世界が環境汚染問題にますます注目する中、自動車各社は軽量化を中心に新素材や新技術の研究開発を進め、自動車の軽量化は重要な開発方向となっている。研究によると、自動車のエネルギー消費の60%は自重によるものである。車両装備の重量を10%減らすと、それに対応する燃料消費は6%から8%減らすことができる。同時に、軽量化は自動車のブレーキ性能もある程度向上させることができ、自動車をより安全で快適な、環境に優しい交通手段とすることができる。アルミニウム合金材料は、軽量で比強度が高く、加工が容易で耐食性に優れているため、今日、軽量化自動車の第一選択肢となっている。
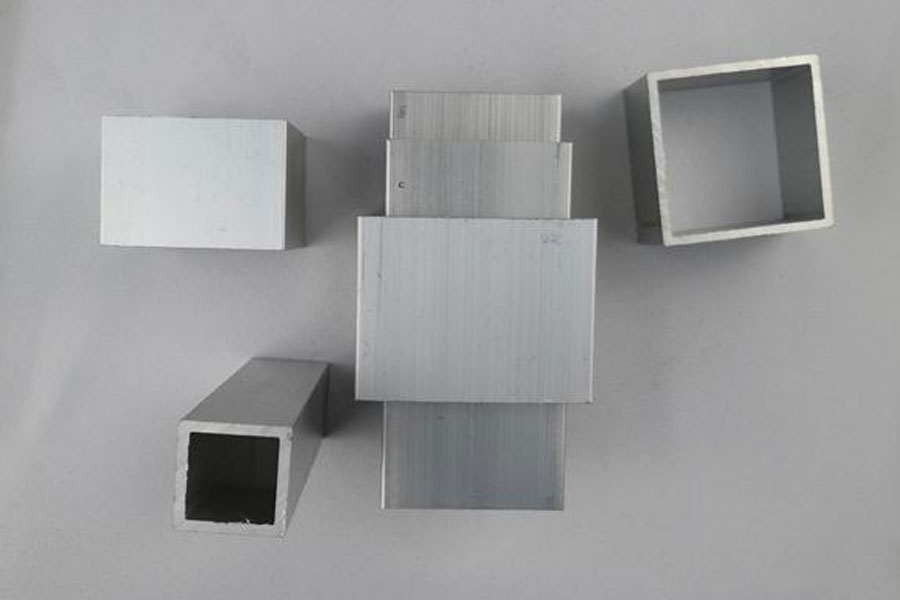
リアサブフレームは、自動車のシャーシ構造の重要な部分として、フロントとリアのアクスルとサスペンションを支持する役割を果たし、ドライビングコントロール、走行安全性、快適性を大幅に向上させることができます。同時に、リアサブフレームの質量を減らすことは、車のハンドリングと安定性を向上させる上で、車の耐荷重性能を向上させることに大きな意味があります。したがって、リヤサブフレームの材質の選択は、クルマ全体の性能向上にとって非常に重要である。従来の国産リアサブフレームは鋼板製がほとんどで、アルミ合金製のサブフレームを採用している車種は少ない。
造泰汽車のあるモデルのリアサブフレーム構造はアルミ合金材料を採用している。合理的な構造設計と体系的な工程を経て、低圧一体鋳造を採用し、強度と耐久性の要求を満たすリアサブフレームを実現し、車両の軽量性を向上させた。定量化レベルリアサブフレームの外形寸法は1,165mm×798mm×396mm、平均肉厚は5mm、質量は30.5 kgである。高強度、高靭性、高耐食性を持つ鋼製部品で、大型かつ複雑な薄肉部品である。これと比較すると、10.1kg、軽量化率は約33%である。
鋳造アルミニウム合金の機械的特性は、第二相の欠陥の特性、分布、性質、数、大きさに依存する。微視的欠陥はアルミニウム合金の破壊における亀裂の発生源であり、機械的性質により大きな影響を与える。したがって、適用に成功した低圧鋳造アルミニウム合金製リアサブフレームの組織と機械的特性を分析する必要がある。
耐久性ベンチテスト
リアサブフレームを構成する部品のシミュレーションには、4チャンネルの疲労試験システムが使用された。300,000回の試験後、製品表面には亀裂などの欠陥はなく、耐久性試験にも合格した。これは、低圧鋳造後のサブフレームの性能が設計要件を満たし、軽量シャーシが改善されていることを示している。
車両全体の路上耐久性試験
リアサブフレームは車両全体に装備され、リアサブフレームの部品の耐久性を確認するため、塩城試験場で30,000kmの総合耐久試験を実施。その結果、リアサブフレームの性能は規格要求を満たしていることが確認された。