の道を歩んでいることになる。採用されている技術は、スクラップ鋼の添加比率を高くし、再炭化装置を使用して再炭化を促進し、溶鉄中の硫黄を増加させ、良好なインキュベーションと十分に高温の溶鉄を使用することです。最近、溶鉄の前処理が提案されている。この点については、すでに多くの話をし、多くの論文を発表している。繰り返すつもりはない。ただ、ブレーキドラムの具体的な鋳造を組み合わせ、参考までにいくつかのコメントを述べたいと思います。
2.受胎問題について
ブレーキドラムの液体鉄を接種する目的は、他の高級鋳鉄部品を製造する目的と同じです。主に、セメンタイトが現れないようにするか、フェライトとカーバイドの合計量が5%を超えないようにして、良好な黒鉛形状を確保する必要がある。(一般にA黒鉛は80%以上と規定されている。B、D、E黒鉛は20%を超えてはならない)。良好な機械的特性を確保すると同時に、被削性を向上させるため、ねずみ鋳鉄の製造実務では、その接種量は一般に0.6%.この時点で皆さんに注意していただきたいのは、肥沃度に注意を払い、肥沃度をコントロールしてください、ということです。というのも、ほとんどの現場鋳造技術者や作業者の頭の中には、いかに接種効果を高めるか、いかに黒鉛中子を増やすか、いかに効率的な接種剤を使うかということがあるからです。ねずみ鋳鉄の製造もダクタイル鋳鉄の製造と同じである。複数回の接種を行い、できるだけ多くの接種剤を使用し、接種がねずみ鋳鉄の収縮特性に及ぼす影響を無視している。また、収縮空洞と気孔がブレーキドラムの廃棄物の大きな割合を占め、収縮廃棄物とブレーキドラムの異常故障との間には何の関係もないことを忘れている。
私たちは皆、各工場が生産したブレーキドラムのスクラップのほか、倉庫にある多くの適格な鋳造品に引け巣や引け巣欠陥があり、メーカーの技術者のほとんどが引け巣欠陥を解決するための対策を止めるだけであることを知っている。注湯温度を下げ、注湯システムの設計を改善する。みんなに言いたい。ブレーキドラムのインキュベーションプロセスにもっと注意と管理を払うべきだ。
今では多くの人が、植菌が収縮多孔性を促進することに気づいている。炭素当量が3.3%の範囲では、接種鋳物のサイズは常に不妊鋳物のサイズより大きい。不妊鋳物には引け巣がないが、接種鋳物には引け巣が生じる。従って、ブレーキドラムの製造においては、接種量が大きくなりすぎないように管理する必要がある。セメンタイトが発生しないこと、加工性を確保することを条件に、接種量はできるだけ少なくし、十分であれば過剰にならないようにする。重要なポイントは、フロー接種をうまく行うことである。途中で2回、3回、4回と継代をとらないこと。
3.金型の気密性について
鋳鉄品の内部収縮キャビティとポロシティ、鋳造品の表面収縮は鋳型の影響を大きく受ける。鋳型に溶鉄を注湯した後、溶鉄の静圧と熱でキャビティの容積が鋳型壁を移動し、鋳型の容積が大きくなり、鋳物の大きさが公差外になり、重量が増加します。変形の大きさは、砂型のコンパクトさ、造型材料、砂の性能パラメータに依存する。海外では、この分野の研究をしている人もいる。彼らは金型製造ラインからブレーキドラムを取り出し、そのサイズを測定し、重量を量った。その結果、各サンプルの重量は大きく変動することがわかった。下図に示すように、ブレーキドラムの重量は162ポンドから173ポンドで、最大差は11ポンド(1ポンドは453グラム)。テストドラムの成形ラインはショック圧空成形機です。この重量差は、金型の品質が変動することを示している。サンドインパクトされたソフトモールドは、激しい砂の膨らみを生じた。成形性の良い鋳型では、膨らみはごくわずかで、鋳物の大きさも正確である。膨れの激しいブレーキドラムは内部に収縮があり、正常な重量のブレーキドラムの品質は正常であることがわかった。そこで、この簡易検査法を用いて、機械加工に運ぶ前の計量でブレーキドラムの内部収縮を判定し、ブレーキドラムの収縮は金型の動きに起因すると考えた。したがって、ブレーキドラムの収縮や緩みを避けるためには、金型の剛性を向上させることが重要な対策となる。
現在、中国で進められている砂入り鉄製ブレーキドラムの生産は、その特性から収縮不良がない。山西省にある大規模な企業では、このプロセスを採用してブレーキドラムを生産している。半機械化された鉄型サンドコーティングラインは3ラインあり、430台以上の日産ブレーキドラムを生産している。工程の歩留まり率は90%、製品の認定率は98%と安定している。現在、4番目の鉄型サンドコーティングラインを設置中である。
河南省南陽市の工場では、樹脂砂を使用して、トップインジェクションと立ち上がりなしの技術で、品質が安定し、収縮のないBeiben大型ブレーキドラムを生産している。
工場によってはスプルーとブレーキドラムの距離が40mmと近すぎる。ここの成形砂は砕きにくいので、収縮穴やポロシティがよく発生します。この距離を60-80mmに変更すると、収縮ポロシティはかなり軽くなります。
小さな工場では、まず砂を全体として打ち、次に鉄の棒を使ってスプルを入れることで、鋳型全体をさらにきつく、打ちやすくしているところもあるが、これは鋳物の収縮が深刻でないことを反映している。