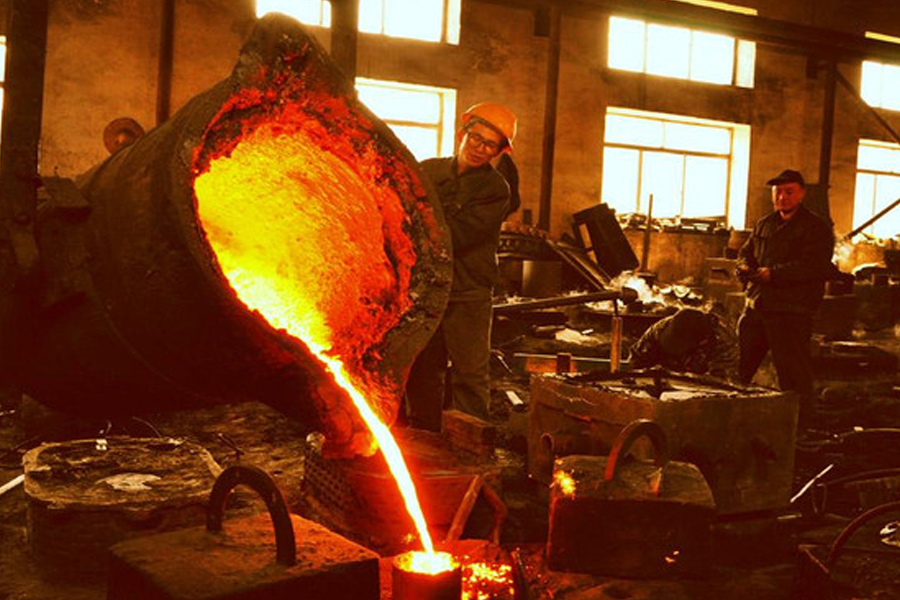
インベストメント鋳造プロセスのコスト構成
全シリカゾルインベストメント鋳造の工程は、ワックスモールド製造、シェル製造、溶解・注湯、後処理の4段階に分けられる。この4段階の検査費用と設備維持費用は補助生産費用に分類される。4つの生産工程のうち、ワックス型製造、製殻、溶解、注湯の3段階におけるコストは、工程の歩留まりと密接な関係がある。鋳造重量で直接計算するよりも、注湯重量で計算する方が正確である。
例えば、ワックスモールドの製造コストを鋳造重量に応じて計算すると、大小の部品間のコスト関係は明らかに実態に即していない。そこで、より合理的な方法として、溶鋼の注湯重量(本稿では注湯重量と呼ぶ)に応じてワックスモールド製造、シェル製造、溶解、注湯工程のコスト(本稿では前段コストと呼ぶ)を算出し、鋳造重量に応じて後処理や補助製造のコスト(本稿では後段コストと呼ぶ)を算出する。溶鋼重量と鋳物重量に応じて算出した製造コストとその構成比を表1に、その分布構造の比率を図1と図2に示す。製殻・製錬段階のコストが工程コストの60%以上を占めていることがわかる。
インベストメント鋳物のコスト差に影響する主な要因
厳密に言えば、各工程における異なる鋳物の製造コストは全く同じではありませんが、いくつかのリンクにおける差は非常に小さく、平均レベルに従って計算することができます。私たちは、鋳造コストに大きな影響を与える要因に注意を払う必要があります。鋳造工程コストの差につながる主な要因は次のとおりである:
1.プロセス歩留まり
歩留まりとも呼ばれる工程歩留まりは、注湯重量に占める実際の鋳物重量の割合です。特定の鋳物では、工程歩留まりは同じツリー内の鋳物総重量の割合に等しくなります。これは鋳造組織とグループプランに関係します。歩留まりは30%から60%の間で変化しますが、一般的には40~50%です。前者のコストと歩留まりの関係は以下の通りです。
鋳物1kg当たりの元原価は、工程歩留まりに反比例する。工程歩留まりが低ければ低いほど、鋳物の単位重量当たりの元原価は高くなり、工程歩留まりが低ければ低いほど、その影響は大きくなります。溶鋼を注湯する第一段階のコストはキログラム当たり6元である。工程歩留まりが45%の場合、1キログラム当たりの鋳造第一段階コストは13.33元、工程歩留まりが30%の場合、鋳造の前段階コストは20元/kgで、平均水準より6.7元高く、工程コストは37.6%増加する。6%.304 ステンレス鋼の鋳造の総費用への影響は約 17% です;プロセス歩留まりが 60% のとき、鋳造の前部費用は平均レベルより 3.3 元低い 10 元/kg であり、プロセス費用は 18% 削減されます。5%.304ステンレス鋼の鋳造の場合、総コストは約7%削減されます;
工程歩留まりが45%の場合、鋳物1キログラム当たりの前払い費用は1ポイント当たり0.3元増加し、工程歩留まりが30%の場合、1ポイント減少するごとに、鋳物1キログラム当たりの前払い費用は約0.67元増加する。
プロセス歩留まりがコストに与える影響は非常に大きいことがわかる。電機の力率と同じで、工程歩留まりを下げることは無効消費電力を増やすことに等しい。もちろん、プロセス歩留まりは高ければ高いほどよく、高ければいいというものではない。工程歩留まりが高すぎると、湯口装置の送給能力が低下し、送給不足と引け巣や引け巣欠陥が発生する。一方、鋳物によっては、特に薄肉鋳物で異形鋳物の場合、鋳造組織やグループ計画の制約から、工程歩留まりを向上させることが困難な場合がある。鋳造価格を決定する際には、この重要な要素を考慮する必要がある。
2.シェル層
鋳物の形状や構造が異なるため、シェル層の数は異なる。例えば、細長い穴やスロットのある鋳物では、2回、あるいは3回面付けする必要があります。一般的に、鋳物では2層の裏打ち層で十分ですが、大きな鋳物では3層以上の裏打ち層が必要になることもあります。鋳物1kgあたりのシェル製造コストは約5.9元で、そのうち67.8%が材料費、23.9%が燃料費と電力費、13.3%が給料である。4元/kgのシェル材料費のうち、ジルコニウム砂とジルコニウム粉末の消費はシェル全体のコストの約63%、42.7%、シリカゾルが12.2%を占める。砂ジルコニウム粉末は表面シェル製造にのみ使用されるが、価格が高いため、シェル製造コストの主要項目となる。
表からわかるように、表面層のコストは裏面層の約4.4倍である。さらに、2つ目の表層に使用される材料は、1つ目の表層に使用される材料よりも多い。10%増加した場合、追加の表層を作るコストは約6.2元となる。鋳物1キロ当たりの平均コストは2.7元増加し、注湯重量1キロ当たりのコストは1.21元増加する。つまり、鋳物1キロ当たりの製殻コストは45.8%増加し、鋳物1キログラム当たりの工程費は15.1%.304ステンレス鋼の場合、総コストと価格への影響は約7%である。鋳物1キロ当たりのコストは0.56元増加し、注湯重量1キロ当たりのコストは0.25元増加した。鋳物1キロ当たりの製殻コストは9.4%増加し、鋳物1キロ当たりの工程コストは3.1%増加し、304鋳物の総コストへの影響は1.4%程度である。
2.後処理の難しさ
鋳造注湯後、シェル破砕、砂洗浄、切断、研削、ショットブラスト、酸洗、整形、補修溶接、補修などの後処理工程を経て初めて、適格な鋳造品が得られる。後処理の平均費用は、鋳物の重量に応じて決定することができる。表1に示すように、鋳物1キロ当たりの後処理の平均費用は3.33元である。
ステンレス鋳物の酸洗コストは約0.3元/kg。炭素鋼の部品は酸洗の必要はないが、注湯後に座ぐりが必要なこと、座ぐり後の砂落としが難しいこと、完成品に防錆が必要なことなどを考慮すると、コスト差は区別できない。
鋳物の構造が異なれば、後処理の工程内容や難易度も異なる。一般的には、鋳造後、シェル破砕、切削、研削、ショットブラストなどの工程でOKですが、工程を増やす必要がある鋳物もあります。顧客が鋳造ブランクに熱処理、表面処理、機械加工などの作業内容を追加することを要求する場合、その費用は別途計上し、合計価格に含める必要があり、本稿の範囲外である。後処理のコスト差は主に砂の洗浄、変形の修正、改修から生じる。そのコストは鋳物の構造と技術的要件に依存する。価格を決定する際には、コスト差を考慮する必要がある。
管理費の配分
企業管理費は、製品工場の販売コストの不可欠な部分であり、重量によって特定の鋳物に配分することができます。見積もりの事前評価では、まず予想損益分岐点生産高または平均生産高を決定し、この生産高に従って鋳物1キログラム当たりの管理費を計算することができる。後評価は、実際の量に従って分配されるべきである。管理費は企業規模と製品構造に関係する。シンプルで安定した製品構造を持つ工場は管理費が低く、品種が多く、技術内容が高い企業は管理費が高くなる。中型金物投資鋳造工場の管理料水準は鋳物1キログラム当たり約5元である。
投資鋳造品の原価計算モデル
1.鋳物1kgあたりの平均製品
上記の方法に従って、異なる工程歩留まりと異なるシェル製造スキームの304ステンレス鋼従来型鋳物の1kg当たりの工程コストと工場コスト(元/kg)を計算します。
2.キャスティングコスト
生産工程における鋳造は、大きさに関係なく、決められた工程に従って1つ1つ行う必要があります。従って、鋳物の実際のコストは重量に完全に比例するわけではなく、特に非常に小さな鋳物の場合、重量によって計算されるコストの偏差は大きくなります。当社では、平均キログラムコストと単価を9:1で加重平均し、鋳造単価を算出しています。次のように表されます。
補助工程費とは、砂の洗浄(サンドドリル、アシッドバイト、サンドブラスト、アルカリブラストなど)、成形などの追加工程の費用を指す。鋳造工程以外の熱処理、表面処理、溶接、機械加工などの費用は別途計算する必要があり、本稿の範囲外である。
鋳物の価格評価
鋳物の原価が明確になれば、鋳物の価格評価は容易である。鋳物の価格評価は、事前評価と事後評価に分けられます。事前評価の目的は見積りであり、事後評価の目的は損益分析である。事前評価には未知の要素がある。標準原価は、過去のデータの統計的分析に基づいて見積もることができる。事後アセスメントでは、様々な経費が判明しており、特定の製品に応じた経費を徴収することができる。費用の配分は、実際の状況とできるだけ一致させるべきである。
鋳物価格評価の基礎となるのは、工場の売上原価に加え、予想される利益、消費税、販売経費などである。式で表すと
鋳造価格=工場販売原価+予定利益+消費税+販売経費
その中でも、期待利益を決定する上で考慮すべき要素は多く、その変動幅も比較的大きく、概ね15%前後である。まとめると、期待利益について考慮すべき主な要因は以下の通りである:
追記本稿の目的は、インベストメント鋳造のコストに影響を与える要因を探り、インベストメント鋳造のコストを科学的に評価することであることを指摘しておく。様々なインベストメント鋳造工場の実際のコスト水準は同じではないため、この記事で引用した統計はあくまで参考である。本稿で採用したコスト収集方法は、従来の工業会計慣行と完全に一致するものではなく、データ収集の際に確認する必要がある。