鋳造ランナーの損失
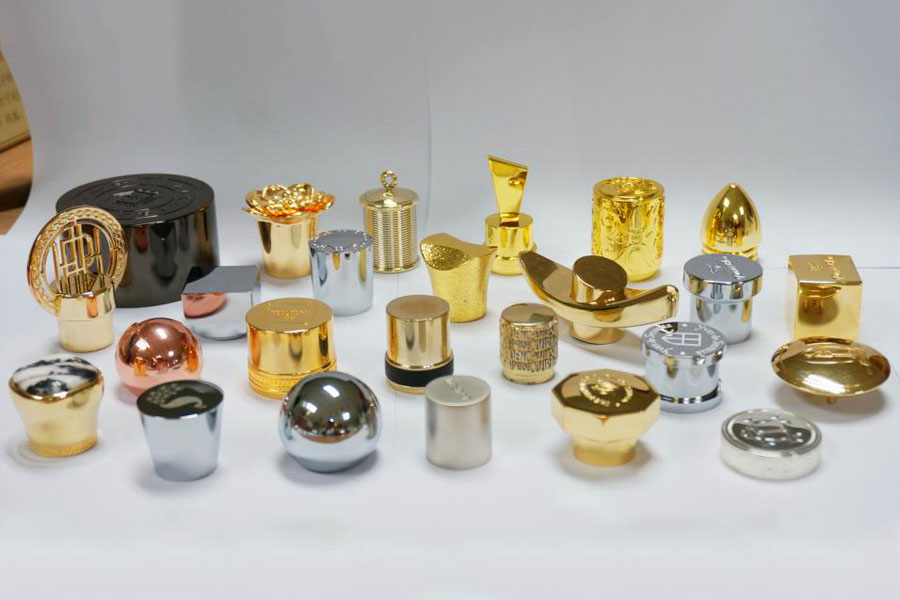
ダイカストを知っている人なら、湯道や残材が鋳物の一部であることを知っているだろう。利益的な価値はありませんが、生産工程上避けることはできません。この部分のコストは、一般的に鋳物のコストに対して一定の割合でしか計算されません。同時に、亜鉛合金のリサイクル性の観点から、最も一般的な現地処理方法は、再溶解のために機械炉にリアルタイムで投げ戻すことです。品質問題を管理する必要性から、中央溶解炉を使用してランナーや廃棄物をリサイクルすることは、徐々に業界に受け入れられている(図1)。スラグについては、大規模なダイカスト工場では独自にリサイクルすることもあり、一般的に残った材料は新しい材料として原料サプライヤーに売却されます。亜鉛材料の現地リサイクル価格は、一般的に新材料の50~70%である。環境条件が良くなければ、スラグの取り扱いは大気汚染を引き起こしやすい。
160トンのホットチャンバーダイカストマシンを例にしてみましょう。毎回少なくとも150グラムのランナー(オーバーフローウェルを除く)を生産し、3シフトと仮定すると、生産サイクルは20秒、機械の稼働率は80%、年間生産量は 口ランナーは190トンに達することができます。もう一つの例:毎回100グラムのランナーを生産する80トンの機械を使用し、同じ仮定で生産サイクルを12秒に変更すると、ランナーの年間生産量は210トンを超える。
ランナーの設計がコストの重要性に影響することがわかる。
さまざまなリサイクル方法
リサイクル方法の中でも、ランナーを直接炉に投げ戻す方法は、最もシンプルでコスト削減につながる。リフロー溶解で作られたばかりの流路は予熱の必要がなく、保管スペースも少なくて済むが、スラグを多く含む溶融材料の品質管理が難しく、炉の温度制御が難しく、合金組成が分からない;さらに重要なことは、新材料の割合やボイラー水の変化を観察するなど、操業スタッフの職人技に頼っていることです。一方、スタッフはオーバーフローした井戸やフラッシュを炉に入れますが、状況を悪化させるだけでなく、廃棄物を直接溶かすこの方法は、廃棄物を隠すことにもなります。不良率が高く、金型設計やダイカストパラメーターが不安定なため、管理者は効果的な改善を行うことができない。この方法は、高い表面品質が要求される鋳物の生産には適しておらず、ランナーロスのコストを正確に計算することは困難である。
中央炉の回収ノズルと不良品は、生産量の多いダイカスト工場で普及しています。その利点は非常に明白で、つまり、リサイクル材料の集中処理により、炉の効率を向上させ、合金の品質を管理することができます。溶湯を中央炉から直接炉に供給すれば、ダイカストマシンの材料温度は安定し、スラグも少なくなる。自動供給制御を装備すれば、液面の変化を最小限に抑えることができます。現在普及している中央溶解炉は、容量の大きい鋳鉄製るつぼ炉、ステンレス製るつぼ炉、連続溶解タイプの非るつぼ炉などに分けられます。亜鉛の液体輸送もいくつかのカテゴリーに分けられます:天井クレーン式液体材料輸送、地上トロリー式(無軌道または軌道式)保持炉(供給装置付き)輸送、炉と中央炉を連結する保持トラフ式重力輸送装置があります。その欠点は、投資額が比較的大きいこと、単一の合金にしか適さないこと(小型るつぼ炉はここでは論じない)、作業場が広い面積を占めるため、小型ダイカスト工場(5台以下)には適さないこと、古い作業場の改造や協力が難しいことである。そのため、一般的には新工場の建設時にのみ再計画される。スプルー材の再溶解に小型るつぼ炉を使用する場合、規模の経済性がないため、中央炉よりもコストが高くなるため、計算の参考にはされない。
溶解コストの計算
中央溶解炉を参考に、ランナーの溶解コストを計算すればよい。80トンまたは160トンのダイカストマシンを5台持っている会社を例にとります。設備の投資額を50万と仮定して、10年間に分けます。毎年約1、000トンのランナー再生材料が処理される(実際の状況は新材料に比例して溶けるはずで、再溶解コストを計算するのは純粋に便利である)。
ゲート材料1キロ当たりの溶解コストは0.93ドルである。以上の5つの機械で計算すると、1000トンのランナーノズルの年間生産量は1000万元近くになる。不良品のリサイクルを含めると、この数字はさらに憂慮すべきものとなる(例えば、平均鋳造重量は100グラム、不良品率は5%、サイクルは12秒、不良品の年間回収量は約53トン)。処理量が多いほど溶解コストは下がるが、環境保護や厳格な品質管理コストはここでは計算に入れていない。ゲートの再溶解コストはかなり憂慮すべきものであり、ダイカスト工場はコストを最小化しなければならないことがわかる。したがって、ゲート重量をいかに減らすかが、コスト抑制の重要なカギとなる。
ランナーコストの計算方法
ノズルの精製コストは、鋳物の製造コストに含める必要があります。最も一般的な方法は、使用する材料に一定の割合を掛ける方法です。例えば、原料価格が10ドル/kgで、ノズルの溶解コストが鋳物の重量の3%であれば、鋳物の材料価格を計算する際に10ドル3セントが使われます。この方法は簡単ですが、コスト計算に狂いが生じ、湯口リサイクルの真のコストが隠されてしまう可能性があります。では、次の例で比較してみましょう:
一定のパーセンテージで計算した場合:
実際の回収コストで計算した場合:
この差は小さく見えるかもしれないが、20秒を生産サイクルとして、機械の稼働率を80%とし、3交代制で、1台の機械が年間1,261,440回生産する。その差は以下の通りである:
固定比率法を使用した場合、鋳造Aと鋳造Bのコストは同じですが、実際には鋳造Bのコストの方が高くなります。この事例から、固定比率法を用いて鋳物Bを計算すると、製造コストが過小評価されるだけでなく、設計者にノズルランナーの軽量化を目的としないよう間接的に促すことにもなり、実費法の適用を促進すべきであることがわかります(下表参照)。
ゲートの重量を減らすために、ショートゲート(ショートノズル)設計を使用し、テンプレートの厚さを減らすのが一般的です。これは、長いマシンノズル(一般的に通常より20mm長い)を使用し、ゲートの重量を減らすために深いキャビティゲート金型設計と組み合わせる。以下は、新しいホットチャンバーダイカストランナー設計です。
ホットチャンバー・ダイカスト・ランナー設計
ダイカストの湯道とは、ノズルから金型キャビティに流れ込む溶湯の通り道のこと。スプルーと湯道から構成される。鋳造品を取り付け、脱型を容易にする必要があるため、スプルには傾斜が必要です。同時に、可動テンプレート上のスプリッター・ブロックはスプルーの厚みを減らすことができます。スプリッター・ブロックに冷却水路を追加することで、金型の熱のバランスを取りやすくし、冷却時間を短縮し、鋳物を引き抜いて排出します。1970年代初頭にオーストラリアのCSIROが行った研究によると、許容できる誤差であれば、ダイカストの場合、亜鉛合金液は以下のように要約できることがわかりました:
液体は非圧縮性流体として振る舞う
流体力学の一般原則に従う
レイノルド数が高いということは、流れが乱流であることを示している。
上記の研究結果によると、溶融金属の理想的な流動状態は次のようになるはずである:
1.ランナー部は円形
円周/面積比が最も小さいため、円形断面管の表面抵抗が最も小さくなり、圧力損失も最も小さくなる。同じ台形断面積に比べ、外周部が20%以上小さくなります。
2.フローパイプはストレート
曲げられたパイプは偏った流れを発生させ、溶融物に気泡を混入させ、圧力損失を引き起こす。特に、曲げ半径/パイプ径の比が1未満の場合、圧力損失が急激に増加する。
3.流路のプロフィールは、液体の流れから見て徐々に縮小する。
パイプのプロファイルが大きくなろうが小さくなろうが、急激な変化は高い圧力損失と渦電流を引き起こす。最良の解決策は、パイプ表面による抵抗損失を補うために、プロファイルを徐々に小さくすることである。