本稿では、まずアルミニウム合金シェルの構造とダイカストプロセスを分析し、UGソフトウェアを使用してアルミニウム合金シェルのダイカスト金型の設計を完了します。設計されたダイカストは合理的で、鋳造品の表面は滑らかで、きれいで、製品の品質は要求を満たす。
アルミニウム合金製リヤシェルのダイカスト部品の構造とプロセスの解析
ダイカストプロセス・パラメータ設計
2.1 ダイカストマシンの選択 ダイカストマシンを選択する場合、まずクランプ力を決定する必要があります。型締力には二つの機能があり、一つはパーティング面をロックする目的を達成するために背圧のバランスをとるために使用され、もう一つは目標とする寸法精度を達成する目的を達成するために溶湯の飛散を防止するために使用されます。この金型にはサイドコアの引き抜き(ダイカストにはサイドホールやアンダーカットがない)がないため、設計された鋳物には部分的な膨張力はありません。従って、Fロック≧KFメイン=1.25×1288.352=1610.44kNとなる。以上の計算により、クランプ力の値と鋳物の重量が求められる。この2つの主な要因によって、ダイカストマシンが選択され、最終的に選択されたモデルは次のとおりです:横型コールドチャンバーダイカストマシン(2500kN)---J1125型、主なパラメータ:
2.2 ダイカスト圧力 ダイカスト圧力はダイカスト工程における主要なパラメータの一つである。従って、ダイカストプロセス中の液体金属の圧力変化を把握し、ダイカストプロセスの各段階における圧力を合理的に制御することは大きな意義がある:
2.3 ダイカスト速度 ダイカスト速度の選択には、射出速度の選択と充填速度の選択という二つの側面がある。この2つの速度の選択は非常に重要であり、鋳物の内外の品質と輪郭を直接決定する。充填速度を選択する際に考慮すべき要素:
具体的な選択肢
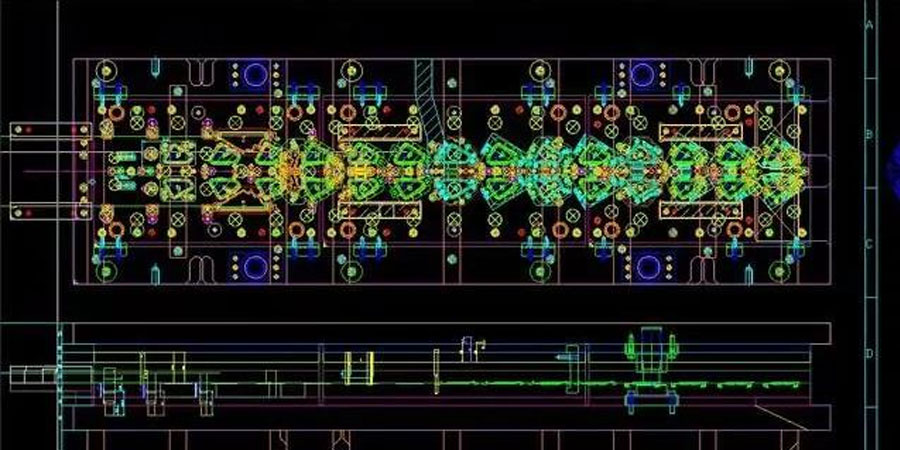
2.4 ダイカスト鋳造時間は、必要な時間のうち、充填時間、保持時間、ダイカスト部品がダイカスト金型内に滞留する時間の3つの部分からなるダイカスト鋳造時間を決定する。圧力、速度、温度、溶湯の特性、さらに鋳造構造(主に肉厚と体積)、金型構造(特にゲートシステムとドレインシステム)など、いくつかの要因が組み合わさってこの結果が得られます。充填時間は0.01~0.2秒が多い。この長さは、鋳物の大きさと構造の複雑さによって決まります。構造が単純で容積が大きい鋳物は、充填時間が比較的長く、構造が複雑で肉厚が小さい鋳物は、充填時間が短くなります。実用的なテストの結果、充填時間は約0.2秒に設定され、これは本論文で設計された中型および小型のアルミニウム合金ダイカストにとって合理的である。保圧時間の機能は:射出パンチが未凝固金属に圧力を加えるのに十分な時間があるので、加圧下で晶析工程を行うことができ、供給が促進され、緻密な組織を得ることに成功する。時間の長さに影響を与える要因:選択した合金の融点、晶析温度範囲、鋳物の肉厚。決定された時間が短すぎる場合、収縮が現れますが、保持時間が長くても大きな影響はありません。1~2sが一般的な保持時間の範囲である。この設計における鋳物の平均肉厚は3mmである。その構造と合金特性を考慮し、保持時間は3sとした。2.5ダイカスト温度 鋳造品の品質を確保するための主な工程パラメータで、溶湯の注湯温度と金型の作動温度である。鋳物の構造、肉厚、充填圧力、速度、合金の種類など、影響を与える要因は多い。ダイカスト温度が適正範囲内で安定し、良好な充填状態が得られるよう、上記のパラメータを総合的に検討する必要がある。注湯温度が合理的な範囲内でなければ、製品の品質は低下し、あるいは不適格となる:
過度の注湯温度は、冷却時に過度の収縮を引き起こし、製品に亀裂が入りやすく、粒が大きくなり、機械的性能が低下する;
注湯温度が低すぎると、コールドバリア、表面模様、注湯不足などの欠陥が発生する。品質の良い鋳物を得るためには、注湯温度、圧力に加え、ダイカスト金型の温度、充填速度、鋳物に選択する合金も同時に考慮する必要があります。ダイカスト部品はアルミニウム-シリコン合金で作られています。その流動性と金型の特性から、ダイカスト温度は620℃が選択される。
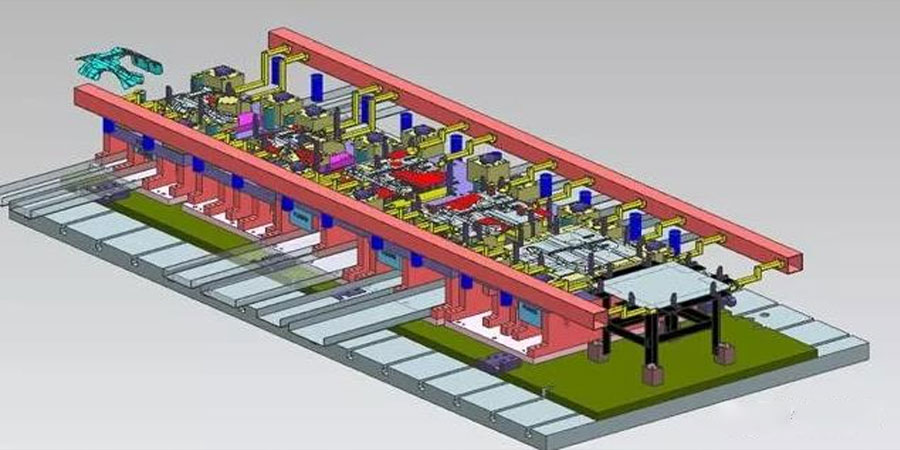
ダイカストの構造設計は背部貝のダイ カストの
3.1 パーティング面の決定 部品は単純な構造をしている。パーティング面選択の原則に従い、図2に示すように、最大の突起部を選択する。
3.2 ゲーティング・システムの設計 ゲーティング・システムは4つの部分で構成されている:
具体的なデザイン:
3.3 オーバーフロータンクと排気システムの設計 オーバーフロータンクの構造設計を行い、諸要因を総合的に勘案して選定した断面形状を台形とした(図4)。合理的な構造は以下の機能を有する:
3.4 排出システムの設計 ダイカストプロセスでは、成形サイクルが完了した後、ダイカスト部品を取り出すためにダイを開く必要があります。この作業を行うには、トップピース機構を1種類追加する必要がある。エジェクターシステムは、金型構造の設計において重要な位置を占めています。エジェクターシステムには主に3つの部品があります:
システム内の制限装置を設計する:
3.5 成形品の大きさの計算
3.5.1 キャビティとコアのサイズ
3.5. 2 中心距離と位置のサイズを計算する:L-成形部品の中心距離と位置の平均サイズ(mm);L-ダイカストの中心距離と位置の平均サイズ(mm)。
3.6 冷却システムの設計は、高品質な鋳造品と長い鋳型寿命を得るために、効率的で制御が容易な鋳型冷却方法-水冷を選択します。水冷の冷却効果は、キャビティ内に配置される冷却水路のレイアウトに依存します:
3.7 ダイカスト金型の全体組立図 バックシェルカバーのダイカスト金型の全体組立図を作成する(図6)。ダイカスト金型は固定金型と可動金型の2つの部分から構成される。固定金型は固定型で、固定金型プレートの上にあります。可動金型はフォロワープレートとともに移動し、フォロワープレート上にある。金型は、可動金型に対する可動金型の移動によって閉じたり開いたりする。
型締め:両者を閉じてキャビティを形成し、ゲートシステムによりキャビティ内に高圧の溶湯を充填する。
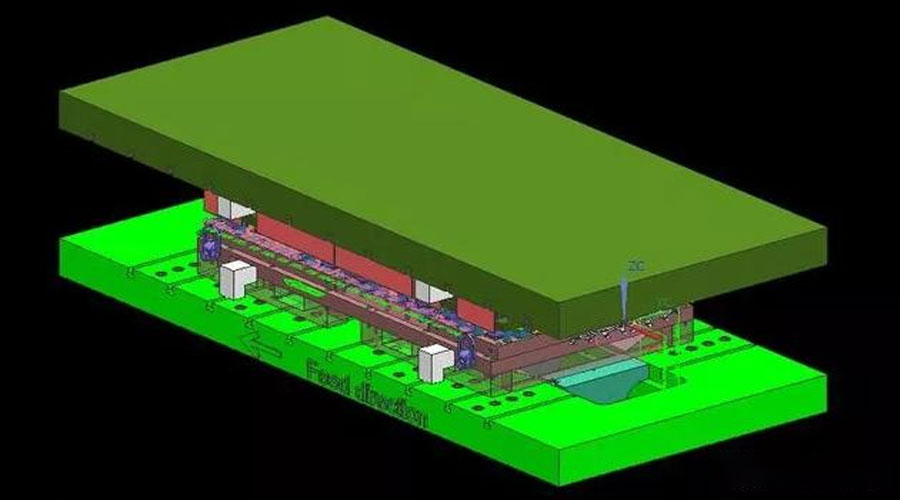
本稿では、UGソフトウェアを使用して裏蓋部品をモデル化し、裏蓋部品のプロセス分析、ダイカストプロセスパラメータおよび金型構造設計を完了します。キャビティは、製造、工程、生産効率などの要因によって制限されます。上記の要因を総合的に考慮し、より合理的な1金型4キャビティレイアウトとして決定した。実際に生産してみると、ダイカスト比圧90MPa、ダイカスト速度20-90m/s、鋳造時間0.2s、保持時間3s、ダイカスト温度620℃の範囲に選択し、得られたリアシェルのスタッフィーカバーは滑らかな表面を持ち、製品の品質要求を満たしている。