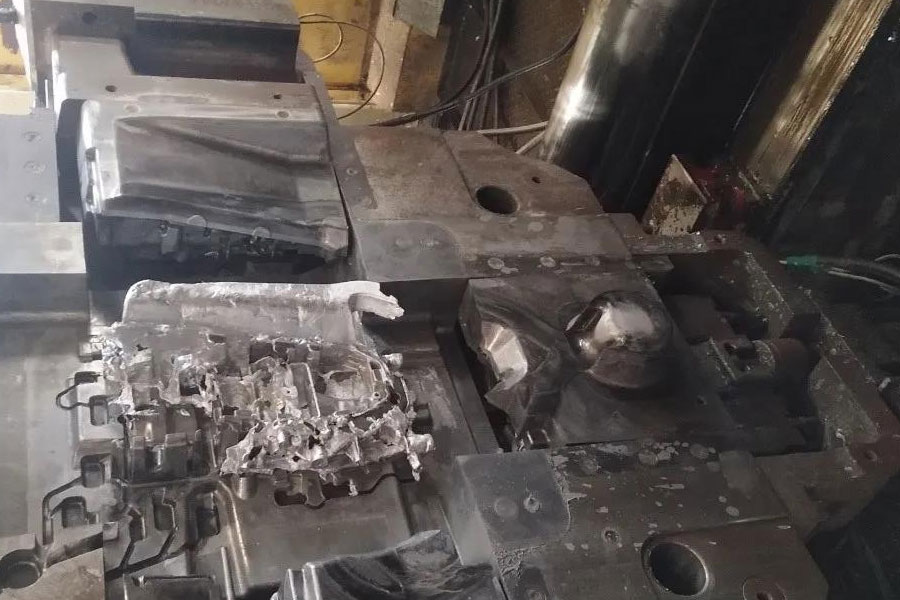
自動車産業の急速な発展に伴い、部品の材料、設計、製造に対する要求が高まり、高集積化、高性能化、低コスト化が開発トレンドとなっている。オイルパンと下部シリンダーブロックは共に自動車エンジンの重要な部品である。下部シリンダーブロックのバランスシャフトとオイルパンの回収ろ過機能を同じ部品に統合することで、エンジンの重量と体積を効果的に減らすことができる。しかし、構造が複雑で肉厚の変化が大きいため、異なる製品に分割して別々に加工した後、組み合わせて加工する必要があり、製品製造に困難が生じる。
本課題で研究したエンジンの一体型オイルパンには、オイルパン本体、バランスベアリングカバー、およびシングルバランスベアリングカバーの3つの鋳物が含まれている。A380改質合金材料を使用し、鋳物の平均肉厚は3mm、最小肉厚は2.74kgである。内部キャビティは300kPaで漏れなく、600kPaで温度が60℃を超えてもオイル通路が漏れないことが要求される。1.5Tエンジンに使用され、年間生産量は400,000個で、典型的な複雑なオイルパン鋳物である。
ダイカスト設計の技術的ポイント
1.1 ランナーデザイン
鋳造1は三方注湯の設計を採用していますが、図1に示すように、全体的な注湯は片側に集中しています。製品が長い(上下の長さは437.2mmに達する)ので、三面注湯設計は、異なる領域に製品を充填するように、長いプロセスの問題を効果的に軽減することができます。しかし、製品全体の肉厚が厚く、注湯位置に盛り上がった挿入部が多いことを考慮し、アルミ溶湯の流動性が阻害されるのを避けるため、片側の充填を強化し、全体として断面積を徐々に狭めてアルミ溶湯の流動を促進させる。デザインスプルー。
鋳造2はバランスベアリングカバーで、比較的シンプルな形状で、中間の二つのバランスシャフトオイル溝だけが厚い。アルミニウム溶湯の単純な流動パターンに基づき、コストを節約し、アルミニウム溶湯の有効生産量を増加させるため、図2に示すように、片側注湯方式を採用し、ゲートを肉厚部に配置して供給する。
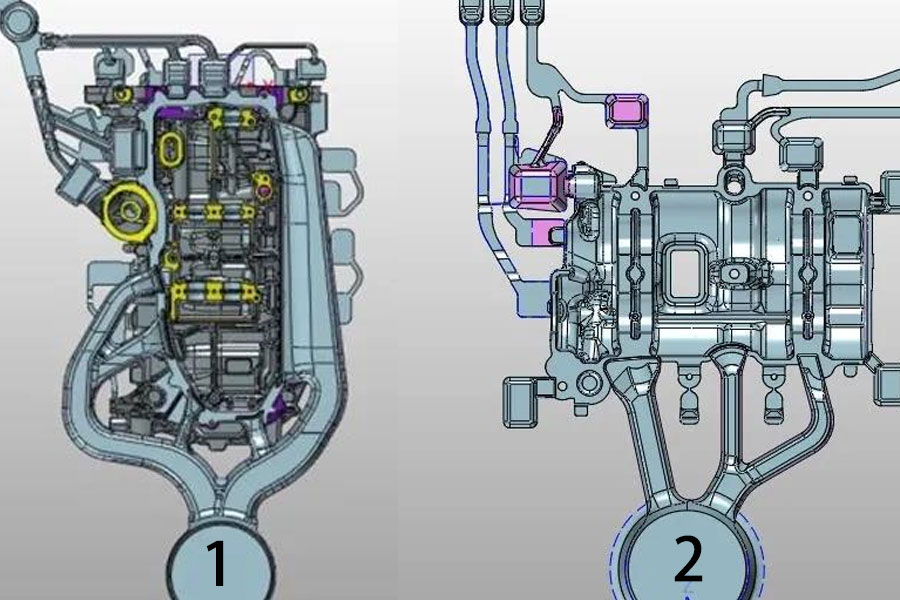
鋳造3は、図3に示すように、小径部(サイズ63mm)×15mm×1個のバランスシャフトタイルカバーで、充填・注湯のために1個のキャビティと8個の鋳型の設計が採用されている。
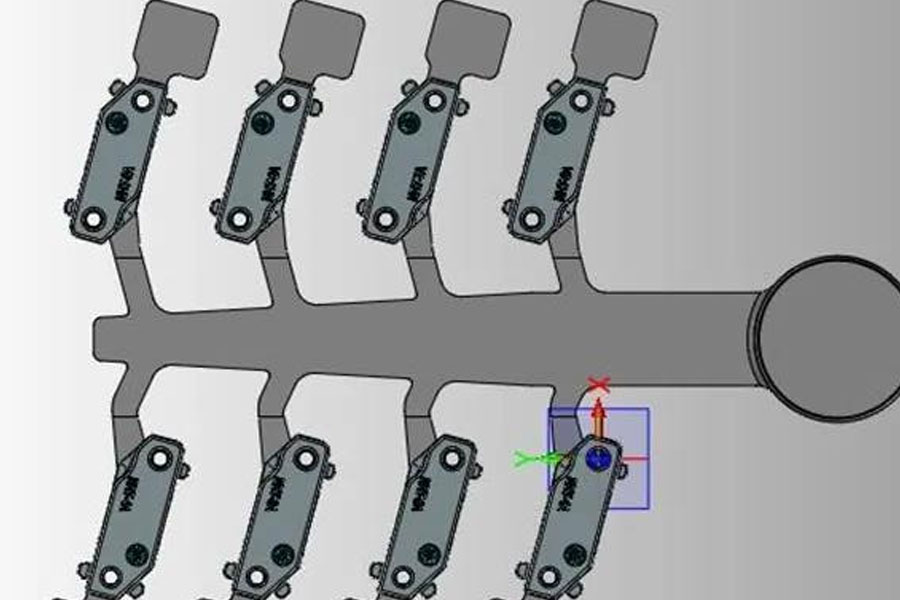
1. 2 排気方法
複合鋳造1では、排気に高真空を使用。鋳造2は、通常の「洗濯板」タイプの排気ブロックを使用。鋳造3はスラグバッグを直接採用し、スラグバッグの尾部に鋳型中子の排気路を設ける。ここでは、鋳造1の排気技術のポイントを強調する。
鋳物の高圧オイル通路とオイルフィルターはウォーターテールに集中しているため、ウォーターテールの排気効果はこれらの場所の内部品質を決定する重要な要因である。鋳物1では、鋳物のウォーターテールの負圧領域の気圧を下げるために、高真空排気を採用しています。まず第一に、真空タンクの容積を≧800L(ここでの800Lは、キャビティとトラフを含む鋳型の容積の10倍以上)を選択し、負圧流路を迅速に形成する必要があります。第二に、金型と真空機をつなぐパイプラインを密閉して気密性を保ち、パイプラインの真空度を2000Pa以内に保つ。第三に、金型はシールテープで密閉され、シンブルとコアピンはすべてシール剤でコーティングされる。金型を閉じた後、キャビティの真空度を4 000 Pa以内に保たなければならない。最後に、密閉ポンチの最適な製造方法を選択するか、ポンチの拡張版を使用してポンチの密閉面積を増やし、キャビティへの空気の漏れを効果的に緩和する。
1.3 金型温度
高真空の特性上、アルミニウム溶湯は理論的な流動状態(図4参照)どおりに完全には充填されず、その中に吸い込まれたアルミニウム溶湯は特定の場所で速やかに凝固しやすく、ダイカストポア、引け巣、クラック等のダイカスト欠陥の原因となる。この鋳造品1は、ポンチが410mmの位置まで移動した時点で真空引きを開始し(アルミ液の充満度が要求値の70%に達する)、540mmの位置で真空引きを終了する。このような短時間では、引抜かれたアルミ液があらかじめ湯尻の重要な位置で凝固しないようにしなければならない。そこで、これらの位置の金型温度は、油温機を用いてそれぞれ220℃と180℃に制御している。金型温度を高め、アルミ溶湯の流動性を高めることが、この重要な2カ所の内部品質を確保するカギとなる。
鋳物2と鋳物3は、構造が比較的単純で、充填距離が短く、成形が容易である。鋳型表面温度が高く、製品が黒くならない限り、高い鋳型温度を必要としない。
1.4 つの金型冷却オプション
この鋳物1は、超点冷却技術と間欠給水技術を採用している。鋳物製造では高温を維持する必要があり、可動金型側のインサートボスの数が多くなるため、高温を確保するだけでなく、盛り上がったインサートがホットジョイントを形成して引け巣割れなどの不具合を発生させないようにする必要がある。切削加工はインサートごとに行い、スポット冷却はインサート内部まで追い込む。同期周辺装置は間欠給水方式を採用している。製品の凝固段階で電磁弁を開き、局所的に冷却する。これにより、より高い温度が得られるだけでなく、良好な冷却効果も得られる。図1の矢印で示すように、超点冷却プロセスはダイカスト中子針用に設計されている。肉厚部分の真ん中に4mmの針があると、直接収縮が起こります。超点冷却設計は、4 mmの針に使用され、ねじ穴の孔問題を解決することができます。同様に、他のクロスホットスポットでは、針が排出できるスーパーポイント冷却針設計が使用され、火傷、気孔、針折れの問題を大幅に緩和します。超点冷却と間欠給水の時間設定は、材料の打ち抜き穴の肉厚とその位置を考慮する必要がある。従って、これらの異なる区域の冷たい針は、ゾーン制御される必要がある。
鋳造2は、バランスシャフトの中間部に4mmの油溝穴と、投入口にΦ8mmのボルト穴があるだけで、超点冷制御を採用している。鋳造3のΦ8mmの16本の小針は、いずれもピンホール付近の緻密層の厚さを維持するために超点冷間制御を採用しています。
1.5 現地押出技術の選択
局部押し出しピンは、肉厚部の収縮を迅速に解決でき、ダイカスト鋳造の分野で広く使用されている。モールドフローのホットジョイントの解析を図5に示す。鋳造1では熱節が多く、押出しピンの位置を合理的に配置する必要がある。まず、冷し針で解消できる熱節は解消し、次に重要な位置にない熱節を解消する。最後に、金型の内部空間におけるスクイズピンのシリンダーの配置を考える必要があります。一般的には、構造が複雑で空気漏れを防ぐ箇所に配置する。.
ダイカスト工程管理のポイント
2.1 ダイカスト鋳造時のスプレーの流れの制御
ダイカスト工程では、移動金型と固定金型で別々にスプレー流量を測定し、移動金型は3 200mL、固定金型は2 200mLに制御します。また、上限偏差値と下限偏差値は、動型と固定型の流量で別々に設定します。選定した電磁流量計の精度は50mLであるため、設定偏差は±200mLとなり、200mLはスプレーガンを1本減らした後の実測値となる。生産プロセス中、偏差値を超えた場合、アラーム信号が直接出力され、ダイカスト生産サイクルが停止します。そのため、スプレーガンによる噴霧が妨げられ、金型の固着や火傷の原因となることを効果的に防ぐことができます。
2.2 アルミニウム溶湯温度のプロセス制御
保持炉の保温効果は良好ですが、定量炉に比べて加熱速度が遅いため、アルミニウム溶湯の入熱温度を制御する必要があります。アルミニウム溶湯の鋳造温度は675±10℃なので、輸送取鍋のアルミニウム溶湯の入熱は700℃以上に保たなければなりません。この温度以下で投入すると、充填時のアルミニウム溶湯の流動状態に影響を与え、局部的に気孔の割合が増加する。730℃以上の材料を添加すると、鋳型の表面でアルミニウムの深刻な焦げや固着を引き起こし、鋳物の外観品質に影響を与えます。保持炉のアルミニウム溶湯の温度アラームを設定してください。注湯温度が範囲内でない場合、保持炉はアラームを発し、ダイカスト生産サイクルを停止します。これにより、アルミニウム溶湯の温度偏差による欠陥を効果的に防止できます。
2.3 真空制御
鋳物1の金型は可動・固定式のモールドシールテープで密閉されているため、シンブルやコアピンはすべてシール剤を塗布して密閉されており、シュートも一体型のシュートであるが、パンチは専用のシールパンチは使用せず、延長プレートパンチ(150mmまで延長)を使用している。このような密閉状態では、真空度が4kPa(4kPaは生産工程でのハイパスレートに応じて設定される経験的なアラーム値)を超えるとアラームが作動し、一般的に真空度は2.3kPaである。クリーン度、目詰まり度は概ね101kPaに近く、設定警報値は90kPa(90kPaは工場でのフィルタータンクの洗浄サイクルに応じて設定される)。洗浄サイクルの最後に、真空バルブフィルタータンクを時間内に洗浄する必要があります。清掃を怠るとバキューム効果に影響します。バキュームタンクの設定値は1kPaで、一般的には2.2~400Paです。設定値を超えるとアラームが鳴り、ダイカストマシンが停止します。
2.4 実際の注入パラメータのモニタリング
ダイカストマシンは国産の宇部1650T型を採用している。独自のダイカストマシンのパラメータ制御システムのほか、二次元コードトレーサビリティシステム(工場ではMESシステムと呼ぶ)を採用し、ダイカストマシンと周辺補機を接続することで、MESシステムは各金型の生産パラメータをリアルタイムで読み取り、クラウドにフィードバックしてクラウド上で比較することができる(クラウド比較値は必要に応じて事前にクラウドに入力し、異なるパラメータの実績達成度に応じて異なる範囲の値を出力する。例えば、低速は±0.05m/s、高速は±3m/sなど。例えば、低速は±0.05m/s、高速は±3m/sなど(表2参照)、比較の結果、範囲を超えた製品はシステムによってロックされ、不適格と判定される。また、クラウドビッグデータは、更新されたデータ量に基づいて、製品の陳腐化とパラメータ変化の関係をリアルタイムで定期的に計算する。一定期間内のスクラップ率の変動原因を突き止め、製品維持の適格率を向上させる。ダイカスト生産工程に変動があり、迅速に問題点を発見し、その場で効果的に好循環を促進することができる。
2.5 ダイカスト水輸送の制御
水輸送の最初に、各ラインは電磁弁を使用して、直接冷却または通常のポイント冷水の輸送時間を制御します。水圧は0.4MPa、水温は30℃の純水です。トラフ、材料スリーブ、パンチ、スプリットコーン、材料スリーブ強制コールドプレートはノーマルオープンで直接冷却であることを除いて、他のすべての直接冷却(水の障壁)と大きなポイント冷却は、電磁弁によって制御され、遅延3秒、金型温度を確保するために15秒を冷却する。すべての針は、Φ4 mmからΦ14 mmまで(Φ1.5ミリメートル)スーパーポイントコールドによって制御され、スーパーポイント冷水輸送圧力は10 MPaであり、水輸送温度は10℃である(ここで温度が低すぎる設定することはできません、低すぎるより多くの熱を奪うが、それは簡単に壊れた針を引き起こすでしょう)、同じサイズの超低温針の各グループは8を超えない(8以上の針は直径G1/2接続パイプの直径を超える )、すべての針は、Φ4 mmのポイントコールド針を除いて、遅延時間は5秒であり、冷却は13秒であり、Φ4 mmのポイントコールド針は、金型温度フィールドをターゲットにするために4秒を遅らせ、冷却時間は13秒に設定されている6グループの合計に結合されます。急速に冷却する必要がある領域では、ホットスポットの発生を低減します。金型温度のバランスと保温を保証するだけでなく、局所的なホットスポットをなくし、製品の品質を保証します。
3.新型多機能オイルパンの品質。3つの製品は2つの異なる機械で生産され、1日の生産量は鋳造1から鋳造3まで、980個/日、1,500個/日、12,000個/日と高い。最終組立までの3製品の総合合格率は97%と高い。図8は鋳物1、2の外観と鋳物1、2、3の内部品質の写真である。