1 ダイカストの固着の理由
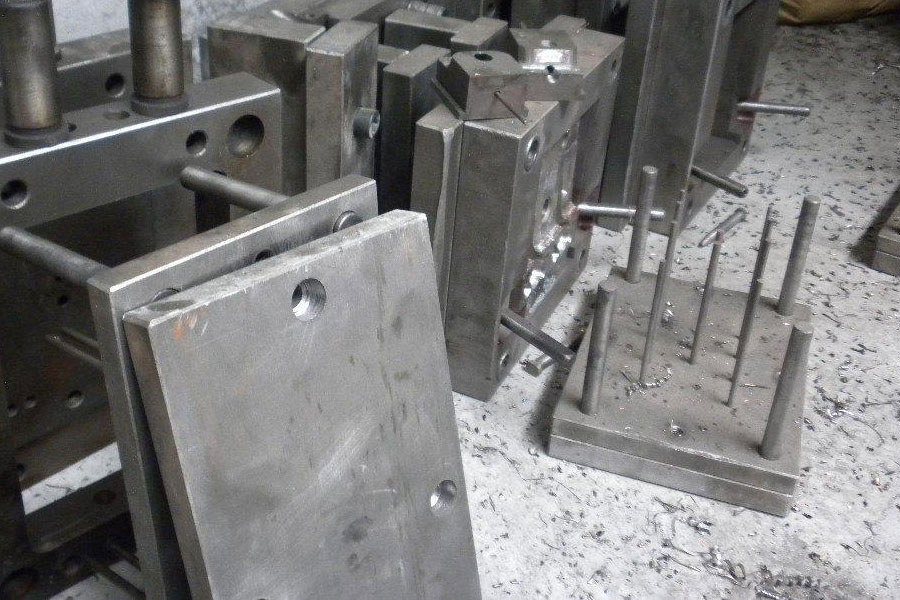
鋳造品に金型欠陥が固着する危険性は、ダイカストが金型に固着すると、軽い表面が粗くなり、外観の粗さに影響する。重い鋳造品の表面は剥がれ、肉が不足し、ひずみ、ひび割れが発生し、鋳造品が漏れることもあり、その結果、バッチで鋳造品がスクラップになる。ダイカストのこびりつきには様々な現象がありますが、基本的なこびりつきの原因は以下の通りです。
1.1 ダイカスト合金とダイス鋼の親和性
ダイカスト合金とダイス鋼の親和性が高いほど、互いに溶融結合しやすくなる。ダイカスト合金が金型壁面に接着した後は、離型抵抗が大きくなり、離型時に鋳物にひずみが生じます。目視では、鋳物の固着部に表面の荒れ、剥離、欠落などの絞り跡があり(注:カーボンデポジットと区別する)、固着がひどい場合は鋳物が破れたり破損したりします。金型キャビティの表面は、目視では積層鋳造合金が付着しており、色は白色である。
ダイカスト合金液の注入または流動が金型壁またはコアに衝突した後、金型壁またはコアの温度が上昇する。高温になると、合金液と金型壁の金型鋼が溶けて溶着し、相互に付着する。合金液の温度が高いほど、射出速度が速いほど、金型温度が高いほど、金型硬度が低いほど、アルミニウム合金液と金型鋼との親和性が高くなり、溶融・溶着付着しやすくなる。ダイカスト合金に付着した金型表面は、脱型時にキャビティ表面と鋳物表面とが圧接し、鋳物表面が破れ、鋳物表面にベタベタした金型ひずみが現れます。
インナーランナー内のダイカスト合金液の充填速度が速いほど、金型壁面への溶湯流の衝撃は激しくなります。溶湯は中子や金型壁に直接衝突し、その衝撃力は熱エネルギーに変換されます。合金液の温度が上昇するだけでなく、衝撃を受けた部分の金型の温度も大きく上昇し、アルミニウム合金液と金型鋼の親和性が大幅に高まります。そのため、金型内のランナーのうち、合金液が高速で衝突する部分で金型の固着が最も発生しやすくなります。固定金型の側面に当たると、固定金型の側面への鋳物の充填力が大きくなる。
金型の硬度が不足すると、脱型時に金型表面がダイカスト合金に圧迫されて変形したり、金型中子が曲がって変形したりして、鋳物の脱型抵抗が大きくなる。
金型材料の不適切な使用、金型温度が高い場合、ダイカスト合金は金型表面に付着しやすい。
1. 2 脱型角度
金型の離型勾配が小さすぎる(または離型勾配がない、または逆に離型勾配がある)、金型側面に凹凸がある(浸食、潰れ、欠陥など)、表面が荒れているなど。脱型方向に支障をきたす。鋳物の脱型時に鋳型にひずみが生じ、鋳物の表面には型開き方向に沿って線状のひずみ痕、すなわち鋳物の深いキャビティの始端部のひずみ痕は広く深く、終端部のひずみ痕は次第に小さくなるか、あるいは消失する。顔全体のひずみ
鋳型の固定成形面が粗すぎたり、加工や製造の痕跡があったり、平滑性が十分でなかったり、加工や研磨の痕跡の線が脱型方向と一致していなかったり、脱型方向の平坦性が悪かったりすると、そのような悪い面が原因で増加する。脱型抵抗が鋳造品の脱型を妨げ、鋳造品の表面に研磨やスクラッチの痕跡が発生する。このようなスクラッチ痕は脱型方向の線状の溝であり、浅いものは0.1mm以下、深いものは0.3mm程度である。
1.3 鋳型に対する鋳物の密着性
鋳物の全体的または局部的な収縮により、鋳型の型締力が強すぎたり、型締力の分布がアンバランスで不合理である。この時、鋳型の固着によって鋳物が変形したり、ひびが入ったり、割れたり、さらには固定された鋳型に鋳物が固着してしまいます。あるいは可動金型の上部に鋳物が張り付いて抜けなくなる現象もあります。
ダイカスト中に毎回発生する固着現象については、その発生原因を詳細に分析する必要がある。例えば、ダイカスト鋳造中に鋳物が固定金型に張り付く場合、鋳物の固定金型への締め付け力が過大になっている原因を確認する必要があります。鋳物の固定金型側の外観を確認し、脱型方向に沿って、鋳物の表面に金型の跡があるかどうかを確認します。固着した金型にひどい傷やひっかき傷があると、脱型抵抗が大きくなり、鋳物の一部または全体がキャビティから出てこなくなり、鋳物が固着したままとなり、固着の原因となります。ひどい場合には、鋳物が破れたり、破損したりするだけでなく、金型の中子やキャビティにひずみ、亀裂、破断などの現象が発生することもあります。ダイカストの固着現象はアルミニウム合金に多い。ダイカストの固着不良を解決するための具体的な対策は以下の通りである。
2 固定金型への鋳物の固着防止策
2.1 ダイカスト金型における固定金型への鋳物の固着防止対策
新しく製作された金型の試用金型や、ダイカスト生産が熱間金型を開始する時、ダイカストの固着現象がよく発生する。ダイカスト作業工程が正常な場合、鋳物の固着の主な原因はダイカスト工程ではなく、鋳造構造設計、金型設計または製造の問題であるはずです。ダイカスト工程とスプレーのデバッグは改善することができますが、改善効果は一般的で、あまり安定しておらず、鋳物の固着現象は依然として発生します。
固定した金型に鋳物がくっつきやすい場合は、ダイカスト前に金型をよく予熱し、低速射出を開始する前に、金型キャビティにくっつき防止の金型ペーストと圧縮空気を塗布する必要があります。金型が固定されたままであれば、金型に問題があり、修理が必要であることを意味します。
設計された鋳物では、鋳物の固定型へのクランプ力が可動型へのクランプ力より大きいのは事実である。鋳物を排出するためには、鋳物の表面を固定金型側にセットできるようにする必要があります。エジェクターマークを残すか、エジェクターマークを取り除きやすくする。このように、金型を設計する際には、鋳物の排出機構を固定金型側に設計する必要があります。
移動金型と固定金型の充填力の計算に注意する。固定鋳型のパッキング力が移動鋳型のパッキング力より大きい鋳物や、固定鋳型と移動鋳型のパッキング力が同程度の鋳物では、固定鋳型が移動鋳型の鋳物に固着する可能性があります。鋳物や金型を設計する際には、鋳物や金型の構造、抜き勾配、表面粗さなどを変える必要があります。また、可動金型の鋳造力を固定金型の締め付け力より大きくする工夫が必要です。
固定金型の片側へのパッキング力が比較的大きい鋳物については、新しい金型を設計する際に、パーティング面をできるだけ固定金型に偏った側に選択し、鋳物のペアリングを高めるために、鋳物をできるだけ可動金型のキャビティに配置する必要がある。可動金型の締め付け力。固定金型の締め付け力を小さくするためには、固定金型の離型勾配を鋳造設計者と再決定する必要があり、固定金型の離型勾配をできるだけ大きくする必要があり、特に固定金型側の鋳造を修正または大きくすることに注意する。金型が金型に密着して緊張している部分の脱型勾配を大きくする。同時に可動金型の離型勾配を適切に小さくする。特にエジェクターピン近傍の可動金型の離型勾配を修正または小さくすることに注意する。可動金型にコアをセットするか、可動金型の片側のコアの長さを長くする。
固定金型の製造時や研磨時に、脱型に影響するアンダーカットや粗面を発生させないようにする必要があります。金型トライ後やダイカスト工程では、固定金型キャビティの潰れや打痕による変形を修正する必要があります;固定金型表面の付着物や金型に付着した合金の付着物を時間内に除去しないと、長い時間が経った後、固着現象がますます深刻になる。しかし、固定金型が鏡面に研磨された後は、塗料の付着には不利になる。鋳型を開くと、鋳物と鋳型の間に真空の狭い隙間が生じ、脱型抵抗が大きくなるため、固定鋳型の深いキャビティの底面を鏡面に研磨することができない。.窒化処理された鋳型の場合、表面の窒化層が損傷しないように、また、磨けば磨くほど鋳型が固着しないように、研磨は慎重に行う必要があります。
金型ランナーを修正し、ランナーの位置、大きさ、充填の流れ方向を適切に変更することで、ランナーが固定金型に与える衝撃によって発生する浸食や金型の固着不良を解消または低減します。例えば
火花冶金法は、炭化タングステン微粒子層を噴霧し、金属タングステン粒子と母材は、ダイカスト金型の表面に2〜4ミクロンの厚さのコーティングを堆積させるなど、金型表面の抗粘着性を向上させることができ、その硬度は、HV4 000〜4 500に達することができ、動作温度は800℃に達することができる、落ちることはありません。
鋳物を可動金型側に引き寄せるためには、エジェクタロッドの頭部からくさび状のバーブフックを補修し(フックの長さは5〜8mm、鋳物部品の厚さは1〜2mm、図1参照)、ダイキャスト製のバーブフックの取っ手により 鋳物を可動金型側に引き寄せ、鋳物上のバーブフックを取り外す。鋳物の可動金型への締め付け力を大きくするためには、鋳物の仕上げが必要な部分と外観品質に影響しない部分の側面について、対応する金型部品の表面粗さを大きくして、鋳物の可動金型の締め付け力に対する効果を大きくすればよい。より分かりやすい。
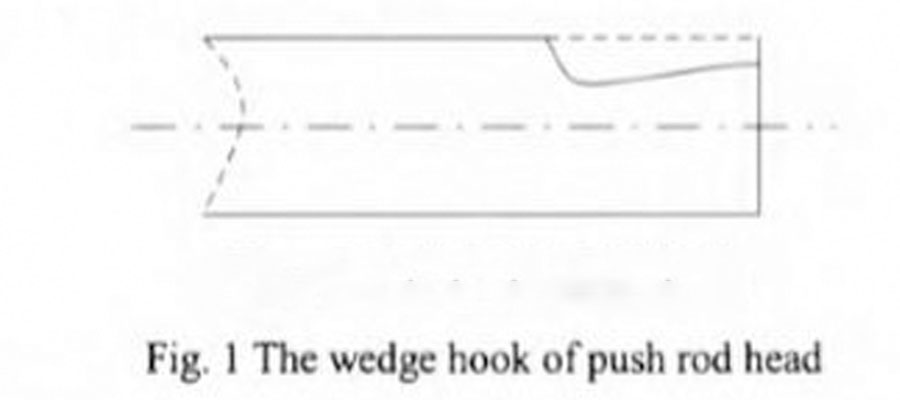
可動金型の締め付け力を高めるために、テンションバーを適宜使用することができる(図2参照):
固定金型側の充填力が可動金型側の充填力より大きい鋳物については、固定金型からスムーズに鋳物を取り出すために、エジェクタプレート、エジェクタロッド、リセットロッドを可動金型と同様に鋳物を取り出すように設計します。固定金型の片側にオイルシリンダーやバネを追加し、固定金型のトッププレートとエジェクターロッドを押し、型開きしながら鋳物を排出することも可能です。エジェクタープレートの後ろにスプリングがある。金型を開くと、固定金型のエジェクターがパーティング面から排出される。金型が閉じられると、可動金型パーティング面が4本のリセットロッドを押して固定金型プッシュプレートとエジェクターを押し、リセットします。
固定金型から鋳物を排出するためにエジェクタロッドを使用するために、3プレート2分割金型と同様のフックロッド、インパクトブロックおよびローラー機構を使用することもできます(図5参照、鋳物、エジェクタロッドおよびリセットロッドは図に示されていない)、固定金型エジェクタプッシュプレートを駆動する金型開動作に依存して、固定金型から鋳物を排出します。という構造である:所定の金型に対して鋳物を排出するエジェクタピンの排出構造を設計し、固定金型のエジェクタプレート5を固定金型模型6からはみ出させ、可動金型1に4個(または2個)のフックをセットする。この4本(又は2本)のフック棒4は、型閉め時に固定型模型6の側方に張り出す。フック棒4、インパクトブロック7、バネ3、ローラ機構8は、4つのフック棒4と固定金型 金型の上面押え板をフックで連結する。金型を開くと、可動金型引き棒4が固定金型エジェクタプッシャ5を引っ掛け、固定金型プッシャがエジェクタ5を押してエジェクタロッドを移動させ、固定金型から鋳物を排出する。この時、鋳物と可動金型は同期して移動する。一定のストロークまで移動した後、インパクトブロック、ローラー、バネ機構を使い、4本のフックロッドのフックを固定金型エジェクタープッシュプレートから外すと、固定金型エジェクタープッシュプレートの移動が止まり、金型が閉じると可動金型パーティング面も使用される。4本のリセット棒を固定金型エジェクタ押し板に押し戻し、固定金型エジェクタを元の位置に戻す。
2.2 ダイカストプロセスにおける固定金型への鋳物の固着防止対策
鋳型上のスプレーコーティング、合金液の流動衝撃速度、鋳型温度は、鋳造の固着に影響を与える主な要因である。
離型剤の種類、品質、濃度、吹き付け位置、吹き付け時間、吹き付け量は、鋳物の粘着状態に影響します。離型剤の散布量は、移動鋳型と固定鋳型の両側の鋳物の離型効果を調整するために使用します。鋳物が固定型に固着するのを防ぐため、可動型に吹き付ける離型剤の時間と量を適切に減らすことができる。可動金型に吹き付ける塗料は薄く均一にするのが望ましいが、塗り残しがあってはならない。金型表面の温度を下げるために、固定金型への離型剤の吹き付け量を増やし、特に固定金型の歪んだ鋳物の表面や絞り跡のある表面には、吹き付け量を増やす。固定金型の側面に定位置がない場合、または金型の痕跡がない場合は、コーティング剤の吹き付け量を適切に増やすよう注意する。
絞り跡のある金型表面には、ダイカスト後に塗料を吹き付ける前に、くっつき防止のモールドペーストを塗布して、くっつき防止のモールドペーストが高温で金型表面に焼結し、合金液と金型表面との間に形成されるようにする。
金型温度を適切に調整し、制御する。鋳物の稠密性と粘着性の鋳型の応力、鋳型の温度差と鋳物の収縮、鋳型温度と合金の収縮と鋳型の稠密性の関係を分析することが必要です。鋳物の表面に粘着性のある鋳型のひずみがある場合は、鋳物の表面品質を確保しながら、鋳型温度を低くするようにします。鋳物自体の締め付け力が大きい場合は、脱型時の鋳物の収縮を抑えることができる高い金型温度を使用するようにする、つまり、鋳物の締め付け力が大きくなっていないときに脱型を開始する。
可動金型の温度を相対的に下げ、鋳物の収縮を促進することにより、可動金型に対する鋳物の気密性を高めることができ、固定金型の温度を相対的に上げ、鋳物の収縮を抑えることにより、固定金型に対する鋳物の気密性を低下させることができる。可動金型の冷却水の流量を増加させることにより、可動金型の金型温度を低下させることができ、固定金型の冷却水の流量を減少または閉鎖することにより、固定金型の金型温度を上昇させることができる。一般にアルミ合金鋳物のダイカストでは、型開き後1〜3秒以内に可動金型キャビティの表面温度を測定する。表面温度は300℃以下、好ましくは(240±40)℃であり、スプレー後金型を閉じる前に、固定金型キャビティの表面温度を1~3秒以内に測定し、140℃以下でなければならない。
注湯温度は鋳型温度と同様に、鋳物の収縮率やパッキンの締まり具合を変化させます。注湯温度を高くし、型開時間を短くすると、充填力は低下しますが、合金液と鋳型鋼の親和性が高くなり、鋳物の厚肉部に固着が発生する可能性があります。
3 移動する鋳型に鋳物が付着するのを防ぐ対策
3.1 ダイカスト金型における可動金型への鋳物付着防止対策
鋳造品が可動金型に固着する主な原因は、鋳造品が可動金型を締め付ける力が強すぎて、エジェクタロッドの突き出し力が不足しているためです。突き出し力が足りない場合は、ダイカストマシンの突き出しシリンダーの油圧を上げるか、突き出し速度を上げる必要があります。エジェクターピンの直径が小さすぎたり、本数が少なかったりすると、エジェクターピンの強度が不足し、曲がったり折れたりすることがあります。
鋳物が可動金型に固着する力が小さいと、脱型時のひずみが軽かったり、金型表面の粗さによる抵抗が小さくても、排出時に鋳物が変形してしまうため、金型固着部を研磨したり、窒化処理したり、離型抵抗を大きくする必要があります。離型剤の噴霧量は離型抵抗を小さくします。.鋳物の可動金型への固着力が大きく、脱型時に鋳物に大きなひずみが生じたり、鋳物の上端が破損・断線したり、エジェクターで鋳物が排出されたりする場合は、鋳造角度を適切に大きくする必要があります。鋳物や鋳型の設計を改善し、鋳物が鋳型に固着して収縮に影響するような無理な構造を排除する。
鋳物の排出力の不均等による金型の固着歪みを防止するため、金型排出板を押すダイカストマシンの4本のプッシュロッドの長さは同じでなければならず、その差は0.20mmを超えてはならない。マシンのプッシュロッドとエジェクタ 鋳物のエジェクタロッドの位置はバランスが取れていて合理的でなければならず、金型キャビティの中心から逸脱してはならず、ダイカストマシンのエジェクタシリンダの中心から逸脱してはならない。
中子抜きと排出設定のバランスが悪いと、鋳物に不均一な応力がかかり、たわみが生じます。ダイカストマシンの油圧排出シリンダーのプッシュロッドの長さが同じでなく、鋳物の排出力が不均一であったり、プッシュロッドの位置が不適切であったりすると、排出時に鋳物がたわんでしまう。改善策としては金型の構造を変更し、中子の引き抜き機構と押し出し棒の位置を調整し、鋳物の力が均等に押し出されるようにし、鋳物が平行に均等に押し出されるようにする;排出機構、ダイカストマシンの押し棒の位置と数量(4-6本の押し棒を使用するのが最も簡単)を調整し、エジェクタロッドと金型の鋳物に均等に応力がかかるようにする;エジェクタロッドの数を合理的に増やし、エジェクタロッドの直径を大きくし、エジェクタロッドの位置を配置して、排出バランスを確保する。
平らな部品や薄肉の鋳物の変形抵抗が不十分な場合は、エジェクターピンの本数や直径を増やす必要があります。また、エジェクタ位置に小さなボスを追加して、エジェクタピンを鋳物の小さなボスに当てさせることもできます。突き出し力面積が大きいと、鋳物の突き出し力が均一になります。
高品質の金型鋼を使用し、金型温度が高い場合、ダイカスト合金は表面に付着しにくい。高品質の金型鋼を使用すれば、金型表面にマイクロクラックが早期に形成されることはなく、合金の固着の基礎もなくなります。
金型硬度が不足していたり、もろかったりすると、合金液が金型に付着しやすくなる。金型硬度が妥当かどうかをチェックし、金型鋼が脆くならないように熱処理工程もチェックする必要がある。インナーランナーの衝撃に耐えるモジュール、金型インサート、すべてのコアの硬度は、金型キャビティモジュールの硬度よりHRc3~5高い。金型設計で問題がないことを確認し、それでも鋳造金型の固着ひずみの解消が難しい場合、窒化処理、KANI 7C、タングステンコーティング、PVDナノチタンプレーティングなどの表面処理手段を用いて、金型の表面硬度を向上させなければならない。
金型キャビティの表面は、一般的にオイルストーンとサンドペーパーで磨く。空気圧工具で磨く場合は、金型表面の窒化物層を傷つけないように、金型を傷つけないように注意しないと、磨けば磨くほど金型のベタつきがひどくなります。ケース粘着性のあるモールドや粘着性のあるドレープのキャビティ以外の部分を掃除するときは、ヘラを使って凹凸を取り除き、サンドペーパーで軽く磨きます。凹凸をすくい取らないと、より深刻な固着の原因になります。金型の空洞をえぐらないように、金型の空洞の中の粘着性モールドをノミで掃除しないように注意してください。
3.2 ダイカスト鋳造工程における移動金型への鋳物付着防止対策
ダイカストマシンの高速射出速度を下げるか、金型内の湯道面積を大きくして湯道の充填速度を適切に下げる。湯道の充填速度を上げずに湯道の面積を大きくすれば、充填時間を短縮でき、湯道の衝撃による総発熱量を低減でき、湯道の衝撃低減効果が得られる。
鋳造圧力を適切に下げる:薄肉部品や気孔のない鋳物には40~55MPa、一般鋳物には55~75MPaと小さめの圧力を選択し、厚肉部品や気孔のある鋳物には75~100MPaと高めの圧力を使用します。鋳造圧力が高いほど、鋳造品の機械的性質が向上し、鋳造品の金型への密着性が高まります。鋳型の固着が発生した場合は、適切な鋳造圧が使用されているか確認する必要があります。鋳物をより高い温度で脱型できるように型開き時間(鋳型冷却時間)を適切に短縮し、鋳型の型締力が最大値に達しないようにすることで、鋳物の鋳型に対する型締力を低減し、鋳型の固着を軽減することができます。程度。
鋳物の脱型角度が小さすぎると、鋳物が金型に固着する可能性が高くなります。従って、鋳物の合金材質や寸法構造に応じて適切な離型角度を選択する必要がある。鋳型の固着が発生した場合、抜き勾配を適切に大きくすることで、熱衝撃や収縮による固着現象を解消することができます。鋳物構造に無理があると、鋳物の収縮・冷却過程で各部の収縮が不均一になり、収縮に対する抵抗力がアンバランスになります。可能かつ必要であれば、鋳物の設計構造を改善し、肉厚を均一にします。断面の厚さについては、厚い部分を中空構造またはリブ連結構造に設計するようにし、厚さの差が大きい移行部は避け、無理なボス、ラグ、補強リブをなくします。また、鋳物の凹角部のフィレットや脱型角度を大きくすることで、鋳型の固着を防ぐことができます。
鋳型の内湯道付近や衝撃キャビティに合金液が充満する部分、鋳物の肉厚の厚い部分、鋳物の隅の凹んだ部分などは、長時間合金液の影響を受けやすい。鋳造棒やひずみが発生するので、金型のこれらの部分に水冷用の冷却水管を設ける必要がある。細長い中子を冷却する場合は、冷却水の圧力を高くする。これらにより、金型温度を十分に下げることができ、金型の固着を防ぐことができる。
ダイカスト合金が鋳物の表面で金型表面に付着すると、表面に小さな気泡が発生することがあります。この現象に対しては、金型表面をエメリークロスやオイルストーンで研磨し、また金型が固着するということを繰り返しますが、完全に問題を解決することはできません。この種のくっつきを解決する良い方法は、くっついた鋳型の表面にショットピーニングを行うか、または鋳型のくっついた部分の表面に幅0. mm、深さ0. mmのネットパターンを形成し、間隔を2~5mmにすることで、鋳物の表面のくっつきの欠陥をなくすことができる。
ランナーの収縮は鋳造変形や鋳型の固着の原因となる。分岐湯道の長さを長くして、分岐湯道の面積を小さくする;湯道の幅を小さくし、湯道の長さを長くし、湯道を小さくする。水路の数;鋳型のランナーの冷却水による冷却を増やして、ランナーの収縮が鋳物に与える影響をなくす。
ダイカスト用アルミニウム合金の鉄含有量が少ない(例えば0.6%未満)ほど、アルミニウム合金液と金型鋼との親和性が高くなり、金型に付着しやすくなる。アルミニウム合金液中の鉄含有量を適切に増加させることにより、アルミニウム合金の金型への付着をより低減することができ、一般的には、ダイカストアルミニウム合金液中の鉄含有量を0.6%〜0.95%に制御することが要求される。低融点金属との混合による金型付着を防止する必要がある。マスターアロイを使用して化学成分を調整する場合、マグネシウムや亜鉛などの単体金属に加え、偏析が激しく金型に固着するのを防ぐため、アルミニウム液に純金属を添加することはできません。
ダイカスト合金の収縮率が大きいほど、金型にくっつきやすくなるだけでなく、高温強度も悪くなる。収縮率が大きい合金もあり、合金の液相と固相の温度範囲が広いほど、合金の収縮率は大きくなります。鋳物の構造形状や複雑さによって、収縮による鋳型の固着や変形の解消が困難な場合は、体収縮や線収縮が小さく高温強度の高い合金に変更するか、合金組成(アルミニウムなど)を調整することを検討する。シリコン合金中のシリコン含有量が増加すると、鋳物の収縮率が小さくなる)収縮率を小さくする;または合金を修正するために、アルミニウム合金液に0.15%〜0.2%の金属チタンおよび他の結晶粒微細化剤を添加して、合金の収縮傾向を小さくする。
4 結論
ダイカストの固着には様々な原因があり、固着の解決策も様々である。本稿では、ダイカストの固着不良を解決するための対策を具体的に提案する。固着の原因を注意深く観察・分析し、的を射た対策を講じるべきである。対応する対策は、効果的に金型の固着の問題を解決することができます。