自動車エンジンの部品間の摩擦を減らす対策として、大きく分けて以下の3種類がある。
ひとつは、部品間の実際の接触面積を減らすことだ;
もうひとつは、部品間のせん断応力を低くすることだ;
3つ目は、コンポーネント間の入力負荷を減らすことだ。
部品の表面粗さを小さくすることは、部品間の実際の接触を減らすのに役立つ。表面の初期粗さを変えないことを前提に、摺動によって相手材の表面を滑らかにすることで、摩擦力をさらに低減することができる。
現在、エンジンのシリンダー・ボアのほとんどは、アルミニウム合金製のシリンダー・ブロックにねずみ鋳鉄製のブッシュを鋳込んで作られている。鋳鉄の熱伝導率(50W/(m・k))はアルミニウムの熱伝導率(100W/(m・k))より低く、鋳鉄の厚さは数mmである。近年、燃焼室内の放熱性を向上させるため、シリンダーボアの代わりに鋳鉄スリーブを使用し、鋳鉄を溶射することが行われている。これにより、界面の密閉性を向上させ、管壁を薄くすることができ、この部分の伝熱・熱伝達を大幅に改善することができる。熱伝達。
また、溶射特有の現象として、皮膜中にある程度の空隙が入り込み、その空隙が表層に露出することで、シリンダーボア表面の油保持性を向上させることができる。
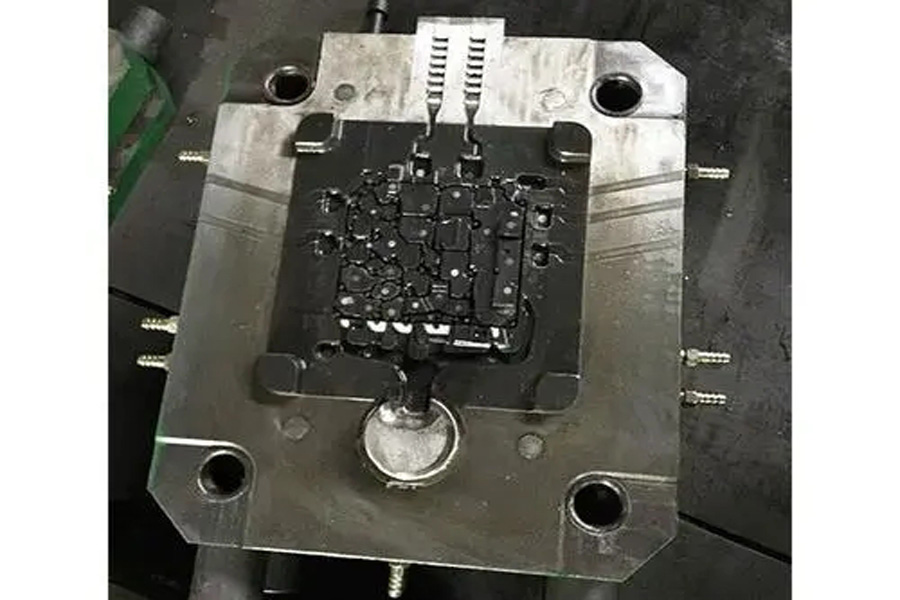
従来のエンジンのシリンダーボアのホーニングメッシュを使用する必要がないため、オイル保持性を確保することができ、シリンダーボアの表面を滑らかにすることができる。前述の伝熱性が良いという利点に加え、境界から混合潤滑領域までの摩擦を効果的に低減できる。
部品の表面粗さに対する突起の接触については、突起を含む表面層全体を低せん断応力材として使用する。粗さを小さくし、摩擦だけを小さくする方法として、固体潤滑剤を使用することができる。
特に、面圧がそれほど高くない場合には、いわゆるソフトコーティングを使用することができる。すなわち、粒状の二硫化モリブデン(MoS2)またはグラファイト、および固体潤滑剤としてのテトラフルオロエチレンをポリアミド樹脂(PAI)中に分散させた媒体中のコーティング、またはMoS2粒子をワークピースに対して高速で直接照射して得られるコーティングである。この種のコーティングは、エンジン部品の接触面積の大きいピストンロッドやクランクシャフトの軸受合金の表面層に適用することができる。
一方、面圧の高い部品に対しては、無潤滑で硬い状態でも固体潤滑剤と同等の低摩擦係数を持つDLCコーティングを開発し、潤滑下でも同様の効果が得られるようにした。コーティング
本稿では、水素を含まないDLC膜(水素フリーDLC膜)とSiを含むDLC膜(Si-DLC)について紹介する。この2つは、被膜自体に独立した特性がなく、潤滑油や潤滑油中の水分との組み合わせで摩擦を大幅に低減できるという点で、これまでの表面処理や設計思想とは大きく異なる。
ピストンリングとシリンダーボアとの摩擦を低減するため、近年、従来のCrメッキや窒化技術に代わり、CrN膜が使用されるようになった。Crメッキ膜の膜厚が100程度であるのに対し、耐摩耗性の良いCrN膜の膜厚は25程度であり、膜厚の偏差幅を小さくすることができる。その結果、ピストンリングの張力の下限値を変えることなく、中間値を小さく設定するだけで、ピストンリングとシリンダーボアとの摩擦を低減することができる。
また、CrN膜の摩耗量が少ないため、ピストンリング外周面の初期曲率を維持することができ、摩耗による接触範囲の拡大を抑制することができ、摩擦低減にも寄与する。