延伸金型は、プレス金型業界全体の中で非常に大きな割合を占めています。私たちの一般的なカップ、モーター上のシェル、ほとんどほとんどの製品は、多かれ少なかれ延伸する必要がある製品を持っています。金型の設計は、従来のアルゴリズムに従って計算すればいいというものではない。工程が多すぎて変数が多く、特に一部の非回転体の延伸は法外である。
絞り金型の設計には、絞り係数、材料の限界に達するかどうか、バネ力の決定、絞り方向が上向きか下向きか、など考慮すべき要素が多すぎるため、一度の成形では思うような結果が得られないことが多く、何度も試行錯誤を繰り返す必要があり、時には金型が廃棄されることもある。そのため、実務での経験の積み重ねが絞り型の設計に大いに役立つ。
さらに、切削材料のサイズも金型全体の試作に重要な役割を果たします。そのため、不規則な深絞り部品を設計する場合、金型設計の段階で空ステップを確保することがほとんどです。
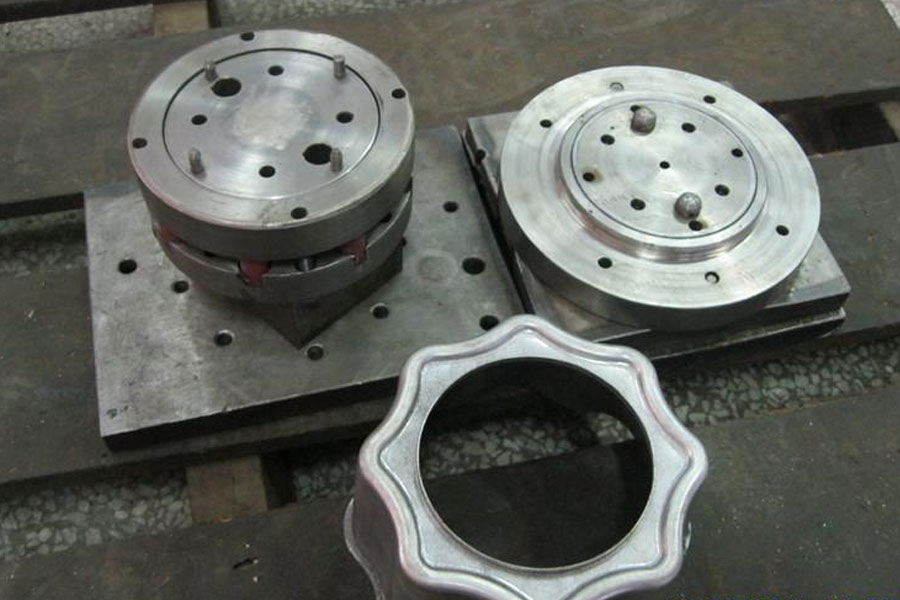
ストレッチ素材
顧客の材料に対する要求がそれほど厳しくなく、金型の試作を繰り返しても要求が満たされない場合は、引張特性の良い材料に変更して再挑戦することができる。良い材料は成功の半分である。延伸のためには、それを無視してはならない。延伸用冷延薄鋼板には、主に08Al、08、08F、10、15、20鋼が含まれる。最も多いのは08鋼で、縁取り鋼と殺し鋼に分けられる。縁取り鋼は価格が低く、表面品質が良い。偏析はより深刻で、"ひずみ時効 "の傾向がある。高いプレス性能と外観が要求される部品には適さない。キルド鋼の方が性能が均一で良いが、価格が高い。代表銘柄はアルミキルド鋼08Al。外国鋼は日本のSPCC-SD深絞り鋼を使用しており、引張特性は08Alより優れている。
金型表面の仕上げ
深絞り加工を行う場合、ダイスとブランクホルダの両面の研磨が十分でないと、特にステンレス板やアルミ板を絞り加工する場合、絞り傷が発生しやすくなり、ひどい場合には引張破断に至ることもある。
ブランクの大きさの決定
より多くのシワとより少ないクラックが私たちの原則です。ブランクの位置決め設計は正確でなければならない。単純な形状の回転体絞り部のブランク径は細くならない。材料の厚さは変わりますが、基本的には元の厚さに近いです。密着度は、ブランクの面積と延伸部の面積(トリミングを加える必要がある場合)が等しいという原則に基づいて計算できる。しかし、延伸部品の形状や工程は複雑であることが多く、時には薄くして延伸する必要があることもある。アンフォールディング計算ができる3Dソフトは数多くあるが、その精度は100%の要求を満たすことはできない。
製品は複数の工程を経なければならないが、一般的に最初の工程はブランキング工程である。まず、抜き型の全体のサイズを決めるために、展開した素材の計算を行い、ブランクの形状とサイズを大まかに把握する必要がある。ブランキング金型の凸型と凹型のサイズは、金型設計が完了してから加工してはいけません。まずワイヤーカットでブランクを加工する(ブランクが大きい場合はフライス盤で削り、クランプする)。その後の延伸工程で実験を繰り返し、最終的にブランクのサイズを決定し、ブランキング金型の凸型と凹型を加工する。
反転プロセスでは、まず絞りダイスを試し、次にブランクのブランキングエッジサイズを加工する。
引張係数
延伸係数は、延伸工程の計算における主要な工程パラメータの一つであり、通常、延伸の順序と回数を決定するために使用される。
延伸係数mに影響を与える要因には、材料特性、材料の相対的な厚さ、延伸方法(ブランクホルダの有無を指す)、延伸時間、延伸速度、ダイスのフィレット半径の凸凹、潤滑など多くのものがある。
引張係数mの計算と選択原理は、様々なスタンピングマニュアルで紹介されている重要なポイントである。計算、表引き、計算など多くの方法があり、私も本に従って選んでいます。私も本に従って選んでいます。目新しいものはありません。本を読んでください。.
素材の相対的な厚み、延伸方法(ブランクホルダーの有無を指す)、延伸回数は、金型補修時に調整するのは容易ではないので注意が必要だ。延伸係数mを選ぶときは、同僚を見つけてチェックしてもらうのがベストだ。
加工油の選択
加工油の選択は非常に重要である。潤滑油が適しているかどうかを見分ける方法は、製品を金型から取り出したとき、製品の温度が高すぎて手で触ることができない場合は、潤滑油の選択と潤滑方法を再考する必要があり、キャビティに潤滑油を塗布する必要があります。または、シートの上にフィルム袋を置く。
引張割れの場合は、凹型に潤滑油を塗布し(凸型には塗布しない)、ワークを0.013~0.018mmのプラスチックフィルムで覆う。018mmのプラスチック膜を被せる。
ワークの熱処理
推奨はされないが、それでも延伸の過程で、加工物は冷間塑性変形による冷間加工硬化を受け、塑性変形性が低下し、変形抵抗と硬度が増すことは言うまでもない。無理な金型設計に加えて、実施する必要がある。中間焼鈍で金属を軟化させ、塑性を回復させる。
注:一般的なプロセスでは、中間アニールは必要ない。結局のところ、コストを上げる必要があります。工程を増やすか、アニールを増やすか、慎重に選択する必要があります!
焼鈍は一般に低温焼鈍、すなわち再結晶焼鈍が採用される。焼鈍で注意しなければならないのは、脱炭と酸化の2つである。ここでは主に酸化について説明する。ワークが酸化されると酸化皮膜ができ、ワークの有効板厚が薄くなり、金型の摩耗が進むという2つの弊害がある。
の条件が得られない場合は、通常の焼鈍が一般的である。酸化スケールの発生を抑えるため、焼鈍時には炉内をできるだけ満たす必要がある。土壌法も使ったことがある:
会社の条件が整えば、窒素炉焼鈍、つまり光輝焼鈍ができる。よく見なければ、焼鈍前とほとんど同じ色である。
冷間加工硬化の強い金属や、引張クラックのある金属を試作金型内で処理する方法が他にない場合は、中間焼鈍工程を追加する。