ラピッドプロトタイピング(RP)は1990年代に開発されたハイテクである。人々の頭の中にあるデザインコンセプトを、素早く実際のモノにすることができる。特に特筆すべきは、製品開発プロセス全体が金型やプロセス設備を必要としないことで、プロトタイプや新製品の試作サイクルが大幅に短縮され、企業の競争力を高める重要な手段・ツールに早変わりする。INCAST2004(11)が発表したインターネットアンケート調査によると、欧州のインベストメント鋳造メーカー400社以上のうち、93%以上がラピッドプロトタイピングを利用している。この新技術の使用は、新製品の開発を加速させるために不可欠であるというのが、インタビューに答えた全員の意見である。企業が市場に迅速に対応する能力を開発し、強化することは非常に重要である。
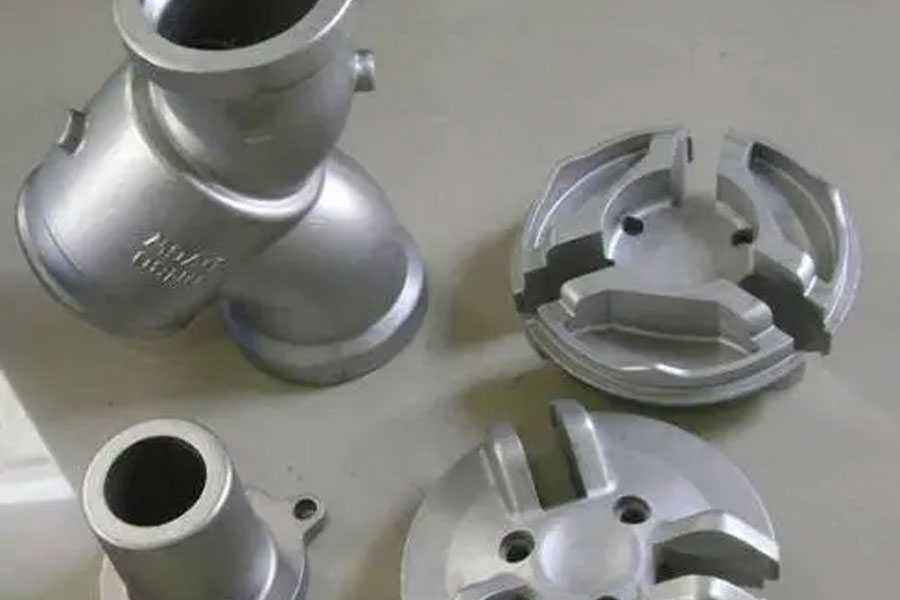
インベストメント鋳造における一般的なラピッドプロトタイピング法の応用
インベストメント鋳造におけるラピッドプロトタイピング技術の応用には、主に以下のような側面がある:
1.投資をする
パターンを作成する際、ラピッドプロトタイピングマシンは、他のCADソフトウェアで確立された3次元幾何学モデルを入力できるだけでなく、工業用CT(コンピュータ断層撮影)でスキャンされたデータファイルを受け取ることもできる。例えば、まず部品(スクリュープロペラ、図 12-1a)を CT でスキャンし、その断面の二次元画像を得る(図 12-1b)。その後、画像処理ソフトウェアが各断面の二次元画像を組み合わせて(図12-1c)、三次元の幾何学モデルを形成する(図12-1d)。そしてそれをラピッドプロトタイピングマシンに送り、パターンを作る(図12-1e)[2]。この復元(リバース)エンジニアリング法は、機械部品を復元するだけでなく、ある種の人間の臓器を模倣することもできる。
2.金型(圧縮成形)およびその他のプロセス機器の作成
ラピッドプロトタイピングで精密鋳造用金型を作るには2つの方法がある:1つはまずマスターモールドを作り、それからエポキシまたはシリコーンゴムのプロファイリングを作り直す方法、もう1つはCADシステムで生成された3次元プロファイリングブロックを使用する方法である 幾何学モデルを直接ラピッドプロトタイピングマシンに入力して樹脂成形を行う。このタイプのプロファイリングは、主に小ロット生産(数十個)に適しています。マスターモールドの表面に厚さ約2mmの金属層を溶射し、その後にエポキシ樹脂を充填して金属-エポキシ複合プロファイルを作れば、数百個の精密鋳造品を製造する要件を満たすことができる。SLS法を用いる場合、例えば、加工対象物を樹脂粉末から、表面に熱硬化性樹脂の薄い層を有する鉄粉に変え、レーザー焼結して成形体を形成し、その後焼成して樹脂を除去し、最後に銅液を成形体の気孔に浸透させる。出来上がったプロファイリングは、強度や熱伝導率の点で金属に近い。さらに、ラピッドプロトタイピング技術は、ある種の不規則な形状の金型を作るのにも使えます。
3.鋳型の直接生産
1990年代初頭、アメリカのサンディアナ国立研究所では、高速鋳造(FastCAST)と呼ばれる特別な研究が行われ、ダイレクト・シェル・キャスティング(DSPC)と命名された。残念ながら、その後の報告はほとんどない。
1994年、アメリカのZ社が3Dプリント技術「3Dプリンティング」の開発に成功した。この技術はもともと、マサチューセッツ工科大学のイリー・サックス教授が発明し、特許を取得したものである。基本原理はSLS法に似ている。まず、耐火物やプラスチック粉末の層をローラーで吹き付ける。SLSとの違いは、レーザー発光ヘッドを駆動する代わりに、インクジェット・プリント・ヘッドを駆動して、製品の断面形状に合わせて "印刷 "用の接着剤を噴霧することである。以上の動作を部品が完成するまで繰り返すので、「3Dプリンティング技術」と名付けられた。そのメリットは、運転コストや材料費が安く、高速であること。噴霧された粉体が石膏とセラミックスの混合粉体であれば、ZCastと呼ばれるアルミニウム、マグネシウム、亜鉛などの非鉄合金鋳造用の鋳型(石膏鋳型)に直接、短時間で作ることができる(図12-2)。
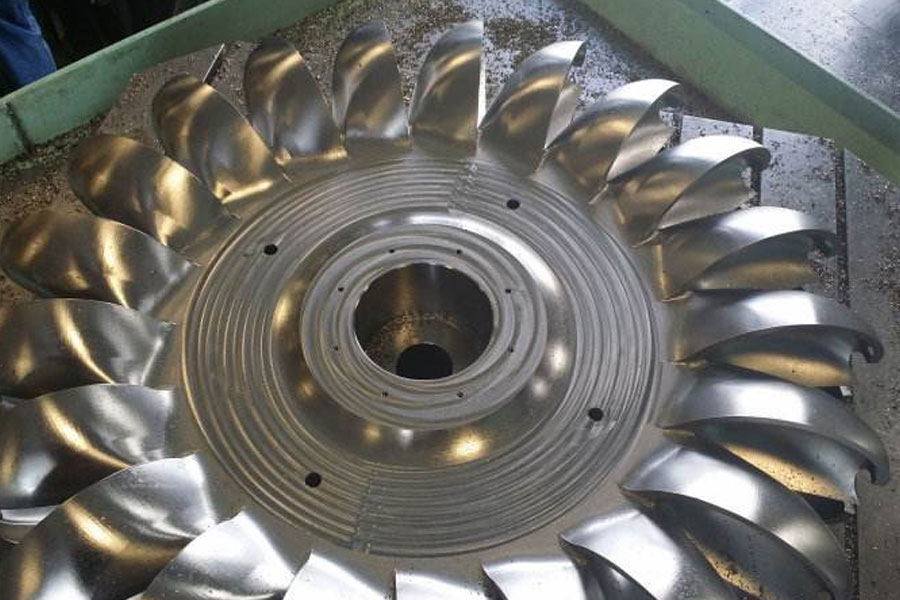
一般的なラピッドプロトタイピング手法の比較 アプリケーションの効果
現在、実生産でよりポピュラーなラピッドプロトタイピング方法には、3次元リソグラフィ(SLA)、選択的レーザー焼結(SLS)、融着(FDM)、積層造形(LOM)、直接鋳型鋳造(DSPC))などがある。近年、多くの海外の研究機関が、インベストメント鋳造における生産パターンの品質と性能の観点から、上記の方法を比較している。その結果は以下の通りである:
パターンの表面粗さの比較
総合的に見ると、SLA法はインベストメント鋳造法とは相容れない部分もあるが、寸法精度や表面品質が良いため人気がある。海外では、特に航空宇宙産業や軍事産業において、インベストメント鋳造企業が広く利用されている。SLS法の品質はSLA法より若干劣るが、インベストメント鋳造のプロセス要件に適合させるのは容易である。そのため、国内のインベストメント鋳造で使用される用途がますます増えています。FDM法はインベストメント鋳造のプロセス要求に最も適合しやすいが、ワックス鋳型の寸法精度と表面品質は満足できるものではない。したがって、インベストメント鋳造に適応するのは難しい。この2つの方法のインベストメント鋳造への普及と応用には一定の制約がある。
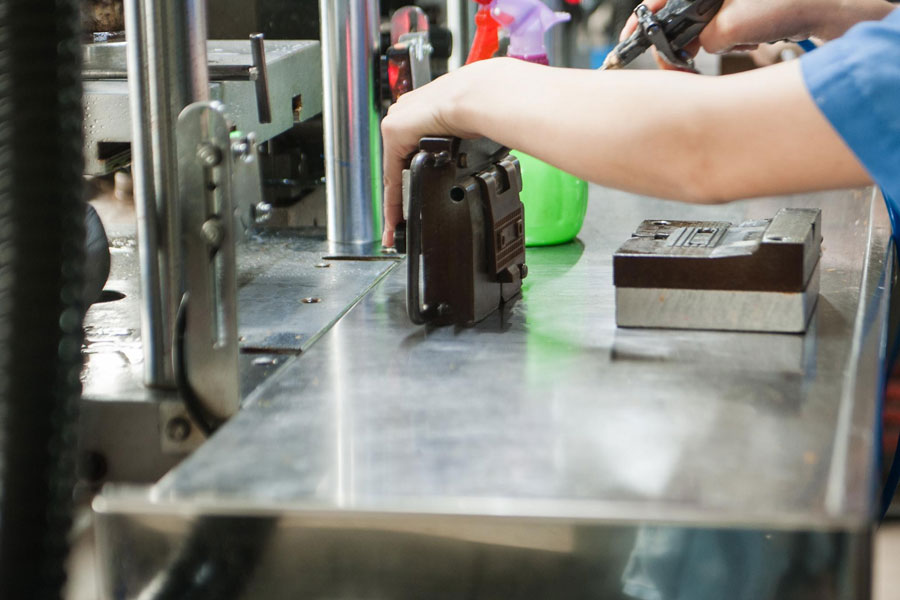
インベストメント鋳造におけるSLAとSLSの応用における新展開
1.新しい光硬化樹脂
SLA法は1987年には実用化されていた。当初は特定の機能を持つ物理的なモデルやプロトタイプを作るために使われていた。1990年代初めには、米国3D System社のQuickCastソフトウェアの開発に成功し、SLAラピッドプロトタイピングマシンによって、滑らかで緻密な外観を保ちながら(図12-3b)、ハニカム形状の構造(図12-3a)を作り出すことができるようになった。さらに、金型製造用の光硬化性樹脂には、次のような特別な要件も必要であることが次第に分かってきた:
近年、米国DSMソモス社は、上記の主な要件を満たす新しいタイプの光硬化性樹脂Somos 10120の開発に成功し、インベストメント鋳造メーカーにかなり支持されている。この新製品は、3つの異なる精密鋳造工場で3種類の合金(アルミニウム、チタン、コバルトモリブデン合金)で鋳造され、満足のいく結果を得ている。
2.小ロット生産にはSLAモデルを使用
SLAパターンを使用した精密鋳造品の小ロット生産で考慮すべき主な問題は2つある。1つは、パターンと鋳造品が達成できる寸法精度であり、もう1つは、生産コストと納期に利点があるかどうかである。Solidiform社、Nu-Cast社、PCC社、Uni-Cast社など、米国の複数の精密鋳造工場では、SLAパターンを使用して数百個の鋳物を鋳造している。鋳造サイズを実測した後、統計分析によると、DSM Somos社が開発した新しい光硬化樹脂11120が使用されている。QuickCast技術により、出来上がったSLAパターンのサイズ偏差は、鋳造公差値の50%以下です。ほとんどの鋳物のサイズは公差要件を満たしており、合格率は95%以上である(図12-4)[7]。
SLAパターンを作るコストは、同じワックス型を作るコストよりはるかに高く、時間もかかりますが、プロファイルを設計・製造する必要はありません。そのため、1つのピースを小ロットで生産する場合でも、コストと納期は有利になる。鋳物が複雑であればあるほど、この利点は明らかです。Nu-Cast社が製造している複雑な形状の航空精密鋳造品を例にとると(図12-5)[7]、鋳型製造コストは約85,000米ドルで、毎日4個のワックス鋳型が製造され、1個のワックス鋳型のコスト(材料費と人件費を含む)は150米ドルである。SLA方式を採用した場合、SLAモデル1つあたりのコストは2846米ドルだが、金型を設計・製造する必要はない。この計算から、出力が32個未満の場合、SLA金型を使用するコストはワックス金型を使用するコストよりも低く、32個以上の場合、コストはワックス金型よりも高くなる(図12-6)。したがって、生産量が87個未満の場合、SLA鋳型を使用すると、鋳物の納品はワックス鋳型よりも速くなる(図12-7)。しかし、87個以上であれば、ワックス鋳型の方が速い[7]。考慮すべきもう一つの要因は、ワックス鋳型を使用する場合、製品が更新されたときに鋳型を作り直す必要があり、コストがかかることである。一方、SLA外観の場合、CAD幾何学モデルを変更するだけでよく、鋳型を作り直すよりもはるかに簡単で迅速である。.
3.SLS焼結ポリスチレン粉末含浸ワックスパターン
SLSは当初、レーザーを使って特殊なワックス粉末をワックス鋳型に焼結させるもので、インベストメント鋳造のプロセス特性に非常に適している。1990年末の時点で、米国には50以上の鋳物工場があり、約3000個のワックス鋳型を生産し、鋳造に成功している。様々な金属鋳物を生産する。しかし、ワックスパウダーは最も理想的な鋳型材料ではない。それで作られたワックス鋳型の強度は不十分で、温度が高いと軟化して変形しやすく、温度が低いと割れやすい。そこで1990年代初頭、米国の一部のSLAユーザーは、ワックスパウダーをポリスチレン(PS)やポリカーボネート(PC)などの熱可塑性パウダーに置き換えようとした。この種の材料は、ゆるく多孔質な形状(気孔率は25%以上)にすることで、脱型時にシェルが膨潤したり割れたりするリスクを減らすことができる。シェルを焼成した後、灰分は少なくなるが、模様の表面は粗くなる。そのため、模様が出来上がった後、表面を滑らかで緻密なものにするために、手作業でワックスをかけて磨く必要がある。現在、この方法は国内外で広く使われている。