ダイカストは非鉄金属成形の重要な手段の一つである。ダイカスト工程では、キャビティ内の溶湯の流動状態が異なるため、コールドバリア、模様、ポア、偏析などの好ましくない現象が発生することがある。これらの好ましくない現象を防止するためには、キャビティ内の溶湯の流れを制御することが極めて重要である。キャビティ内の溶湯の流れを制御する鍵は、ダイカスト金型ゲートシステムの研究と設計にあります。
ダイカスト金型の製造工程
ダイカスト金型製作のCAD/CAE/CAM/CATプロセス。
ダイカスト金型注湯システムの設計
ダイカスト金型ゲートシステムの研究において、ゲートの位置と形状は、溶液の流動状態と充填方向を制御する重要な要素である。まず、ゲートの位置とランナーの形状に注目し、ゲート、ランナー、スラグバッグ、オーバーフロー樋、排気ダクトを設計し、CAEソフトを使ってキャビティ内の溶液の流れを解析する。内側ランナーと内側ゲートの位置と大きさは、充填方法に決定的な影響を与える。
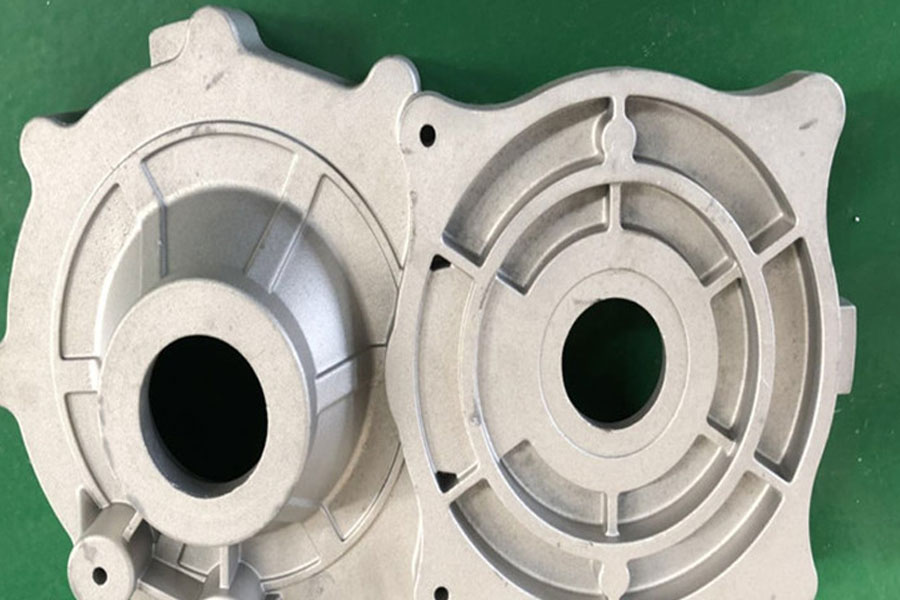
内門のデザイン
完成品にゲートを設ける場合、通常は以下の手順で行う:
スプルーと排気システムの設計
内ゲートは、溶湯がキャビティ内で最もよく流れ、排気が充満し、キャビティの隅々まで溶湯が行き渡る位置に設定する。可能な限り、内ゲートを使用する。複数の内ゲートが必要な場合は、キャビティの渦の中で溶湯が収束しないように、溶湯の流れが互いに干渉したり、分散せずにキャビティ内で合流したりしないように注意する(つまり、金属流が一方向に流れるように誘導する)。
ダイカストのサイズが大きい場合、1つの湯道だけでは必要な湯道断面積が得られないことがあり、複数の湯道を使用する必要がある。ただし、内湯の設定は、キャビティ内の溶湯が合流する際の渦電流を避けるため、溶湯が一方向にのみ流れるように誘導する必要があることに留意する必要がある。
溶湯がダイカストの肉厚部分に到達できるように、溶湯の流れはキャビティ内でできるだけ回転しないようにする。
溶湯の流れはできるだけ短く、均一でなければならない。
インナーランナーの断面積は、インナーランナーに向かって徐々に小さくなり、ガス巻き込みを減少させ、ダイカストのコンパクト性を向上させるのに有益である。インナーランナーは、急旋回や流動衝撃をできるだけ避けるため、流動過程でスムーズに移行することが望ましい。
複数のキャビティがある場合は、各キャビティの容積比に応じてランナの断面積を分割して小さくする。
キャビティ内の空気と潤滑油の揮発ガスは、流れる溶湯によって排気溝へ押し出され、排気溝からキャビティ外へ排出されることが望ましい。特に、溶湯の流れが盲孔にガスを残して排気溝を早期に塞いでしまわないようにする。
金属の流れは、放熱不良の上に熱衝撃を形成してはならない。リブのあるダイカストの場合、金属はできるだけリブの方向に流れるようにする。損傷しやすい金型部品や中子を溶湯が直接洗い流すことは避けるべきである。やむを得ない場合は、スプルーに隔離ゾーンを設けて熱衝撃を避ける。
一般に、インナー・ランナーの幅が広く厚いほど、流れが不均一になる危険性が高くなる。同時に、過度に厚いゲートを使用しないようにし、ゲート切断時の変形を避ける。
キャビティの排気
オーバーフロー樋は、鋳造時に最初に吹き付けられた溶湯を除去し、鋳型の温度を一定にするために使用します。湯流れ溝は、鋳型がガスを含みやすい位置に設けられ、溶湯の流動状態を良くし、キャビティの隅々まで溶湯を誘導して良好な鋳肌を得るために排ガスに使用されます。排気溝はオーバーフロー溝とスラグバッグの前面に接続されるか、キャビティに直接接続されます。
排気スロットの総断面積は、インナー・ランナーの断面積とほぼ等しくなければならない。
パーティング面の排気溝の位置は、キャビティ内の溶湯の流動状態により決定する。排気溝は、溶湯が飛散して人を傷つけないように、「まっすぐ」ではなく「曲がった」方がよい。パーティング面の排気溝の深さは通常0.05mm~0.15mm、キャビティの排気溝の深さは通常0.3mm~0.5mm。5mm;金型端面の排気溝の深さは通常0.1mm~0.15mm;排気溝の幅は一般的に5mm~20mmである。
エジェクターピンとプッシュロッドの間の排気ギャップは、キャビティの排気にとって非常に重要であり、通常は0.01mm~0.02mmに管理されるか、バリが発生しなくなるまで拡大される。
コアの固定排気も有効な排気方法です。通常、コアの外周に0.05mm~0.08mmの間隙を制御し、コアの位置決めネックを1mm~2mmの排気溝幅と厚みで開き、キャビティ内のガスをネックに沿って排気溝から外部に開放。キャビティ底部から排出される。排気口の粗さは無視できない。使用中に塗料が汚れに付着して塞がれ、排気に影響が出ないよう、高い平滑度を保つ必要がある。
流動解析の評価と対策
金型設計では、メタルフローはできるだけ一方向に流れるようにする。流れが解析された後、キャビティ内で渦電流が発見された場合、インナーゲートのリード角度やサイズを変更して渦電流状態を解消する必要があります。
溶湯が合流するとき、溶湯はある距離流れ続けてから流れを止める。したがって、合流部のキャビティの外側にオーバーフロー樋とスラグバッグを追加して、過冷却溶湯と空気化合物がオーバーフロー樋とスラグバッグに流れ込むようにする。異なる部品の充填速度が異なる場合、基本的に同じ充填速度の目標を達成するために、内側ゲートの厚さまたは幅を調整(必要に応じて徐々に増加)する必要がありますが、それはできるだけ内側のランナーを広げることによって達成されるべきである。
流動解析の結果、充填遅れ部が見つかり、インナーランナーを追加することもできる。薄肉のダイカスト部品では、充填時間の短いダイカスト部品を選択する必要があるため、インナーランナーの断面積を大きくして充填時間を短縮し、表面品質を向上させる必要がある。
高いコンパクト性が要求される厚肉のダイカストでは、効果的なガス抜きを確保する必要がある。ダイカスト鋳造では、中程度の充填時間を使用する必要がある。従って、インナー・ランナーの断面を調整し、対応する充填時間を得て、より良い表面品質と内部品質を得る必要がある。
つまり、ダイカスト金型設計の過程では、多くの好ましくない現象を避けるために注意を払う必要があります。CAEによる解析が可能な現代においても、スプルー設計の初期段階では、まずその経験をゲーティングシステムに反映させ、有機的に組み合わせ、解析し、改善し、改良することで、半分の労力で倍の効果が得られるに違いありません。