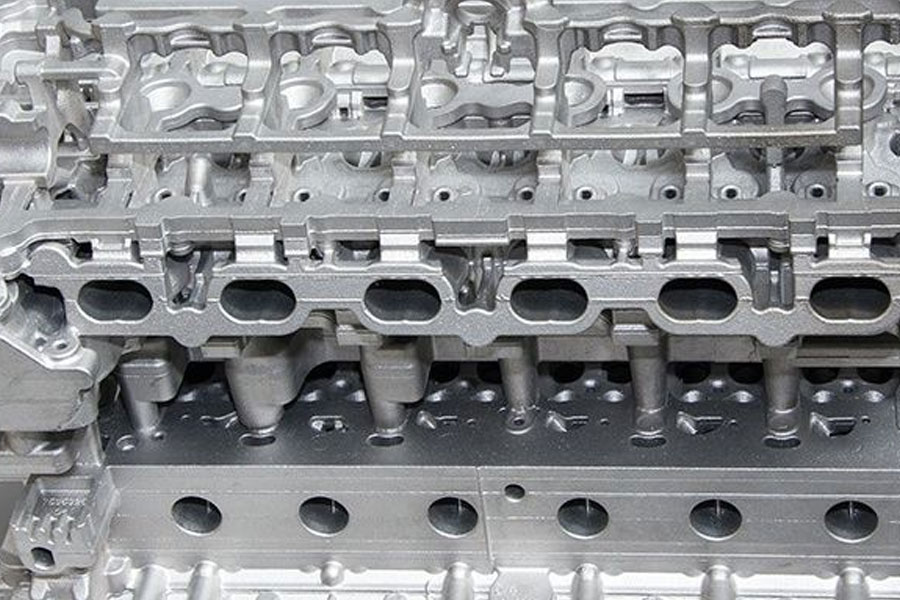
自動車鋳物の統合設計
自動車の省エネ、環境保護、生産コスト削減の要求が高まる中、鋳造の利点を生かし、プレス、溶接、鍛造、鋳造で形成される複数の部品を合理的に設計し、構造最適化することで、一体化した部品の鋳造を実現する。成形により、効果的に部品を軽量化し、不要な加工工程を削減することで、軽量で高性能な部品を実現します。
一般的な鋳造一体型アクスルハウジングの主な形態は、シームレス鋼管をハーフアクスルスリーブとしてアクスルハウジングの両端に圧入し、ピンで固定してアクスルハウジングアセンブリを形成するものである。第一汽車グループは、アクスルハウジングの強度と剛性をさらに向上させ、工程を簡略化するため、アクスルスリーブ(図1のアクスルハウジング両側の部品)をアクスルハウジングに直接鋳造する一体型アクスルハウジングを開発した。加工が難しく、コストダウンが多く、アクスルハウジングの構造が単純になりがちで、アクスルハウジングの剛性が向上し、複雑で理想的な形状にすることができ、肉厚を変更することができ、理想的な応力分布を得ることができ、その強度と剛性の両方が大きく、確実に動作します。アクスルスリーブの統合により、鋳物のサイズが大幅に増加している。鋳物の長さは2 258 mmで、単体重量は200 kgを超えます。この一体化鋳物の特性を踏まえ、同社では専用の生産ラインを設けて生産を確保している。
自動車鋳物の一体化の発展傾向は、非鉄合金鋳物の発展においてより顕著である。複雑な構造の鋳物を生産できる鋳造プロセスの特性を生かすため、ドアインナーパネル、シートフレーム、インストルメントパネルフレーム、フロントエンドフレーム、ファイヤーウォールなどの高圧鋳物の一体化設計が登場している。寸法は現在生産されているものよりかなり大きい。鋳物の場合、生産には4,000トンから5,000トン、あるいはそれ以上のトン数のダイカストマシンが必要になる。
自動車鋳物の軽量化
クルマの強度と安全性を確保することを前提に、クルマの縁石重量を可能な限り減らして軽量化を図り、クルマの動力性能の向上、燃費の低減、排気ガスの公害低減を図る。車両の縁石重量を100kg減らすごとに、100kmあたりの燃料消費量を0.3~0.6L減らすことができ、車両重量を10%減らすと、燃費を6~8%向上させることができる。環境保護と省エネの必要性に伴い、自動車の軽量化は世界の自動車発展のトレンドとなり、自動車鋳物の軽量化も自動車鋳物の重要な発展方向の一つとなっている。
自動車鋳物の軽量設計
鋳物の総合的な安全係数の必要性から、等厚設計は自動車鋳物の主な設計方法の一つである。しかし、等厚設計の主な欠点は、構造性能を十分に生かすことができず、鋳物の重量が増加することである。CAE解析、トポロジー最適化などの手法を用いて、各部品の応力値が近くなるように、つまり各部品の肉厚が一定にならないように、力の小さい部品は薄くしたり、不要な部品は軽量化するように設計を最適化する。鋳物成形は複雑な構造の鋳物の成形が実現できることを考えると、様々な異形断面が実現できる。設計の際には、CAEやトポロジー最適化を用いて部品の応力解析を行う。その応力分布から、部品の形状や具体的な部品の材料厚を決定する。鋳物を補強し、穴を掘り、厚くすることで、部品の重量を大幅に減らすことができる。
軽合金自動車鋳物
現在、各国の自動車メーカーが採用している軽量化対策の中心は、アルミニウムやマグネシウムなどの軽合金材料の使用である。アルミニウムは密度が鉄の1/3と小さく、耐食性、延性に優れている。マグネシウムは密度がアルミニウムの2/3と低く、高圧鋳造条件下での流動性に優れている。アルミニウムとマグネシウムの比強度(質量に対する強度の比)はかなり高く、自重の軽減と燃費の向上に決定的な役割を果たしている。過去2年間における米国自動車産業の競争力向上は、アルミニウム・マグネシウム構造鋳物および一体鋳造の大規模な採用と密接に関係している。
ドイツのBMW社が発売した新型5シリーズには、最新世代のマグネシウム・アルミニウム複合直列6気筒エンジンブロックが搭載され、前世代に比べて10kgの軽量化が図られ、性能と燃費が大幅に向上している。ただし、アルミニウムやマグネシウムなどの軽合金の原料価格は鉄鋼材料よりもはるかに高いため、自動車産業での幅広い応用には限界があることに留意する必要がある。しかし、原材料の価格が比較的高いにもかかわらず、現在の自転車用マグネシウム鋳物とアルミニウム鋳物の消費量は年々増加している。一方では、技術の進歩がコストの上昇を補ってきた。他方、市場競争により自動車メーカーは利益を減らし、より軽合金を採用せざるを得なくなっている。しかし、軽合金の量を大幅に増やし、マグネシウムとアルミニウムの地金の購入価格を下げるためには、高度な成形技術の開発がカギのひとつとなる。
自動車用鋳造材料の高性能化
材料の性能を向上させ、部品の単位重量がより高い荷重に耐えられるようにすることは、鋳物の重量を効果的に減らす方法の一つである。ブラケット型構造鋳物は、自動車鋳物に占める割合が大きいため、その開発が注目されている。熱処理などを通じて材料の組織を変化させ、部品の強度や剛性、靭性を向上させることで、効果的に部品の軽量化を図ることができる。
オーステンパーダクタイル鋳鉄は、通常の鋳鋼材料よりも強度が高いだけでなく、鋼よりも密度が低い。鋳鋼の密度が7.8g/cm3であるのに対し、オーステンパーダクタイル鋳鉄の密度は7.1g/cm3であり、近年広く推奨されている材料である。オーステンパーダクタイル鋳鉄を採用し、同じ大きさの鋳物で鋼鉄鋳物より10%軽い。東風汽車有限公司では、鋼鋳物に代えてオーステンパーダクタイル鋳鉄を用いたある種の商用車の軽量化検証を実施した。オーステンパ・ダクタイル鋳鉄部品の高い強度特性を考慮し、専門家フォーラムでは14のサスペンション部品が再設計された。一般的に、自動車鋳物の材料置換は、部品の軽量設計に付随して行われることが多い。
アルミニウム合金やマグネシウム合金の鋳物では、代わりに高強度・高靭性の材料が使用される。本来の軽合金の軽量化をベースに、さらに軽量化するために高性能な材料を使用する。米国のゼネラル・モーターズは、高性能AE44合金を代わりに使用している。オリジナルのアルミ合金は、サブフレームの製造に高圧鋳造を使用し、アルミ合金の重量をさらに6kg軽量化している。
自動車鋳物開発のデジタル化
自動車鋳物開発とデジタル技術の総合的な組み合わせは、鋳物技術のレベルを大幅に向上させ、製品設計と試作サイクルを短縮することができる。現在、デジタル製造技術は自動車鋳物の開発に広く使われている。鋳造構造設計と鋳造工程設計の段階では、Pro/E、CATIA、UGなどの3D設計ソフトウェアが広く使われており、一部の先進的な鋳造企業はペーパーレス設計を実現している。MAGMA、ProCAST、Huazhu CAEなどのソフトウェアは、自動車鋳物の凝固プロセス、微細構造、成分偏析、材料特性のシミュレーションに広く使用されています。また、鋳造プロセスにおける速度場、濃度場、温度場、相の解析も可能です。場、応力場などのシミュレーションが可能です。これにより、量産前に工程計画を最適化することができます。
自動車鋳物の迅速な開発ニーズに対応するため、CAD/CAEの設計・開発をベースに、自動車鋳物の迅速な試作にRP(ラピッドプロトタイピング技術)が広く利用されている。CAD/CAEの元データを取得した後、レイヤーバイレイヤー方式を採用し、鋳物の原型、または鋳物を成形するために必要な金型の原型を、接着、焼結、焼結によって得る。前者はインベストメント鋳造や石膏鋳造などで鋳物サンプルを試作し、後者はそのまま鋳型として砂中子を製造し、中子組立造形で鋳物を流し込むことができる。また、粉末レーザ焼結法(SLS)を用いれば、砂中子と砂型を直接完成させることができ、鋳物の試作に必要な砂型を得ることができる。また、比較的簡単な構造の外型については、CNC工作機械を使用して、機械加工可能なプラスチックでCAM加工を行い、鋳物の試作に必要な中子箱とパターンを得ることもでき、砂塊を直接加工して外型の砂型を直接得ることもできる。
一般的に言えば、デジタル技術は鋳物の設計、開発、試作のすべての側面に浸透しており、鋳物開発のスピードと効率を効果的に向上させている。現在の主な問題は、設計、解析、迅速製造のデジタル技術が互いに独立していることである。開発プロセスがある段階から別の段階に移行する際には、かなり面倒なデータ変換作業も必要となる。将来的には、鋳物開発のあらゆる側面に適用されるデジタル技術のための統一されたデータインタフェースプラットフォームを開発し、標準化されたデータ変換標準を確立して、異なるソフトウェア間のシームレスなデータ変換を実現し、鋳物の開発速度をさらに向上させることが期待される。
薄肉複雑構造鋳物の製造技術
自動車産業の発展と省エネ・排ガス低減の要求により、自動車部品の軽量化が進んでいる。薄肉設計を通じて、軽量化はエンジンブロックの重要な発展方向である。一汽フォルクスワーゲンの鋳鉄製シリンダーブロック生産の一汽鋳造有限公司を例にとってみよう。初期に生産された06Aシリンダーブロックの肉厚は4.5mm±1.5mmで、EA111シリンダーブロックの肉厚は4mm±1mmである。現在量産されているEA888Evo2シリンダーブロックの肉厚は4mm±1mmである。3.5mm±0.8mm、次世代EA888Gen.3シリンダーブロックの製品構造はより複雑で、その肉厚はわずか3mm±0.5mmで、現在最も薄いねずみ鋳鉄シリンダーブロックである。大量生産では、中子破損、中子浮き、肉厚変動が大きいなどの問題があるが、砂中子と成形砂の品質を管理することで、広く使用されている水平注湯プロセスでもEA888Evo2シリンダーの生産要件を満たすことができる。しかし、EA888Gen.3シリンダーブロックの生産要件を満たすことができないため、全中子アセンブリ垂直鋳造プロセスを採用する必要があります。
大型アルミ・マグネシウム合金構造部品の製造技術
省エネ、環境保護、部品コスト削減の要求が高まる中、アルミ・マグネシウム合金大型構造鋳物は重要な発展傾向となっており、その製造技術も現在の発展焦点となっている。現在、アルミニウムマグネシウム合金大型構造部品の主な生産技術には、高圧鋳造、スクイズ鋳造、低圧鋳造などがある。高圧鋳造は生産効率が高く、製品品質も良いため、現在の主な生産工程となっている。その製造技術の開発は、主に高圧鋳造工程中のガスの巻き込みやすさと、鋳物内部に気孔が形成されることに焦点が当てられており、熱処理の問題を改善することができない。
ドイツFulai社は真空負圧吸引鋳造プロセスを開発し、ダイカストプロセス全体が高真空(30mbar以下)下で行われる。溶湯は真空状態で金型、加圧室、吸引管を通過し、酸化することなく吸引管によって炉から吸引され、離型剤の蒸気も真空システムによって排出される。上記真空負圧吸引鋳造プロセスの主な特徴は、定量注湯開始時、システム全体が高真空状態にあること、定量注湯プロセスにおいて、キャビティ内のガスと溶湯を効果的に排出できること、注湯プロセス中、金属溶湯の酸化がないこと、注湯プロセス中の熱損失がなく、より低い注湯温度で注湯できること、リアルタイム監視下で無撹乱層流注湯を実施できることである。上記のプロセスは、Auto Expert Forumの自動車構造鋳物の量産に成功し、高品質の軽合金鋳物の応用に先進的な成形方法とプロセスを提供している。
スイスのビュラー社は、構造用鋳物の生産用に二重回路の真空システムを開発した。この生産技術は構造生産技術と呼ばれている。構造物生産技術を使用すると、真空引きの速度を上げることができ、それによって安定した生産条件が得られ、ダイカスト鋳造品の品質が大幅に向上する。図5に示すように、2回路真空システムにおける1回路の空気抜き口は、圧力室の上端に配置され、主に圧力室内の空気を抜くために使用される。射出プランジャーが前進して注出口を封止するときに始動し、プランジャーが吸引口を封止しようとするときに閉じる。もう一方の回路設定は従来の真空プロセスと同じで、主にキャビティ内の空気を抜くために使用される。現在、この技術は乗用車のアルミ合金一体型衝撃吸収タワー、ドアインナーパネル、ボディレールの製造に応用され、成功を収めている。
鋳物の精密鋳造成形技術
一般的に自動車鋳物の精密鋳造と呼ばれるものは、主にロストフォームとインベストメント鋳造技術を指します。自動車鋳物成形技術の発展に伴い、鋳物精密成形は鋳物成形法の一種である。このような成形方法で製造された鋳物は、切削加工なし、または切削加工を少なくしてそのまま使用することができます。鋳物の寸法精度に対する要求が高まるにつれて、精密鋳造技術は近年急速に発展し、精密砂型鋳造法、ロストフォーム鋳造法、制御圧力鋳造法、圧力鋳造法などの一連の新しい鋳造法が出現した。コスワース鋳造法は英国で開発された鋳造法で、ジルコニウム砂中子集合体と電磁ポンプを用いて注湯を制御する。アルミ合金のシリンダーブロックの量産に成功し、ポンプ注湯のような電磁プロセスの代わりに低圧注湯を用いるなど、多くのプロセスバリエーションが登場している。この鋳造法では肉厚3.5~4.0mmのアルミ合金シリンダーが製造可能で、現在の精密砂型鋳造の代表的な工程となっている。
ロストフォーム鋳造法は1965年に発明され、生産される主な自動車鋳物はシリンダーブロック、シリンダーヘッド、吸排気管などであり、大規模な生産を形成している。20世紀の1990年代にロストフォーム鋳造技術が導入されて以来、我が国は形を整え始め、伝統的な鋳造業を変革する最も広く使われているハイテク・新技術として国家に推進されている。現在、わが国の投資精密鋳造プロセスには、珪酸ソーダシェル、複合シェル、シリカゾルシェルという3つがある。その中で、自動車製品のシリカゾルシェル製造に使用される鋳物の表面品質はRa 1.6μmに達することができ、寸法精度はCT4.等級、最小肉厚は0.5~1.5mmに達することができます。東風汽車精密鋳造有限公司は、シリカゾル+水ガラス複合シェル製造プロセスを採用し、複雑な構造の一体化鋳物を生産し、生産コストを大幅に削減します。インベストメント鋳造技術鋳造プロセスの発展傾向は、鋳造品がますます最終製品に近づき、製品の複雑性と品質がますます高くなっている。CAD、CAM、CAEの応用は製品開発の主要技術になり、専門的な協力が現れ始めた。
真空鋳造、酸素充填ダイカスト、半凝固金属レオロジーまたはチキソトロピックダイカスト、および高圧鋳造プロセスを基礎として開発されたその他のプロセス方法は、鋳造欠陥を排除し、内部品質を向上させ、ダイカストの適用範囲を拡大するために設計されています。スクイズ鋳造法では、加圧下で溶湯を充填・凝固させるため、平滑性、金属飛散がない、金属液の酸化ロスが少ない、省エネ、安全操業、鋳巣などの欠陥低減などの利点がある。アルミニウム合金のサブフレームなどに使用される。高性能アルミニウム合金鋳物の開発と応用が広く行われている。
自動車生産台数の継続的な増加により、高品質、優れた性能、正味に近い形状、多品種、低消費、低コストの方向での鋳物生産の発展が急務となっている。なぜなら、完成車の部品の約15%から20%が鋳物だからである。そのため、鋳造業界は様々な新技術や新素材を継続的に適用し、鋳造の全体的なレベルを向上させる必要がある。鋳物の精密鋳造成形技術は自動車鋳物の上述の要求を満たすことができ、その応用は自動車鋳物の異なる鋳造生産工程もカバーする。
Conclusion
ますます厳しくなる環境保護規制に対応するため、自動車は軽量化の方向に進んでいる。車両重量が10%減少するごとに、燃料消費量は5.5%削減でき、燃費は3%から5%向上し、排出ガスは約10%削減できる。自動車鋳物の軽量化を実現するためには、アルミ・マグネシウムなどの非鉄合金鋳物の適用、大型複合構造一体鋳物の開発、鋳造精密成形技術の普及などが挙げられる。従って、現代の自動車産業のニーズを満たすために、デジタル技術の広範な利用を基礎として、高性能鋳造材料と自動化設備の広範な応用による自動車鋳物の研究開発と生産を実現することが求められている。