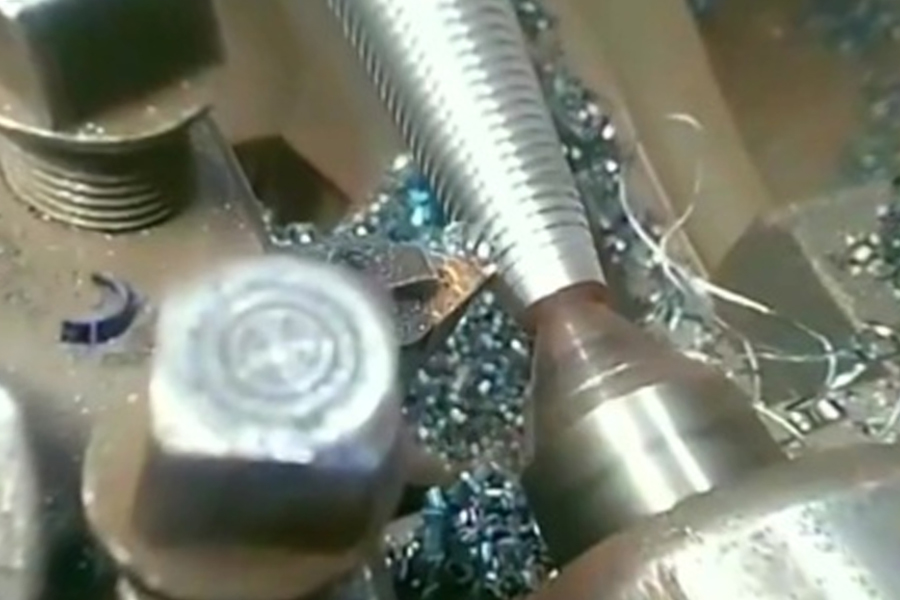
CNC旋盤やマシニングセンタでのねじ切り加工に刃先交換式ねじ切り工具を使用することは、ユーザーにとって非常に重要である。ねじ切り技術を正しく合理的に選択することは非常に重要である。
ねじ切り加工は、加工部品の構造や使用するCNC工作機械によって異なる。一般的には、右ねじの加工には右刃を使い、左ねじの加工には左刃を使うと、刃が安定して支持されるという利点がある。もちろん、一般的には逆の方法も適用できる。
ブレードの片側が過度に摩耗し、工具の寿命が短くなるのをできるだけ避けるため、一貫性を保つ。
d2・・・ピッチ径 A・・・刃の傾斜角度は通常、刃先交換式ねじ切り工具のシムによって決まる。標準工具は+ですが、内径16mm、020mmの内ねじ工具はスペースが小さいためシムがありません。そのため、刃の傾きが+2°を超えると加工できない。
ねじ切り加工の送り方法は、切削機械、被削材、チップの形状、加工するねじのピッチによって決まる。通常、以下の4つの送り方法がある:*一般的に使用される切削方法は、旋削工具の左側と右側が同時に切削され、軸方向の切削成分力はある程度相殺され、軸方向の切削成分力によって引き起こされる旋削工具の偏差の現象を部分的に克服する。両側が均一に摩耗するため、きれいな歯形を確保できるが、切りくず排出性が悪い、放熱性が悪い、力が集中するなどの問題がある。ピッチ1.5mm以下のねじの切削に適している。D片側送りカッタは、半径方向に対して斜めに送り出す。切り屑は刃から転がってストリップ状になり、放熱性に優れている。欠点は、摩擦部分の非切削により、もう一方のエッジが硬化することである。D片面切込み方向30°の角度切込み。切れ刃が両側で切削するため、転造切屑が形成され、切屑排出がスムーズで、放熱性がよく、ねじ面粗さ値が低い。一般的に、ステンレス鋼、合金鋼、炭素鋼の旋削加工に最適な方法である。約90%のねじ切り材がこの方法を採用している。CNC旋盤でのねじ加工には、この方法を使うのが最適である。一般に、固定サイクルを呼び出すことができ、プログラミングも簡単である。
左右交互送り切削、つまりラジアル送りのたびに一定距離を左右に移動し、旋削工具の片側だけが切削に参加するようにする。この方式は一般的に汎用旋盤や3mm以上の中距離のねじ加工に使用され、CNC旋盤でのプログラミングはより複雑になる。
ねじ切り加工は、主にマシニングセンタなどのCNC中ぐりフライス工作機械で使用される。一般に小径の内ねじ(20mm)であればタッピングで加工できる。しかし、大径の内ねじや外ねじの加工には、タッピングやスリーブねじでは問題が多い。そのため、中目金切削加工が最適である。
これは、パターンCNCフライス加工が主に工作機械の3軸リンクとヘリカル補間処理によって実現されるためです。軸方向の移動距離をフライス加工する。片刃フライス加工である。したがって、最良の送り方法は、ラジアル直接送り切削方法を使用することで、2つの切削刃が同時に切断され、力がより均一になります。CNCプログラミングは比較的簡単です。
第二に、ねじ切りおよびフライス切削の選択 ねじ切りパラメータ(切削速度、バックカット量、パス数)の選択は、工具と部品の材質によって決定される。ねじ切り加工の切削速度は、一般的に通常の旋削加工よりも25%~50%低い。また、ねじ山の裏削り量とパス数の選択も特に重要である。D値が正しいかどうかは、中実パターンが適格かどうかに直結する。量は切断力の大小に直結する。ムカデの背の量は減少の原則に従う必要がある。つまり、背の量は前の背の量より少なくなければならず、背の最小値の値を下回ってはならない。5 胃でなければならない。次の2つの表は、メートル法による内径と外径のメディア・パターン背量の値を示している。この表は、ねじ切り加工にも適している。
表1 ISOメートルパターンバックナイフ設定値(外ねじ)(mm)ピッチバックナイフ切削回数フレーバーバックナイフ切削回数表2 ISOメートルパターンバックナイフ設定値(内ねじ)カドミウムバックナイフ切削回数CNC中ぐりフライス工作機械では、ねじ切りフライスは3軸リンクスパイラル補間加工で実現され、ねじ切りとは異なるが、切削量の選択は依然として旋削メディアを使用することができます。パターンの関連切削パラメータ。ねじ切り加工は片刃切削であるため、切削速度は旋削加工の半分とし、バックカット量は旋削加工に準じて選択することができる。
3.ねじ切りおよびフライス加工 CNC プログラムの準備 CNC 旋盤の場合、一般的な標準ねじ切りプログラミング命令は、G33(固定ピッチ切削)、G34(ピッチが増加する可変ピッチのバタフライ切削)、G35(ピッチが減少する可変ピッチのねじ切り)である。中距離は/と人定規で指定され、K /, A:はそれぞれX軸とZ軸に対応する。しかし、一般的なCNCシステムや工作機械メーカーは、ユーザーが使用できるようにねじ切り定型サイクルを提供しており、必要なパラメータを入力するだけでよい。H.特殊なバタフライパターンを加工する場合は、Gコマンドを使用し、自分で座標点を計算するプログラミング方法が必要である。
ねじフライス加工のプログラミングは、CNC旋盤加工とは異なる。G02とG03円弧補間コマンドが主に使用されます、つまり、第3軸直線補間が追加され、2軸円弧補間が追加され、スパイラル補間運動を形成します。以下は、通常の内ねじM30X 2、深さ14ミリメートルCNCフライス加工プログラムであり、ナイフを1.2ミリメートルに戻し、ラジアル直接切断法を採用しています。
F200はエッジ補正を行い、ラジアル送りでバックグラビングツールの位置まで送ります。世紀切削では、多くの場合、工具(チップ、シム、アーバなどを含む)、送り方法、切削量などの選択の正しさに起因する。ムカデの加工品質に影響する。例えば、ネジの表面にショックマークがある、表面粗さの値が篼。これは、部品や工具の伸びすぎ、剛性不足、工具中心の削りすぎ、切削量・刃物・針金の選択ミスなどが考えられます。切削速度の増減、工具の外側の伸びを短くする、センターハイトや送り方法の調整、サイドフィードやラジアルフィードの採用、十分な冷却、パス数の増加などの解決策が考えられます。
工具の摩耗が早く、工具寿命が短いのは、切削速度が速すぎる、冷却が不十分、切削回数が多すぎる、刃物の銘柄が間違っていることが原因である。切削速度を下げる、冷却を十分にする、切削回数を減らす、靭性の良い耐摩耗刃Dの硬度を選ぶ、切削角度を変える、冷却を増やす、切削速度を上げる、バックナイフの量を減らす、センターフレームを調整するなどの方法がある。
従来の加工工程では、まず底面をスクライブ、プレーニングし、その後T611中ぐり盤で加工していた。加工中、1個1個修正する必要があり、クランプが面倒で、時間と手間がかかり、能率が悪い。
加工能力が不足している。そこで、工作物の主要サイズであるベアリングブラケット(H7rr35、中心高さ257s)を製作するために、旋削・中ぐり用の特殊な工具冶具を設計した。これに基づき、治具の設計は図のようになる。治具はCW6263旋盤で使用する。
クランプは本体3と三爪セルフセンタリングチャック4から構成される。三爪セルフセンタリングチャックの片方の爪を外す。本体3の左端をチャックに連結し、ボルト1で固定する。A側テーブルをベアリングブラケットの位置決め面に載せる。s まず、ベアリングブラケット5の中心を確保し、不適切な選択による三爪自動選択で、送り方法を変更し、角をカットする。
切れ刃にビルドアップエッジが施されているため、切削速度が向上し、冷却効果も高まります。コーティングされた超硬チップは、改善されたサイドフィードでの切削に使用されます。
工具の過度の塑性変形は、冷却不良、高すぎる切削速度、間違った刃の等級、および毎回のバックグラビングの量が大きすぎることが原因です。バックグラビングの量を減らし、冷却を増やし、切削速度を下げ、切削時間を増やし、高硬度、耐摩耗性硬質合金またはXu層ブレードを使用すべきである。
ねじ山にバリがある場合は、切削速度を上げる必要があります。切削センタリングチャック4の自動センタリング原理を使い、ワークをクランプして加工する。
その後、チャックを締めてワークをクランプする。
衝突の代わりに車を使用することで、ベアリングブラケットの設計要件を完全に満たし、寸法精度と位置精度を保証し、ワークのスクライビングと修正を節約し、品質を保証し、作業効率をボーリングに比べて1.8倍向上させます。
センター高さの異なるベアリングブラケットは、パッドアイアンを追加することで調整できるが、ボルトで固定する必要がある。
使用前には、遠心力がワークの品質や装置のプレッシャープレートに影響するのを避けるため、バランス調整が必要です。