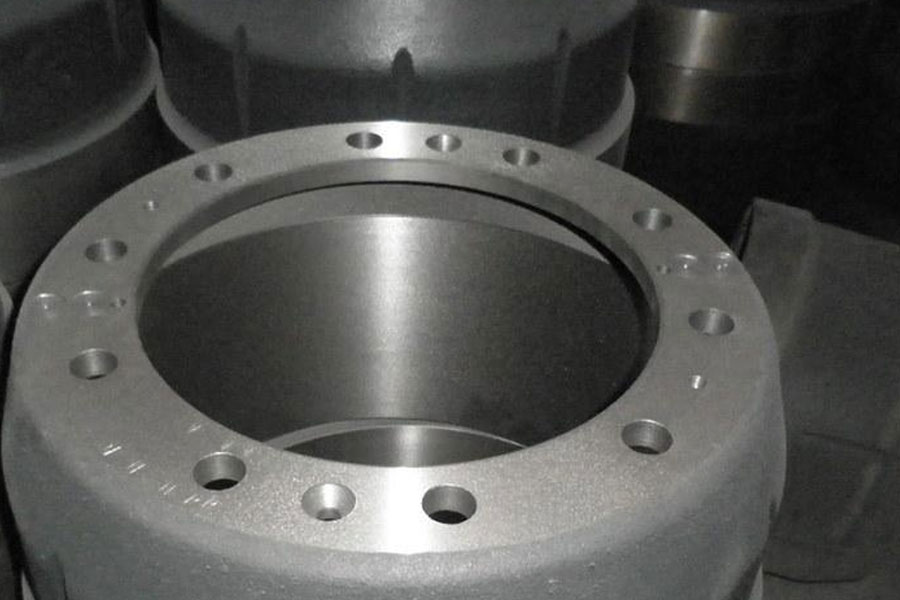
超大深度坑井掘削の要求を満たすため、ドローワークスブレーキハブの過度の摩耗と熱疲労亀裂に対処するために多くの作業が行われてきた。一方では、技術革新を通じて材料の耐摩耗性を向上させ、ブレーキハブの耐用年数を延ばした。例えば、ブレーキハブの耐摩耗性を向上させるために、Q345Aマトリックス上に耐摩耗性材料の層を表面溶接したり、代わりに鋳造構造を使用したり、鍛造によってより緻密で微細かつ均一な組織を得ることで、材料の耐摩耗性を向上させる。一方、Cr-Mo鋼に希土類を添加するなど、新しい耐摩耗材料や複合材料を開発し、ブレーキハブの耐摩耗性と熱強度を向上させ、ブレーキハブの寿命を延ばす。しかし、サーフェシング工法は生産効率が低く、通常はブレーキハブが摩耗した後の寸法補修としてしか使用されないこと、ブレーキハブを鍛造するためには大型のリングローリング設備が必要であり、加熱工程が増えるため生産コストが高くなること、Cr-Mo鋼は貴金属を含むため材料コストが高くなることなどの問題がある。したがって、ブレーキハブの寿命を延ばすために、低コストで耐摩耗性の高い新しいタイプの鋳造ブレーキハブ材を開発することは、技術的に大きな意義がある。
今回使用したMn-V合金は、国内の石油機器メーカーが独自に開発した新素材である。熱強度と耐摩耗性に優れ、過酷な使用条件下でのブレーキハブの使用条件を満たすことができる。経済効果も高い。しかし、筆者の調査と油田統計を通じて、この材料の溶接継手は長期使用中に亀裂が発生しやすく、この材料の応用に一定の影響を与えることが分かった。本稿では、この材料の溶接性能を改善するために、この材料の溶接サンプルを分析する。
実験用試験板は、アルカリフェノール樹脂砂型鋳物製である。樹脂砂の割合は樹脂1.6%、硬化剤0.4%、残りは砂である。砂は新砂と古砂の混合で、新砂と古砂の比率は1:3である。押湯を切断した後、1100℃で保温する。焼ならし保温時間は6時間。焼ならし後、鋳造ブランクを530mm×180mm×25mmの試験板に加工し、60°Vの溝をつけ、Φ1.2mmのJQ-MG50-6溶接ワイヤーを用いてGMAW多層マルチパス溶接を行う。溶接前にサンプルを150℃に予熱し、層間温度が300℃を超えないように制御し、溶接後にゆっくりと冷却する。
ブレーキハブをMn-V鋼で溶接した後、継手にはある程度の硬化性があり、継手の脆性割れが発生しやすい。溶接後、継手に時効処理を施すと、溶接継手の塑性靭性が向上し、第二相の強化や細粒強化により、継手の総合的な機械的性質が改善される。500℃で30分間時効処理したサンプルは、降伏強さ560MPa、引張強さ715MPaと最高の機械的特性を得た。熱影響部は継手全体の弱点であり、引張試験片はすべて溶接継手の熱影響部で破断した。溶接後のブレーキ・ハブの時効処理は、継手の塑性靭性を改善することができ、継手は時効後に脆性破壊から延性破壊に転じる。時効温度が300℃を超え、時効時間が30分を超えると、塑性破壊として現れます。