加工効率を向上させる場合、切削の三要素(切削速度、切削深さ、送り速度)を向上させることが最も単純で直接的な方法であることは誰もが知っている。しかし、工具の切削三要素の改善は、一般的に既存の工作機械の設計条件によって制限される。そのため、最も安価な方法は、良い工具材料を選択することである。
カッティングの3要素の決定ルール
ナイフの深さ、送り量、直線切断速度を決める。
切削深さ:一般的に加工代に応じて決定される;
送り速度:荒加工の送り速度は工作機械のパワーによって決まり、仕上げ加工の送り速度は表面粗さによって決まる;
切削速度:工具の材質と工作機械の主軸回転数によって決まる。
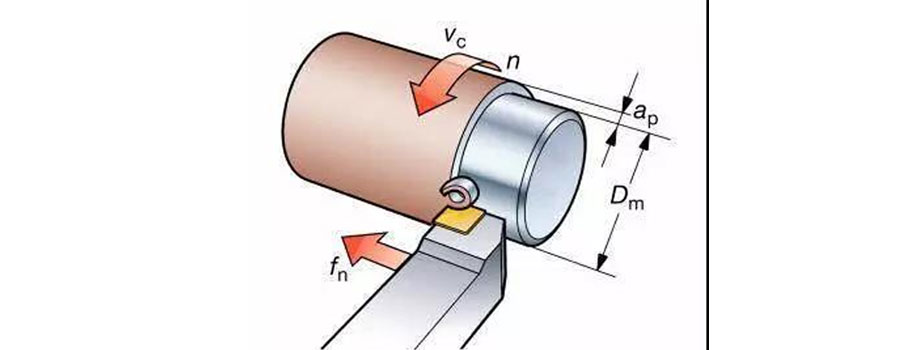
CNC加工の効率向上の観点から、切込み深さを大きくすることは、おそらく検討に値する方法であろう。その重要な理由の一つは、切削深さが送りの10倍と等しくなれば、切削深さを増やしても工具耐久性への影響はほとんどないことが実験で示されているからである。切削速度を上げる場合、切削速度を変えると工具の耐久性はほぼ2倍の速度で変化し、送りを変えると工具の耐久性もほぼ同じに変化する。従って、量産形態のブランクで、いわゆる「ネットサイズ」が実現できない場合、切込み深さを大きくすることは、工具コストの大幅な上昇を招くことなく、高能率な生産サイクルを実現できる選択である。
ツール選択
超硬工具は、現在の工具市場で主流の工具である。誰もが知っている工具です。超硬工具の3つの切削要素を実際の加工現場の状況に応じて調整することで、工具寿命と加工効率を最大限に高めることができる。しかし、立方晶窒素 ホウ素系工具の開発はそれほど長くなく、触ったことのない人も多い。しかし、硬い材料や難削材の出現に伴い、立方晶窒化ホウ素工具は徐々に皆の視野に入ってきた。しかし多くの人は、立方晶窒化ホウ素工具は高速切削加工や仕上げ加工に限定されると考えがちだ。
実際、超硬工具業界の継続的なRandDと革新に伴い、立方晶窒化ホウ素工具は粗加工工程と断続切削条件で広く使用されている。立方晶窒化ホウ素工具の選択は超硬工具と同じである。異なる被削材に応じて、異なる工具材種と工具構造を選択する。
複合溶接立方晶窒化ホウ素ブレードは、一般的に仕上げ加工に使用されます。刃先部分は立方晶窒化ホウ素材のみで、母材は超硬母材です。刃物の深さは0.5mm以内に制御されるため、仕上げ加工にのみ使用でき、大きなマージンや不規則な表面を持つものには、一体型の立方晶窒化ホウ素刃を選択する。本体全体が立方晶窒化ホウ素製。切削深さは1~10mmで、工具寿命は一般的に3時間/刃先。
立方晶窒化ホウ素工具の研究の進歩と実際の加工ニーズに伴い、本来の高速仕上げは断続仕上げ、粗仕上げ、半仕上げへと発展し、通常の工作機械でも使用できるようになりました。
さらに読む
立方晶窒化ホウ素工具と超硬工具の加工範囲は重複している。例えば、ねずみ鋳鉄、超硬工具、立方晶窒化ホウ素工具はすべて加工できます。企業のニーズに応じて、より経済的で費用対効果の高い工具材料である超硬合金を選択することができます。超硬工具の最大線速度は350m/minですが、立方晶窒化ホウ素工具は1500m/minです。同時に、立方晶窒化ホウ素工具の耐久性は普通の超硬工具の30~50倍である。層状超硬工具の寿命の5~15倍。
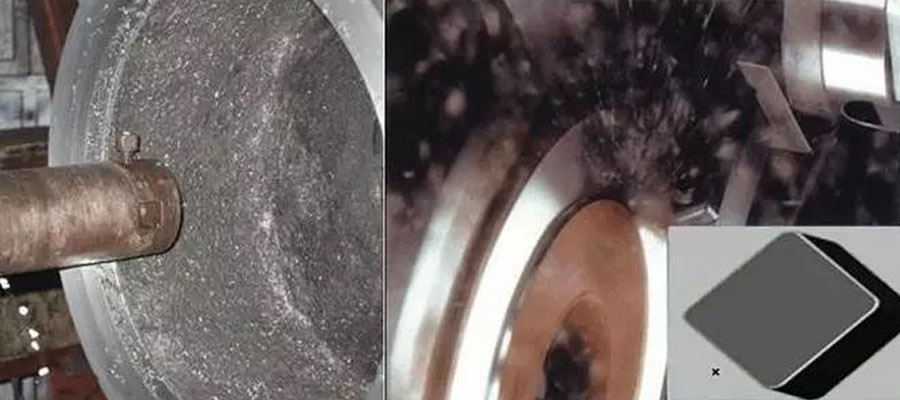
しかし、企業はねずみ鋳鉄を加工するために、やみくもに立方晶窒化ホウ素工具を選択しない。結局、立方晶窒化ホウ素工具の価格は超硬工具より高い。そのため、大量生産と高い加工効率が要求される場合に選択することをお勧めします。立方晶窒化ホウ素切削工具の場合、加工効率が高くなく、仕事が少ない場合は、超硬切削工具を選択する方が経済的で費用対効果が高い。