1.成形品の外観、サイズ、適合性
1.製品表面の欠陥は許されない:材料不足、焦げ、上白、白線、ピーキング、ブリスター、白化(または割れ、破損)、ベーキング、しわ。
2.溶接マーク:一般的に、円形の穿孔溶接マークの長さは5mm以下、特殊な形状の穿孔溶接マークの長さは15mm以下であり、溶接マークの強度は機能安全試験に合格することができます。.
3.収縮:外観上明らかな部分については収縮を認めず、明らかでない部分(へこみを感じない部分)についてはわずかな収縮を認める。.
4.一般的に小型製品の平面度は0.3mm以下である。組立が必要な場合は、組立条件を保証しなければならない。
5.明らかな外観に空気線や材料の花があってはならず、製品には一般的に気泡があってはならない。
6.製品の幾何学的形状と寸法精度は、正式かつ効果的な金型図面(または3Dファイル)の要件を満たす必要があります。製品の公差は公差の原則に基づくべきである。シャフトの寸法公差は負の公差であり、穴の寸法公差は正の公差である。顧客は要求されるように、要求されるように持っている。
7.製品の肉厚:製品の肉厚は、一般的に平均肉厚であることが要求され、非平均肉厚は、図面の要件を満たす必要があり、公差は、金型の特性に応じて-0.
8.製品の調整:表殻と底殻の調整:表面のずれは0.1mm以下であり、傷があってはならない。穴、シャフトと表面は、一致する要件があり、一致する間隔と使用要件を確保する必要があります。
第二に、金型の外観である。
1.金型銘板の内容が完全で、文字が明瞭で、配列がきちんとしている。
2.銘板はテンプレートと基準角の近くの金型脚部に固定する。銘板は信頼性が高く、剥がれにくい。
3.冷却水ノズルはプラスチックブロック水ノズルであるべきですが、顧客はそうでなければ必要な場合は、要件に従ってください。4.冷却水ノズルは金型ベースの表面から突出しないでください。
5.冷却水ノズルにはザグリ加工が必要です。ザグリ径は25mm、30mm、35mmがある。オリフィスは面取りされており、面取りは同じでなければならない。.
6.冷却水ノズルには、出入り口を記すこと。
7.マークの英字と数字は5/6以上、位置はタップの真下10mmとする。筆跡は明瞭で美しく、整然とし、等間隔であること。
8.金型の付属品は、金型の吊り上げや保管に影響を及ぼしてはならない。設置の際、オイルシリンダー、蛇口、プリセット機構などが露出する。これらは支持脚で保護されるべきである。
9.支持脚の取り付けは、支持脚を貫通するネジで金型ベースに固定する必要があり、長すぎる支持脚は、加工された外ネジ柱で金型ベースに固定することができる。
10.金型のエジェクターの穴の大きさは、指定された射出成形機の要件を満たす必要があります。小さな金型を除き、1つのセンターで射出することはできません。
11.位置決めリングは固定された信頼性の高いものでなければならない。リングの直径は100mmと250mm。位置決めリングは底板より10-20mm高い。顧客の特別な要求がない限り。
12.金型の外形寸法は、指定された射出成形機の要件を満たす必要があります。
13.向きが決められている金型は、前面テンプレートまたは背面テンプレートに矢印で取り付 け方向を示してください。矢印の横に "UP "と記載する。矢印と文字は共に黄色で、文字の高さは50mm。
14.モールドベースの表面には、ピット、錆跡、冗長リング、水蒸気の出入り、オイルホールなどがあってはならない。外観に影響を及ぼす欠陥がないこと。
15.金型は吊り上げ、運搬が容易でなければならず、吊り上げ中に金型の部品が分解してはならず、吊り上げリングがウォーターノズル、オイルシリンダー、プリセットロッドなどに干渉してはならない。
3.金型の材質と硬度
1.モールドベースは、規格に適合した標準モールドベースでなければならない。
2.金型成形部品およびゲートシステム(コア、可動金型および固定金型インサート、可動インサート、スプリットコーン、プッシュロッド、スプルースリーブ)は、40Crより高い性能を持つ材料で作られています。
3.金型に腐食性のあるプラスチックを成形する場合は、成形品に耐食性のある材料を使用するか、成形面に防食対策を施す。
4.成型部品の硬度は50HRC以下、または表面硬化処理の硬度は600HV以上でなければならない。
4、イジェクト、リセット、フェルールを抜く、取り出す
1.排出がスムーズで、詰まりがなく、異音がないこと。
2.傾斜上面は研磨され、傾斜上面はコア面より低い。
3.摺動部に油溝を設け、表面に窒化処理を施し、処理後の表面硬度をHV700以上とする。
4.すべてのエジェクターロッドに回転止めの位置を決め、各エジェクターロッドに番号を付ける。
5.排出距離はリミットブロックによって制限されるべきである。
6.リターンスプリングには標準部品を使用し、スプリングの両端を磨いたり削ったりしてはならない。
7.スライダーと芯抜きにはストローク制限が必要で、小型のスライドはバネで制限される。バネの取り付けが不便な場合は、波形のネジを使用できる。シリンダーの芯抜きにはストロークスイッチが必要である。
8.一般的にスライダーの芯抜きには傾斜ガイドポストを使用し、傾斜ガイドポストの角度はスライダーのロック面の角度より2°~3°小さくする。スライダーのストロークが長すぎる場合は、オイルシリンダーで引く。
9.シリンダーの芯抜き形成部の端面を覆う場合、シリンダーはセルフロック機構を備えていることが望ましい。
10.幅150mm以上の大型スライドの下には耐磨耗プレートを設けること。耐摩耗プレートの材質はT8Aとする。熱処理後の硬度はHRC50-55。耐磨耗プレートは大型の表面より0.05~0.1 mm高い。オイルタンクを開ける。
11.エジェクターロッドが上下に動かないこと。
12.トップロッドにバーブを付け、バーブの方向を一定にする。
13.エジェクターピン穴とエジェクターピンの間のクリアランス、シール部の長さ、エジェクターピン穴の表面粗さは、関連する企業標準の要求に従ってください。
14.製品は作業者が取り出すのに便利でなければならない。
15.製品が排出されるとき、傾斜した上部をたどるのは簡単であり、上部のロッドには溝をつけるか、エッチングを施すべきである。
16.トップロッドに固定されるトップブロックは堅固で信頼できるものでなければならず、円周上の非成形部分は3°~5°の勾配で加工され、下部外周は面取りされていなければならない。
17.金型ベースのオイル通過孔に鉄粉があってはならない。
18.リターンロッドの端面はフラットで、スポット溶接はない。胚頭の底にガスケットがなく、スポット溶接。
19.3プレート金型のゲートプレートはスムーズにスライドし、ゲートプレートは簡単に開く。
20.金型のリミット棒は、金型設置方向の両側に3枚板を配置するか、金型ベースにプルプレートを追加してリミット棒が作業者の邪魔にならないようにする。
21.オイル回路とエア通路はスムーズでなければならず、油圧エジェクタ・リセットは所定の位置になければならない。
22.排気口はガイドスリーブの底部に開口していること。
23.位置決めピンの取り付けに隙間があってはならない。
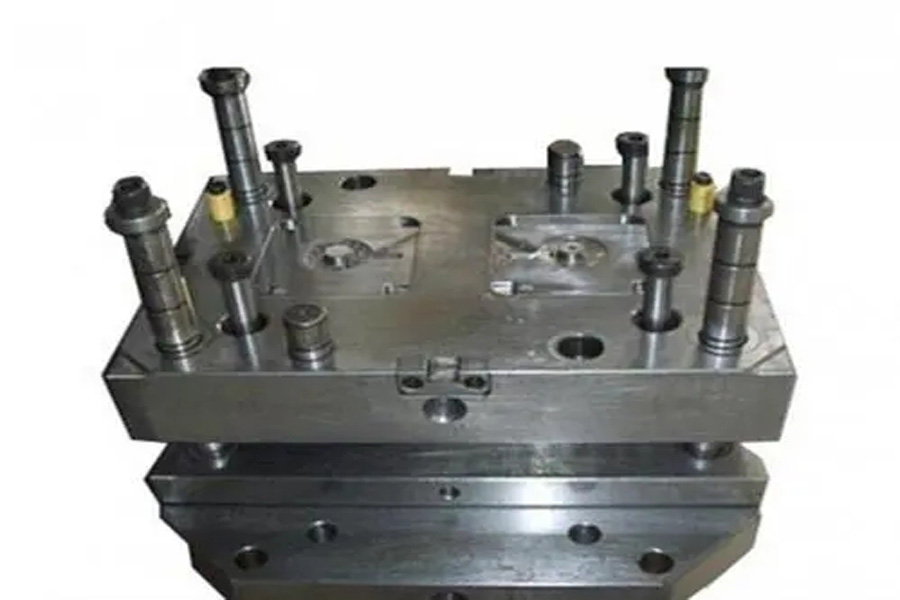
5.冷暖房システム
1,冷却または暖房システムが完全にブロックされていないこと。
2.シールは信頼できるものでなければならず、システムは0.5MPaの圧力下で漏れることはなく、点検や修理が容易でなければならない。
3.金型ベースに開けられたシール溝のサイズと形状は、関連規格の要件を満たす必要があります。
4.シールリングを設置する際にグリースを塗布し、設置後は金型ベースの表面より高くなるようにする。
5.水と油の流路セパレータは、腐食しにくい材質で作られるべきである。
6.フロントとリアの金型は集中給水を使用すること。
6、注入システム
1、ゲートの設定は、製品の外観に影響を与えず、製品の組み立てを満たす必要があります。
2.ランナー断面と長さを合理的に設計し、成形品質の確保を前提に工程をできるだけ短縮し、断面積を小さくして充填・冷却時間を短縮する。同時に、注湯系の塑性ロスを最も少なくする。
3.三板金型ランナーの前金型後方の部分は、台形または半円形にする。
4.3プレート金型は、ゲートプレートに材料ブレーカーがあり、ゲート入口の直径は3mm以下でなければならず、ボールヘッドにはゲートプレートに凹んだ3mmの深さの段差がある。
5.ボールエンドプルロッドは確実に固定する必要があり、位置決めリングの下で押したり、ヘッドレスネジで固定したり、プレッシャープレートで押したりすることができる。
6.ゲートとランナーは、図面の寸法要求に従って機械加工されるべきであり、手動の研削機や研磨機は認められない。
7.点ゲートゲートは、仕様書の要求事項に従うこと。
8.ランナーの前端には、コールドスラッグホールとして延長部があるはずだ。
9.引っ張り棒のZ字型逆バックルは、滑らかな移行部を持つべきである。
10.パーティング面のランナーは丸く、前後の金型がずれてはならない。
11.エジェクター・ロッド上のラテント・ゲートには表面収縮がないこと。
12.透明製品のコールドスラグ穴の直径と深さは、設計基準を満たすべきである。
13.取っ手の取り外しが簡単で、製品の外観にゲート跡がなく、製品組立時に取っ手が残らない。
14.湾曲フック潜りゲートの場合、インサートの2つの部分は窒化処理する必要があり、表面硬度はHV700に達することができます。
セブン、ホットランナーシステム
1.ホットランナーの配線レイアウトは、メンテナンスが容易なように合理的であるべきであり、配線番号は一対一対応であるべきである。
2.ホットランナーは安全性試験を受け、対地絶縁抵抗が2MW以上でなければならない。
3.温度制御盤、ホットノズル、ホットランナーは標準部品を採用する。
4.メインフローポートスリーブはホットランナーとネジで接続されており、底面はホットランナーと接触してシールされています。
5.ホットランナーは加熱プレートまたは加熱ロッドとよく接触し、加熱プレートはネジまたはスタッドで固定され、表面はよくフィットする。
6.J型熱電対を使用し、温度調節計に合わせる。
7.各発熱体群は熱電対によって制御されるべきであり、熱電対の位置は合理的に配置されるべきである。
8.ノズルは設計要件を満たしていること。
9.ホットランナーは、少なくとも2本の位置決めピンで確実に位置決めするか、ネジで固定する。
10.ホットランナーとテンプレートの間に断熱パッドがあること。
11.温度調節計の設定温度と実際の表示温度との誤差は±5℃以下であるべきであり、温度制御は敏感であるべきである。
12.キャビティとノズルの取り付け穴を通す。
13.ホットランナーの配線は束ね、プレッシャープレートで覆う。
14.同じ仕様のソケットが2つあり、明確に表示されていなければならない。
15.コントロール・ラインはシースされ、損傷していないこと。
16.温度制御盤の構造は信頼でき、ネジは緩んでいない。
17.ソケットはベークライトに取り付けられ、テンプレートの最大サイズを超えることはできない。
18.ワイヤーが金型の外に露出してはならない。
19.ホット・ランナーやテンプレートがワイヤーに接触するすべての場所には、丸みを帯びた移行部を設ける。
20.テンプレートを組み立てる前に、すべての回路に開回路や短絡がないこと。
21.すべての配線は正しく接続され、良好な絶縁性能を備えていなければならない。
22.テンプレートを取り付け、クランプした後、すべての回路をマルチメーターで再度チェックすること。
8.成形部、パーティング面、排気溝
1.フロントおよびリア・モールドの表面に、外観に影響を及ぼす凹凸、くぼみ、さびその他の欠陥があってはならない。
2.インサートを金型枠に合わせ、角の丸みの周囲に1mm以下のクリアランスがあるようにする。
3.パーティング面はきれいに整頓されている。空洞を避けるために携帯用砥石はなく、シール部にはへこみがない。
4.排気溝の深さは、プラスチックのオーバーフロー値以下でなければならない。
5.インサートの研究と配布は、スムーズな配置と確実な位置決めがなされていなければならない。
6.インサート、インサートなどは確実に位置決めして固定し、丸駒が回転しないようにし、インサートの下に銅板や鉄板を敷いてはならない。
7.エジェクターロッドの端面はコアと一致している。
8.前後金型の成形部にアンダーカットや面取りなどの欠陥がない。
9.リブはスムーズに押し出されるはずだ。
10.マルチキャビティ金型製品の場合、左右の部品は対称であり、LまたはRを表示する必要があります。位置や大きさについて顧客の要求がある場合は、顧客の要求を満たす必要がある。一般的には、外観や組立に影響のないところに追加する。文字サイズは1/8とする。
11.金型ベースのクランプ面が所定の位置にあり、75%以上の面積が接触していること。
12.エジェクター・ロッドは、側壁の近く、リブやボスの横に配置し、より大きなエジェクター・ロッドを使用すべきである。
13.同じ部品については、1、2、3などの番号を示す。
14.それぞれの接触面、貫通面、パーティング面を研究し、所定の位置に合わせること。
15.パーティング面のシール部分は設計基準を満たす必要がある。中型金型は10-20mm、大型金型は30-50mm、残りの部分は空隙がないように加工する。
16.肌の質感とサンドブラストは、顧客の要求を均一に満たすべきである。
17.外観が要求される製品については、製品のねじに収縮防止対策を施すこと。
18.深さ20mm以上のスクリュー・コラムには、ジャック・パイプを使用する。
19.製品の肉厚は均一であるべきで、その偏差は±0.15mm以下に制御されるべきである。
20.リブの幅は、外面の肉厚の60%以下とする。
21.傾斜屋根のインサートコアとスライダーは、確実な固定方法が必要である。
22.前側の金型を後側の金型に挿入するか、後側の金型を前側の金型に挿入し、側面を傾斜面でロックし、空気が入らないように加工する。
九、射出成形生産工程1、金型は射出成形生産の安定性と通常の射出成形工程条件の範囲内のプロセスパラメータの調整の再現性を持っている必要があります。
2.金型射出生産時の射出圧力は、一般的に射出成形機の定格最大射出圧力の85%未満でなければならない。
3.金型の射出成形生産の射出速度は、4分の3ストロークの射出速度は、定格最大射出速度の10%以上、または定格最大射出速度の90%以上ではありません。
4.射出成形中の金型の保持圧力は、一般的に実際の最大射出圧力の85%未満であるべきである。
5.射出成形時の金型の型締力は、適用機種の定格型締力の90%以下でなければならない。
6.射出成形の製造工程では、製品とノズル材料を簡単かつ安全に取り出す必要があります(時間は一般的にそれぞれ2秒以内)。
7.インサート付き金型の場合、インサートの取り付けは簡単で、インサートは生産中に確実に固定されます。
10.梱包と輸送
1 金型キャビティを清掃し、防錆油をスプレーする。
2.摺動部に注油すること。
3.スプルーブッシュの入口はグリースでシールする。
4.金型はクランプピースを備えている必要があり、仕様は設計要件を満たしています。
5.スペア部品と消耗部品は、詳細なリストと供給業者名が記載された完全なものでなければならない。
6.金型の水、液体、ガス、電気の出入り口に異物が入り込まないよう、密閉措置を講じること;
7.顧客の要求に応じて、金型の外面にスプレー塗料を塗る。
8.金型は、顧客の要求に応じて、防湿、防水、バンプ防止包装で梱包する必要があります。
9.金型製品図面、構造図面、冷却および加熱システム図面、ホットランナー図面、予備部品および金型材料サプライヤーの詳細、操作説明書、金型試験報告書、工場検査証明書、電子文書がすべて揃っていること。