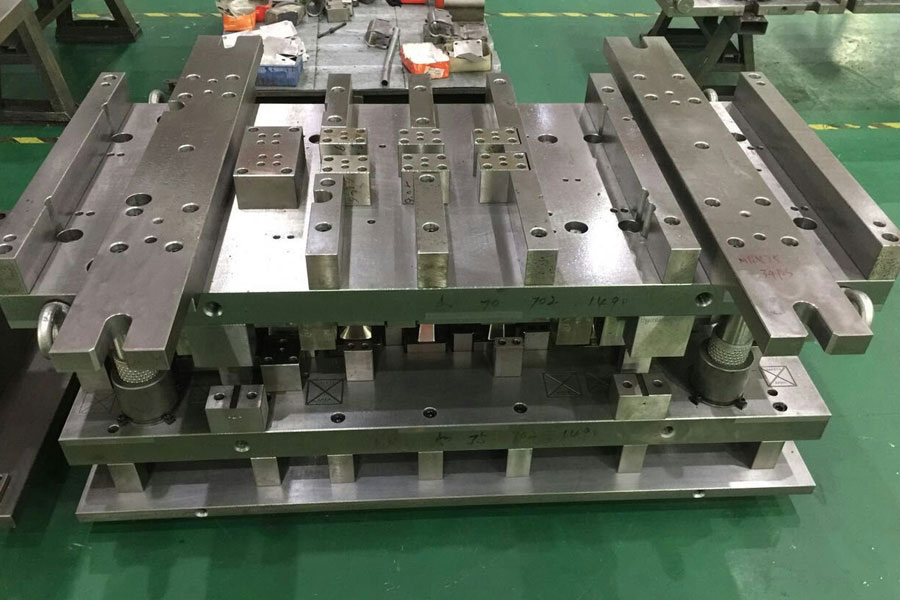
スタンピング加工は、技術と経済の面で多くのユニークな利点を持っています。主な利点は、高い生産効率、便利な操作、機械化と自動化の容易な実現です。
ダイカスト鋳造とは、金型鍛造の鋳造方法である。ダイカスト金型鍛造工程は、ダイカスト金型鍛造機で行う専用工程である。プレス室に融合金液を注入し、高速で鋼型の空洞に充填する方法である。そして合金液を加圧凝固させて鋳造する方法です;
ダイカストの基本プロセスは、まず溶融金属を金型のキャビティに低速または高速で充填することである。金型には可動式のキャビティ面がある。溶湯の冷却過程で加圧鍛造され、ブランクの収縮をなくす。また、収縮欠陥は、鍛造状態でブランクの内部構造を破砕粒に到達させ、ブランクの総合的な機械的特性は著しく改善されている。また、この工程で製造された粗材は、表面粗さ7(Ra1.6)であり、冷間押出や機械加工で製造された表面と同様で、金属光沢がある。そこで、ダイカスト金型鍛造法を "究極の成形法 "と呼んでいる。
ダイカスト部品とスタンピングの違い
いずれも金属加工技術だが、両者には大きな違いがある:
金属プレス加工とは、パンチや金型を使ってステンレス、鉄、アルミニウム、銅などの板材を変形させたり、割ったりして、一定の形状や大きさに仕上げる加工である。
ダイカストは一種の圧力鋳造部品である。鋳造用金型を備えた機械式ダイカストマシンを使い、加熱した銅、亜鉛、アルミニウム、アルミニウム合金の液体をダイカストマシンの注入口に注ぎ、ダイカストマシンを通過させます。ダイカストとは、金型によって制限された形状や大きさの銅、亜鉛、アルミニウム部品やアルミニウム合金部品を鋳造することです。このような部品は通常ダイカスト部品と呼ばれます。
ダイカストとスタンピングは、どちらも部品の加工・成形方法だが、ダイカストは金型に圧力をかけて液体金属を充填し、金型と同じ部品を得る方法であり、スタンピングは金型の機能を利用して固体金属の一部を除去し、必要な部品を得る方法である。
ダイカスト金型とスタンピング金型の違い
スタンピングはコールドスタンピングとホットスタンピングに分けられる。コールドスタンピングに比べ、ホットスタンピングプロセスは軽量化と衝突安全性、高強度スタンピング部品のスプリングバックと金型摩耗の問題を効果的に考慮することができます。ホットスタンピングは、成形金型によって実現されます。金型の設計が合理的であるかどうかは、ホットスタンピングの効率に直接影響します。
ホットスタンピング金型の設計と製造方法は、主に穴あけ型、積層型、シャワー型、鋳造型の4種類に分けられる。
1.ドリリングタイプ
穴あけタイプは、凹凸のある模型面の下で、パイプを最大限以下のように配置することで、インサート冷却システムの配置を実現している。加工が容易で、金型の交換が容易であり、汎用性が高いという利点がある;
欠点は、形状加工に追従できないこと、金型冷却の均一性が悪いことである。
2.階層的
レイヤータイプは、冷却パイプを界面として、金型表面などを層状に設計・加工する。適合性がよく、熱交換面積が大きく、密閉が簡単という利点がある;
欠点は、高精度の加工装置が必要なこと、冷却パイプラインが複雑なこと、伝熱性能が低いことである。
3.シャワータイプ
シャワー式は、金型表面に小さな穴をいくつも開け、その穴にノズルを配置する。金型を閉じた後、ノズルを使って高圧のクーラントを高温の鋼板にミスト状に噴射し、焼き入れと冷却を行う。冷却効果がよく、加工材料の相変化が十分で、部品の機械的特性が優れているという利点がある;
欠点は、加工が難しいことと、金型に残留した水滴が金型表面に深刻なダメージを与え、金型の寿命を縮めることである。
4.鋳造タイプ
溶融鋳造型は、固定された冷却パイプを通して砂型に全体があらかじめ埋め込まれ、鋳造によって鋳型ブランクが得られ、機械加工後に一体化された鋳型が得られる。冷却パイプの配置が自由で、適合性がよく、パイプの密閉が簡単で信頼でき、加工が容易であるという利点がある;
欠点は、鋳型の強度が低いこと、溶解と鋳造の工程が複雑であること、パイプと基板との冶金的な組み合わせが必要であること、位置精度が高いこと、部分的な鋳型の修復が難しいことである。
4つのホットスタンピング金型の設計と製造方法の中で、穴あけ型と積層型が最も広く使用されている。