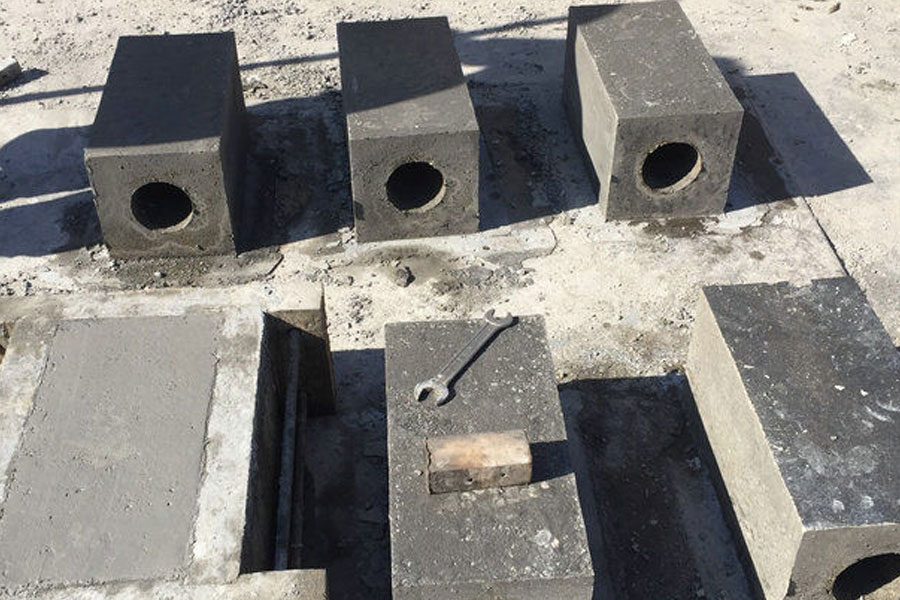
ウォーターグラスの "老化 "に影響する要因は何ですか?ウォーターグラスの "老化 "を防ぐには?
調製したての水ガラスは真性溶液である。しかし、保存中に水ガラス中のケイ酸は縮合重合を起こし、真の溶液から徐々に重縮合して高分子ケイ酸溶液となり、最終的にはケイ酸ゲルとなる。したがって、水ガラスは実際には重合度の異なるポリケイ酸からなる不均一な混合物であり、その弾性率、濃度、温度、電解質含有量、保存時間によって容易に影響を受ける。
水ガラスは、保存中に分子が縮合重合してゲル化し、保存時間の延長とともに結合強度が徐々に低下する。この現象を水ガラスの老化という。
高弾性率水ガラス(M=2.89, ρ=1.44g/cm3)を20, 60, 120, 180, 240日間保存した後、CO2硬化水ガラスをブローした。砂の乾燥引張強さは、9.5%, 36.8%、40%低下した。低弾性率ケイ酸ナトリウム(M=2.44、ρ=1.41g/cm3)は、乾燥後7、30、60、90日間保存。引張強さはそれぞれ4.5%、5%、7.3%、11%低下した。
エステル硬化水ガラス自硬性砂の初期強度には水ガラスの保存時間はほとんど影響しないが、その後の強度には大きな影響を与える。測定によると、高弾性率水ガラスでは約60%、低弾性率水ガラスでは15~20%低下する。残留強度も貯蔵時間の延長とともに低下する。
水ガラスの保存中に、ポリケイ酸の重縮合と解重合が同時に進行し、分子量が不均化し、最終的にモノオルトケイ酸とコロイド粒子が共存する多分散系が形成される。すなわち、水ガラスのエージング過程において、ケイ酸の重合度が不均化し、保存時間の延長とともにモノオルトケイ酸とハイポリケイ酸の含有量が増加する。保存中に水ガラスが縮合重合と解重合反応を起こす結果、接着強度が低下する。
水ガラスの "老化 "に影響する主な因子は、水ガラスの保存時間、弾性率、濃度である。保存時間が長いほど、弾性率が高く、濃度が高いほど、"老化 "が深刻になる。
長年使用されてきた水ガラスに様々な改良を加えることで、"老化 "を解消し、真水ガラスの性能を取り戻すことができる:
1.物理的修正
水ガラスのエージングは、ゆっくりとエネルギーを放出する自然発生的なプロセスである。老化した水ガラスを物理的に改質することは、磁場、超音波、高周波または加熱を利用して水ガラス系にエネルギーを与え、ポリケイ酸糊の高重合を促進することである。粒子が再解重合し、ポリケイ酸の分子量の均一化を促進することで、物理的改質のメカニズムであるエージング現象を解消する。例えば、磁場処理後、珪酸ソーダ砂の強度は20-30%増加し、珪酸ソーダの添加量は30-40%減少し、CO2が節約され、崩壊性が改善され、良好な経済効果がある。
物理改質の欠点は耐久性がなく、処理後保存すると接着強度が低下するので、鋳造工場で処理後できるだけ早く使用するのに適している。特にM>2.6の水ガラスは珪酸分子の濃度が大きく、物理改質・解重合後は比較的早く重縮合する。処理後すぐに使用するのがベストである。
2.化学修飾
化学修飾は水ガラスに少量の化合物を加えることで、これらの化合物はすべてカルボキシル基、アミド基、カルボニル基、ヒドロキシル基、エーテル基、アミノ基などの極性基を含み、水素結合や静電気によってケイ酸分子やコロイド粒子に吸着する。表面、表面ポテンシャルエネルギーと溶媒和能力を変化させ、ポリケイ酸の安定性を向上させ、"老化 "の進行を防ぐ。
例えば、水ガラスにポリアクリルアミド、変性デンプン、ポリリン酸塩などを加えると、より良い結果が得られる。
通常の水ガラス、あるいは改質水ガラスに有機物を配合することで、次のような様々な機能を発揮することができる:水ガラスの粘性流動特性を変化させる;水ガラス混合物の造形性能を向上させる;水ガラスを絶対的な添加量にするために結合強度を増加させる 珪酸ゲルの可塑性を向上させる;残留強度を低下させる、そのため水ガラス砂は鋳鉄や非鉄合金により適している。
3.物理化学的修飾
物理改質は熟成水ガラスに適しており、改質後すぐに使用できる。化学修飾は、新鮮な水ガラスを加工するのに適しており、修飾された水ガラスは長期間保存することができます。物理的改質と化学的改質を組み合わせることで、水ガラスに持続的な改質効果を持たせることができる。例えば、オートクレーブにポリアクリルアミドを添加し、"老化 "水ガラスを改質すると良い効果がある。その中でも、オートクレーブの圧力や加圧を利用する。攪拌は物理的な改質で、ポリアクリルアミドの添加は化学的な改質です。
CO2ブローで硬化したケイ酸ソーダ砂型(中子)の表面チョーキングを防ぐには?
珪酸ソーダ砂にCO2を吹き込んで固めた後、一定時間放置すると、下型(中子)の表面に霜のような物質が発生することがあるが、これはその場所の表面強度を著しく低下させ、注湯時に砂洗い不良を生じやすくなる。分析によると、この白い物質の主成分はNaHCO3であり、珪酸ソーダ砂中の過剰な水分またはCO2が原因と考えられる。反応は以下の通りである:
解決策は以下の通りだ:
水ガラス砂型(中子)の耐吸湿性を向上させるには?
CO2や加熱法で固めたソーダ水ガラス砂中子を湿った粘土型に組み立てる。もし時間内に流し込まれなければ、砂中子の強度は急激に低下し、クリープするだけでなく、崩壊することさえある。表1は、CO2硬化ナトリウム水ガラス砂中子を相対湿度97%の環境に24時間置いた場合の強度値を示している。湿度の高い環境で保管すると強度が低下する理由は、ナトリウム水ガラスが再水和するためである。ケイ酸ナトリウムのバインダーマトリックス中のNa+とOH-が水分を吸収してマトリックスを侵食し、最終的にケイ素-酸素結合Si-O-Siが破壊され、ケイ酸ナトリウム砂の結合強度が著しく低下する。
この問題を解決するための方策は
4 CO2ブロー硬化型水ガラス-アルカリ性フェノール樹脂サンドコンポジットプロセスの特徴は?
近年、鋳鋼品の品質を向上させるため、一部の中小企業ではレジンサンドプロセスの導入が急務となっている。しかし、経済力に限界があるため、レジンサンドの再生設備を購入することができず、古い砂をリサイクルして再利用することができないため、生産コストが高くなっている。コストをあまり上げずに鋳物の品質を向上させる効果的な方法を見つけるために、CO2ブロー硬化ケイ酸ソーダ砂とCO2ブロー硬化アルカリフェノール樹脂砂のプロセス特性を組み合わせ、CO2ブロー硬化ケイ酸ソーダ-アルカリフェノール樹脂を使用することができます。レジンサンドコンパウンドプロセスは、表面砂にアルカリフェノール樹脂砂、裏面砂に水ガラス砂を使用し、CO2を吹き込んで硬化させます。
CO2-アルカリフェノールレジンサンドに使用されるフェノール樹脂は、強アルカリ触媒の作用下でフェノールとホルムアルデヒドを重縮合し、カップリング剤を添加して製造される。PH値は13以上、粘度は500mPa・s以下である。砂に対するフェノール樹脂の添加量は3〜4%(質量分率)である。CO2流量が0.8~1.0m3/hの場合、最適なブロー時間は30~60秒である。ブロー時間が短すぎると、砂中子の硬化強度が低くなり、ブロー時間が長すぎると、砂中子の強度が上がらず、無駄なガスとなる。
CO2-アルカリ性フェノール樹脂砂は、N、P、Sなどの有害元素を含まない。H2S、SO2などの有害ガスが注湯中に放出されないので、環境保護に有益である。
CO2ブロー硬化水ガラス-アルカリフェノール樹脂砂複合プロセスは、鋼鋳物、鉄鋳物、銅合金、軽合金鋳物に広く使用できます。
合成プロセスは簡単で便利なプロセスである。まず、樹脂砂とケイ酸ナトリウム砂を別々に混合し、2つの砂バケツに入れます。次に、混合した樹脂砂を表面砂として砂箱に入れます。
ブローチューブの直径は一般に25mmで、硬化可能範囲はブローチューブの直径の約6倍である。
ブロー時間は、砂型(中子)の大きさ、形状、ガス流量、排気プラグの面積によって決まる。一般的に、ブロー時間は15~40秒以内にコントロールされます。
硬い砂型(中子)を吹いた後、型を取ることができる。砂型(中子)の強度はすぐに上がる。型取り後30分以内に刷毛で塗り、4時間後に注湯用の箱を閉める。
複合プロセスは、レジンサンドの再生設備を持たず、高品質の鋳物を生産する必要のある鉄鋼鋳造工場に特に適している。プロセスは単純で制御が容易であり、製造される鋳物の品質は他のレジンサンド鋳物と同等である。
CO2ブロー硬化ケイ酸ソーダ砂は、CO2ブロー硬化ポリアクリル酸ソーダ樹脂砂とコンパウンドすることもでき、様々な高品質の鋳物を製造することができます。
CO2-有機エステル複合硬化ケイ酸ソーダサンドプロセスの長所と短所を教えてください。
近年、CO2-有機エステル複合硬化ケイ酸ソーダ砂プロセスは、用途拡大の傾向にある。そのプロセスは次の通り:砂の混合中に一定量の有機エステルを加える(通常、通常の必要量の半分、または水ガラス重量の4~6%);造形完了後、CO2を吹き込んで離型強度(一般に圧縮抵抗が必要。強度は約0.5MPa)まで硬化させる;脱型後、有機エステルは硬化を続け、造型砂の強度はより速い速度で上昇する;CO2を吹き込んで3~6時間置いた後、砂型を組み合わせて流し込むことができる。
硬化のメカニズムは
水ガラス砂にCO2を吹き込むと、ガスの圧力差と濃度差の作用で、CO2ガスは成形砂の四方八方に流れようとする。CO2ガスは水ガラスに接触すると、直ちに水ガラスと反応してゲルを形成する。拡散効果により、反応は常に外側から内側に向かうため、まず外層がゲル膜を形成し、CO2ガスと水ガラスが反応し続けるのを防ぐ。したがって、どのような方法でCO2ガスを制御しても、短時間ですべての水ガラスと反応させることは不可能である。分析によると、成形砂が最良の吹き強さに達したとき、CO2ガスと反応する水ガラスは約65%である。つまり、水ガラスは接着効果を十分に発揮しておらず、少なくとも35%は反応しない。有機エステル硬化剤はバインダーと均一な混合物を形成し、バインダーの結合効果を十分に発揮させることができる。中子砂のすべての部分が同じ速度で強度を増す。
水ガラスの添加量を増やすと砂型の最終強度は上がりますが、残留強度も上がり、砂の洗浄が困難になります。水ガラスの添加量が少なすぎると、最終強度が小さくなりすぎ、使用条件を満たせなくなる。実際の生産では、水ガラスの添加量は一般的に4%程度に抑えられている。
有機エステル単独で硬化させる場合、有機エステルの添加量は水ガラス量の8〜15%が一般的である。複合硬化を用いる場合、CO2を吹き込んだ時点で水ガラスは約半分が硬化しており、約半分はまだ硬化していないと推定される。従って、有機エステルの使用量は水ガラス量の4〜6%が適当である。
複合硬化法は、CO2硬化と有機エステル硬化の二つの長所を十分に発揮することができ、水ガラスとの接着効果を十分に発揮することができ、硬化速度が速く、離型が早く、強度が高く、崩壊性が良く、コストが安い。総合的な効果
しかし、CO2-有機エステル複合硬化法は、単純な有機エステル硬化法よりも水ガラスを0.5~1%多く添加する必要があり、使用済み水ガラス砂の再生難易度が高くなる。
珪酸ソーダ法で鋳鉄を製造すると、なぜ砂に粘りが出やすいのか?それを防ぐ方法は?
珪酸ソーダ砂で作られた砂型(中子)を鋳鉄の注湯に使用すると、しばしば深刻な粘着性の砂が発生し、鋳鉄製造への適用が制限される。
珪酸ソーダの砂に含まれるNa2O、SiO2と、注湯時に液体金属から発生する酸化鉄が低融点珪酸塩を形成する。前述したように、この化合物に可溶性の非晶質ガラスが多く含まれると、このガラス層と鋳物表面との結合力が非常に小さくなり、収縮係数が金属と異なる。大きな応力は、砂が付着することなく鋳物の表面から容易に除去できる。鋳物の表面に形成される化合物がSiO2の含有量が多く、FeO、MnOなどの含有量が少ない場合、その凝固組織は基本的にSiO2、FeO、MnOなどの含有量が少ない。その凝固構造は基本的に結晶構造を持ち、鋳物と強固に結合して粘着性のある砂になる。
珪酸ソーダ砂を用いて鋳鉄を製造する場合、鋳鉄の注湯温度が低く炭素含有量が多いため、鉄やマンガンが酸化されにくく、得られる粘着性砂層は結晶構造を有し、鋳鉄と粘着性砂層との間に適当な層を設けることが困難である。酸化鉄層の厚さは、鋳物と粘着性砂層との間の樹脂砂とは異なり、鋳鉄を製造する際に樹脂の熱分解によって明るい炭素膜を生成することができるため、粘着性砂層を除去することは容易ではない。
鋳鉄品の製造によるソーダ水ガラス砂の発生を防ぐために、適切な塗料を使用することができる。水性塗料などは塗装後に表面を乾燥させる必要があるため、アルコール系の速乾性塗料が最適である。
一般に鋳鉄は、珪酸ソーダ砂に適量の石炭粉(例えば3%〜6%)(質量分率)を添加することもでき、鋳物と砂層との間の石炭粉の熱分解によって明るい炭素膜を生成することができる。金属やその酸化物に濡れないので、粘着性のある砂層が鋳物から剥がれやすくなる。
珪酸ソーダは、廃砂を出さない環境に優しい鋳物砂になると期待されているのですか?
水ガラスは無色、無臭、無毒である。皮膚や衣服に触れても、水で洗い流しても深刻な問題を引き起こすことはないが、目に飛散することは避けなければならない。水ガラスは、砂の混合、造形、硬化、注湯の際に放出される刺激性ガスや有害ガスはなく、黒色や酸による汚染もない。しかし、工程が不適切で、珪酸ナトリウムの添加量が多すぎると、珪酸ナトリウム砂の崩壊性が悪くなり、砂の洗浄時に粉塵が舞い、これも公害の原因となる。同時に、古い砂の再生は難しく、廃砂の排出はアルカリ性環境汚染の原因となる。
この2つの問題を克服できれば、ケイ酸ソーダ砂は基本的に廃砂を出さない、環境に優しい造型砂になる。
この2つの問題を解決する根本的な対策は、水ガラスの添加量を2%以下にすることで、基本的には砂を振り切ることができる。水ガラス添加量を減らすと、旧砂中の残留Na2Oも減少する。比較的簡単な乾式再生法を用いれば、循環砂の残留Na2Oを0.25%以下に維持することが可能である。この再生砂は、中小鋳鋼用単成型砂の用途要件を満たすことができる。この時、古い珪酸ソーダ砂が高価で複雑な湿式再生法を使わず、比較的簡単で安価な乾式再生法を使っても、完全に再生でき、基本的に廃砂は排出されず、砂と鉄の比率を1:1以下にすることができる。
ケイ酸ナトリウム砂の効果的な再生方法は?
旧ケイ酸ソーダ砂の残留Na2Oが高すぎると、ケイ酸ソーダを添加した後、造型砂の可使時間が不足し、またNa2Oが蓄積しすぎると石英砂の耐火性が劣化する。従って、使用済みのケイ酸ソーダ砂を再生する際には、残留するNa2Oをできるだけ除去する必要がある。