アルミダイカスト鋳物は、生産効率が高く、加工コストが低く、生産工程の機械的自動化が容易で、鋳物の寸法精度が高く、表面品質が良く、総合的な機械的性質が良いという利点があるが、鋳造工程でポア、フローマーク、キズが発生しやすい。キズ、へこみ、割れ、鋳造不足などの欠陥がある。ダイカストの外観品質や機械的性質を劣化させる。ダイカスト成形工程における上記のような問題を回避するために、構造設計者はダイカスト部品の構造設計において事前に計画を評価し、部品の構造設計において合理的なレイアウトを行い、構造の最適化により欠陥を最小限に抑える必要がある。
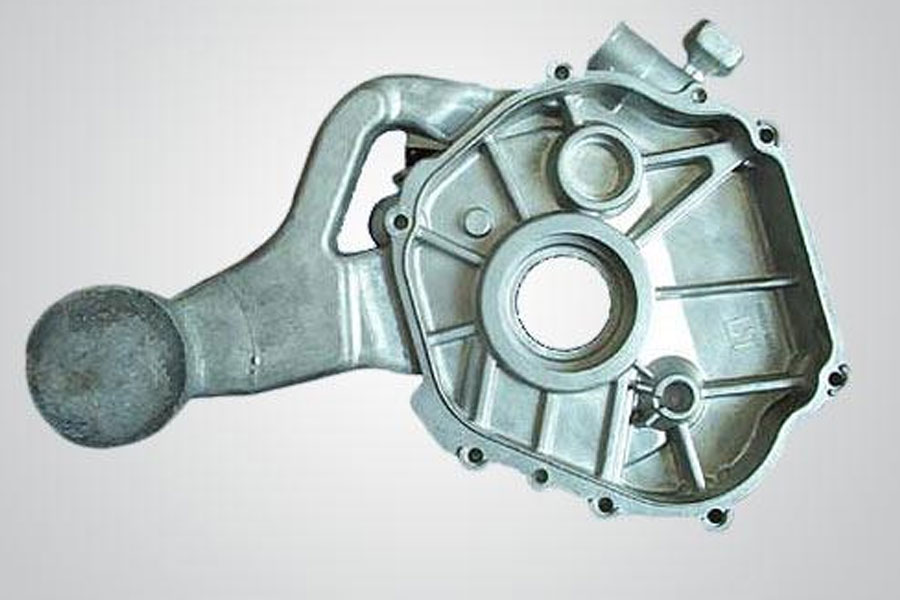
アルミニウム合金ダイカストの成形原理
アルミニウム合金のダイカスト部品は、ダイカストマシンとアルミニウム合金を総合的に組み合わせて、金型によって形成する必要があります。ダイカスト鋳造の原理は、溶融金属を高圧で精密金型のキャビティに高速で流し込み、加圧下で溶融金属を冷却凝固させて鋳物を形成します。コールドチャンバーダイカストとホットチャンバーダイカストは、ダイカストプロセスの2つの基本的な方法です。コールドチャンバーダイカストでは、手動または自動注湯装置によって溶融金属をプレスチャンバーに注湯し、射出パンチを前進させて油圧で金属をキャビティに圧入します。ホットチャンバーダイカストプロセスでは、加圧チャンバーはルツボに対して垂直であり、溶湯は加圧チャンバーの供給ポートから自動的に加圧チャンバーに流入する。射出パンチが下方に移動し、溶湯をグースネックからキャビティ内に押し込む。溶湯が凝固した後、ダイカスト金型を開き、鋳物を取り出してダイカスト成形の全工程を完了する。
リブ厚とダイカスト肉厚の関係(mm)
アルミ合金ダイカストの設計ポイント
ダイカスト設計の合理性はダイカスト成形の全工程に関係する。ダイカスト部品を設計する場合、ダイカスト部品の構造特性やダイカストの工程条件を十分に考慮し、ダイカスト成形工程で設計したダイカスト部品の欠陥を最小限に抑える必要があります。最適な設計計画により、ダイカスト部品の品質は最大限に向上します。
Min.ダイカスト傾斜
2.1 ダイカストの肉厚設計の合理性
アルミニウム合金のダイカスト構造を設計する際には、肉厚を十分に考慮する必要があります。肉厚はダイカストプロセスにおいて特別に重要な要素です。肉厚は、充填時間の計算や内部ゲート速度の選択など、プロセス全体の仕様と密接な関係があります。凝固時間の計算、金型温度勾配の分析、圧力の影響(最終比圧)、金型保持時間の長さ、鋳物の排出温度と作業効率のレベル;設計肉厚が厚すぎると、引け巣、砂穴、気孔が発生し、内部粒子が粗いなどの外面欠陥が発生し、機械的特性が低下し、部品の品質が向上し、コストが増加する;設計肉厚が薄すぎると、アルミニウム液の充填が悪く、成形が難しく、アルミニウム合金の溶解が悪く、鋳物の表面への充填が難しくなる。気孔が増加すると、ダイカストの内部気孔、収縮などの欠陥が増加する。従って、鋳物の十分な強度と剛性を確保することを前提に、鋳物壁の厚さを最小にし、断面の厚さを均一に保つ必要がある。
2.2 ダイカスト用補強リブの合理的設計
大面積や薄肉のダイカスト部品は、強度や剛性が低く、変形しやすい。この時、補強材を使用することで、ダイカストの収縮や破断を効果的に防ぎ、変形をなくし、ダイカストの強度と剛性を高めることができます。プラットフォームのような構造物では、補強リブを使用して応力分布を改善し、ルート破壊を防ぐことができます。同時に、補強リブは溶湯の流れを助け、鋳物の充填性能を向上させます。補強リブの根元の厚さは肉厚を超えないようにし、一般的には0.8~2.補強材の抜き勾配は一般に1°~3°に設計され、高さが高いほど抜き勾配は小さくなる。リブの付け根にフィレットを付けるのは、部品の断面が急激に変化するのを避けると同時に、溶湯の流れを助け、部品の応力集中を緩和し、部品の強度を高めるためである。フィレットは一般に肉厚に近く、リブの高さは一般に肉厚の5を超えない。補強材の厚さは一般的に均一であることが要求されます。薄すぎると補強材自体が破断しやすくなり、厚すぎると凹みや気孔などの欠陥が発生しやすくなる。表1にリブの厚さとダイカストの肉厚の関係を示します。
2.3 ダイカストの角度の合理的な設計
ダイカスト傾斜の役割は、鋳物と金型キャビティ間の摩擦を減らし、鋳物を取り出しやすくすること、ダイカスト表面にひずみが生じないようにすること、金型の寿命を延ばすことです。金型の傾きは、ダイカストの高さに関係する。高さが大きいほど、ダイの傾きは小さくなります。通常の場合、ダイカスト部品の外面の出口角度は、内側のキャビティの出口角度の約1/2であるが、実際の設計では、肉厚を維持するために、ダイカスト部品の内面と外面を同じに設計することができる。均一化、構造設計の簡略化。例えば、表2は各種合金ダイカストの最小抜き勾配角度の参考値であり、表3は各ダイカストキャビティの抜き勾配角度と深さの関係を示したものである。
キャビティの傾斜と金型の深さの関係
2.4 加工代の合理的な設計
ダイカスト部品を設計する場合、機械加工はできるだけ避けるべきである。機械加工は部品表面の緻密な層を破壊し、部品の機械的特性に影響を与え、ダイカスト部品の内部気孔を露出させ、表面品質に影響を与え、部品のコストを増加させる。ダイカスト部品の機械加工を避けることができない場合、切削量が大きい設計はできるだけ避け、機械加工ができるだけ容易な構造設計にするか、加工面積を小さくして加工コストを下げる必要がある。
ダイカスト部品の上部は高い寸法精度が要求されたり、平面粗さの要求が高く、ダイカスト加工では対応しにくい部分がある。この場合、後加工が必要となる。この部分の構造については、設計時に加工代をできるだけ確保する必要がある。ダイカスト部品の表面強度、硬度は内部より高い。加工時の表面密度の維持に注意し、加工代は過大にならないようにする。過度の加工は気孔や外面欠陥の原因となります。表4は機械加工プラス余裕の参考値です。
2.5 アルミニウム合金ダイカストの溶射設計
ダイカスト部品の表面溶射設計は、一般的に粉体溶射プロセスを採用しており、その原理は静電溶射である:塗料は主に電極によって分極され、次に溶射される対象物は反対の電荷で帯電され、粉体は電界力の作用下で対象物の表面に均一に付着する。.粉体噴霧プロセスの特徴:粉体静電噴霧は大気汚染を引き起こさない、粉体はリサイクル可能で材料消費コストを削減できる、塗膜は耐酸性、耐アルカリ性、耐食性に優れている。